Keeping your Weighbridge Healthy
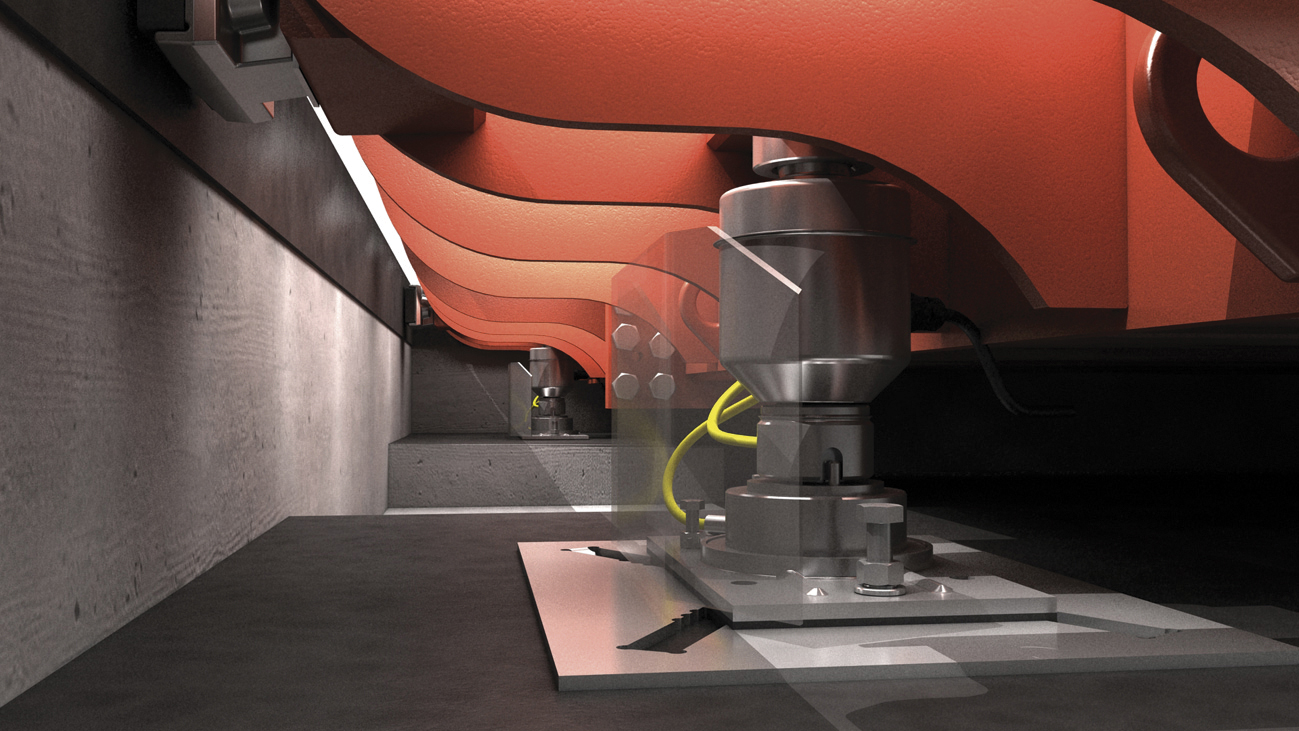
First published in the March 2020 issue of Quarry Management
Nick Burley, sales director at Weightron Bilanciai Ltd, examines the key causes of weighbridge failure, highlights the importance of good housekeeping and explains how remote predictive maintenance could revolutionize weighbridge support
Weighing plays a vital role in quarry operations, with equipment ranging from weighbridges and silo weighing systems through to hopper scales and bulk throughput weighers. The quarry operating environment is, almost certainly, the harshest of any industry, with equipment subjected to long and arduous operating hours in hostile conditions.
The recent months of heavy rain and subsequent flooding in many areas of the UK have been particularly demanding for weighing equipment, resulting in an increase in disruptive and expensive breakdowns. With reductions in maintenance staff at many sites and increased pressure to keep plants operational, vital maintenance can be overlooked.
Weighbridges
There is no doubt that quarries could not function without reliable vehicle weighing. However, the ongoing performance of weighbridges can be taken for granted and it is often easy for operators to forget that weighbridges are more than just a large steel platform until it is too late. As with most weighing systems, accurate vehicle weighing is dependent on the performance of the load-cells (and mounting hardware) at the heart of the system. Although modern weighbridge load-cells are robust and, in general, better sealed than their predecessors, they are still precision measuring instruments, converting tiny mechanical deflections into meaningful weight-related outputs. To this end, they need looking after.
Preventative maintenance
Quarries often have weighbridges of different types and it is prudent to take out a structured maintenance contract with a recognized service supplier who has the expertise and nationwide resources to support a range of equipment. However, quarry operators can easily limit weighbridge breakdowns by adopting a simple preventive maintenance regime. Understanding how weighbridges function can help operators to implement such a programme.
The typical weighbridge consists of a steel or steel-concrete composite deck structure supported on strain-gauge load-cells. There are two main structural designs – pit mounted and surface mounted. Surface-mount bridges usually have approach and exit ramps of steel or concrete. Pit weighbridges, as the name implies, sit in a preformed concrete pit with drainage.
