Window Of Opportunity At Warmsworth
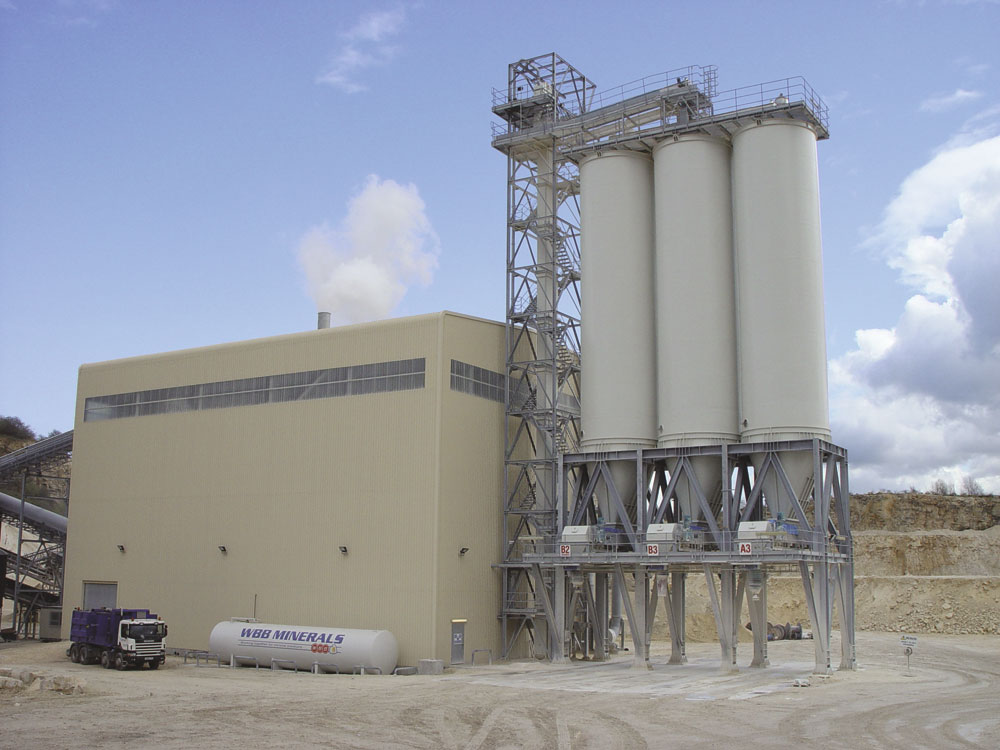
WBB Minerals’ £4.5 million investment in new sand plant boosts output and improves environmental control at Dolomite Quarry
Last year WBB Minerals commissioned a new £4.5 million sand-processing plant at Dolomite Quarry, the company’s aptly named site near Warmsworth, on the outskirts of Doncaster. Since December 2004 the new plant has been producing finely ground dolomite for supply to the glass industry, in particular to the site’s former owner and largest customer, Pilkington Glass.
Pilkington originally acquired Dolomite Quarry in 1980, having recognized the unique quality of the dolomitic limestone in this locality. With the lowest iron content of any dolomitic deposit in the UK (0.25% on average), the material produced at the plant is largely used as a flux in window glass manufacturing. The dolomite also supplies magnesium into the glass, allowing it to bend and giving it more flexibility, which helps prevent shattering.
A decade or so after acquiring the site, however, Pilkington opted to withdraw from their non-core activities, such as quarrying, and in 1993 the site was acquired by Hepworth Minerals & Chemicals Ltd (HMC). However, it was not until the acquisition of HMC by Belgian-based Sibelco in 2000, followed a year later by HMC’s integration with another Sibelco-owned company, Watts Blake Bearne, to form WBB Minerals, that significant investment in the site was forthcoming.
WBB Minerals’ recent £4.5 million investment at Warmsworth was driven by the need to make environmental improvements to the dolomite sand plant as well as the need to increase production capacity following the opening of Guardian Glass’ new float glass factory in Goole in 2003.
