Weighty Matters: Do Screens Need to be Heavy?
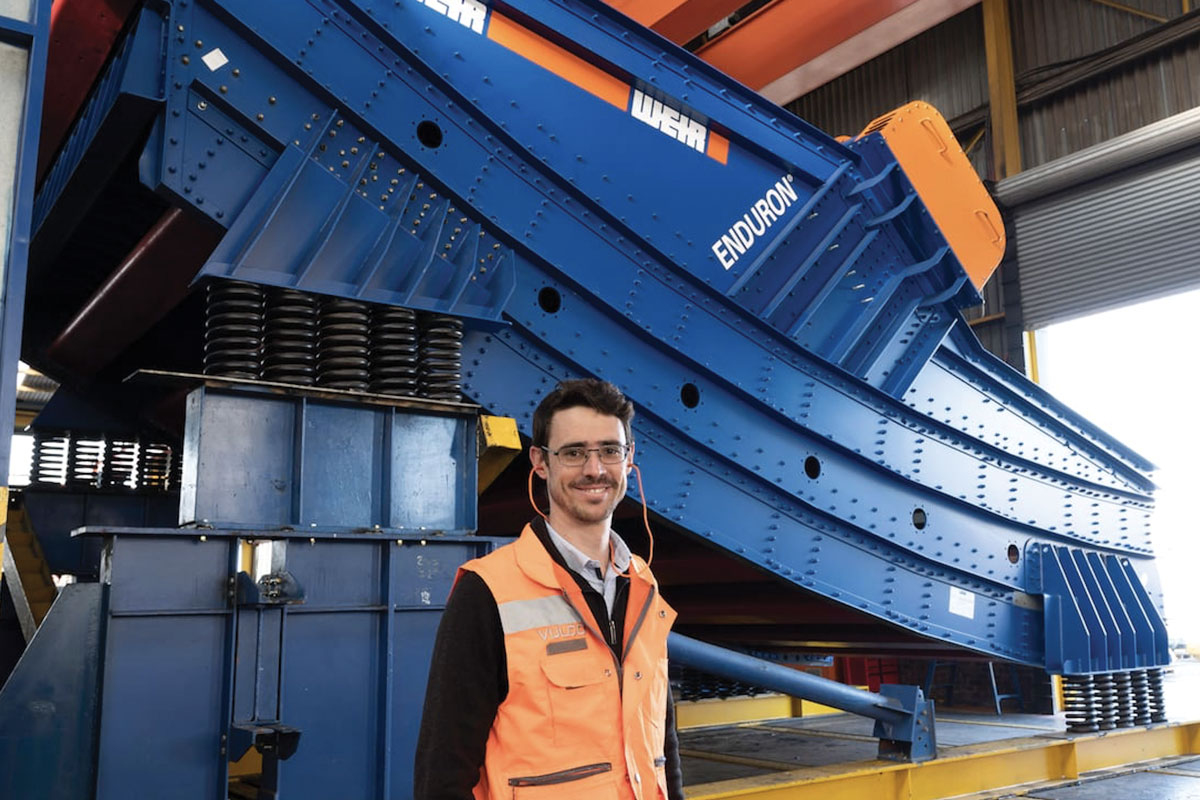
First published in the February 2021 issue of Quarry Management
With added safety features and higher-quality materials, is a heavier screen always better? The answer may come as a surprise. Steven Hunter, separation technology group leader with Weir Minerals, explains how new technology is changing the way screens are designed and built
There is an old adage about mining and quarrying equipment: ‘heavier is better’. Traditionally, engineers wanted to incorporate additional, weighty safety factors, together with the highest-quality materials, to guarantee a robust and long-lasting solution. Whilst this line of thinking is, perhaps, more acceptable with regard to certain types of equipment, such as pumps and valves, when applied to screens it has often resulted in exceptionally heavy units that are over-engineered in all the wrong places.
New methods are radically changing the way screens are designed. Today, digital calculations, simulations, modelling and drafting allow designers more freedom to challenge traditional designs and make use of material advancements to build screens that are more reliable, safer and efficient, without the need for unnecessary weight.
When a product’s primary function is to move – the product’s own mass is always a drawback. The airline industry is a prime example; a lighter plane will always outperform a heavier model. Considerable effort is made on every new design iteration to ensure that airliners are made as efficient as possible by removing unnecessary weight.
Until now screen manufacturers had been unable to capitalize on the best practices shown in other industries due to the difficulties and inertia that manual design entailed. However, as computer-aided design has become more advanced, screen designers are now empowered to make wholesale changes to their product. The introduction of computer-simulated finite element analysis (FEA) has allowed design engineers to instantly validate any design changes made, a process that was not previously possible.
The result of such progression and innovation within the field of screening is often a differently shaped and weighted product. But while these screens may be lighter compared with previous models, Weir Minerals ensure that their ‘engineered to order’ Enduron screens are as ‘as heavy as they’re required to be’, using the customer’s requirements, flowsheet and on-site data as the design’s foundation.
Without modern design tools it would be practically impossible to customize equipment so fundamentally in order to meet the needs of a specific application on a specific site. By identifying the specific features, size and wear materials required to excel in their intended application, design engineers are now free to remove weight where the screen assembly is experiencing low stresses, thus decreasing both operational and manufacturing costs. Previously, screens were built big and heavy to ensure that if anything went wrong, it would not go catastrophically wrong. It was a brute-force approach to safety, which, if used today, would produce an unnecessarily heavy screen.
Nowadays, there are a number of tools available to ensure there are no surprises when the time finally comes to physically test the equipment. Engineers run a natural frequency simulation to check that the screen will not run at its natural frequency when operated, which is vital to avoiding resonance that can cause premature failure in the equipment. A frequency response simulation is also used to analyse each design using the actual forces the screen will encounter on site (loaded and unloaded), allowing engineers to evaluate each part of the product for high stress points and reinforce the screen where it is actually useful.
At Weir Minerals these design and testing processes are extensive and carried out by a team of experts who combine experience with outside-of-the-box innovation. The team tests new ideas and design philosophy against the company’s extensive bank of proven designs and data gathered from real applications in mines and quarries around the world.
Using these tools, screens can be built that are optimized around a specific application’s actual requirements, rather than against any potential problem a screen may possibly face. This allows the screen’s weight and complexity to be reduced, which has knock-on savings in terms of manufacturing time and transport costs, as well as making installation and maintenance safer.
However, this modern approach to screen design goes beyond material reduction. The added data and evaluation allows products to be supplied that are easier to operate and maintain, more efficient, require less power and have access to alternative exciter and vibrating motor options.
Using modern design tools, expertly customized screens can provide the robust construction and vital safety features needed without any ‘excess baggage’. So, next time you compare heavy-duty screens for a job, ask yourself if they are heavy because they need to be, or if they are just heavy because no one has put in the effort to optimize them. For further information visit: www.weirminerals.com
- Subscribe to Quarry Management, the monthly journal for the mineral products industry, to read articles before they appear on Agg-Net.com