Selecting the Right Crusher for Quarry Operations
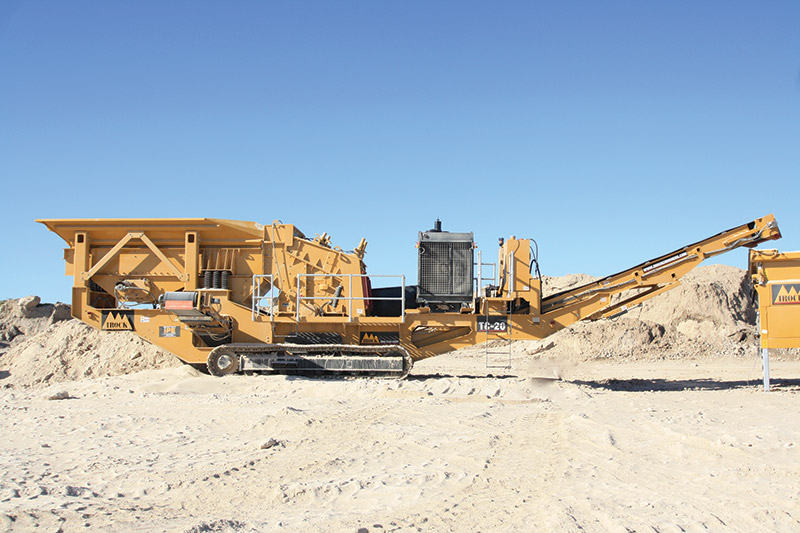
First published in the September 2014 issue of Quarry Management as From Flintstone to Finesse
Sean Donaghy, national sales manager of IROCK Crushers discusses what needs to be considered when choosing a crusher
Crushing rock is an age-old idea, but the reality of the task is a far cry from that of Fred Flintstone and his good buddy Barney Rubble. Although crushing rock and other materials may seem simple, it is really a science. Selecting the right equipment to maximize productivity while minimizing maintenance can make the difference between profitability and growth or frustration and financial woes. And while the selection of a crusher may be thought of as a relatively easy task, several critical factors must be considered, including output requirements, feed material, application and machine design.
Application
Perhaps the first and most fundamental aspects to consider are application and feed material. A variety of crushers exist and each is tailored to meet the demands of very specific applications or materials. The most critical factor with feed material is its degree of hardness. This is typically measured in terms of compressive strength, ie the maximum force that the material can withstand before breaking. Hardness levels can range from that of concrete at 7,000 psi to 50,000 psi for ores or other hard rocks. The harder the material, the longer it may take to crush, but in addition to production times, the degree of hardness will also influence the specific crusher for the operation.
Jaw crushers
Jaw crushers, which use a moveable jaw and a stationary plate designed to form a ‘V’, crush material using compressive force. These crushers offer an ideal solution for primary crushing applications involving hard, abrasive materials such as granite or recycled concrete. Efficient and less costly to operate because of their minimal moving parts, jaw crushers are well suited to applications where the primary objective is to reduce raw feed material to a manageable size, usually down to about 150mm.
While these machine may be appealing due to their lower operating costs, they are not well suited to applications that require smaller material sizing and are therefore used in conjunction with other crushers. Another critical application factor to note is the effect of contaminated material; jaw crushers do not perform well with materials contaminated with clay, dirt or metal debris.
Cone crushers
Cone crushers, which are also known for their ability to crush hard, abrasive ores and rocks, break material by squeezing or compressing it between convex- and concave-shaped surfaces. Best suited for secondary crushing applications, cone crushers are designed to crush pre-sized materials, usually 100mm, 150mm, or 200mm, depending on the size of the crusher. Cone crushers can form finished products down to 12mm or less.
Like the jaw crusher, the cone crusher provides a relatively low-cost crushing solution, but there are application drawbacks which may make another crushing solution more appealing. First, cone crushers cannot accept all material sizes. Any material fed to the crusher must be pre-sized for that particular crusher (usually 200mm or less). In addition, the cone crusher will not produce a consistent cubical product, which is a key requirement in many material specifications. Finally, these units, like jaw crushers, are not suitable for handling any clay or metal mixed in with the rock or concrete feed material.
Impact crushers
Designed to fill the gap left in the market by cone and jaw crushers, horizontal impact crushers are ideally suited for contaminated materials and can easily handle any clay, dirt or metal mixed in with the feed material, such as rebar, wire mesh or dowel pins. Horizontal-shaft impactor (HSI) units produce a uniform cubical product and can deliver high reduction ratios, allowing them to accept all in-feed and providing maximum productivity in both primary and secondary applications. Whilst HSI units can handle hard material, they are ideally suited for soft-to-medium rock.
HSI crushers consist of a rotor attached to a horizontal rotating shaft. The shaft is placed inside a chamber which is lined with replaceable liner plates, anvils and blow bars. Material is fed into the top of the chamber where it impacts the rotor which then throws the material outward against the curtain anvils. Repeated impacts against the curtain anvils by the blow bars reduces the material until the desired size is reached. Material sizing is achieved by rotor rotational speeds and adjustments of the clearance between the blow bars and curtains. The nature of HSI crushing can lead to slightly higher operating costs, the cost being incurred for greater versatility and uniform product sizing.
Machine size and output
Determining the desired tonnes/h for a plant is also essential in the selection process. Companies should be able to calculate what their projected sales are for a year and then break the number down to the desired tonnages per month. Operators can then calculate the number of days per week the machine will be in operation to determine tonnage outputs.
