Finer grinding with new BHS ‘sand maker’
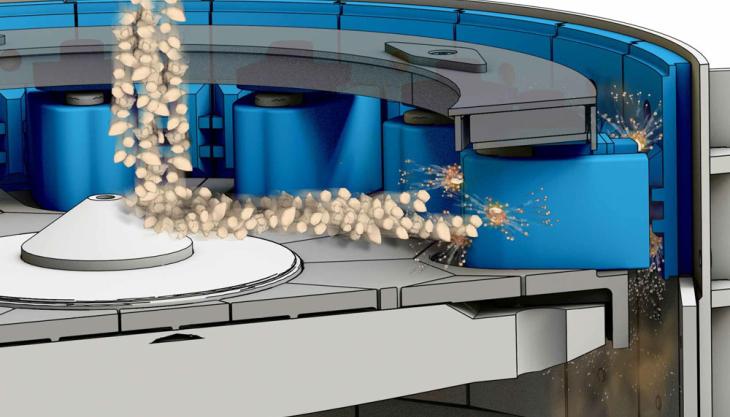
More efficient crushed sand production with new RPMF rotor impact mill from BHS-Sonthofen
BHS-Sonthofen have introduced their new RPMF rotor impact mill – a variant of their proven RPM rotor impact mill. The new RPMF machines are said to produce even finer fractions, making them more efficient at producing crushed sand.
BHS designed both types of machines to be used primarily with pre-crushed, brittle and mildly abrasive materials, such as limestone, as impact crushing has proven to be the best method for crushing these kinds of materials.
However, the new machine has been specifically developed to produce even finer output sizes. Thanks to a longer, narrower milling gap and increased circumferential speed (of up to 90m/s) in the rotor, the RPMF machine archives a higher reduction ratio and delivers material containing a greater proportion of fine sand.
According to Ludwig Bechteler of BHS, who oversaw testing of the new machines, the tests demonstrated that RPMF machines produce a significantly higher proportion of usable fine sand in the 0–1mm size range than RPM rotor impact mills. ‘For example, RPMF machines produce more than 50% more usable dry mortar sand,’ he said.
The new RPMF machines also feature a significantly narrower gap between the grinding tools and the anvil ring, which can be set to a minimum of 5mm.
By yielding significantly more fine sand, the new machines make sand production more efficient by reducing the return flow of coarse material and the number of times that material needs to pass through the mills. This, in turn, also means that these machines require less screening and conveyor technology.
RPMF feed material, which is delivered into the machine from above via a central pipe, can be up to 32mm in size, while the RPM rotor impact mill can be used to pre-crush feed fractions up to 56 mm. The milled material leaves the rotor through the gap between the rotor and the anvil ring, falling down through the two outlet chutes.
To reduce wear on the hammers, the mill can alternate between clockwise and counter-clockwise operation, while easy-to-replace spacers allow the operator to modify the milling gap in accordance with the wear on the impact hammers.
BHS-Sonthofen produce the new RPMF rotor impact mill in two different designs: the RPMF1116, which has a circumferential speed of up to 90m/s and a throughput of up to 25 tonnes/h; and the RPMF1516, which has a circumferential speed of up to 90m/s and a throughput of up to 55 tonnes/h.