Gyro invest in new Kleemann mobile impact crusher
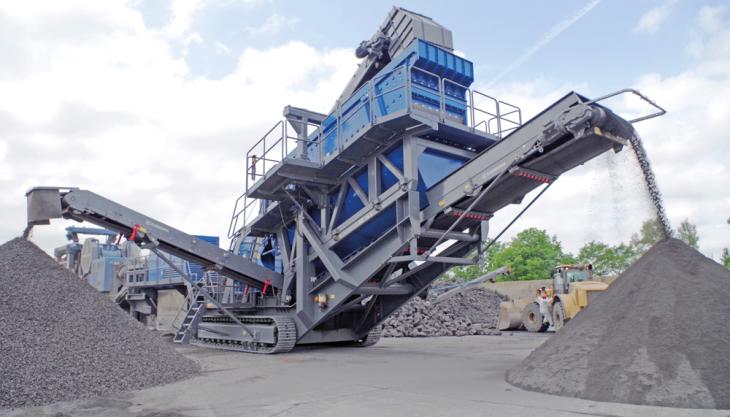
Belgian recycling specialists increase productivity with MOBIFOX M 16 S plant
GYRO have strengthened their machinery fleet with the addition of a Kleemann MOBIFOX M 16 S mobile impact crusher. The machine has been put straight into action at the recycling operator’s Antwerp site where it is working alongside a Kleemann MC 125 Z jaw crusher to process slag, which is created as a by-product during the recycling of precious metals.
‘With the combination of a MC 125 Z and the MF 16 S, we are able to achieve the best result with high cubicity and 30% fines content,’ said Guy Kempeneer, managing director of Gyro. ‘At the same time we have a high hourly output of 350 tonnes.’
Rough grain sizes of 300-900 mm are used as armour-stones. During the primary phase, finer material is crushed by the MC 125 Z jaw crusher and grain size at 0–125mm is fed directly into the MF 16 S unit.
Meanwhile, fine material (0–4 mm) is fed into a triple-deck vibrating screen, while any oversize grain is crushed to 4–28 mm. Both final grain sizes are used for concrete applications instead of sand and gravel.
Jef Kempeneers of Gyro commented: ‘The requirements for materials recycling are becoming more and more stringent. In order to achieve CE and COPRO certification, we regularly take product samples and continuously examine the quality of materials in our labs.’
Thanks to the high performance of the MF 16 S impact crusher, Gyro are able to produce higher tonnage rates in a shorter time and reduce operational costs in the long run. But, according to Gyro, it was not only the product quality and performance that were key deciding factors in the purchase of the plant.
The company already owns 15 Kleemann crushing and screening plants and places a high level of trust in the brand. The latest MF 16 S addition was designed especially for recycling applications with optional features, including a spray system for minimizing dust formation and an external power supply for lower operational consumption.