SynchroPower
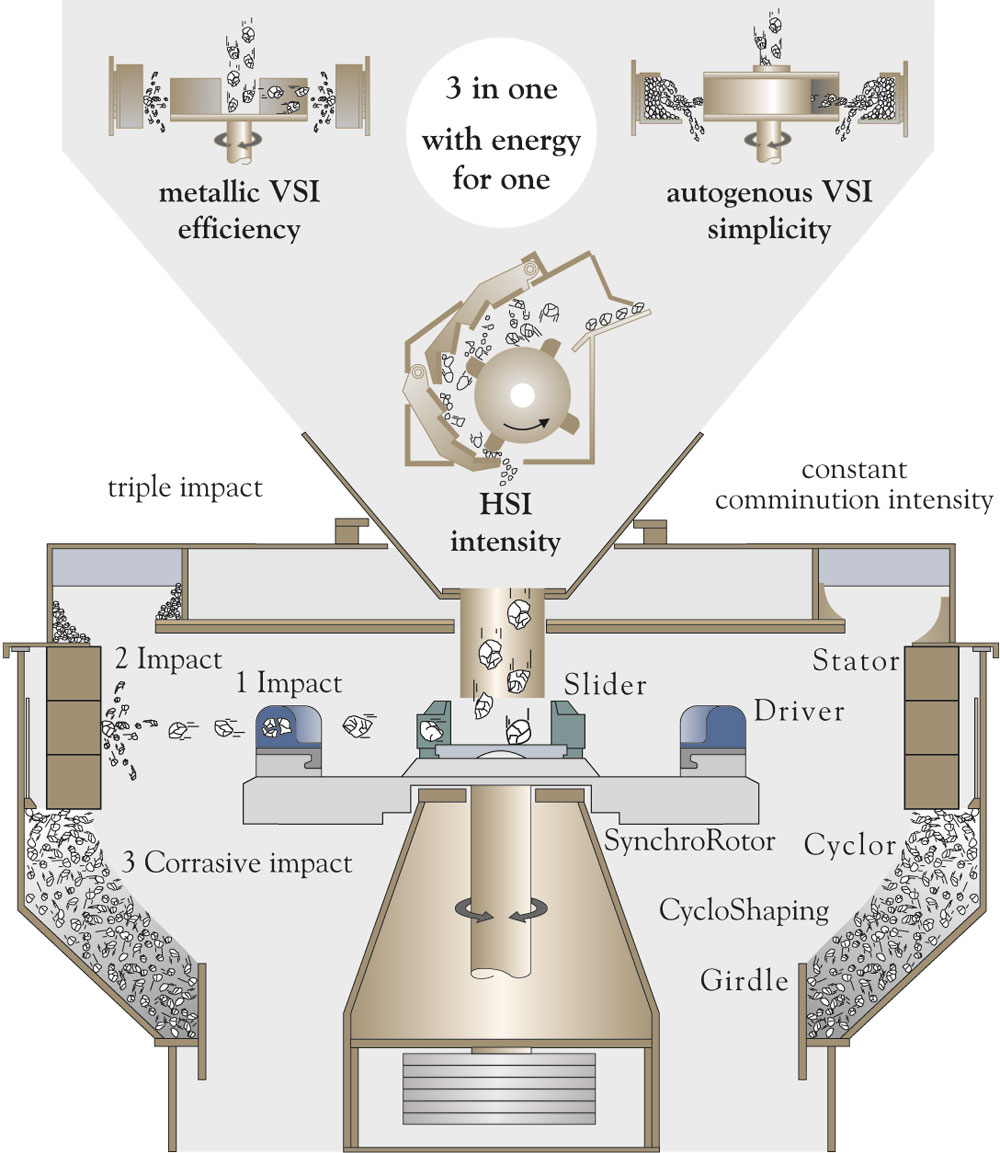
Comparing the comminution intensity of the SynchroCrusher with the conventional VSI
By Hans and Rosemarie van der Zanden
The market is constantly on the lookout for new crushing equipment that will improve competitiveness. Unfortunately, genuine new developments in comminution technology are rare.
The cone crusher is a first-rate machine but has a tendency to produce of elongate particles. The market accepted this until the stone-on-stone impact autogenous vertical-shaft impactor (VSI) was introduced. This proved to be eminently suitable for the shaping of cone-crushed material and many thousands of machines of this type have been sold worldwide for this purpose. However, the autogenous VSI is an additional expensive step in the production process, is limited to a maximum feed size of 40–50mm and tends to produce more fines and cubical particles with rounded edges, mainly due to the intense attrition generated. This can be a problem in applications where sharp-edged cubical particles are required.
