New TWS Washing Plant for R Collard
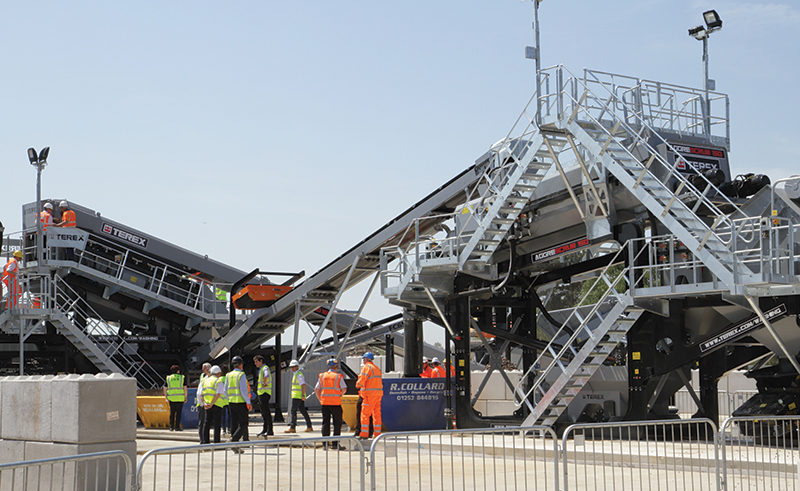
First published in the October 2015 issue of Quarry Management as Enhanced Washing
R Collard open new aggregate washing plant as part of a major investment programme to improve their recycling efficiency and environmental performance
Formed in 1994, R Collard Ltd have evolved to become one of the most prominent names in the recycling, demolition and construction products markets in the south of England.
With many of their customers operating in a more eco-friendly manner, the company has seen a huge demand for recycled aggregates and waste-management services on local projects.
This has prompted R Collard to embrace the latest technological developments and enhancements to further reduce their own energy usage, carbon footprint, and that of their customers.
Making an important contribution to the environment by minimizing the need to quarry for virgin materials, the company processes waste concrete, stone and hardcore into high-quality recycled aggregate materials as part of its ‘zero to landfill’ commitment. Some of the materials produced include: 10mm, 20mm and 40mm aggregates; as well as washed sharp sand suitable for floor screeding and block paving.
Earlier this year R Collard opened a new aggregate washing plant as part of an ongoing major investment plan. Located at the company’s Eversley recycling site in Hampshire, the system – designed and supplied by Terex Washing Systems (TWS) – will provide a local source of high-grade recycled aggregates to local construction and civil engineering projects across southern England.
Demonstrating their commitment to sustainability and continuous improvement, the washing plant represents a £2 million investment by R Collard and was installed and project managed by DUO.
With a maximum rated capacity of 120 tonnes/h, the plant is expected to process up to 250,000 tonnes of waste concrete and hardcore collected from local construction/demolition projects each year for use on a number of regional developments, including: the M3 ‘smart motorway’ project; M4 widening scheme; and Bracknell town centre regeneration.
Robert Collard, founder and managing director of R Collard, commented: ‘Transport is a major contributing factor in the cost of aggregates so the investment in this plant is a direct response to increasing demand for high-quality recycled products within our catchment area in the South East. The technological refinements will allow us to process more waste materials than we’ve collected before and create a truly closed-loop recycling system for construction waste in the south of England.’
TWS specialize in recycling processes that transform construction and demolition waste into clean, homogenous recycled products and the new plant for R Collard boasts a number of advanced features which achieves exactly that. These include: cyclone technology that produces a high-grade coarse sand product with <2% silt content; integrated sorting systems that remove non-mineral contaminants so more waste is used as feedstock; and a new feeder system which can process cohesive material even when moisture content changes.
It was also important for R Collard to operate a bespoke system in line with their ongoing policy of delivering good sustainable practice – and to meet these requirements TWS and DUO have ensured the plant takes an innovative, efficient and cost-effective approach to processing waste materials into valuable commodities.
The wash plant set-up comprises: scalping (Powerscreen Warrior 1400); aggregate rinsing and sand washing (AggreSand 165); aggregate scrubbing and sizing (AggreScrub 150); and water treatment (thickener) and recycling (filter press).
The process begins with the Warrior 1400 heavy-duty scalping unit removing excess oversize and then passing the bulk of material to the washing equipment. Particularly suited to claggy and clay-contaminated/high soil content feeds, the 1400 scalper incorporates a specially located magnet that extracts ferrous metals in free fall before material is transferred to the AggreSand 165 wash plant.
The AggreSand unit is equipped with a 16ft x 5ft three-deck screen that produces clean 50mm and oversize for subsequent crushing, while the mid- and bottom-deck outputs are delivered to the AggreScrub 150 for attrition and sizing.
Designed specifically for the C&D recycling market, the AggreScrub 150 plant was chosen for its ability to effectively scrub aggregates and float out clays/silts/lights (wood/plastics) on one chassis. As well as its floatation capabilities, the AggreScrub is designed to liberate adherent clays by heavy attrition, producing ‘organic-free’ aggregates for a wide range of construction requirements.
Another key feature of the AggreScrub unit is a 12ft x 5ft two-deck rinsing and sizing screen, which uses high-quality polyurethane decks to grade the final aggregate splits, as specified by R Collard.
Any underflow from the AggreScrub’s integrated trash screen and aggregate sizing screen is collected and pumped back to the AggreSand 165 unit for recovery of any saleable material and to deliver efficient water management.
The AggreSand system produces two high-quality sand products (from the recycled feed material) suitable for use in concrete, pipe bedding and construction applications. Sand and water from the AggreSand screen, together with the collected water and fines from the AggreScrub, are recovered via the integrated hydrocyclones, producing coarse and fine sand fractions. These are dewatered by the system (12% moisture content), providing clean, ready-to-handle materials for stockpiling.
All dirty water flows from the cyclones to the congruent water-management system, where polyelectrolyte (flocculant) dosing is carefully controlled on a batch basis via an 8m rake thickener with automated monitoring. Suspended solids coagulate and sink to the bottom of the thickener and are drawn to the central outlet by constantly rotating rakes. This thickened mud is pumped into a large homogenizing sludge buffer tank, while clean recycled water overflows from the thickener to a storage tank.
A high-frequency screen featuring a fine steel mesh is installed between the thickener and the water tank, removing any residual organics and floatable contaminants (eg polystyrene balls).
Sludge from the buffer tank is delivered to a 150 plate (2m x 1.5m) filter press by a powerful double centrifugal pump (at up to 16 bar pressure). This, effectively, reduces waste output to a highly compressed, low-moisture content by-product which can be easily handled and removed from the site.
The thickener and filter press combination recycles around 90% of the water used in the plant, preserving precious water resources and allowing R Collard to operate a highly productive and efficient processing system that uses only 30m3/h of water.
For more information visit: www.terex.com/washing
- Subscribe to Quarry Management, the monthly journal for the mineral products industry, to read articles before they appear on Agg-Net.com