Depending on the size and capacity of the weighbridge, the number of load-cells is usually six, eight or 10, although some older designs relied on only four higher-capacity load-cells. To ensure optimum load input into the load-cells, they are usually contained within an integral mounting kit arrangement, which is designed to allow a small and controlled amount of lateral self-restoring movement in the weighbridge deck. Reliable and accurate weighing is dependent on this deck movement and any build-up of debris in the gaps between the deck and the pit foundations or ramps can be problematic. Such mounting kits also compensate for thermal changes in the weighbridge, which can be significant between winter and summer. Access to the load-cells is usually via hatches in the deck, although some drive-through designs have the load-cells out-board of the deck.
The key factors which can lead to problems are:
- Overloading and unnecessarily heavy braking
- Lack of cleaning of approach areas and the weighbridge deck itself
- Blocked drainage/flooding
- Build-up of debris around the load-cell assemblies
- Damage to cables caused by rodents or poor cable management
- Electric welding on the weighbridge deck or ramps.
Overloading and heavy braking
This can be a major problem, resulting in damage to load-cells, mounting hardware, the deck itself and its foundations. It can difficult to prevent this, but making drivers aware of the consequences, together with adequate signage, including speed-restriction signs, can help. A simple traffic light system can also be useful in reducing speed.
Lack of cleaning
This is the most fundamental, yet often most overlooked, factor in good weighbridge housekeeping. Ensuring the area around the weighbridge, together with the approach roads, is free of debris is very important for health and safety and operational reasons. It is particularly important in winter months and after periods of heavy rain. Pit weighbridges usually have a ‘T’ section rubber seal around the edge of the deck to prevent ingress of debris. It is important to check this remains in situ.
Blocked drainage and flooding
This is probably the biggest cause of problems with weighbridges in quarries. Standing water around the weighbridge will exacerbate problems, especially with load-cells where the sealing may have been compromised through damage, fatigue or corrosion. If flooding does occur, extra checks should be made after the water has drained away.
Build-up of debris around the load-cells
This has a number of consequences which can result in premature load-cell failure. Any built-in lightning protection can easily be compromised and ongoing corrosion can result. Great care should be taken when cleaning around load-cells and no chemicals should be used. It is worth asking for advice on the best way to carry out the cleaning.
Cable problems
Rodents love to chew cables and can easily do thousands of pounds worth of damage to load-cells and electronics. Rodent-proof cable and ducting can prevent this.
Electric welding
The high currents involved with electric welding can easily damage load-cells and electronics. If it is necessary to carry out repairs, professional advice should be sought from the weighbridge supplier or service provider.
Checking the operation of weighbridges
A quick check can be done to regularly test the basic operation of a weighbridge – simply by driving a small van or car of approximate known weight on to the weighbridge deck.
Most weighbridges in the UK are calibrated in units of 20kg. In other words, the weighbridge weight indicator display moves up and down in steps of 20kg. The vehicle should be positioned at three different points – at the two ends and in the middle. Ideally, the displayed weight reading at the different positions should be in close agreement.
It should be noted that if critical components, including load-cells and instrumentation, are replaced on a legal-for-trade weighbridge, there is a legal requirement for the weighbridge to be re-verified by an approved company certified to carry out such verification. This will require the weighbridge to be loaded with calibrated weights. Failure to comply can result in fines for the operator and the risk of the weighbridge being taken out of service.
Hopper scales and silo weighing systems
A wide range of hoppers, tanks and vessels are fitted with load-cells and it is important to carry out routine preventative maintenance checks on a regular basis. It is important to ensure all the load-cells are functioning but it can be difficult to ascertain whether the weighing system is working correctly, especially with storage vessels. Unlike weighbridges, the load-cells on vessels may be an essential part of the structural integrity and any mechanical failure could have important negative consequences (by comparison, if one or more weighbridge load-cells fails mechanically, there is little or no residual risk to the integrity of the system). It is important, therefore, to ascertain the cause of any failure and engineers should not be tempted to electrically disconnect the faulty cell. For example, if the load-cell has failed through ingress of moisture or chemicals, corrosion could cause the mechanical integrity of the cell to fail with dangerous consequences.
Predictive maintenance – the future
The frustration of not knowing ‘when’ or ‘if’ your weighbridge might fail and for what reason, could become a thing of the past. Remote predictive maintenance using Cloud technology is one of the latest tools becoming available for weighbridge operators. This technology is set to revolutionize weighbridge support by allowing service providers to view individual weighbridge performance, remotely in real time.
With such a system installed, engineers can log in to view the performance of the weighbridge. A key feature of this technology is that the system will immediately flag up any load-cell or instrument malfunction. The system can also show ‘when’ and ‘how often’ the weighbridge is being used, highlighting any spikes in load caused by overloading.
The technology is ideal for single- and multi-site installations. This real-time vision allows rapid response to site issues and ensures that engineers know what the problem is before they arrive. It also ensures the correct spares are available and allows the service provider to co-ordinate the calibration truck to ensure minimum downtime.
Depending on the particular site, it should also be relatively straightforward to upgrade existing weighbridges to take advantage of this technology. It is expected that such systems will also have the capability to allow operators themselves to view basic information relating to their weighbridges.
Conclusion
When it comes to looking after quarry weighbridges, basic good housekeeping will pay dividends and should minimize any unwanted breakdowns. Understanding fundamental weighbridge design and operation will help operators carry out effective preventative maintenance. Driver guidance and training, together with effective site signage will also help with long-term reliability. Finally, new remote predictive maintenance technologies are set to improve ongoing weighbridge diagnostics and ensure any problems can be dealt with quickly and effectively.
For further information visit: www.weightron.com
- Subscribe to Quarry Management, the monthly journal for the mineral products industry, to read articles before they appear on Agg-Net.com