Hints and Tips for Selecting the Right Mobile Screener
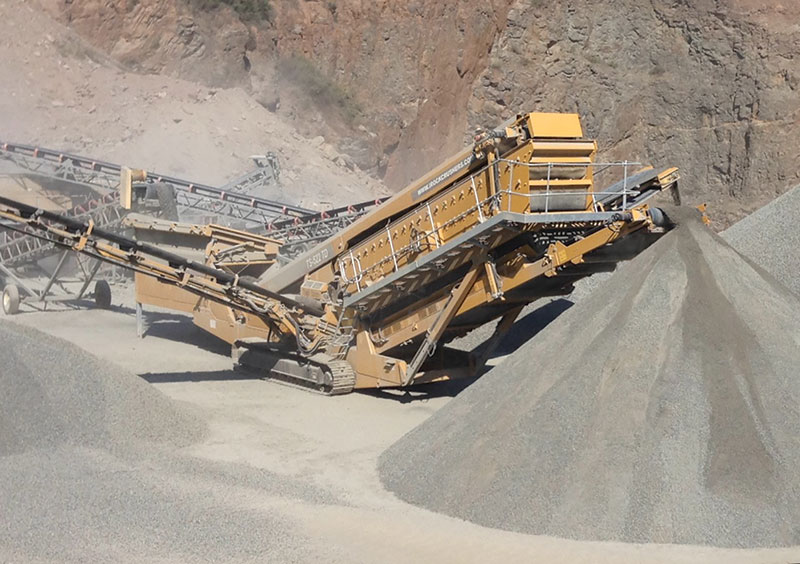
First published in the February 2015 issue of Quarry Management as Sifting Through the Facts
Sean Donaghy, national sales manager with IROCK Crushers, provides a few tips on selecting the correct mobile aggregate screener
Portable screening plants are a major part of the business for aggregate producers and contractors in quarrying, demolition and recycling operations, and any operator will testify just how important quality screeners are to a business. But what is right for one operator may not fit the bill for the next, and while it may seem that the only thing separating one mobile screener from another is the colour and a logo, there are many factors to sift through, from small, highly customized design modifications to the overall type and size. With new technologies and the development of advanced screen media, operators need to do their research and take advantage of the ever-growing options and choices.
Selecting the right screener takes time, research and a clear idea of the goals of the operation. The first step in the process is to consider whether the company’s production has already been maximized or will continue to grow.
Size matters
There is nothing more important than sizing the equipment to match the operation. Understanding the application, materials and desired production is crucial. With plenty of research and consideration of desired production, size and abrasiveness of material, and the number of sized end products required, operators can find well-specified screeners that will align with the goals of their operations.
It is important to keep the company’s goals in mind during the selection process. Calculate projected sales for a year and break the number down to tonnages per month. For example, if a company can sell 750,000 tons a year, its screeners will need to sort 62,500 tons a month. If the screener is in operation three days a week (approximately 13 days a month) for eight hours a day, the operation will require a machine capable of screening around 600 tons/h.
This rate is key to the success of a business. In the above example, a screener that processes 300 tons/h will limit profits and cap the company’s growth potential. On the other hand, a machine with a potential output of 900 tons/h will, more than likely, come with extra expenses but no added value.
Another thing to keep in mind is the end product. Many machines are two-deck screeners capable of sorting two sized products and an oversize, while other machines feature three screen decks and can produce an additional sized product.
Also bear in mind that screenboxes vary in size and design. For example, a few screener/scalpers are labelled ‘high energy’, but what does this mean and what is the benefit? A high-energy screenbox runs faster and produces a higher stroke than a standard screenbox. Many customers notice that the more efficient, lively stroke boosts a machine’s output and produces a cleaner product in comparison with a standard screenbox. Operators should look out for these stand-out features and determine what is best for their organization before looking any further into the details.
Scalp or screen
There are two main types of screeners: scalpers and standard screens. Several key differences separate a scalping plant from a standard screening plant. Standard screens have a tipping grid or livehead over the feed hopper to prevent large material from entering the hopper. Also, the feeder belt speed can be adjusted to help produce a clean, sized finished product. These screens are typically found in sand and gravel pits, quarries and recycled concrete and asphalt applications, and are often considered ‘finishing screens’ because they are capable of producing specific sized end products.
A scalper feeds material directly on to a screen as it comes out of the hopper, eliminating blockages due to oversized, contaminated and dirty material. Ideal for demolition contractors pre-processing materials such as recycled concrete, scalping screens also are designed to handle much larger, heavier material in larger crushing operations or for producing a gabion stone in a quarry. They are versatile but not an ideal choice for creating a finished product – especially when the operator needs smaller, specified materials.
While both units have their differences, the type of screener is not the only factor that needs to be taken into consideration. Many other factors can make a big difference.
Hopper size
The industry standard hopper is 12ft wide, usually with an option to upgrade to 14ft. Although very few manufacturers offer a 14ft wide hopper as standard, the width of the hopper is significant. Obviously, the wider the hopper, the easier it is to feed the machine. An extra 2ft can help capture more product and prevent spillage. The size becomes most pertinent, however, when pairing the screener with a loading machine. For example, excavators with a narrow bucket are ideal for loading a 12ft hopper, but a 14ft hopper is wide enough to accommodate a wider bucket. In comparison, a wheel loader bucket can hold approximately twice as much as an excavator bucket, so the extra 2ft of loading space can make a huge difference. Using a wheel loader is, therefore, a simple way for a company to pick up extra production.
