Custom-fit Screen Media
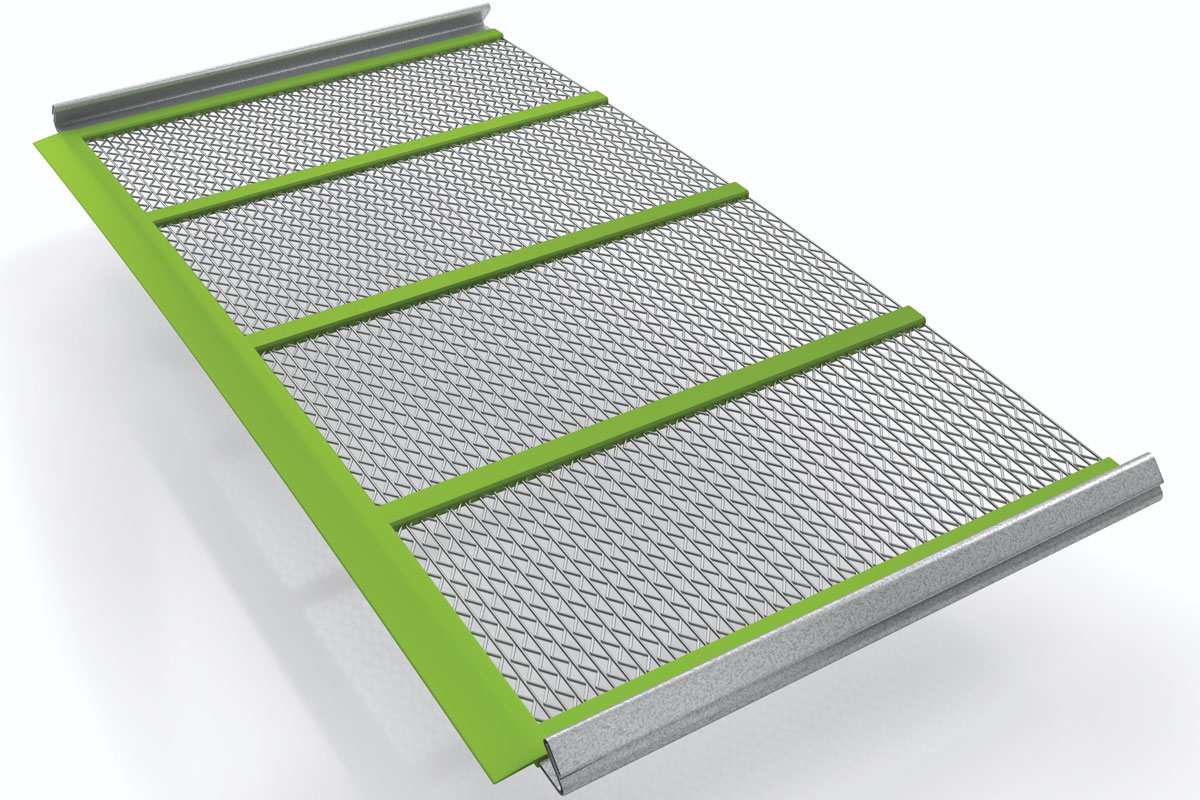
First published in the February 2021 issue of Quarry Management as MAJOR Variations
Enhanced customization with Flex-Mat custom-fit screen media in five styles
MAJOR, global manufacturers of high-performance wire screens, offer their Flex-Mat custom-fit screen media in five styles (D, DD, S, T and L) to suit a wide variety of material applications and to give producers options to improve efficiency and screening quality.
‘Our priority is to always provide screen media products that improve our customers’ profit margins and ease their workday,’ said director of product technology Lars Bräunling. ‘By offering different series of Flex-Mat, we can virtually guarantee the media’s profit-boosting qualities in a style that fits each application.’
The D series is the most commonly used style. It features single wires in the standard Flex-Mat pattern with square openings, making it particularly suitable for replacing square-opening woven wire for precise and accurate sizing of material while improving screening capacity.
This style prevents elongated material from passing through the screens and eliminates blinding and pegging. MAJOR say each opening is manufactured with precise 90° angles for maximum performance. The style is available in tensioned and modular setups.
