Screen Versatility
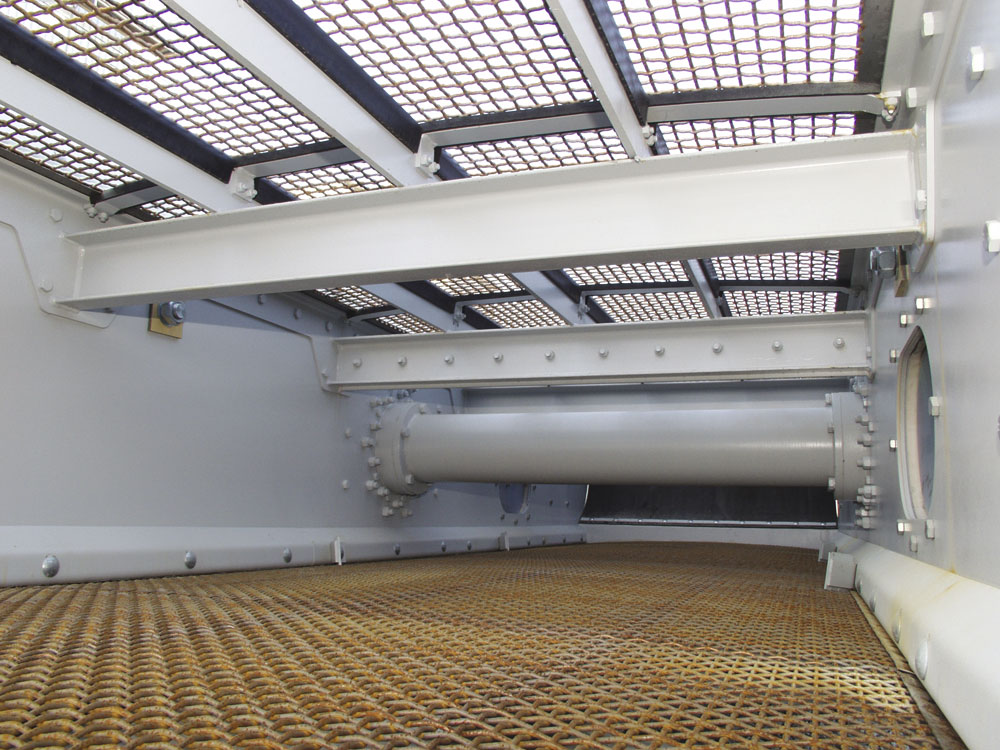
Examining the design and construction of screening machines
By Peter Grotjohann, Haver & Boecker Engineering Division
The classification of materials into different size fractions is a highly complex task. Two main functions have to be fulfilled to achieve a successful screening operation; the feed material has to be distributed over the entire screen width and the material has to be transported over the screen. Furthermore, the feed material has to be loosened (break-up phase) so that fines can migrate to the screen deck for classification (classifying phase). During the final phase of the screening process, when the screening of near-size particles takes place, particles are being screened that are just slightly smaller than the mesh width; this phase is very important for high selectivity.
In order to meet these different criteria, manufacturers of screening machines use different techniques to achieve optimal results depending on the end requirements. The method of screening, the characteristics of the feed material, the cut sizes required, the particle size distribution, the screen quality, the wear-out rate and other final-product requirements are all important factors. Correct evaluation of these requirements and the subsequent design and construction of a suitable screening machine involves a multi-faceted examination of mineralogy, petrography, mineral-processing technology and mechanical engineering.
TECHNICAL AND PHYSICAL KEYNOTES
Reject screens utilize the vibrating motion of the machine or the screen cloth to effect the distribution, conveying and loosening of the feed material. This technique has no direct connection between the amplitude and frequency of the vibration and the particle size (cut size). Large cut sizes with relatively large vibration amplitudes (5–8mm) and low frequencies (650–900rev/min) are used.
The machine identification code ‘K’ is a numerical factor of g, the acceleration of gravity. K represents the acceleration of the machine applied to the feed material. It can be calculated as the product of amplitude and frequency. In order to guarantee optimal screening results the amplitude and frequency have to be in due proportion for all material being screened.
When using reject screens good loosening can be obtained with large amplitudes. Large particles cannot be sufficiently loosened by small amplitudes, but small particles exposed to large amplitudes will ‘skip’ the screen and leave the machine unclassified.