Today the site sells around 3,500 tonnes of 2mm and 3mm finished products a week, in addition to a range of roadstone aggregates. In terms of volume, some 75% of dolomite sand production is destined for glass manufacturing, with the remainder being used in construction and agricultural applications. In terms of value, however, around 90% of the site’s revenue is derived from the sale of low iron content dolomite sand to the window glass industry.
The quarrying process
Quarrying at Warmsworth is carried out by campaigned contract, which generally takes place once a year using WBB Minerals’ Caterpillar 385 excavator and quick-hitch ripper attachment together with the contractor’s dumpers, loader and dozer. Each annual extraction campaign lasts for approximately four to six months, with material being stockpiled adjacent to the primary crusher where preliminary segregation takes place to identify the various iron contents needed to meet customer specifications.
Feeding of the primary crusher is carried out by a Volvo L220E wheel loader. Material drawn from the 200,000-tonne stockpile is crushed through a Pegson 40in x 32in single-toggle jaw crusher followed by a BJD rotary crusher, which reduces the dolomite to 75mm or less. Before entering the primary crusher, the stone is scalped at 40mm to remove any soil, which could cause impurities in the glass-making process.
From the secondary crusher the –75mm dolomite is fed, via a recovery conveyor and elevator, into a series of 64 storage bins, each holding around 40 tonnes, which act as a blending facility for the product. A critical factor in dolomite used for glass-making is consistency in quality and notably iron content. A major feature of the production process, therefore, involves achieving a consistent product by carefully controlled blending.
As the blending bins are being filled an automatic sampler takes an incremental sample, which, after automatic milling, is analysed on an XRF analyser to determine the iron content. This result is then regarded as representative of a particular 40-tonne bin. Material for sale in the form of nominal 3mm or 2mm dolomite sand, is produced by blending six of these bins together, two at a time, and conveying the material to the new 240 tonnes/h processing plant.
New processing plant
Although initial design work for the new plant started in 2000, capital approval for the final scheme was not given until May 2003. The task of principal contractor was awarded to the Italian company Dutto Progettiazone, another subsidiary of Sibelco, but the construction project brought together other companies from countries across Europe including Austria and Holland.
Once decisions about plant, equipment and designs had been made, the specialized processing items (dryer, mills, screens etc) were sourced directly by WBB Minerals. Dutto were then asked to submit drawings for approval by the company and the construction process began in earnest.
Construction of the new plant took eight months from start to finish with the civil engineering works commencing in April/May 2004 and Dutto beginning work on site in June. Most of the material-handling equipment and the plant building itself was manufactured in Italy and transported to the UK by lorry (in excess of 50 lorry loads in total). These were erected on site using a 40m tower crane.
The main difficulty during construction involved the existing plant, which was still in commission and had to be linked to the new processing section and the current crushing and blending circuit. This entailed a four-week shutdown period during which customers were serviced from strategic stocks held in several warehouses situated locally to them. These stocks had been built up during the preceding months when weather and production conditions were favourable.
The new dolomite processing plant brings together equipment from across Europe.
The blended –75mm stone is first conveyed on to an Austrian-built Binder Bivitec vibrating screen — a 7m long x 2.5m wide unit capable of handling up to 260 tonnes/h and designed to achieve a single cut to provide 110 tonnes/h of –3.5mm dryer feed.
The oversize from this cut is fed directly to a pair of BJD 36in x 48in hammer mills, which reduce the dolomite to 14mm or less. This is recycled in a closed circuit arrangement until it passes the cut at 3.5mm.
The dryer unit is a Dutch-built Ventilex vibrating fluid-bed dryer/cooler capable of accepting up to 110 tonnes/h of material at 11% moisture content, drying it to below 3% moisture, and discharging it with an exit temperature of less than 35ºC.
From the cooler, the material is passed over twin Rotex double-deck screens, which give the final top size of the product, with oversize once again being returned, via WAM screw conveyors, to the BJD hammer mills for re-crushing.