This paved the way for the conventional metallic VSI that applies stone-on-steel impact. This crusher is simple and reliable and produces well-shaped, sharp-edged cubical material with a lower fines content. Wear costs are high, but in a production line this machine can replace both the cone crusher and the autogenous VSI, and can handle a maximum feed size of up to 100mm. Nevertheless, the conventional VSI also has a number of shortcomings. In particular, comminution intensity is generated with a single impact only and falls sharply when the anvils start to wear out, which happens relatively quickly. This causes fluctuations in product quality with a repetitive cycle of increasing oversize and undersize and poorer cubical shaping with each anvil exchange.
According to its designers, the SynchroCrusher is said to offer a solution to all these shortcomings in that it eliminates virtually all the problems of the conventional VSI — both autogenous and metallic — and provides many unique additional features.
THE CONE CRUSHER
The cone crusher, which works by applying pressure loading, is essentially a very straightforward and reliable crushing machine that has an almost ideal crushing chamber with low wear rates. For practical reasons, however, the design is rather complicated and therefore expensive to produce, and regardless of any sophisticated automation the cone crusher has a number of significant shortcomings.
In particular, a strong tendency to produce elongated particles makes the cone crusher less suitable (and sometimes completely unsuitable) for the production of aggregates that need to have well-shaped particles in order to obtain a close packing structure.
Particle shape
A distinction can be made between cubic-shaped particles that have sharp edges (with a rough surface texture) and those that have more rounded edges (with a smoother surface texture). Sharp-edged cubical particles, which result from impact loading, produce a stronger, more stable packing structure than round-edged particles, which result from attrition treatment. Moreover, a rough surface texture increases the bond between the binder and the aggregate surface and is often preferred for aggregate and manufactured sand for use in concrete, asphalt and roadbase applications.
THE AUTOGENOUS VSI
The Barmac autogenous VSI proved to be extremely suitable for the shaping (cubisizing) of cone-crushed aggregates and soon became very popular for this purpose and is now widely copied.
The autogenous VSI is a very simple, reliable and effective machine with a unique autogenous rotor that suffers only limited wear. However, for cubisizing purposes it involves an additional stage in the production line and has a number of shortcomings, depending on the particular application.
In the rotor housing the metered material spirals outwards in the opposite direction to the rotation of the rotor. Therefore, the direction of the material stream has to be completely reversed to be picked up by the guiding members. This creates a chaotic process of intense autogenous milling within the rotor chamber. The hard-metal tip-ends limit the maximum feed size to 40–50mm. The rock shelf surrounding the rotor provides autogenous stone-on-stone impact followed by corrasive impact motion along the autogenous bed.
Autogenous stone-on-stone impact provides only limited comminution intensity while the autogenous milling action and corrasive impact motion generate intense levels of attrition. Although producing well-shaped cubical particles, they do, however, have rounded edges, a smoother surface texture and contain a high amounts of fines (–0.063mm).
The autogenous VSI can be provided with a cascading system which is designed to reduce energy consumption and wear. Cascading is, however, a controversial issue depending on the particular application, the problem being that the centrifugally thrown (horizontal) material streams ‘scrape’ along the cascading (vertical) stream that surrounds the rotor as a falling curtain, and can therefore collide with only a part of the cascading particles. Furthermore, to obtain a reasonable result both streams have to be kept as constant as possible, which is very difficult to achieve; though manufacturers do claim to have made major improvements in this area. Cascading can be very suitable for shaping purposes but for size- reduction it often leads to an increased recirculation load.
CONVENTIONAL METALLIC VSI
The shortcomings of the autogenous VSI led to the success of the conventional metallic VSI, a very simple, reliable and cheap stone-on-steel impactor that combines a high reduction ratio with the production of well-shaped (cubical) particles and can handle feed sizes of up to 100mm (or more). The metallic VSI has become very popular because it can successfully replace both a cone crusher and an autogenous VSI, however it too has a number of shortcomings.
Rotor shoes provide effective centrifugal acceleration, but only 35–40% of the wear material can be used, resulting in 60–65% wastage. This not only has financial implications, but also restricts lifetime. Moreover, if the shoes wear through completely the holders can be severely damaged, thus strict control during production is essential.
Anvils provide only a single impact and the protruding corners cause heavy impact disturbance. New anvils generate good comminution intensity with a high reduction ratio, limited fines and sharp-edged cubical particles. However, when the anvils wear out the level of comminution intensity declines progressively, which can happen fairly quickly. This results in a sharp reduction in comminution intensity, a greater amount of fines and poor shaping.
