Collard Group invest in modular waste-processing plant
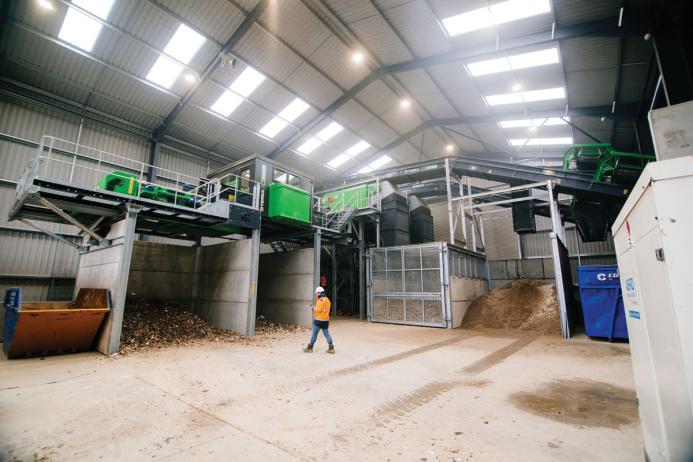
First published in the October 2023 issue of Quarry Management as Raising the Bar
Molson Group supply high-performance modular waste-processing plant to Collard Group
The name Rob Collard is well known in motor racing, particularly in the British Touring Car Championships. Having won the Independent’s Cup title in 2003, he continues to compete at the highest level in the sport.
However, many people are unaware that Rob Collard also runs a highly successful waste-recycling and demolition firm and has done so since 1995. Headquartered in Eversley, Hampshire, Collard have rapidly become one of the most prominent names in the construction products and recycling markets in the south of England.
Since its inception, the company – founded by managing director Rob Collard – has grown and diversified into one of the largest privately owned national demolition contractors and waste-management businesses in the UK, with more than 400 employees and a turnover in excess of £70 million per year.
Operating from nine strategically located recycling centres across five counties in the UK, Collard process over one million tonnes of waste materials every year and have recently taken massive strides in recovering a higher percentage of construction, demolition and excavation (CD&E) waste, enhancing their recycling rates, and improving the quality, reliability, and grading of recycled resources.
The company’s recycling facility in Reading, for example, has recently been upgraded with a state-of-the-art and what is claimed to be an industry-first waste-processing plant designed to increase the ability to segregate materials in a faster, more efficient manner.
Sourced through Molson Green and manufactured by Terex Recycling Systems, the installation of the new plant has been hailed by Lee Phelan, managing director of Collard’s waste and recycling division, as a huge step forward for both the company and the wider environment.
‘Here at Collard, we are great believers in the circular economy and have a drive to deliver just that for ourselves, our customers, and the wider environment,’ he commented. ‘We have been recycling materials for more than two decades, but as technologies have advanced, we have invested heavily in these to ensure we consistently meet a 98% landfill diversion rate across the group.’
The new Terex modular recycling plant has been designed to fit into a combination of an existing shed and a newly built shed, with the aim of increasing Collard’s recycling and segregation capabilities on site.
A key factor in the selection of Molson and Terex to deliver the waste-recycling solution was their ability to customize the new plant to suit the specific characteristics of the feed material and understand Collard’s requirements going forward.
‘There was a lot of going backwards and forwards to get the specification and designs just right,’ said Mr Phelan. ‘The result is a plant that not only exceeds our current throughput requirements, which has not only future-proofed our business, but is also capable of segregating material even more productively and accurately than we have done before. While part of our requirement was the increased segregation of material, we also wanted to reduce the amount of labour-intensive segregation we have undertaken in the past.’
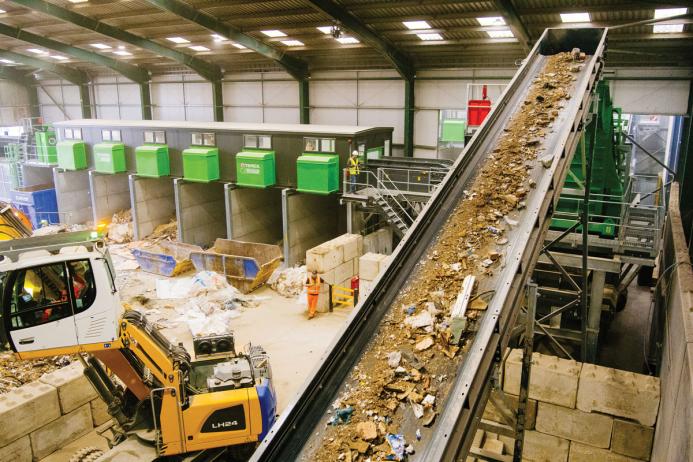
With Collard’s own specifications and design of the waste-segregation facility agreed, Terex commenced the building of the bespoke processing plant with various major equipment items delivered to site in November 2022. The entire construction/installation process of the new waste-recycling solution was supervised by Carl Longhorne, senior operations manager at Molson.
