Astec Industries introduce the GT2612V
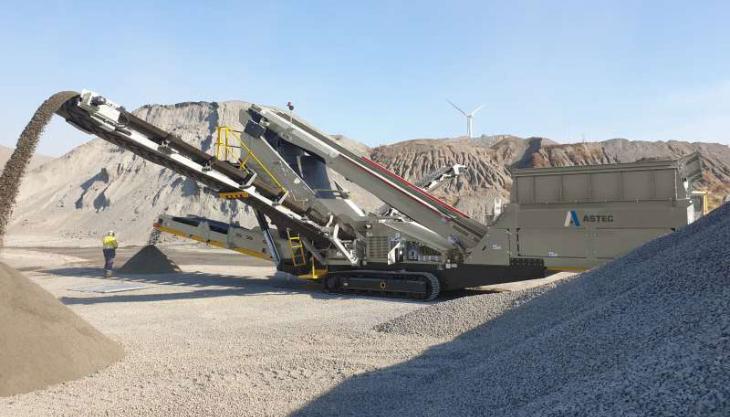
New mobile high-frequency screen plant with unique rotary screen media tensioning system
ASTEC Industries’ Materials Solutions Group have launched their newest mobile high-frequency screening plant, the GT2612V. The plant features a two-deck, 6ft x 12ft (1.8m x 3.7m) 2612V Vari-Vibe screen which uses a unique rotary tensioning system that is said to allow some of the quickest screen media changes on the market, giving producers more uptime.
The 2612V also has deck-mounted, variable- speed hydraulic vibrators, a hydraulic mechanism for varying operating angles, a fines collecting hopper, top- and bottom-deck discharge chutes, and an aggregate spreader. The high-frequency screen can quickly and efficiently size crushed stone, recycled asphalt, sand, gravel, coal, and a variety of other materials.
The mobile GT2612V is manufactured on a heavy-duty, welded-steel main frame with a channel cross-section. A walkway around the screen and remote grease lubrication for ground-level access make maintenance simple.
The plant includes a large 8 cubic metre capacity hopper quipped with 6in (15.2cm) sloped grizzly openings and a remote tipping grid. The hopper also includes foldable wings and hydraulic support legs. The variable-speed, 48in (122cm) wide belt feeder features a high-torque hydraulic drive, full-length impact bed, rubber-lagged head pulley, and self-cleaning wing tail pulley.
The screening plant is equipped with four conveyors: a delivery conveyor, two side conveyors, and a fines conveyor. All four conveyors feature a variable-speed hydraulic drive and easily fold for transport.
The GT2612V is powered by a 136hp (101.4kW) Caterpillar Tier 4 Final engine, whilst engine-mounted hydraulic pumps operate all plant functions. The plant includes a PLC control system with pendant remote controls for the tracks.
Additional options for the GT2612V mobile plant include engine alternatives (Caterpillar Tier 3 and Stage V), 15ft (4.6m) hopper/feeder in lieu of standard for additional capacity, heavier-duty grizzly section with replaceable grouser bar cartridge, vibrating grid, bridge breaker, vinyl dust cover, standard steel screen cloth, engine enclosure filter kit, engine block heater, immersion heater, wireless track remote, telematics system, auto-grease system, and more.