Anvil behaviour
When the anvils are fully worn out — ie after some 35–40% of the wear material has been utilized — the comminution intensity will have dropped to about 70% of the level obtained with fresh anvils. This is a critical threshold beyond which the crusher is no longer efficient in operation [VanderZanden, 2003]. Operation beyond this critical level causes a sharp increase in the amount of oversize and undersize, as well as less well-shaped particles. Typically, this critical level is reached after seven or eight sets of four shoes have been used.
Comminution intensity
Because of the reduction in the level of comminution intensity as the anvils wear out, it is not possible to produce a product of relatively constant quality, and the options to choose and adjust this level are very limited. Furthermore, the machine is less suitable for the processing of finer material (–15mm feed size) and not at all suitable for fine material (2–5mm feed size).
The reduction in comminution intensity can be compen-sated for to a limited degree by gradually increasing the rotational velocity as the anvils wear out. This, however, increases both energy usage and the wear rate of the shoes and anvils, thereby shortening lifetime and increasing costs.
The success of the conventional metallic VSI is a remarkable phenomena because its wear costs are relatively high. This shows how much the market values factors such as sharp-edged cubical shaping, rough surface texturing, lower fines and simplicity. Nevertheless, there is no doubt that the market is still on the lookout for even better alternatives.
THE SYNCHROCRUSHER
The SynchroCrusher differs from the conventional VSI — both metallic and autogenous — in that the SynchroRotor is provided with four or five simple sliders weighing some 5–10kg each. These make a significant difference in that acceleration is now achieved by impact instead of sliding, which turns a chaotic process of single impact into a fully deterministic process of multiple impact that increases comminution intensity by some 25% and achieves this using less energy and with significantly lower wear. The SynchroCrusher could be described as the ideal alternative in that it eliminates virtually all the shortcomings of the conventional VSI (it actually turns the disadvantages into advantages) and offers a several unique additional features.
Of most importance is that the deterministic multiple (double or triple) impact generates a much higher level of comminution intensity that stays constant as wear progresses and can be carefully chosen and accurately adjusted within very wide limits. This makes the SynchroCrusher suitable for effectively processing a wider range of materials than any other crusher. Furthermore, determinism allows for very efficient utilization of the wear material: up to 50–60% for the drivers and 70–75% for the stator.
Extensive comparisons have been made between the SynchroCrusher and the conventional metallic VSI that show that the SynchroCrusher produces about 10% more net product while using around 20% less wear material, some 10% less energy and about 25% fewer wear-part exchanges [VanderZanden, 2003].
Reinforced drivers
Care has to be taken that to ensure the metallic drivers, which provide co-rotating
impact, are strong enough to withstand the combination of high centrifugal forces (150–250kN) and heavy impact loading.
For particles larger than 40–50mm it is necessary to construct the drivers in a reinforced composite form with a steel reinforcing plate, which allows for the processing of feed material up to 100mm in size. This reinforced composite is somewhat more expensive but makes it possible to effectively utilize much more wear material and avoid damage to the holders when the drivers wear through completely.
SynchroPrinciple
The SynchroRotor applies the SynchroPrinciple in that the position of the spiral flight path between the slider and the driver is invariant and therefore not influenced by the rotational velocity. This makes it possible to carefully choose and accurately adjust the co-rotating impact velocity. Primary impact proceeds undisturbed and the level of comminution intensity generated stays constant as wear progresses.
Stator principle
The Stator principle makes it possible to avoid protruding anvils because the straight flight path of the centrifugally thrown particles moves increasingly in radial direction. Therefore, when the stator is located at a far enough radial distance, material collides against the stator surface at an optimum angle (about 75°). In this way secondary impact proceeds undisturbed.
A stator requires a wide-body design but has the additional advantage that it allows for the use of a cyclor, thereby providing tertiary impact.
SynchroCrusher
Both the SynchroRotor and the SynchroCrusher can be configured in many different ways and some direct practical applications are shown here. Each configuration (either small-body or wide-body) can be provided with either a metallic or an autogenous SynchroRotor.
SynchroRotor
The SynchroRotor can be super-symmetrical for two-way operation. This, together with reinforced composite drivers that can wear through completely without causing any damage to the rotor, allows for fully automatic operation.