With the original waste-sorting plant still in operation during the build process, the Molson engineering team had to work around the ongoing operation at Collard’s Reading recycling depot and did so successfully, delivering a completed plant ready for operation in February this year.
‘It was a tight squeeze at some points with the constraints of the building and the recycling work still going on,’ said Mr Longhorne. ‘But both parties had an end goal to get the plant up and running and we worked together to deliver just that.’
To meet Collard’s specific output requirements, pre-sorting of incoming material (using a 13-tonne excavator) and selector grabs takes out some of the larger waste items before a dedicated material handler loads the new recycling plant with the remaining material.
A conveyor system transports the waste material to an inclined Spalek screenbox, where various grades of feed material are separated. The waste is subsequently diverted in two directions, with 100–300mm fragments transported to a state-of-the-art, brightly lit and heated picking station, where operatives will pick out wood, paper/card, plastics, metals, and general waste, whilst remaining materials (eg ferrous metals) are taken out with an overband magnet.
Light material is separated with a blower into a cage and heavier waste is sent to a bay outside the shed for onward crushing. Smaller materials separated at the Spalek are split into three sizes: 0–10mm; 10–50mm; and 50mm–100mm.
These streams pass through an overband magnet to remove any ferrous metals, with materials classed as fines dropping straight into their own dedicated bay. A pair of Westeria air separators remove the ‘lights’, with the final quality-control station taking out smaller items of wood and other materials. Finally, an eddy current separator removes any non-ferrous metals from heavy waste material such as tile, brick and stone, which are transported to a separate heavy bay.
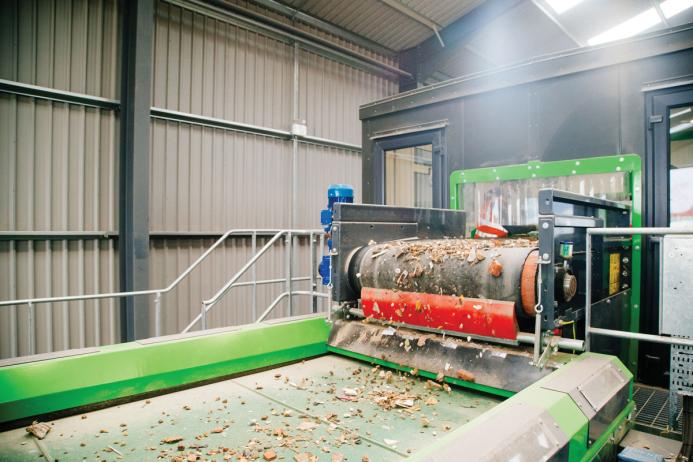
The new Terex waste-processing plant gives Collard up to 10 different end-products, all of which can be further recycled, enabling maximum processing of various waste recyclables and reducing the environmental impact of using primary aggregates.
‘We are using some of the heavy materials once they are processed, they are added to our quality-assured, BSI-approved concrete,’ commented Mr Phelan. ‘We have undertaken several projects where our demolition teams have cleared a site, the waste material has gone through our recycling process, and we are able to create high-quality recycled aggregates for construction projects.’
Other materials segregated by the plant are sent out to a variety of sources, both in the UK and abroad, for final processing, strengthening Collard’s commitment to the circular economy by recycling more CD&E waste materials, and preserving natural resources and virgin aggregate.
Not only has the installation of the new Terex plant increased the range of waste materials segregated and recycled, but there has also been a positive impact on the local economy with Collard adding a further six jobs since the commissioning of the waste-processing facility.
‘One would think that the increased automatic segregation of materials would reduce the amount of labour required to complete the tasks,’ said Mr Phelan. ‘The fact that we have now increased the range of final products, along with maximizing our volume of feed material, has meant that we have had the opportunity to offer employment in the locality.’
As well as recycling more materials, Collard are reflecting on their own journey towards a more sustainable future. Reducing their environmental impact, for example, is a key responsibility for the business and the Collard team is recording and collating data to measure and actively manage their energy usage and carbon footprint.
Collard are also implementing sustainability measures to make significant reductions in energy usage and carbon emissions across their recycling depots. At their Reading site, where the new Terex plant is located, the roof of the building has been specially designed to harvest rainwater for reuse as part of an effective dust- and odour-suppression system during operation.
With the new Terex waste-recycling plant installed and working as expected, Collard are delighted with their recent investment. Mr Phelan concluded: ‘We have several waste-segregation plants from other manufacturers operating at our recycling facilities, but it was the level of detail Molson went into that made us look at the Terex product. It’s a well-known and respected brand in the crushing and screening industry and with that heritage and pedigree, along with the knowledgeable staff, it was a relatively easy decision to make.’
Subscribe to Quarry Management, the monthly journal for the mineral products industry, to read articles before they appear on Agg-Net.com