New Coating Plant For Cowieslinn Quarry
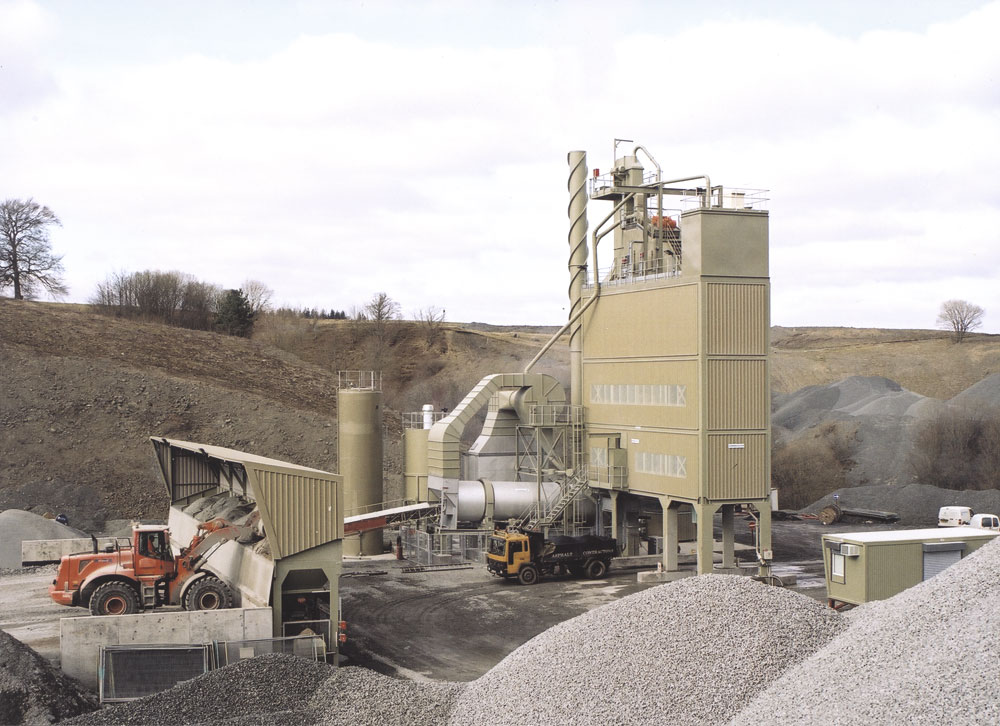
RMC choose Benninghoven for Scottish Borders site
According to its operators, the newly installed Benninghoven coating plant at RMC Scotland & North East’s Cowieslinn hard rock quarry near Peebles in the Scottish Borders is currently exceeding all expectations. Located just 14 miles south of Edinburgh’s city bypass, the new plant complements the company’s existing coating facility in Leith, which was also supplied by Benninghoven.
Indeed, it was the proven performance of the plant at Leith that was a significant factor in RMC’s decision to work with Leicester-based Benninghoven UK Ltd on the Cowieslinn project.
‘Benninghoven have exceeded our expectations in terms of erecting, commissioning and on-line operational time scales, with plant productivity proven to the original specification,’ commented Iain Haldane, regional managing director of RMC Scotland & North East.
‘Feedback from our strategic alliance partner, Scottish Borders Council, has proved positive with excellent comments received from our customer base. This is of paramount importance to our business as we continue to strengthen our reputation of being a proven supplier of quality products and service catering for small sole traders to medium-to-large customers. We aim to exceed the expectations of all our customers on an ongoing basis through continued improvement and their valued feedback.’
To achieve their production and environmental criteria at Cowieslinn, RMC opted for a Benninghoven EBA 2000 ‘Continental’ asphalt plant capable of producing up to 160 tonnes/h at 5% initial moisture.
