Breedon Group boost efficiency at North Cave
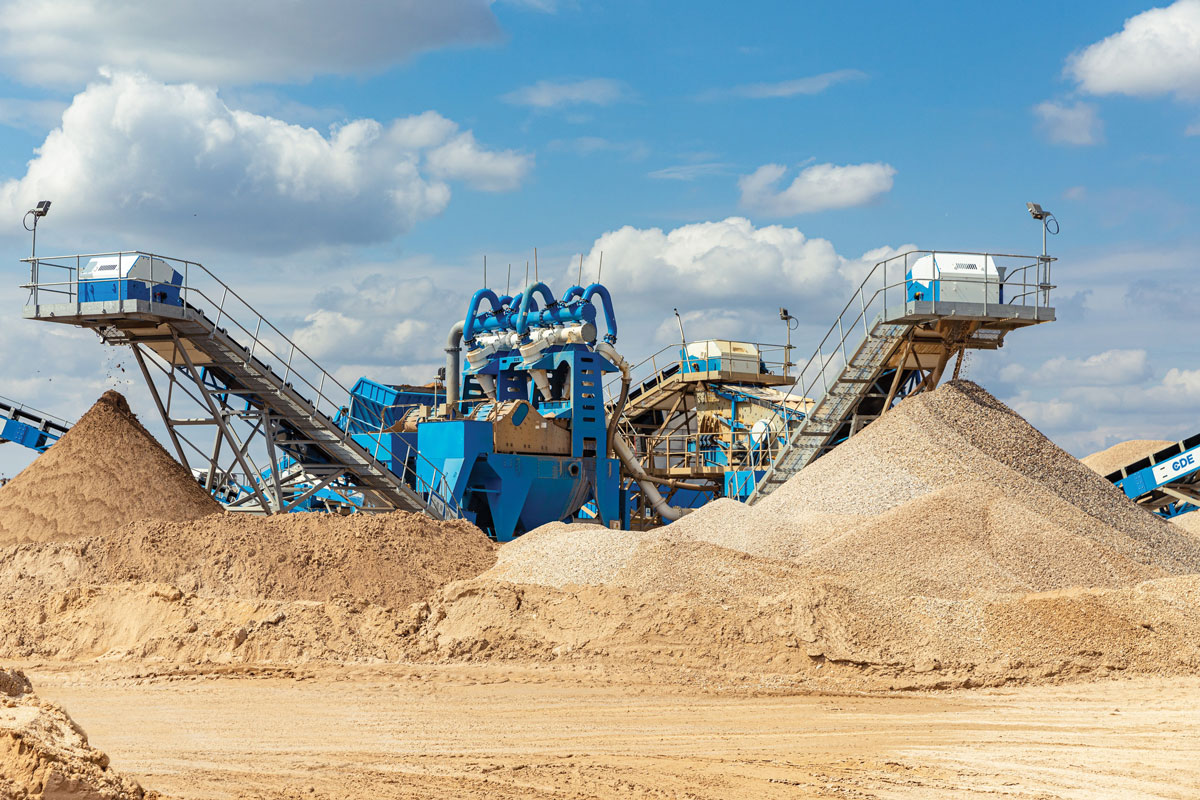
First published in the November 2021 issue of Quarry Management
CDE solution replaces three existing plants and boosts efficiency by 60 percent
Breedon Group, one of the leading suppliers of construction materials throughout the UK and Ireland, commissioned a new state-of-the-art wet processing solution from industry specialists CDE in 2020 to maximize efficiency at their North Cave Quarry and accelerate the adoption of long-term sustainable working practices within the extractive industry.
When Breedon Group acquired North Cave Quarry in 2017 they inherited three existing plants at the site which continued to operate for several years, but according to John Neesham, area general manager at that time, inconsistencies in product specification across the multi-plant operation restricted growth.
‘We were extracting from two different sites at North Cave and running the material through three different plants. Our biggest challenge was consistency in material output,’ he said.
‘When we acquired the site, our long-term vision was to streamline its operation in a way that successfully aligned the group’s commercial and environmental objectives. By consolidating the three plants into one solution, we could minimize our environmental impact while simultaneously reducing operating costs and ensuring the production of premium, consistent products.’
He added that Breedon Group have an obligation to limit their environmental impact and fulfilling that obligation will sustain the business going forward.
‘In order to successfully deliver on our purpose to make a material difference to the lives of our colleagues, our customers, and our communities, we – the extractive industry – must adapt. Adapting to better ways of working ensures we maintain a competitive advantage. It protects our licence to operate over the longer term. These are developments that are welcomed not only by the sector but by the communities we operate in.’
Synergy
A competitive tender process was launched, and Breedon Group engaged with a selection of manufacturers for the project.
