New Quarry Plant for Holme Sand and Ballast
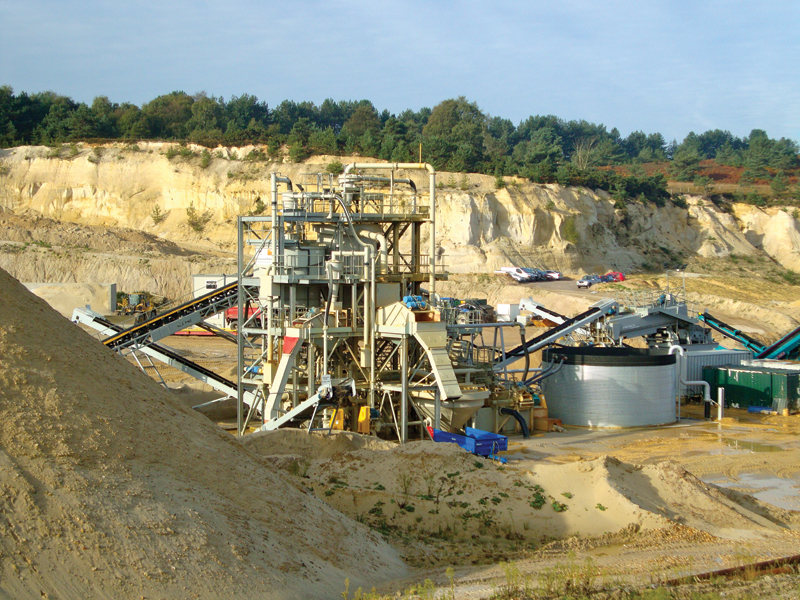
First published in the February 2014 issue of Quarry Management as From Challenging Raw Material to Premium Product
New sand-processing plant for Holme Sand & Ballast’s Masters Quarry in Dorset
Holme Sand & Ballast LLP’s Masters Quarry, near Wareham, in Dorset, produces around 200,000 tonnes of sand with a small amount of gravel each year for a diverse range of applications.
These include sands for equine surfaces, golf courses and top-dressing sports pitches and greens, as well as construction sands for end products such as ready-mixed concrete, precast drainage pipes and precast paving products, and – following a recent contract win – specialist sand for the inner containment concrete on a new nuclear power station.
In 2011 the company decided to upgrade the sand-processing plant at the quarry in order to increase capacity, efficiency and reliability. This task was given to a related company, Holme Mineral Processing Ltd (HMP) who, in turn, contracted Weir Minerals Europe to supply a complete sand-processing system.
The essential challenges at the site are ensuring the cleanliness and purity of the sand and achieving the accurate grading of two products – one coarser and one finer. The coarser of the two contains particles between 5mm and 500 microns while the finer grade contains 500micron to 75micron particles.
New plant
The system specified to meet these challenges included: a Warman SJ submersible pump on a floatation unit; electrically driven centrifugal Warman WGR slurry pumps; Enduron vibrating dewatering screens fitted with a silt-return arrangement and including screen underflow pipework, supporting structure and supports; Cavex hydrocyclone; Enduron sizing screen; T-Type classifier and dense-medium separator. To transport the sand slurry between each piece of equipment, heavy-duty Linatex-lined cut-end hose was also supplied.
The first of the challenges – cleanliness and purity – is made more difficult by the presence of lignite found in the Dorset sands from the Poole Formation. Lignite is a soft, combustible rock that, like coal, is formed from organic matter. If left in the sand it will oxidize to give unsightly black stains on the final products.
Removing it is challenging because the density of lignite is similar to that of sand and therefore the separation process needs to be very accurate and consistent. To achieve a marketable product, the lignite content – along with other unwanted materials – must be reduced to less than 0.5% by weight. To ensure this is always the case, in the purchase contract Holme specified a maximum lignite content of 0.3% by weight for the sand products produced by the plant.
The wide range of end products in the Holme range is achieved by accurately blending the clean, classified coarse and fine products in different ratios using a bespoke touch-screen programmable logic control (PLC) system designed and installed by Weir Minerals. The feed to the dewatering screen is controlled by Linatex-lined flow-control valves linked to density transmitters in the classification units that can be adjusted depending on the feed material being supplied and the grading of the end products required.
In order to ensure reliability, maximize the wear life of parts and minimize downtime, the Warman WGR and AH centrifugal slurry pumps supplied with the plant are equipped with the upgraded WRT impeller and throat bush combination, which features an advanced computer-modelled hydraulic design to reduce turbulence and wear.
Linatex natural rubber lining was also applied where necessary – including on screen underpans and feed and discharge chutes – to provide the lowest cost of ownership through superior abrasion resistance.
The high-precision Cavex hydrocyclone supplied with the plant can be adjusted to classify particles very accurately according to their density, which allows the lower-density lignite particles to be separated from the sand with a high level of effectiveness. Weir Minerals have actually guaranteed that the units will deliver lignite content in the final washed sand products of less than 0.04% – seven times less than Holme’s requirements.
The additional capacity delivered by the new plant has allowed Holme to increase production at the quarry to more than 150 tonnes/h, theoretically giving a maximum sand production capacity in excess of 300,000 tonnes per annum if required.
The Weir Minerals team also recommended installing a fines-recovery system to reduce wastage and create a third, finer product that would provide an additional revenue stream for Holme whilst maximizing lagoon space for silt.
Recycled sand
As well as processing sand and gravel quarried at the site, Holme also use the plant to recycle sand. While this currently accounts for only a small proportion of production, the company is aiming to increase it to around 40% in the years ahead, and the reliability of the processing plant will be essential in allowing this to happen. To this end, the system supplied by Weir Minerals incorporates a trash screen to treat the overflow from the initial feed sump; this removes any polyurethane or unrecyclable light particles from the waste water.
Ron Blazer, process design manager with Weir Minerals Europe, said: ‘We worked closely with the site team at Holme from the initial design and specifications right though to installation and testing to ensure the system would deliver on every goal.
‘From the enquiry landing, it took us just 12 weeks to complete the installation. Considering the size and complexity of the system, we’re proud of this achievement.
‘For an independent sand supplier such as Holme Sand & Ballast LLP, reliability and efficiency of production are critical as they directly affect the bottom line of the operation, affecting how competitive and profitable the business is able to be.
‘We take a great pride in delivering whole processing systems that have the engineering and build quality to improve our clients’ productivity, and our service team will continue to support Holme in the years ahead to ensure that the plant continues to deliver optimal performance.’
Trevor Poole, managing partner at Holme Sand & Ballast LLP, said: ‘I am very glad that we entrusted the delivery of the sand plant to the Weir Minerals and Linatex team. I dealt with a small number of professional engineers who really knew their stuff and listened to me as a customer to deliver exactly what we wanted.
‘Our previous experience with hindered-settling tanks from another supplier led us to believe that we needed a more heavyweight solution to lignite removal at Masters Pit and so we specified the Weir Minerals solution above other options.
‘We now have premium-quality engineered sand products that are quality assured by both ISO 9001 and CE Level 2+ compliance – not bad for one of the smallest sand suppliers in the business.’
- Subscribe to Quarry Management, the monthly journal for the mineral products industry, to read articles before they appear on Agg-Net