Diagnosing Screen Media Problems
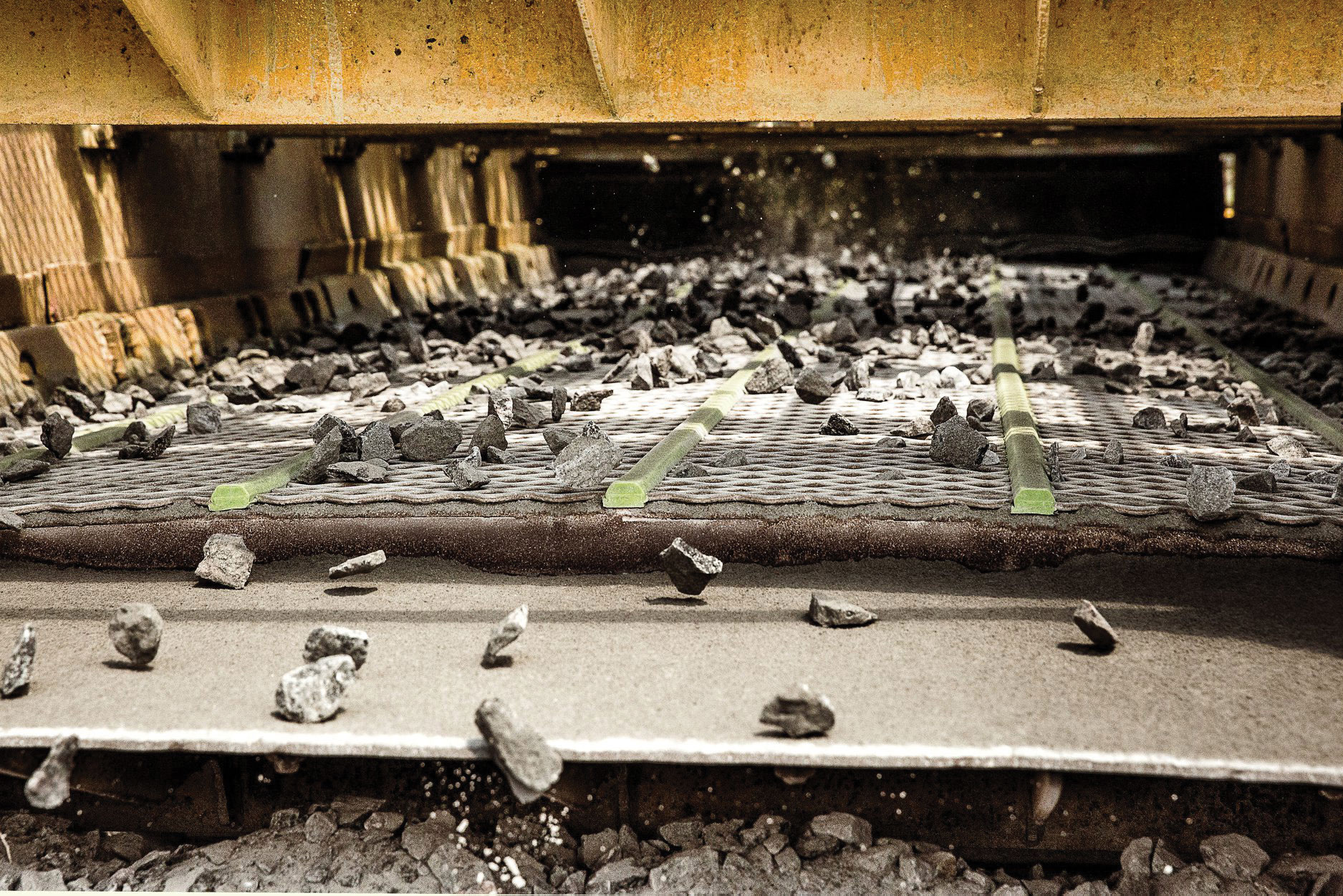
First published in the February 2022 issue of Quarry Management
Finding the best solution to common screening issues
By Lars Bräunling, MAJOR director of product technology
Persistent problems with uptime and production quality can be frustrating. Aggregates operations must work as quickly as they can to resolve issues and minimize losses from downtime and repairs. Common screening complications that operations face include contaminated piles, clogged screens, or lower-than-expected screen media life. Knowing how to diagnose problems and find the best fix can expedite the process.
Many of these problems have more than one solution. Operations first need to identify the issue and potential for future problems, then look to get them fixed. Material issues such as blinding, pegging, and carryover likely require a new style of screen media. Screen media breakage problems may require an alternative type of screen media, but often also an examination of the vibrating screen maintenance and the installation practices of the screen media.
First step: Identify the problem
While many problems are easily identifiable, it can be helpful to do a thorough evaluation of the process and look for any apparent screen media issues, in addition to the screen setup and equipment condition.