The nominal 2mm and 3mm products from the Rotex screens are screw fed into a 35m high bucket elevator and delivered, via Robson Airglide sealed conveyors, into one of three 450-tonne storage silos ready for discharge by weigh-feeder into 30-tonne delivery tankers or tipper trucks.
The Warmsworth site employs a total of 10 staff, however the new plant is automatically controlled via a SCADA system and requires only one operative for monitoring and control purposes.
Environmental benefits
In addition to the need to increase production, the other main driver behind WBB Minerals’ development of the new dolomite processing plant at Warmsworth was the range of environmental benefits that would result from the replant. These benefits manifest themselves in both internal and external improvements.
In terms of benefits for the company’s workforce at Warmsworth, the new plant replaces three separate production units and, as a result, the suppression of dust and noise has been simplified. Furthermore, the new plant is fully automatic, which means that operators are remote from any remaining noise and dust that has not been controlled by engineering means.
A further reason for the simplified environmental controls stems from a basic change in the production process. This has been made possible by moving the drying operation further downstream so that the inherent moisture content of the dolomite is used as a natural dust suppressant during the crushing and blending operations. Previously, the blending operation in particular had been a steamy, dusty operation.
Another key to the success of the environmental controls is that once the material has been dried, conveying is carried out almost exclusively by sealed screw conveyors or bucket elevators. In addition, unlike the previous rotary dryer, which dried –75mm stone, the new Ventilex unit is totally sealed and sound insulated to eliminate dust and reduce noise. The new dryer/burner combination is also easier to control and burns more efficiently, resulting in a 30% reduction in oil consumption.
Moreover, any fines that are removed from the product as part of the drying process are conditioned with water for subsequent disposal in the quarry in the form of a paste. This is in direct contrast to the previous method whereby fines were hauled by dumptruck in a virtually dry and often dusty state.
Similarly, milling of the –75mm material now takes place in a wet condition, once again largely using the inherent moisture content of the stone to suppress dust.
All of the above processes now take place in one fully enclosed building as opposed to the three former disparate sections. This, in combination with all the other benefits, gives rise to a far more environmentally friendly workplace for WBB Minerals’ employees.
From an external perspective, the environmental benefits include:
- the tipping of fines in a conditioned state, not as before when disposal could cause dust emissions in close proximity to a public footpath
- the stockpiling of fines in a conditioned state, thereby reducing wind-blown dust
- the elimination of steam emissions to the atmosphere arising from hot materials in the blending plant
- the installation of a bag filter with continuous stack monitoring to ensure efficient operation of the dryer and effective plant dust suppression. An alarm is activated should a filter bag burst or the preset emission limit be exceeded
- the plant has been moved deeper into the quarry and is no longer visible from the public footpaths nearby.
Another positive initiative undertaken by WBB Minerals in recent years has been the use of a Caterpillar 385 excavator equipped with a quick-hitch ripper, allowing the stone to be won by non-explosive methods and resulting in the virtual elimination of blasting at the quarry. With a number of residential properties and the A630 Doncaster to Sheffield trunk road situated within 150m of working faces at the quarry, this change has been a vital part of Warmsworth's development in order to secure a long-term future.
Also, recognizing the importance of keeping both individuals and organizations in the local community informed from the outset, WBB Minerals initiated a mail drop that outlined the proposals for the new plant, and throughout the planning and construction stages the company held several liaison meetings with the local authority planning and environmental departments as well as representatives from the parish council and residents of Warmsworth. All of the meetings received positive responses from the local inhabitants.
The recent investment at Warmsworth has succeeded in both of its key aims, namely to increase production and to improve environmental control both internally and externally. This achievement, together with the uniqueness of the Warmsworth dolomite and the site’s clear focus on providing value rather than volume, should help secure the future of the site and the UK’s window glass industry for many years to come.
Acknowledgement
The editor wishes to thank WBB Minerals for permission to visit the site and, in particular, Graham Blount, site manager, for his help in preparing this report.