The plant’s aggregate feed system comprises seven cold-feed hoppers, each of 9.5m3 capacity, with the two sand hoppers equipped with 10mm UHMWPE liners and vibrator motors (fig. 1). All the hoppers are fitted with variable-speed belt feeders that deliver correctly proportioned aggregate mixes on to a 30m long collecting conveyor. This in turn feeds an 18m long inclined conveyor equipped with quick-release, canvas-type dust covers and safety pull wires (fig. 2). The entire cold-feed arrangement is enclosed on three sides and covered with a roof to prevent moisture ingress.
The inclined conveyor delivers the aggregates to the dryer drum, a 9m long x 2.2m diameter friction-driven unit fitted with Benninghoven high-efficiency lifters and 70mm thick rock wool insulation with aluminium cladding. These features, together with the well proven Benninghoven Rax-Jet Turbo oil burner, provide high levels of drying efficiency with minimum fuel usage (fig. 3).
A twin-chain vertical bucket elevator, equipped with back-stop and inching facilities, transports the hot aggregates from the dryer discharge to a six-deck screen driven by externally mounted twin vibrator motors, thereby allowing high-temperature mixtures to be produced (fig. 4). The screen’s front discharge assembly is fitted with replaceable Abro liners and mounted on wheels and tracks, thus allowing it to be pulled back to give easy access for screen mesh changes. Access to the back end of the screen is by a folding door arrangement.
Mounted on top of the screen housing is a scavenging fan which extracts dust created by the screening process and delivers it to the plant’s dust collector, while also maintaining a negative pressure throughout the mixing tower.
Mounted below the screen is a 120-tonne hot-stone storage unit comprising seven bins in total — five hot aggregate bins and a split sand/fines bin; these are selected by a remotely operated diverter door. The bins are insulated with 150mm thick mineral wool insulation and aluminium cladding and each compartment is fitted with a continuous level indicator. The two sand/fines bins also have temperature probes (fig. 5).
Accurate weighing of ingredients is performed by separate load-cell-mounted weigh hoppers, comprising a 2,000kg capacity vessel for aggregates, a 300kg vessel for filler and a 200-litre vessel for bitumen.
Aggregates and bitumen are gravity fed from their respective weigh hoppers to the mixer, while filler is delivered to the mixer via a screw conveyor (fig. 6). Reclaimed and imported fillers are stored in two 40m3 capacity silos that are integral to the mixing tower and fitted with screw conveyor feeds to the filler weigh hopper (fig. 7). A paddle-type wet dust conditioner has also been supplied ‰ to cope with any excess reclaimed filler.
The plant’s paddle mixer unit comprises a 2,000kg twin-shaft mixer incorporating the latest Benninghoven paddle arms, tip and liners, all designed to significantly improve wear rates. Mounted below the mixer outlet is a secondary door which acts as an anti-drip device for direct truck loading (fig. 8).
The mixing tower is fully sheeted up to screen level to minimize noise and emissions and to improve the structure’s aesthetics
(fig. 9).
The plant is equipped with a 52,000Nm3/h dust-collection unit with pre-skimmer device for coarse dust separation (fig. 10). This system achieves particulate emissions of less than 20mg/m3, with all coarse dust collected by the pre-skimmer being returned to the vertical elevator feed boot, while fine dust from the dust collector is pneumatically blown to the reclaimed filler silo.
Benninghoven also supplied a granulate addition unit comprising a 30m3 capacity storage silo with load-cell-mounted weigh hopper and blow line to the cyclone collector mounted above the filler feed screw to the mixer (fig. 11).
The entire plant is controlled by the latest Benninghoven Online Batcher 3000 computer control system featuring a 500-recipe storage capacity and fault-diagnostics facility, all housed within a modern control room with exterior profile cladding, large windows with roller blinds and air-conditioning for improved operator vision and comfort (figs. 12 & 13).
All the equipment was supplied, installed and commissioned in compliance with current CDM and UK health and safety directives, with Benninghoven UK Ltd taking the lead as principal contractor during the construction phase.
Acknowledgement
The editor wishes to thank Rod Bishop of Benninghoven UK Ltd and Iain Haldane, regional managing director of RMC Scotland & North East, for their assistance in preparing this article.