Mining Waste Directive
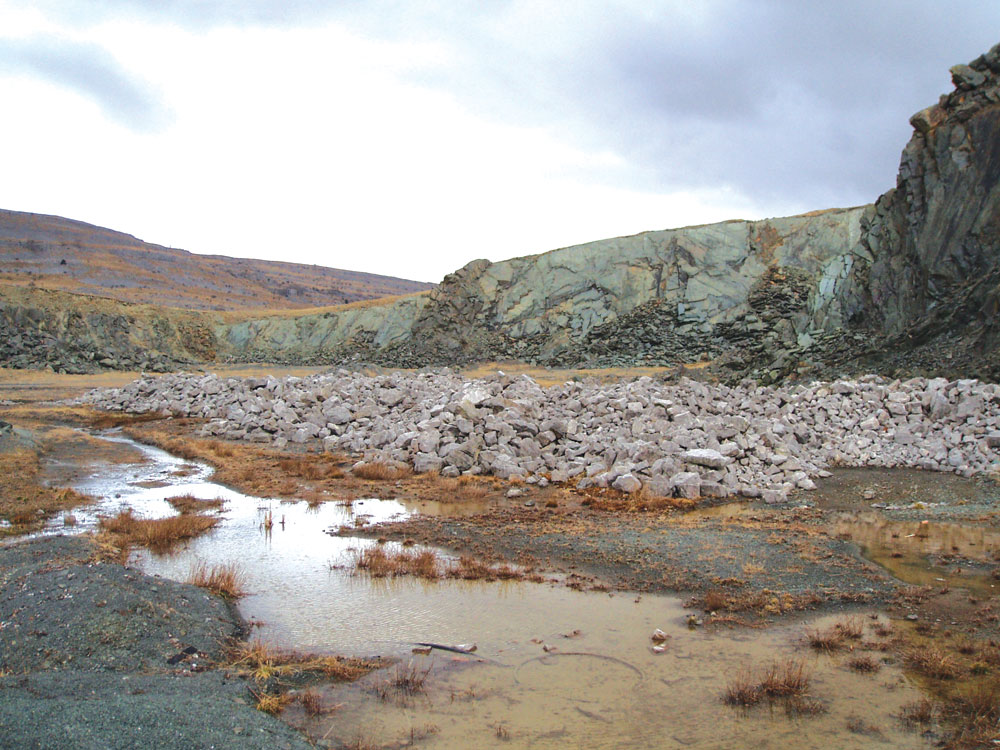
What every quarry manager needs to know
By Paula Coopland, waste manager, Golder Associates (UK) Ltd
Do you have overburden/spoil heaps on your site, or maybe a settlement lagoon? Do you consider that you are not generating waste? Then think again.
In its simplest form, waste is something you intend or are required to discard. It should not be assumed that because you think you have not discarded something, the regulator will agree with you, as ‘discard’ is described by the European Court of Justice as having ‘special meaning’.
European Union Directive 2006/21/EC on the management of waste from the extractive industries (the Mining Waste Directive), requires member states to introduce measures, procedures and guidance to prevent or reduce, as far as possible, any adverse effects on the environment and any resultant risks to human health brought about as a result of the management of waste from the extractive industries. It applies to waste resulting from the extraction, treatment and storage of mineral resources (hereinafter simply referred to as ‘waste’). It does not apply to waste from offices, canteens, oil from machinery servicing etc.
You may be able to provide evidence that you are not generating waste. This may be, for example, in the form of planning submissions that clearly identify all the residues that will be used to backfill a void, for example. A guarantee that these residues will actually be used for this purpose and the timeframe for use may also be required.
Until regulations are in place, there are numerous questions without answers. However, operators who start looking at the minimum requirements in the Directive now could save themselves considerable expense in the long term.
If you generate waste you will need to produce a waste-management plan and review it every five years. These plans should not be too onerous – much of the information is likely to have been submitted in support of planning applications, but it may need to be updated or reformatted. As far as the regulators will be concerned, quality is likely to be looked upon more favourably than quantity (the submission of irrelevant information will simply add to the regulatory burden and slow down the processing of waste-management plans. It could also cost the operator more in the long term if the regulators have to increase the charges to cover the cost of extracting the relevant information).
You may be operating a ‘waste facility’, in which case you will also need to provide a financial guarantee or equivalent. Operations with these facilities are required to be regulated more rigorously than those without, essentially as there is a greater risk to the environment and humans.
Without going into too much detail, a ‘waste facility’ is an area where extractive waste is deposited, stored or treated either in liquid (including suspension or solution) or solid form for more than a certain period of time. The period of time varies according to the classification of the waste – whether it is hazardous, non-hazardous or inert. Again, it is related to the potential for the waste to impact on the environment and humans.
You are likely to have a ‘waste facility’ if you have a coal discard dump or tailings lagoon that is in use for more than a year. Similarly, if you have not agreed with your regulator that your overburden is not waste, if it is inert and stored for more than three years, it is likely to be a ‘waste facility’.
The most strictly controlled sites will be those with a ‘Category A’ facility. In addition to waste-management plans and financial provision, you will need to provide major accident prevention plans. This classification will apply to facilities dealing with hazardous waste or dangerous substances above certain thresholds. In addition, and possibly of more significance to UK operators, it will apply to facilities where a failure or incorrect operation could give rise to a major accident – be it for inert, non-hazardous or hazardous waste. If this looks likely to apply to your site, it may be time to look at redesigning or relocating facilities. It is up to you to show that in the event of an incident, the impact on human and environmental receptors will not be ‘major’.
Another thing to look out for is how the Directive will be implemented where your operations are located. It looks likely that the mechanisms for implementing the Directive in Scotland, England and Wales will be different, so any guidance or articles with ‘UK’ or ‘national’ in the title should be treated with caution.
Inevitably, this article only covers a snapshot of the requirements of the Directive and the potential impacts it may have on operators. While it is no substitute for reading the Directive and the forthcoming regulations, hopefully it will inspire quarry managers to take a look for themselves and seek advice on how to minimize its impact.
The views of the author are not necessarily those of Golder Associates (UK) Ltd or Quarry Management.