Livehead or tipping grid
Operators can add a livehead or tipping grid above the hopper. While both of these perform a similar duty, they are very different. A tipping grid is suitable for preventing larger materials from passing into the hopper and through the screener. The hinged grid catches larger materials and operators can clear the grid by tipping it via a remote control. Although this is an affordable option, it can become a chore, particularly in wet or dirty applications where the tipping grid may become plugged more frequently.
The other option is a livehead, which is essentially a vibrating screen that attaches to the hopper. This piece of equipment is ideal for heavy-duty, dirty, wet and sticky applications. The unit can be used to scalp dirty material and eliminate the need for manual cleaning, or to size material going into the machine so operators can produce an additional sized product.
Although these units are designed to boost production and create an additional product, they can become a hindrance if used in the wrong application. They are built with thick bars that limit the open area, so operations processing finer materials might discover material on the ground that should have been in the hopper.
Apron vs belt feeder
From the hopper, material is generally fed on to a standard belt feeder. This is cost-efficient and will hold up well in numerous applications, such as sand and gravel operations. However, for operators working with large or abrasive rocks, a standard belt feeder may tear or break. Heavy-duty applications may require an apron feeder, which is essentially a belt made of metal. Because of its durability, the apron feeder can handle virtually any application, making the entire machine much more versatile.
Screen media
There are many types of screen media just as there are many different materials to screen. Screens often feature a wire mesh media for different sizing applications, but there are several sturdier options for operators working with abrasive materials.
Operators may wish to consider stainless steel as an alternative to regular wire mesh. Although the cost is nearly twice as much, stainless steel offers greater wear resistance and longer wear life that can be worth the extra cost.
Another replacement for the standard screen for certain scalping jobs is bofar bars. These long bars with spaces between are designed for materials that commonly contain a lot of dirt and miscellaneous matter, such as recycled concrete. Although bofar bars do a certain amount of sizing, the process does not necessarily end with thoroughly sorted product.
Punch plates are another option for heavier applications. These are essentially a piece of sheet metal with spaced holes. Compared with bofar bars, punch plates are better for sizing and are very durable, customizable and affordable.
Finger decks are well suited to reclamation, landfill or any other type of screening where clogging, blinding or breakage may be an issue. Finger decks can easily accommodate high-impact loads mixed with recycled waste and debris.
Stockpiling
A stockpile may look like a simple pile of rock, but stockpiling is an art. The taller the cone and the wider the base, the more tonnage the entire pile will hold. The additional tonnage possible with a higher pile is the reason why stockpiling height is so important. A typical stockpile might hold approximately 228 tons of rock if the pile is 8ft high with a top width of 2ft and a base width of 16ft. By increasing the height of the pile by just 9in, the total weight of the stockpile will increase by 29% to approximately 295 tons. Higher stockpiling capabilities serve as a time saver, as operators can run for longer periods without having to move material. This is why screener conveyors with the potential to stack even 8–10in higher can make a significant difference to an operation.
Conveyors
Conveyors commonly incorporate rollers which can be hot spots for damage and can reduce wear life, particularly when large materials are being processed. Rollers can break under the pressure and belts can become torn or punctured. As an alternative, some manufacturers offer an impact or sleigh bed conveyor. These conveyors provide more support and are more durable when handling heavy rock products. The impact bed is solid and runs the width of the conveyor to best accommodate the impact of material and prevent belt damage.
Furthermore, most discharge conveyors measure about 48in in width, although the industry offers belts up to 63in wide, which helps prevent clogging. Because the screen is wide and material gets funnelled down to the conveyor, machines with smaller conveyors can create a bottleneck effect. The material begins blinding in the corners, narrowing the opening. This creates productivity and maintenance problems, forcing operators to shut down the machine to clean it out. Operators should look for a machine that has less (or no) restriction as material transitions on to the discharge belt. A free-flowing machine with a low drop height is the best option to minimize wear and maintain productivity.
Machine design
Operators are guaranteed to get more value for money when they choose a machine that is taller, bigger and more rugged. More robust machines often offer features that boost convenience and productivity, such as larger access areas. Double-panelled engine compartments allow mechanics more space when servicing the machine. Dual fuel nozzles provide fuelling access from both sides of the machine and some manufacturers build units with access to the engine from both sides too. In this way, if the unit is parked alongside an obstruction, fuelling and maintenance can still be performed from the opposite side.
Customer support
Customer support becomes pivotal when parts or repairs are needed. The availability of wear parts and service can make or break an operation’s financial figures for any given month. Operators should choose a manufacturer with a good reputation not only for quality equipment and durable components, but also for exceptional customer service. Some companies offer the convenience of 24h online parts ordering with live service support that is responsive and able to help keep an operation on track. Similarly, every manufacturer should be capable of providing a one-year, 1,000h warranty.
Countdown to the purchase
Purchasing the wrong screener can cause problems, slow production and result in revenue losses. Taking the time at the start to sift through the facts and separate the good from the bad will prevent headaches, downtime and loss of production later.
- Subscribe to Quarry Management, the monthly journal for the mineral products industry, to read articles before they appear on Agg-Net