Finning rebuild 15-year-old Cat dozer
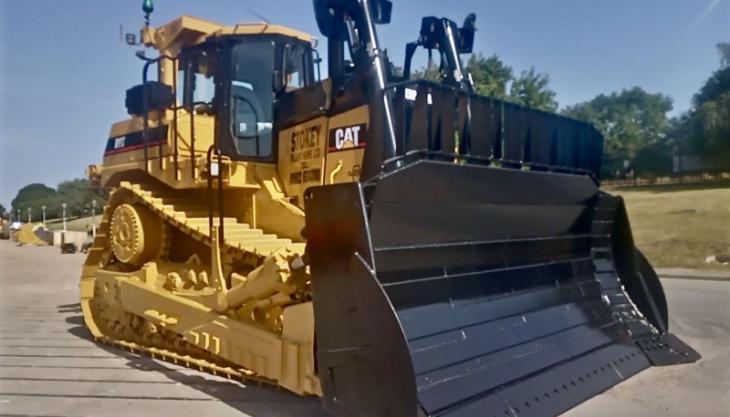
Stokey Plant Hire make sustainable choice to rebuild rather than trade up Cat D9 workhorse
WHEN one of their hardest-working Cat D9 dozers was coming to the end of its operating life, the team at Stokey Plant Hire had a dilemma on their hands – whether to trade up for a new, state-of-the-art Cat replacement, or commission Finning and their expert team of service engineers to rebuild the trusted dozer to give the old D9 a new lease of life.
Stokey have been a valued customer of UK and Ireland Cat dealer Finning for more than 15 years, during which time they have only ever bought new Cat machines when upgrading their fleet. However, this time a combination of factors led them to make the most sustainable and cost-effective choice, to rebuild their dozer.
‘It’s well known that Cat machines are ‘built to be rebuilt’,’ explained Adam Walker, product manager for engines and drivetrains at Finning. ‘Choosing to have a machine rebuilt gives companies the opportunity to save thousands (compared with buying new), but crucially supports their sustainability ambitions by giving the machine a second, third, or even fourth life.
‘Machines working in quarries need to be both robust and reliable as they’re working in harsh, unforgiving environments. While the engine, transmission, and other key components will eventually need replacing before they fail and cause operational issues for the site manager, the main chassis and body of the machine is structurally sound so can be stripped back and restored to its former glory and used again and again.’
For Stokey, the decision to have the Finning service engineers rebuild the machine came down to several key factors – sustainability, cost, reassurance on performance, and reliability. Finning were also able to provide a rental D9 dozer replacement for the duration of the rebuild, which sealed the deal.
Stokey originally purchased the Cat D9 dozer from Finning in 2007 and it has been hard at work in quarries across the Midlands ever since, clocking up more than 22,000 machine hours (around 1,500 a year for the last 15 years). Finning recommended a certified powertrain (CPT) rebuild, which includes replacing the transmission, engine, differential, and final drives, instead of buying a new machine.
Mr Walker continued: ‘Rebuilding a machine is by far the most sustainable choice. If we look at the environmental impact of manufacturing a new cylinder head, for example, compared with using a remanufactured one, it generates 61% fewer greenhouse gases, requires 85% less energy, and uses 86% less water. A remanufactured cylinder head also requires 85% less material than a new manufactured one and means there’s 85% less waste being sent to landfill.
‘A large proportion of the parts that are removed from the original machine during a rebuild are also recovered, restored, and reused as a standard part of the rebuild process. So, when the machine is stripped down, a proportion of the components and materials are recycled back into remanufactured components – creating a circular economy of sorts.
‘Any new components and parts for the rebuilt machine, such as the engine and hydraulics, are sourced through a combination of remanufactured parts fully certified through Caterpillar, via the Finning parts service exchange programme, or bought new.’
According to Finning, customers choosing a rebuild machine option will typically save around 55–60% on the cost, compared with buying a new machine.
In Stokey’s case, the total investment in the rebuild of the D9 was just under £300,000 – significantly less than the £850,000 it would have cost to buy a brand new equivalent D9 dozer, albeit with the latest engine, components, and technology, and an Equipment Protection Plan (EPP) warranty package.
Upon completion, Finning also provided a full five-year warranty on the major powertrain components, with the option to tie in additional Customer Value Agreement (CVA) servicing packages.
The team at Stokey Plant Hire have been involved in the rebuild throughout, regularly visiting the service workshop to check on progress at each of the key stages.
Sarah Jones from Stokey said: ‘We’ve been delighted with the level of input and communication from the Finning team throughout this entire project. We’ve had weekly calls and visits and have been kept informed and involved at each stage. This is the first rebuild that we’ve commissioned Finning to do, and I have to say we’re blown away with the finished result – it looks and sounds better than ever.
‘What’s impressed us most is the level of expertise across the Finning team and professional pride in the work they do – from project management to the quality of the engineering work, and the commitment from all the team throughout.
‘This experience has certainly opened our eyes to the prospect of considering more rebuilds, both in terms of the financial gains over replacing with a new machine and with sustainability in mind as well – we’re giving an old machine a completely new lease of life instead of sending it off for resale or, worse still, to be broken down and scrapped. We’ve already booked in another machine to be rebuilt off the back of this.’