New Wash Plant for Kennetholme Quarry
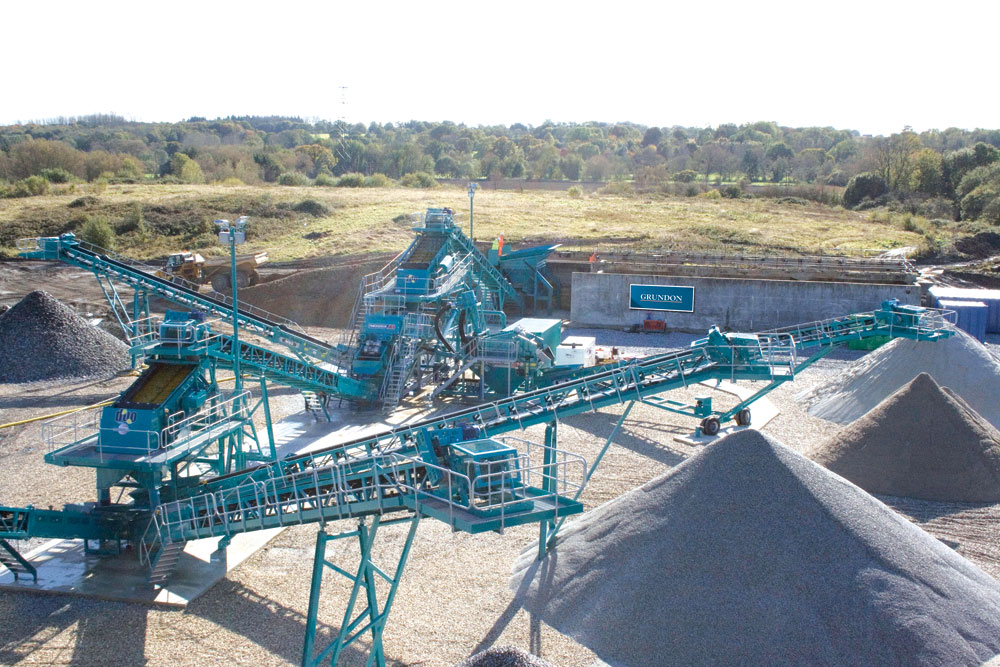
Grundon choose DUO (Europe) to supply and install complete system
Grundon, the UK’s largest privately owned waste-management group and a company widely acknowledged as being in the vanguard of waste-management practice and innovation, have recently installed a new aggregate washing plant at their Kennetholme Quarry operation.
The prime objective of the new plant is to process ‘as-dug’ material as a replacement for Grundon’s existing operation at nearby Padworth Quarry, where mineral processing will soon cease.
Following a site survey and consultations, DUO (Europe) were commissioned to supply and install a plant capable of processing material at a rate of up to 150 tonnes/h, producing the required products of sharp sand, 10mm, 20mm, 40mm and +40mm oversize.
The site at Kennetholme, which has over 10 years of reserves of a flint-based sand and gravel, was originally a paper mill and some of the old infrastructure has proved useful for the new plant installation. For example, the old water-treatment system has been brought into service for water storage and an old concrete structure is being utilized as a supporting wall for the hopper feed ramp.
Production process
As-dug material is fed by dumptruck or loading shovel into a 30-tonne capacity feed hopper equipped with a remote-control tipping grid (4in grid spacing) and variable-speed drag-out belt. Any +125mm oversize material is immediately rejected to the ground, while –125mm material is fed on to an inclined, 24m long feed conveyor.
This discharges the –125mm material on to a 16ft x 5ft double-deck rinsing screen, which rejects any material larger than 40mm for delivery to stockpile via a conveyor. Meanwhile, all –40mm material is fed to a Powerscreen Powerscrub log-washer. This twin-shaft unit with its interchangeable high-tensile blades is fitted with an elevated spray bar that constantly adds water, helping to wash the material and encouraging lighter particles to float through the water exits.
The scrubbed material then passes over an 8ft x 4ft dewatering screen fitted with polyurethane modules before being delivered, via a 20m long transfer conveyor, to a 12ft x 5ft double-deck dry screen. This unit grades the material into 10mm, 20mm, and 40mm final sizes, which are conveyed and stocked by three 20m long stockpile conveyors.
Meanwhile, all waste water from the Powerscrub unit is sent over a 6ft x 2ft dewatering trash screen fitted with polyurethane modules. All foreign materials are removed from the system at this point and fed into a skip, while the water and sand content flow into an adjacent Powerscreen Fines Master 120 compact sand plant.
The Fines Master plant incorporates a rubber-lined Linatex cyclone with fixed spigot and a rubber-lined Linatex centrifugal pump. The system also has a self-regulating collection sump with built-in float system. The underflow from the cyclone is discharged on to a high-frequency dewatering screen fitted with polyurethane modules and adjustable vibrating motors.
Dewatered sand from the Fines Master is delivered to stockpile by a radial sand conveyor, while the waste water from the sand-classification unit is pumped to a nearby lagoon.
Commenting on the project, Ken Branigan, Grundon’s aggregates general manager, praised DUO (Europe) for installing the plant in a very efficient and professional manner, with specific attention to health and safety.
He said: ‘At Grundon, we currently operate eight quarries across southern England, producing a wide range of products for a wide variety of customers.
‘Our core aggregate business is the supply of sands and aggregates to the building, construction, landscaping, decorative and leisure markets, and we offer a unique ‘open door’ policy, actively encouraging the general public, smaller builders, landscapers and DIY enthusiasts to come along and purchase directly from our quarry weighbridge offices – no matter how little product is required.
‘With our emphasis on customer care and a commitment to high standards, we are energetically committed to minimizing the environmental impact of all our operations and services.’