Metallic SynchroRotor
During co-rotating impact particles are simultaneously accelerated and very efficiently loaded in a fully deterministic (undisturbed) way. With similar energy consumption co-rotating impact loading alone generates a comminution intensity that is, on average, close to that generated by a conventional VSI fitted with an anvil ring (at higher rotational velocity, which increases both the energy consumption and wear rate, the comminution intensity of the SynchroRotor can be increased to a level similar to or greater than the conventional VSI).
Contrary to the conventional VSI, with the SynchroRotor the level of comminution intensity stays constant as wear progresses. Furthermore, the SynchroRotor utilizes wear material much more efficiently. The savings obtained are about equal to the amount of conventional VSI anvil throw-away material, ie some 60–65% of the anvil volume.
Metallic SynchroRotor with stator
A SynchroCrusher equipped with a stator requires a wide-body design and, on average, generates (with similar energy consumption) about 20% more comminution intensity than a conventional VSI equipped with an anvil ring, which stays constant as wear progresses. Most of the comminution intensity (about 70%) is generated during co-rotating primary impact. Secondary stator impact adds some 30%, where the already (partly) broken and, therefore, finer particles create significantly lower stresses and a lower wear rate compared with the conventional VSI. Furthermore, up to 70–75% of the stator volume can be utilized as against 35–40% for the anvils. Together this increases the life of the stator to about 2.5 times of that of an anvil ring in a conventional VSI. In addition, the stator allows for the use of a cyclor for tertiary corrasive impact motion (triple impact), which further contributes to comminution intensity in that shaping is further improved. The result is a high reduction ratio and a crushed product of superior quality with low fines and well shaped (sharp-edged cubical) particles, all achieved at much lower wear rates/costs.
Metallic SynchroRotor with rock-shelf
A SynchroCrusher with a rock-shelf provides a combination of a metallic VSI and an autogenous VSI and allows for a small (normal) body design. The rock-shelf provides for around a 10% increase in comminution intensity, without increasing wear costs, and stays constant. With similar energy consumption, this combination equals the comminution intensity of a conventional VSI equipped with an anvil ring but suffers significantly less wear and produces a consistent quality product with sharp-edged cubicity and reduced fines.
Metallic SynchroRotor with anvil ring
The combination of a metallic SynchroRotor and an anvil ring also allows for a small-body design. On average the anvil ring increases comminution intensity by some 35%; with fresh anvils the increase is about 40%, somewhat higher than with a stator. As the anvils wear down this level is gradually reduced to a level below that of a stator. However, because about two-thirds of the comminution intensity is generated constantly by the SynchroRotor, the reduction in the comminution intensity is far less dramatic than is the case with a conventional VSI. In fact, at the critical level, when the anvils are worn out, the reduction is some 12.5%, but with a total anvil utilization only of 20% this can be effectively compensated for by gradually increasing rotational velocity as the anvils wear down. This makes utilization beyond the critical level a realistic option, which makes it possible to double anvil ring life. The quality of the crushed product is then only marginally lower when compared with the stator combination.
Autogenous SynchroRotor
When an autogenous rotor is equipped with sliders, the autogenous guiding members are turned into autogenous drivers for autogenous impact. This restricts the grinding action to a considerable degree because reversal of the direction of the material stream proceeds in a more natural, less chaotic way. It is, therefore, preferable to design the SynchroRotor symmetrically for two-way operation, which also doubles lifetime.
To equal the life of the tip-ends, the sliders also have to be provided with hard-metal elements, but these have a much lower wear rate because they move at a much lower velocity than the tip-ends.
Material is accelerated by a combination of autogenous impact and autogenous sliding that generates a certain level of attrition treatment. Like the conventional autogenous rotor, maximum feed size should not exceed 40–50mm.
During autogenous impact a certain degree of constant comminution intensity is achieved, while owing to the reduced milling action less fines are produced and the particles display a more sharp-edged cubicity. The increase in comminution intensity is difficult to quantify because the conventional autogenous rotor provides autogenous grinding while the autogenous SynchroRotor provides autogenous impact. However, it can be stated that, at a similar co-rotating impact velocity, autogenous driver impact generates about 20% of the comminution intensity of metallic driver impact.
Autogenous SynchroRotor with rock-shelf
In combination with a rock-shelf, the replacement of a conventional autogenous rotor with an autogenous SynchroRotor almost triples comminution intensity, resulting in a significant increase in the reduction ratio, less fines and a more sharply defined cubicity. For many applications a SynchroAutogenousCrusher is undoubtedly much more effective than a conventional autogenous VSI (ie without sliders), particularly when the aim is to realize a moderate reduction ratio, the amount of fines is to be limited and a more sharp-edged cubicity is preferred.