For example, if a company can sell 500,000 tonnes per year, its crushers need to produce just short of 42,000 tonnes each month. If the crusher is set up to run three days a week (approximately 13 days a month) for 8h a day, the operation will require a machine capable of processing 400 tonnes/h.
Proper production capacities are critical to the success of a business. A crusher that is too small will fail to produce the desired tonnages, thereby limiting yields and profits, and capping the growth potential of the organization. A machine that is too large will carry extra expense with no added value – especially considering crushers tend to work best when choke fed and under pressure.
A crusher’s maximum tonnes/h output is determined when the machine is at or close to full capacity during its peak performance. Failing to maintain a full load can result in improper wear and inefficient crusher operation. Using a machine capable of processing 450 tonnes/h to perform at a much lower rate, such as 50 tonnes/h, will result in visible signs of irregular wear and lead to costly repairs to the crusher. That said, it is important to review the business plan, calculate short-term growth initiatives and purchase a machine sized to allow for that growth while still maximizing efficiencies.
Number of different sized products
Whilst tonnes/h are critical, another production factor that significantly impacts the crusher selection process is the number of end product specifications required, ie is the operation producing and selling just one size of product or are two, three or even four different specifications required? The number of screens available on a crusher unit will dictate the number of different sized products a machine can produce in one pass.
Closed-circuit machines equipped with a two-deck screen offer the ability to produce up to three different sizes of product. The top deck might be screening materials 50mm or less, the bottom deck 25mm or less, with the oversized material either being fed back to the hopper for additional crushing or, with the installation of flop gates, kept as a third product for sale. Similarly, three-deck plants are required when production specifications require four different size classifications.
To move or not to move
Some operations do not require mobility since the projected life of the quarry will be decades. In such cases stationary crushers are put in place offering a custom-built, heavy-duty design. However, most contractors require highly mobile machines which can be easily dismantled and moved from one site or job to another. Mobile crushers allow operators to move the crusher unit closer to the quarry face, effectively reducing unnecessary expense associated with loading and hauling large materials across a the site.
Wheeled mobile crushers offer maximum convenience for transport. These units can be hooked up to a truck and hauled to different locations, meeting all transport legislation requirements. They can also be relocated on site with the help of a truck, and are commonly self-contained, thereby eliminating the need for additional diesel engines.
Tracked mobile crushers are ideally suited for applications that require movement within a job site as they can move under their own power. They are also easily transported from one site to another by loading them onto a trailer. However, the convenience of these machines can come at a cost. If an operator wishes to run multiple items – such as a screening plant and conveyors – it may also be necessary to run three to five diesel engines, depending on the additional items. Furthermore, because they are built for constant relocation on a trailer, they are more compact and lightweight than wheeled versions, making maintenance more challenging than on a stationary or wheeled crusher.
Transport regulations are obviously a key consideration with portable units. Due to the weight of a portable unit, operators may have to transport the hopper feeder separately to meet weight regulations, which will require additional lifting and transporting equipment. A unit with a hydraulic system for the hopper can reduce this problem for the more mobile operators. The hydraulic power pack, designed for removal or installation in minutes, makes for convenient transportation and feeder set-up by one person. These qualities can be a huge benefit to operations that do not have lifting equipment and additional workers on site.
Features, components and overall durability
Crushing is demanding and arduous work so machines must be durable enough to withstand the daily rigours of the task. It is widely accepted that operators who invest in quality equipment and components right from the start tend to save money in the long run by reducing the costs of upkeep and future maintenance. Components such as the crusher’s engine, hopper and wear liners are just as important in ensuring the best fit and keeping maintenance to a minimum.
A powerful, well-known engine is the backbone to a good crusher – one that will perform not just until the end of the day, but for years to come. Directly related to crushing, the horsepower ultimately dictates whether the engine will meet the operation’s output needs. Strong brand name engines provide a proven track record and the network required to ensure service and support whenever and wherever the operator/contractor needs it.
Another main component, the hopper, should be sized to suit the operation. The hopper size dictates the amount of in-feed the machine can handle at one time, and although an oversized hopper does not technically equate to a boost in production, it can accommodate larger equipment used to feed the unit.
Transfer points on a crusher have to endure a tremendous amount of wear. Most transfer points are lined with standard rubber material, and while these liners allow for quieter operation, they also wear quickly. Some manufacturers have started to introduce the option of AR-400 liners, which significantly increase durability and product life. Abrasion-resistant transfer points throughout the machine will provide the extra strength needed for certain applications, greatly reduce costly replacements and prevent downtime.
A high-quality machine will also feature designs that reduce or even eliminate maintenance. The quality of components such as conveyors, bearings, rollers, shafts and drives are easily identified upon visual examination. The more robust designs will extend life and prevent failure.
For example, a crusher’s discharge chute is an area of the machine that is under a lot of stress for the majority of the machine’s running time and, as a result, requires regular maintenance. To eliminate these extra costs, operators should look for a specially designed discharge rock box that will reduce the need for wear-liner replacement. This specialized design uses a shelf system with an abrasion-resistant wear bar that allows crushed material to build up and act as a wear liner. The result is zero-maintenance, which translates into considerable savings in labour and wear parts.
Clearly, there is no shortage of options to consider when selecting a mobile crusher. Spending time fully evaluating the needs of an operation will help ensure the proper selection is made, resulting in optimal usage of the right features and the highest level of production possible. The goal for all operators is quality production at low cost. Selecting the right machine will make each job easier and more profitable.
- Subscribe to Quarry Management, the monthly journal for the mineral products industry, to read articles before they appear on Agg-Net