Molson Finlay material processing train for Catplant
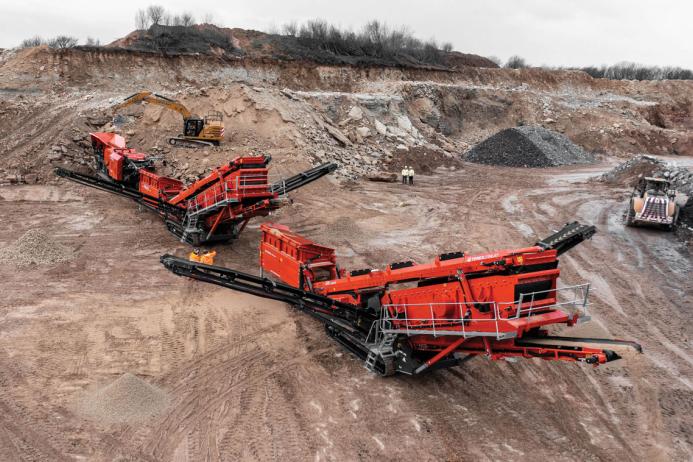
First published in the July 2023 issue of Quarry Management as Set-up is key for Catplant
Molson Finlay supply and install three-machine material-processing train for Yorkshire quarry operator
To the uninitiated, the crushing and screening of aggregates looks a simple task. This can be far from the truth. Whilst correct machine selection plays a huge role in obtaining the production figures a quarry requires, the correct set-up of these machines is key to meeting and even exceeding these targets.
Since their acquisition of Finlay Scotland in 2019, Molson Finlay have built up a team with an enviable reputation within the quarrying sector for delivering crushing and screening packages designed and installed to the full satisfaction of their clients. One of the most recent installations was at the Doncaster quarry of Yorkshire producers Catplant.
Catplant have a long history of providing a range of quality aggregates and block stone from their quarry close to the A1. Whilst many quarries blast the material from the face resulting in a relatively uniform material being fed into the crusher, Catplant’s operation is different thanks to the fragmented and softer geology in the area. Using a 95-tonne excavator the material is pulled from the face before being stockpiled for a 20-tonne machine to load the crushing and screening equipment.
For more than a decade Catplant’s crushing and screening requirements have been sourced from the Irish manufacturer’s stable. ‘We have run Finlay equipment for over two decades now and they have both stood up to the task, delivering what we were expecting in terms of reliability, and met our production demands,’ explained quarry manager, Bryn Anderson.
The quarry has recently taken delivery of a new, front-line material processing train consisting of a Finlay J-1170 jaw crusher, Finlay 696 three-deck screen and Finlay 696 two-deck screen. Delivered direct from the factory in Northern Ireland, the machinery joined a team from Molson Finlay headed by technical sales manager Ben Sherratt, whose role within the company brings his vast operational knowledge from the contract crushing industry to both the sales and engineering side of the business.
‘I work closely with the sales teams to ensure that specifications for particular applications are correct and that the client’s aspirations can be achieved with the machinery they are wanting to put into service,’ said Mr Sherratt. ‘Once the right machinery has been specified, I’ll work on site with the client and our installation teams to ensure the equipment is correctly installed, should the client request this service.’
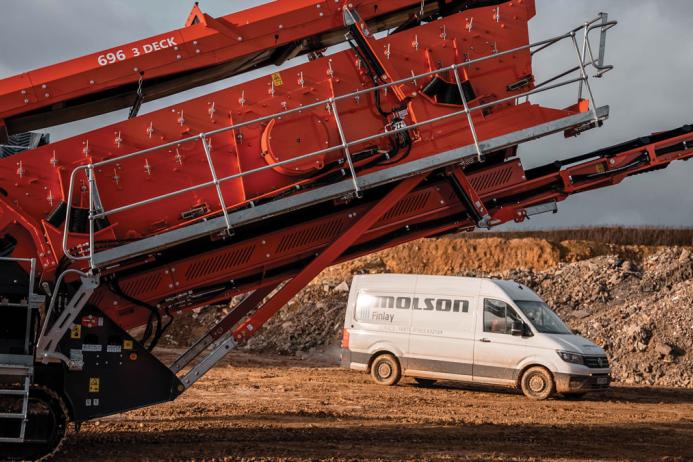
The experienced team at Catplant requested Mr Sherratt’s and his team’s assistance in setting up their new equipment to allow it to perform to its full capability. ‘We will work a particular bench for a few weeks, so getting the train set up right for the first one will allow us to mirror that every time we move the machines along,’ explained Mr Anderson.
Having identified a suitable location on the bench, the J-1170 was positioned to allow the excavator to load the crusher’s 9m3 hopper without too many issues. ‘We like to get the crusher level and create a slight pad for it to sit on. If the crusher is level and stable, it will operate as it’s supposed to. Having it set correctly will ensure it runs as economically as possible,’ commented Mr Sherratt.
The 50-tonne class J-1170 is a hydrostatically driven machine with a maximum closed-side setting (CSS) of 150mm and a minimum CSS of 50mm. The quarry’s choice of configuration calls for all of the material passing through the jaws to be passed on to the first screener, leaving the side-discharge conveyor redundant.
Satisfied with the crusher’s position, Mr Sherratt and his team moved on to the first of the Finlay 696 tracked screens. This three-deck version has been set up to produce four specific products with oversize from the crusher being removed by the 696’s grizzly while a steady stream of material flows up the conveyor and through the screening media to produce +80mm, 80-40mm and
40-20mm, with any 0-20mm material passing on to the second Finlay 696. This final tracked screen, this time a two-deck version, delivers three more products: 20-10mm, 10-5mm and 5-0mm.
Ensuring the discharge conveyor from the J-1170 feeds the material steadily into the first 696 hopper, Mr Sherratt took time to tweak the screen’s position to make sure it was just right. ‘We have seen incidences where quarries are losing material over the grizzly because the position of the in-feed conveyor isn’t quite right. It’s not just a case of reversing the screen under the conveyor and away you go,’ he said.
With the three pieces of plant set up, Mr Sherratt and his team wanted to try the train out. Putting an excavator on the bench and feeding the J-1170 allowed them to monitor and adjust the setting, first on the crusher to get the correct sizing of the material coming out of the jaw, and then the screens to make sure their discharge conveyors were keeping the material piles segregated. Following an hour of run time, the entire train was shut down to give the quarry management team the opportunity to review the material produced. With the nod of approval from Mr Anderson the final checks and tweaks were carried out for the following day when full production began.
Catplant managing director Ronnie Harrod said: ‘We have been using the Finlay brand for many years with great success. We are always fighting against time every time we need to relocate the crushing and screening train but having Ben and the Molson team here to set everything up correctly helps us in getting it right the next time we do it.’
Mr Sherratt commented: ‘We know the parameters the machinery needs to work to in order to get the optimum performance and productivity out of it. Being able to do this to meet the customer’s requirements is just part of the customer service we provide at Molson. The entire specification and purchasing process is where the hard work is done, ensuring the client’s requirements match our products and vice versa. What we don’t do is sell the customer a machine that will ultimately never meet their demands. Not only does that lose you future business, but it gives you a bad reputation within this close-knit industry. If we can produce a quality, reliable and efficient product that meets the client’s expectations, we know we are doing the right thing.’
Subscribe to Quarry Management, the monthly journal for the mineral products industry, to read articles before they appear on Agg-Net.com