Replant At Woodhall Spa
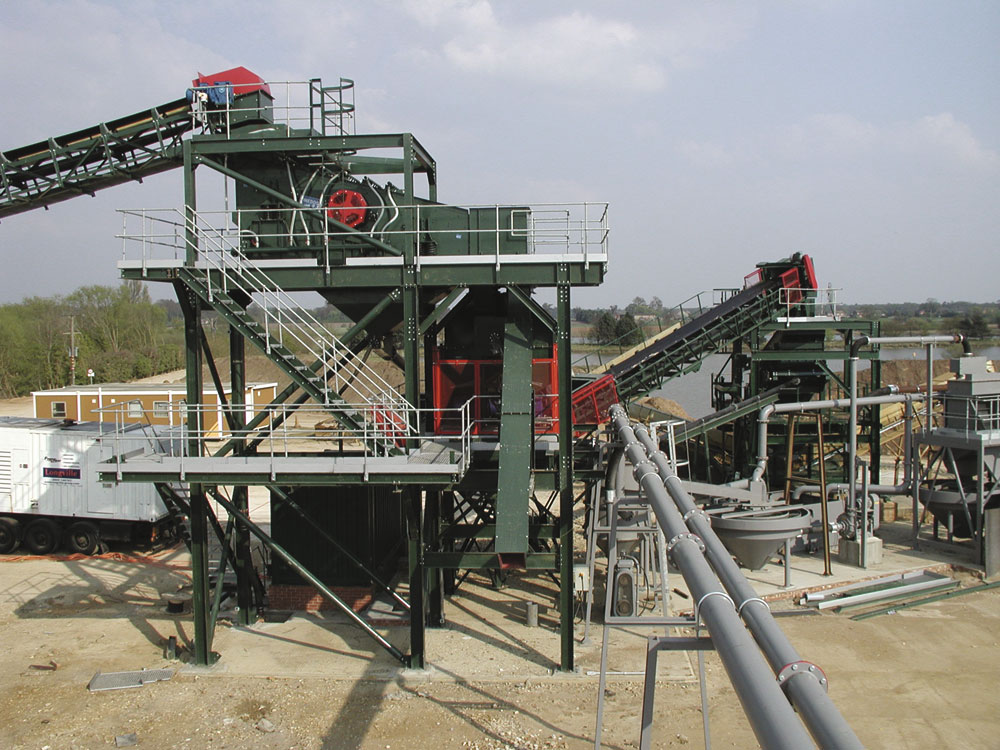
New processing plant and new owners for Lincolnshire operator
For the last 70 years Woodhall Spa Sand & Gravel Ltd (WSSG) have operated as an independent family-run aggregates business, based in the heart of rural Lincolnshire. The company were founded at their current site near Woodhall Spa in 1934 by the Jones and Coulson families from Yorkshire and London, respectively, and since then have built up a reputation in Lincolnshire and the East Midlands for the quality of their products and service.
Last month, however, WSSG were acquired by Aggregate Industries, but although the company will now be operating as part of a much wider portfolio, WSSG will continue to serve their well established customer base under their current name.
The company’s decision to invest in a new plant followed the granting of planning permission to extract sand and gravel from a further 80 acres of land adjacent to their existing operations.
WSSG work the sand and gravel deposits on the flood plain of the Old River Bain between the villages of Kirkby-on-Bain and Tattershall Thorpe, producing a full range of aggregate products in line with the new European Standards. The company also market their own decorative gravel under the brand name Golden Spa, a product that has proved particularly popular with builders’ merchants and the general public because of its warm golden-yellow colour.
The indigenous flint sand and gravel deposit in the Woodhall Spa area is glacial in origin and variable in depth and thickness. The sand to gravel ratio at the current extraction site is around 30:70 although this can vary considerably, necessitating tight processing controls to keep finished products within specification.
With the water table lying just below the topsoil, dewatering ahead of extraction allows the sand and gravel to be worked in a semi-dry state. Material is delivered to the new processing plant by a recently installed 900m long field conveyor system.
Commissioned in June 2003 and with the ability to deliver up to 200 tonnes/h, this has removed the need for articulated haulers and provides a quieter, more environmentally friendly transport solution. Moreover, in order to reduce the number of feed hopper/field conveyor movements as extraction progresses, WSSG have recently invested in a new Liebherr 944B long-reach excavator.
On arrival at the new processing plant the field conveyor discharges on to the inclined section of a 5m high overhead conveyor that delivers the material directly into the plant’s 40-tonne capacity feed hopper. Supplied and installed by Morley-based Finedoor, this unit has a 4.7m wide feed opening with an inclined static grid and features a hydraulically operated flow-control door at its base that discharges the raw material on to a 900mm wide by 5.9m long 11kW electronically controlled variable-speed belt feeder. Ramped access to the rear of the hopper allows separate or simultaneous feeding by mobile plant.