Autogenous SynchroRotor with anvil ring
Compared with the combination of a conventional autogenous rotor and an anvil ring, the combination of an autogenous SynchroRotor with an anvil ring increases comminution intensity by some 20%, resulting in a significant increase in the reduction ratio, while particles produced display good sharp-edged cubicity and contain significantly less fines.
Because the comminution intensity generated by the autogenous SynchroRotor stays constant, the comminution intensity declines as the anvils wear out, but to a lesser extent than with a similarly configured conventional VSI. Also, the lifetime of the anvil ring is increased to a certain degree, which compensates for the extra cost of the hard-metal sliders.
The combination of an autogenous SynchroRotor with an anvil ring has been proven to be eminently suitable for the production of manufactured sand, for which the feed size can be varied from less than 5mm to more than 40mm, increasing the reduction ratio significantly and producing better-shaped particles and less fines (–0.063mm).
SynchroCascading
With SynchroTechnology a synchronized collision can be achieved between two different horizontal streams of material moving at widely different velocities, and it is also possible to accurately adjust the amount of material in each stream. SynchroCascading can be achieved in a very simple way and avoids the problems of conventional cascading mentioned earlier. One material stream is guided from the slider towards the autogenous driver and is then thrown outwards as an accelerated stream, while an associated cascading stream is guided from another slider towards a collision area were both streams cross. Preliminary tests indicate SynchroCascading to be about as effective as impact against an autogenous driver. SynchroCascading proceeds accurately and is not interrupted as is the case with conventional cascading. Normally, the cascading stream moves at a velocity of about 30% of that of the accelerated stream, producing an optimum and regular comminution intensity.
BIBLIOGRAPHY
VAN MUIJEN, H.: ‘The SynchroCrusher: a new low-energy vertical-shaft impact crusher’, Quarry Management, 1998, vol. 24, no. 7, pp 17–23.
VANDER ZANDEN, H., et al.: ‘SynchroCrusher: 21st century crushing technology’, The Institute of Quarrying, Developments in quarrying and recycling, International seminar, June 1999, paper 9, pp 33–44.
VALENCHON, P.: ‘Le SynchroConcasseur: du nouveau dans l’impact, Mines et Carrières, Industrie Minérale, October 1999, pp 32–39.
ANON: ‘Le SynchroConcasseur’, Les Techniques de L’industrie Minérale, no. 4, 1999, pp 67–68
VAN DER ZANDEN, H., et al.: ‘El SynchroCrusher: La technologia de trituracion del siglo XX, Rocas y minerales, October 1999, pp 84–100.
VAN DER ZANDEN, H.: ‘The SynchroCrusher: 21st century crushing techology’, Quarry Management, vol. 25, no. 11, pp 45–54.
VAN DER ZANDEN, H., et al.: ‘SynchroCrusher: 21st Century Crushing Technology’, report prepared for Siltech conference, 1999, pp 1–64.
CASTEEL, K.: ‘Synchro Inside’, World Mining Equipment, Jan/Feb 2000,
pp 44–47.
VAN DER ZANDEN, R.: ‘The SynchroCrusher’, Novem Newsletter, September 2000, pp 22–24.
CASTEEL, K.: ‘Significant Impacts’, World Mining Equipment, October 2000, pp 70
ANON: Neuartiges Prinzip, Baumagazin, October 2002, pp 5.
VAN DER ZANDEN, H., et al.: ‘The SynchroCrusher’, AufbereitungsTechnik 41, 2000, no. 10, pp 462–471.
CASTEEL, K.: ‘First Cuts – Crushing and Screening – Bauma in review, June 2001, pp 28–29.
VAN DER ZANDEN, H.: ‘Synside lanza el nuevo concepto de impactor SynchroCrusher, Rocas y minerales, February 2002, pp 64–68.
ANON: ‘Energieeffizienz in der Zerkleinerung neu entdeckt’, Steinbruch und Sandgrube, 2002, no. 11, pp 16.
VAN DER ZANDEN, H., et al.: ‘The SynchroCrusher — Determinism versus Chaos’, AufbereitungsTechnik 43, 2002, no. 10, pp 13–26.
VAN DER ZANDEN, H., et al.: ‘The SynchroCrusher — Determinism versus Chaos’, Marktfocus Brecher, 2003, pp 2–13.
VAN DER ZANDEN, H., et al.: ‘The SynchroCrusher — a detailed comparison with the conventional VSI’, AufbereitungsTechnik 44, 2003, no. 6, pp 37–61.