The easiest and most reliable way to identify problems and solutions is to work with an OEM-certified technician to complete a screening performance assessment. In this case, the expert is often the screen media manufacturer or dealer. Representatives are constantly encountering operations with new problems, giving them valuable insight into solving both common and unique issues. They also draw from a network of experts to help uncover solutions.
One key part of that assessment should be a vibration analysis conducted on the entire screenbox. This technology is advancing to a point where simple-to-use sensors have no wires, work well with a smartphone, and do not require shutting down the equipment. The process serves a dual purpose. First, it gives insight into screenbox health and has the potential to help spot abnormalities unseen by the human eye that could develop into costly problems, such as premature screen media wear. The software also visualizes the setup of the machine, which plays a huge role in the performance that can be expected for each individual job.
Following a vibration analysis, step back and take a good look at the equipment. Examine the screenbox and screen media for signs of wear or damage. Listen to the machine run to try to catch abnormalities or metallic sounds that could mean loose media, worn clamp bars, or broken wires.
Look also at the crusher feed belt coming off the screen. This is an easy way to check whether saleable rock is being sent to the crusher or conveyor because the deck capacity was exceeded. It could be the result of blinding, pegging, poor open area, non-ideal vibration setup, or the wrong screen media configuration.
Another good indicator is the condition of screen media in the scrap pile. Look at the underside of the spent screens to diagnose installation challenges. Black markings on the underside can show that the panels have moved and rubbed against machine supports, meaning they were not properly fixed in place as they should have been during installation. Shiny hooks are also a sign that the screen media was loose and moving back and forth during operation.
Pegging, blinding, and carryover
It is no secret that operations regularly face issues with near- or odd-size material pegging screens, or fine sticky material blinding openings. The depleted open area can ultimately result in carryover or contamination of the screened product, making this a costly problem.
The primary solution for these issues is often the choice of screen media. If using woven wire, consider high-vibration wire bonded with polyurethane strips. This setup allows wires to move independently, effectively dislodging pegged or blinded openings, such as when screening material with heavy clay deposits. The extra vibration also improves overall stratification.
Operations can sometimes also benefit from polyurethane or rubber screen media, especially with tapered openings to force material through. The flexibility of this type of media helps reduce some screening issues, while the material itself is highly resistant to impact and abrasion.
Generally, if the pegging and blinding is solved, the carryover should be reduced or eliminated, so long as the machine is not being overloaded. The improved stratification from high-vibration wire also greatly contributes to less carryover by increasing screening capacity.
Too much wear and early breakage
If the scrap pile is growing too quickly then it may be time to investigate a new screen media configuration. Ideally, the screen media should complement the three main phases of screening: the feed end, the middle of the deck, and the discharge end. Many operations use mixed screen media for optimal results.
Material of all sizes hits the deck at the first phase on the feed end. For that reason, this section should be able to handle large material impacting the deck, as well as fine particles. If the screen media in this area is wearing down or breaking too often, something more durable should be considered. Depending on the application, this could mean thicker wires, steel plate, rubber or polyurethane, or polyurethane strips reinforcing key parts of the screen deck. The middle of the deck should still be durable but may feature more open area to increase screening action. The discharge end generally features the most open area, because by this point any remaining material should be near- or oversize. Near-sized particles, for example, need the most tries to screen out successfully.
Some operations feature a reinforced media on the feed end and high-vibration wire screens — or self-cleaning screen media — on the rest of the deck. As mentioned above, the high-vibration media reduces common screening problems while maintaining an increased level of durability.
Another factor to consider is whether the problems may be caused by damaged equipment or improper installation. Proper tension is key for both the performance and the longevity of the screen media. Check tensioning weekly to ensure it is correct. Improper tensioning leads to early breakage.
Replace clamp bars that are getting thin or caving in order to prolong screen media life. Rubber or polyurethane-reinforced clamp bars are another option to improve longevity. Also, confirm there is a bolt in every hole to maximize durability. Make sure to purchase any replacement components, such as tension rails, from the OEM. Even the smallest deviation from the original design can lead to early screen media failure.
The counterpart of the clamp rails that contributes to proper tension is the crown curve of the deck. Tension cannot be achieved on a flat deck and on a curved deck any deviation will leave the screen hanging in the air, leading to improper tension and, ultimately, breakage. Additionally, check that all the support bars and rubbers are in good condition and that the panels are laying firmly on the supports.
Work with an expert
Consider scheduling screen media maintenance and installation training either with the manufacturer or a local dealer. The benefit of a trained team is knowing media is installed correctly and will have the longest wear life possible.
Work with an expert to conduct a thorough evaluation of the screening process to identify problems and the best solutions. Make sure to choose media that fits the application and the different phases of screening. Careful thought and selection can improve the bottom line and reduce headaches associated with downtime and lost profit.
For more information, visit: www.majorflexmat.com
- Subscribe to Quarry Management, the monthly journal for the mineral products industry, to read articles before they appear on Agg-Net.com