The belt feeder discharges on to a 650mm wide by 47.5m long inclined main conveyor, again supplied and installed by Finedoor. Driven by a 15kW motor and shaft-mounted gearbox, and operating at a speed of 1.5m/s, this delivers the raw feed to a Finedoor twin-deck primary rinsing screen measuring 5m in length x 1.5m in width and mounted on a raised platform with an all-round walkway for ease of maintenance. Directly driven by an 11kW motor and cardan shaft, the screen is fitted with SCS modular polyurethane mats with 40mm apertures on the top deck and 6mm apertures on the bottom deck.
Any oversize rejected by the top deck is stockpiled on site for subsequent crushing. Once crushed, the material is fed back into the process flow via the main feed hopper.
Coarse sand contained in the underflow from the bottom deck of the primary screen is recovered by a new Linatex sand plant arrangement. The slurry is fed initially to a 1,676mm diameter Linatex S-type classifier. From here a 75kW Linatex Mk III 200/150mm centrifugal pump is used to pump the denser underflow to a tower-mounted Linatex HK200 sand separator/dewaterer via 200mm diameter suction pipework and trestle-mounted delivery pipework. The separator tower includes three sets of Linatex-lined discharge chutes and is of sufficient height to provide a coarse-sand stockpile capacity of 3,750 tonnes. The overflow from the sand separator is delivered to the site’s extensive effluent-treatment lagoons via 250mm diameter return pipework and an effluent buffer tank, with facilities provided for partial recirculation of the slurry by means of butterfly valves.
The –40mm +6mm fraction from the primary rinsing screen discharges directly into a high-specification scrubber barrel supplied by Wileman Engineers Ltd of Ashby-de-la-Zouch, Leicestershire. Measuring 3m in length x 2m in diameter and equipped with Linatex rubber liners, a Renold gearbox/drive unit, FAG bearings and Michelin tyres, the barrel has a maximum water requirement of 400 gals/min and delivers a maximum throughput of 120 tonnes/h. The unit incorporates a contraflow system which allows water and sand to be removed from both the feed end and the discharge end of the barrel. This, say Wileman, has the effect of creating a cleaner dewatered product prior to final grading — a claim fully endorsed by WSSG who confirm that the cleanliness of the products now being produced would not have been possible with their original scrubber barrel. Dirty process water from the scrubber is also fed back to the S-type classifier for coarse-sand recovery.
The clean –40mm +6mm material is discharged from the scrubber barrel on to a short inclined conveyor which delivers it directly to a second Finedoor twin-deck rinsing screen featuring a similar drive arrangement to the primary screen. This unit, however, is fitted with SCS modular polyurethane mats with 24mm apertures on the top deck and 6.5mm apertures on the first section of the bottom deck and 13mm apertures on the remainder. A discharge chute and two short stockpile conveyors deliver the final gravel products (40mm, 20mm and 10mm single sizes) to their respective piles. Process water from this screen is also piped back to the S-type classifier for sand recovery.
According to WSSG, the irregular composition of the local gravel deposit, which contains a relatively high proportion of elongate particles, means that continual fine-tuning of the modular screen mats is needed to keep the products within specification. The company say Rugby-based SCS (Screening Consultancy and Supplies Ltd) have been very helpful in this respect, supplying customized decks in short lead times and developing a screen mat ‘rotation’ system using a combination of old and new mats to achieve optimum results. Moreover, the use of modular deck units means that downtime is kept to a minimum when mats are being moved or replaced.
The overflow (containing fine sand) from the S-type classifier mentioned earlier is fed into the first of two new 2,440mm diameter Linatex feed-regulating sumps. From here an 11kW Linatex Mk III 150/125mm centrifugal pump is used to pump the sump’s underflow to a new Linatex sieve bend unit where any lightweight contaminants are removed. This in turn discharges into the second feed-regulating sump from where the underflow is pumped by an existing pump and 150mm diameter delivery pipework to the site’s original fine-sand tower and Linatex separator/dewaterer. The overflow from both feed-regulating sumps is fed to the site’s effluent tank together with the overflow from the separator, although the latter can be partially recirculated to both sumps, for liquid make-up purposes, by means of butterfly valves.
Acknowledgement
The editor wishes to thank Woodhall Spa Sand & Gravel Ltd for permission to visit the site and, in particular, Peter Gray, quarry manager, and Allen Smith, works manager, for their help in preparing this article.