The mechanical strain placed on screening machines also imposes physical limits. If the frequency and amplitude are higher than specified, the lifespan of the machine will be reduced unnecessarily. If the frequency is too low screen performance will be reduced. If the amplitude is too low screen efficiency will decrease, owing to a reduction in loosening, and screen blinding will increase as jammed particles will not be sufficiently accelerated to be rejected out of the screen cloth.
SCREENING SYSTEMS
Table 1 shows a summary of the screening machines produced by Haver & Boecker for the screening of different types of bulk materials to meet various end requirements.
METHODS OF SCREENING
Classifying
Standard classification involves separating the feed material into two or more products according to particle size. When designing screens, and during screen operation, attention must be paid to ensure that the maximum thickness of the feed material on the screen is not exceeded otherwise particles smaller than the cut size will not have the chance to migrate to the screen cloth. Approximately 50% of the material passing the screen cloth and migrating into the screen underflow represents a normal specific capacity. It is very important to maintain the relevant standards for classification into different final products, ie a high-precision cut size.
Scalping
Scalping aims to separate fractions of feed material by means of a screening machine prior to further processing, typically to reduce the workload of primary crushers in quarries. In this process excavated rocks of a certain size are prevented from reaching the crusher and other downstream processing stages. It is important that screens of this type offer high capacity, robust construction, no clogging and high flexibility regarding the feed material in terms of moisture content, particle composition etc. For this particular task the load-independent eccentric screening principle is the established method.
Fines removal
A typical example of this is the separation of unwanted fines from a crushed stone product with a particle size ranging from 0–2mm for use as a concrete additive, which can contain only a certain portion of elutriable components. Ninety percent of the feed material passes the screen as product overflow, with only 10%, ie the filler fraction, being screened. The use of a relief deck is recommended due to the low specific screen output. Preconditions for a successful screening process are, if possible, a dry feed material and a de-dusting system.
Reject screening
Reject screening is an example of a highly specific screen application involving the removal of unwanted components (ie material lumps and other oversize particles in the cement industry) that can occur sporadically in the feed material. Around 95% of the feed material will pass the screen with occasional foreign bodies being retained. Reject screens are often used to guarantee safe operation during the loading or packing of construction materials. Depending on the specific application, reject screens can be manufactured with unbalanced motors or eccentric drives and can achieve a capacity of more than 1,000 tonnes/h.
SELECTION OF THE VIBRATING SYSTEM
The screening machines normally used in the quarrying industry can be classified depending on the vibrating system used. When choosing the correct system the combined effects of amplitude and frequency play a crucial role. Structural conditions also need to be considered, particularly when retrofitting.
Vibrating system options include:
—eccentric screens (load-independent)
—free-swinging screens (load-dependent)
1. circular swinging motion
2. linear swinging motion
a. with double unbalanced shafts
b. with exciter drives
c. with unbalanced motors/magnetic actuation
3. elliptical swinging motion
—screening machines with direct excitation of the screen cloth
—special designs, such as shaft-axle screening machines.
When designing screening machines the following specific characteristics also need to be considered:
Machine parameters
—machine identification code K (see figure 2)
—screen identification code Kv (depending on the inclination of the machine/screen)
—rotational speed or frequency of the screen drive
—inclination of the linear motion vector
—amplitude a of the vibrating motion (2 x a = total vibrating width)
—specification of the cut sizes
—requested screen material quality grade
—wear protection.
Specification of the screening method
—negative screening
—positive screening
—combined positive/negative screening.
For dry screening:
—dust-proof version with resonant casing
—dust-proof version with stationary dust hood and lower rubber sealing
—combination of resonant and stationary casing.
For wet screening:
—available water quantity
—available water pressure (3–4 bar, if possible)
—for increased washing effect (6–8 bar, if possible).
Specification of the screen type
—input rate of the feed material
—material supply (drop height, material distribution etc)
—abrasive effects of the feed materials
—clogging/blinding of the screen
—agglomerate formation on the screen.
Screen media:
—perforated plate (material, size and aperture shape)
—woven-wire screens (mesh design, wire type and materials)
—polyurethane screen panels (either connector or clamping system)
—grizzly bars (rigidly installed and/or vibrating).
Extensive communication with the processing plant operator is required to fully assess the above parameters and characteristics prior to the design and engineering of the screening machine. Consideration of upstream and downstream processes also has an important part to play. At the start of the processing stream it often makes sense to invest in high-class screening technology. Coarse and mid-size fractions will be classified close to the required cut size and the overloading of any downstream screening machinery (with finer cut sizes) will be avoided.