Evolution of the Sandvik Leopard DI650i
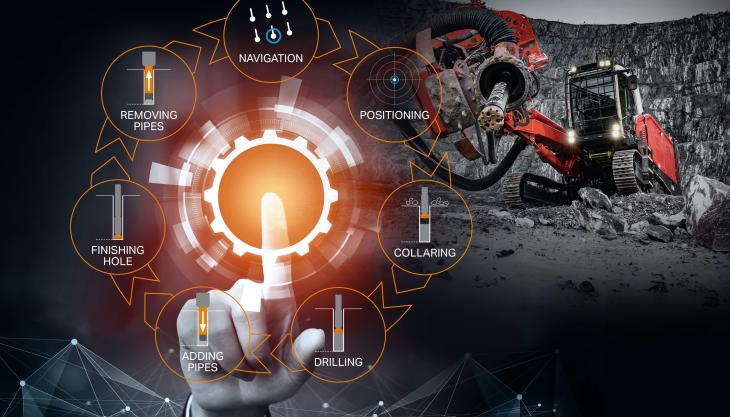
Sandvik are evolving this popular down-the-hole drill rig to support fully autonomous blasthole drilling
SANDVIK Mining and Rock Solutions are evolving their Leopard DI650i down-the-hole (DTH) drill rig to support fully autonomous operation. The new iDrill automation platform expands the existing on-board automated drilling cycle and matches seamlessly with AutoMine Surface Drilling to allow fully autonomous Leopard DI650i fleet operation from a control room.
‘The latest development is a major step on Sandvik’s DTH drill rig automation journey,’ said Jari Läntinen, product manager for surface drilling. ‘This means shifting from individual automated tasks and sequences towards a genuine ecosystem of automation platforms and operating with a connected fleet of automated mining equipment.
‘This will also change the role of one operator handling a single machine into a specialist controlling multiple drill rigs remotely and utilizing their expertise to optimize drilling process productivity.’
The new iDrill automation for Leopard DI650i complements existing automated drilling functionalities with several new features such as drilling stabilization, automated collaring, automated cleaning and detaching from hole. The result is an optimized iDrill drilling cycle where the operator only needs to monitor the process.
The iDrill drilling cycle of Leopard DI650i is engineered to ensure consistent high-quality drilled holes. It supports the fleet operator by minimizing common drilling errors, such as hole inclination, depth and positioning inaccuracies. The intelligent iDrill drilling cycle handles and optimally controls the DTH drilling tools for best possible service life without compromising drilling performance.
The iDrill drilling cycle starts with automated positioning, where the TIM3D drill navigation system guides the rig to the correct spot according to the drill plan. Feed beam and boom are automatically positioned to the correct drilling angle. The drill rig is automatically stabilized and the feed beam is accurately aligned to match the drill plan to ensure high-quality holes.
The existing cycle has been upgraded with new features such as anti-jamming pullback monitoring and intelligent collaring sequence, including suction head automatics and centralizer automatics to match the hammer and pipe size for optimal support while collaring.
In full-power drilling, the iFlow control system automatically adjusts the air pressure and volume levels and the iTorque drilling control system monitors the rotation torque and automatically optimizes the feed force to match the rock conditions.
The pipe-handling system adds and removes pipes automatically. An intelligent hole finishing sequence eliminates any harmful tensile stresses due to inaccuracies and prevents dirt from entering into the DTH hammer. Finally, detaching from the hole sequence makes the drill rig ready to move safely to the next hole.
The iDrill drilling cycle allows manual intervention and can be activated or deactivated at any stage of the cycle. In addition, the operator can add optional ‘wait’ stages between automated sequences, if additional checks are needed for safety reasons or challenging drilling conditions are encountered. After intervention, the cycle will commence automatically until the desired hole depth is reached and the hole sequence is finished.