A solution for every application
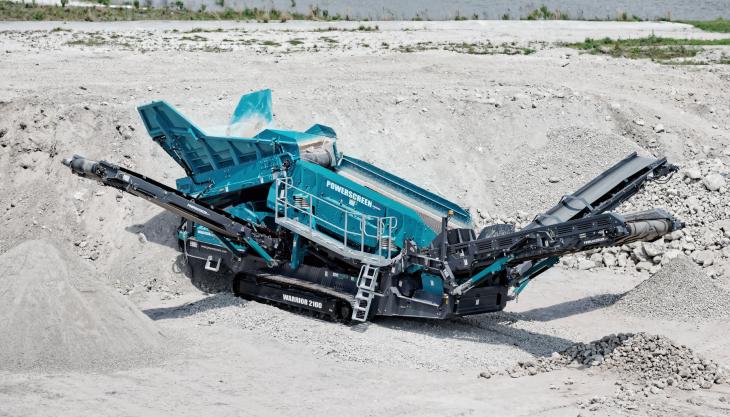
Powerscreen launch two further variants of their successful Warrior 2100 triple-shaft screen
BASED on their highly successful Warrior 2100 triple-shaft screen, Powerscreen have launched two further variants – the Spaleck model and a single-shaft model – making the Warrior 2100 a suitable solution for almost every screening application.
Powerscreen say their proven triple-shaft technology, which is now well established in markets worldwide, is designed so that the Warrior 2100’s 16ft x 5ft screenbox is highly effective and efficient whilst maintaining exceptional throughput productivity. The machine’s extreme screening acceleration is said to offer the Warrior 2100 improved capabilities over its class rivals, especially in sticky scalping applications.
Now Powerscreen are offering what they describe as the ultimate in mobile screening and separation technology. At the core of new Warrior 2100 Spaleck model is a two-deck, high-performance, waste-recycling screen with a Flip-Flow bottom deck. The stepped top deck design combined with the bottom-deck Flip-Flow technology is said to place this screen in a class of its own for customers in many sectors of the waste recycling industry.
Key to this is the introduction of the Flip-Flow bottom deck, which uses rubber panels that move in a smooth wave motion, expanding and contracting to keep the material constantly in motion. This breaks down sticky material, such as clay and soil, making it possible to produce 0-10mm fines with minimal contamination from non-inert materials, such as wood and plastic, which generally fall into the +10mm particle band.
Recyclable material enters the top deck, which consists of five stepped 3D screening segments formed from open-surface panels. As well as preventing waste from catching in the surface and reducing downtime for clearance, this design helps ensure that long, thin pieces cannot pass through to the bottom layer, thereby reducing wear and tear on the bottom deck media. The deck panels on the top and bottom deck, are easily removable, and can be replaced individually or together.
Meanwhile, delivering effective screening capabilities with a more conventional approach, the new Warrior 2100 single-shaft model is designed for efficient operation in less demanding applications when the power of a triple-shaft drive or the precision of a Flip-Flow deck is not required. Supported on two 130mm bearings, Powerscreen say the single-shaft screen is still capable of providing an impressive screening stroke and screening angles of up to 18°.
The drive system is mounted directly to the screen side and is pulley driven to ensure that optimum hydraulic efficiency can be realized at both standard and increased amplitudes, making the Warrior 2100 single-shaft unit a leader in the conventional 16ft x 5ft class.
The Warrior 2100 range is powered by the 4-cylinder Cat C4.4 diesel engine, which is designed to run at 1,800 rev/min, making it one of the most fuel-efficient platforms in its class. The machine can be ordered with Powerscreen’s Dual Power option, which has a fully integrated control system that allows the end-user to power the machine via the onboard diesel-hydraulic engine or directly from a mains power source.
According to Powerscreen, the Warrior 2100 range’s unrivalled conveyor and stockpiling configurations, high-performance two-speed tracks and superior serviceability and maintenance access make it an extremely flexible and user-friendly platform.
The machine is now available to order in any of the three screen variants, with screenbox conversion in the field also available through local Powerscreen distributors. This kind of flexibility, say Powerscreen, could be beneficial to customers in the rental industry, screening contractors or those with seasonal limitations, providing users with the ability to produce saleable material in the broadest range of applications.