Similar to the D series, MAJOR offer the DD series for producers with high-impact, heavy-material applications who still need a large amount of open area. The style features double wires and is said to offer durability without sacrificing productivity and screening performance, as can be the case with rubber and steel plate screen media.
The DD series is also said to eliminate the ‘popcorn effect’, which often causes larger rocks to bounce higher than smaller ones on single-wire vibrating screen media. MAJOR say operations can see as much as three times more wear life than traditional woven wire and 50% more productivity compared with steel plate and rubber panels.
If installed on a machine with a proper feed pan, a 4in (101.6mm) opening DD series setup can efficiently screen material sizes exceeding 8in (203.2mm). The DD series is available in tensioned sections, and producers can choose to add heavy-duty polyurethane strips for added durability.
The S series is designed for low-impact and low-weight round or cubical-shaped material, as well as for instances when precise passing is not required. It is also effective for sticky material. The style features an opening range from 0.059–2in (1.5–50.8mm) and is especially recommended in applications where it is important to remove fines and output a clean product on top of the screen, or when elongated material is not a concern.
The S series maximizes open area through the use of parallel wires that are not touching each other, which helps prevent blinding, pegging and lack of stratification. Material has less of an opportunity to stick to the surface because there are no holes to block. The style is available in modular and tensioned sections.
MAJOR offer the T series for fine screening with openings under 0.059in (1.5mm). This style is said to prevent the blinding, pegging, lack of efficiency and poor wear life seen in fine mesh. Featuring more open area than fine mesh, T-series wires improve stratification and increase wear life. Producers can purchase the style in tensioned and modular sections.
The L series is available for tensioned media and is suitable for producers working in natural sand applications and with sticky materials. The style, which offers a variety of opening ranges, starting at as small as 0.031in (0.8mm), helps prevent blinding while also improving production rates over other types of screen media. The sections are made up of straight parallel wires that cause almost no restriction against material going through the screen.
To improve wear life, MAJOR manufacture all Flex-Mat with polyurethane strips holding the wires together rather than the plastic strips or woven wire seen in other designs. As a result, opening sizes stay consistent for the life of the wires because the polyurethane strips outlast the wires.
MAJOR also offer overlaps and side seals to use in conjunction with Flex-Mat for enhanced screening performance. Overlaps prevent material from falling between two consecutive side-tensioned sections and contaminating material. Additionally, they can enhance performance by allowing material to pass from one screen to another without hitting the first wire on the second screen, increasing screen wear life.
Side seals prevent oversize material from falling between the screen section and the wall of the screenbox. They also improve ease of installation by allowing producers to order a narrower screen that can easily slide into the screenbox. The side seals will close the gap between the walls and the screen.
Flex-Mat ID Enabled
Meanwhile, MAJOR have introduced Flex-Mat ID Enabled – an RFID technology that tracks and stores screen media data such as panel dimensions and customer-defined details to offer users information at their fingertips for simple re-orders. The technology is said to improve convenience and productivity for any operation using Flex-Mat with ID Enabled installed, as it takes the guesswork out of re-ordering and prevents costly mistakes that can result from measuring incorrectly and ordering improperly sized screen media.
All Flex-Mat screen media are now embedded with the ID Enabled microchip, with product information easily accessed through the company’s new MAJOR app without the need of an additional reading device.
‘Our customers’ efficiency is always top priority, which encourages us to continue to push limits and be at the forefront of innovation in the industry,’ said MAJOR’s president, Bernard Betts. ‘We are introducing ID Enabled technology as a way to help customers track screen media specifications and improve accuracy during re-ordering, ultimately resulting in a more consistent end product.’
Operators simply scan the Flex-Mat panel with the MAJOR app to access product information, simplifying re-ordering and inventory management. MAJOR can also program the chip during production with some customer-defined information to improve convenience. Unlike some systems, users just need their smartphone to view the data and do not need to use a separate RFID reader.
Prior to ID Enabled technology, operations required time-consuming gauge measuring – by hand – to order properly sized media, which left room for human error. Even the slightest mismeasurement could mean ordering the wrong size screen media, resulting in material not meeting proper specifications and leading to lost profits. ID Enabled also allows operations to track orders with an electronic record instead of paperwork.
For further information visit: www.majorflexmat.com
- Subscribe to Quarry Management, the monthly journal for the mineral products industry, to read articles before they appear on Agg-Net.com