‘Some couldn’t provide what we wanted at all,’ said Mr Neesham, ‘but CDE proposed more than just a solution that would deliver the positive results we were after, they proposed a partnership with a supplier that shared similar values.’
David Kinloch, director of business development for the UK and Ireland at CDE, said a detailed site audit and tests on the feed material were necessary to propose a solution tailored to Breedon Group’s site-specific needs.
‘When CDE were invited to tender for this project, we sat down with the team at Breedon Group to better understand their requirements and what they wanted to achieve. A lot of time was spent on site evaluating the three existing plants to see where the inefficiencies were and analysing material to inform the design of our solution.’
According to Mr Kinloch, CDE’s ‘unrivalled process knowledge combined with experience’ offered Breedon Group confidence in their investment.
‘We were able to demonstrate our technical ability alongside proven solutions that are delivering for our customers. The results speak for themselves, but underscoring any successful project is a successful partnership. Synergy between our two companies and a collaborative design process provided Breedon Group with the reassurance that CDE are fully committed to the project,’ he explained.
CDE solution
Using their unique co-creation approach, which places the customer at the centre of every stage of the project, CDE worked in collaboration with Breedon Group to design and engineer a wet processing solution that would allow the business to achieve its commercial and environmental objectives.
CDE proposed a 400 tonnes/h sand and gravel washing system designed using proven and extensively engineered modular components. A static system, the solution offers all the same flexibility and capabilities of CDE’s modular approach.
‘The plant offers the same unrivalled access of a static wash plant but with the benefits of modular components connected through a system of static conveyors. This means the plant can be easily relocated in the future,’ said Mr Kinloch.
The new system combines all washing operations following the installation of an R4500 primary scalping screen to handle the site’s difficult and complex feed material.
Oversize material (+50mm) is isolated and removed by the R4500, while –50mm material continues to a ProGrade rinsing unit which produces three washed aggregate fractions with all –4mm material being captured in its integrated sump. The –4mm material is processed by two EvoWash units, which remove the silts and clays and produce two clean finished sand products.
The plant also features CDE’s OptiMax technology, the latest addition to CDE CORE – an innovative range of technology solutions developed to give customers greater control of their plant. CORE uses automation and sensors to monitor and enhance productivity, minimize downtime, automate processes, and reduce operating costs, whilst maximizing profitability.
The results
The plant is currently producing five variable-sized clean products, including two sands (0–2mm and 0–4mm) and three aggregates (4–10mm, 10–20mm and 20–40mm).
According to Jonny Danby, territory sales manager for Breedon Group, the plant offers variety and consistency.
‘We’re producing two main types of sand: a 0–2mm building sand, which is used for concrete batching plants and paving; and a 0–4mm coarse sand. We’re also producing three aggregates: our 4–10mm is generally used for pipe bedding, our 10–20mm Yorkshire Cream is earmarked for the decorative market, and our 20–40mm oversize product is used for restoration works in the wetlands.’
Commenting on the consistency of the product, quarry manager Patrick Tighe said there had been zero non-conformities from the company’s technical department.
‘We’re producing a consistent, in-spec material every week. The cleanliness of our 20mm product is over and above the original specification required. Our customers are extremely pleased with the grading of the products and how we’ve significantly reduced our moisture content from around 18% down to approximately 9–10%.’
The new CDE turnkey solution is Breedon Group’s first direct purchase, although the company has acquired several other CDE plants through various acquisitions of other quarrying companies in previous years.
‘Working with CDE has been an exceptional success – from initial presentations, through the procurement process, installation, and the final commissioning,’ said John Neesham.
‘The new wash plant has had a transformational effect on the aesthetics and operational efficiency at North Cave Quarry. It has given us exactly what we wanted. It has reduced our footprint and reduced our energy requirements by 40%. At the same time, it has increased our profitability, minimized maintenance costs, and increased operational efficiency by around 60%.’
He added that the efficient solution allows Breedon Group to reduce their environmental impact too.
‘By consolidating the three plants, we’ve significantly reduced our energy consumption and carbon emissions at the site. We’re also recovering higher volumes of material and at a higher specification. By maximizing output and material retention we can extend the life of the available reserves at North Cave.’
David Kinloch concluded: ‘We are proud of the results that have been realized together for Breedon Group at North Cave. The company sought to consolidate its wash plant operations, whilst increasing production throughput and reducing operational costs on site. The new system at North Cave was designed with both objectives in mind. Our engineered solution is delivering positive results for the company and provides them with the technology and infrastructure to continue operating efficiently long term.’
- Subscribe to Quarry Management, the monthly journal for the mineral products industry, to read articles before they appear on Agg-Net.com