CMB Horizontal Screen Installation for Thomas Armstrong
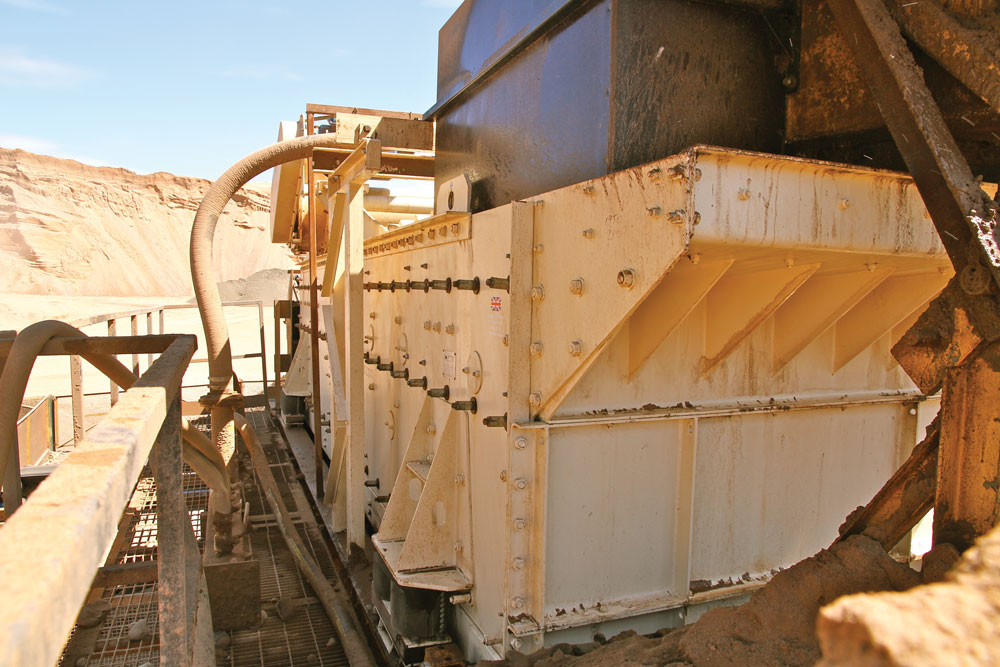
First published in the August 2018 issue of Quarry Management as Back on the Level
CMB International bring production back on line at Overby Quarry with new ‘Dual Drive’ horizontal screen
Located near the village of Aikshaw, in Cumbria, Overby Quarry is owned and operated by Thomas Armstrong (Aggregates) Ltd (TAL), part of the Thomas Armstrong holding company.
The company’s Aggregates division consists of two sand and gravel operations, one at Overby and a second near Carlisle, where material is extracted from a lake by dragline. Within this division the company operates a fleet of 60 trucks that cover tipper, crane, tanker and flat-bed work.
The fleet operates out of Overby Quarry transporting sand and bagged and bulk aggregates to block-making and ready-mixed concrete plants, builders and construction sites within a 90-mile radius.
Overby Quarry is a long-established site that was originally jointly worked by TAL and another company. TAL also worked the adjacent New Cowper Quarry, which was closed 15 years ago and reinstated.
At this point TAL decided to acquire the whole of Overby and move all their processing to this site. In the years since then the quarry has been expanded with the original wash plant being upgraded to maximize the end products.
Currently, the processing plant is producing washed concrete sand, building and plastering sand, and 10 and 20mm gravel at a rate of 4,000 tonnes per week.
Recently, the primary washing screen had suffered from numerous bearing failures, and after frequent and considerable downtime, the team at Overby decided to seek a suitable replacement screen.
Transport director Ian Morrison said: ‘We researched the market for a replacement and it was suggested to us that CMB International are excellent manufacturers, so after an initial meeting and site survey we placed the order for the new screen with them.’
CMB International are highly experienced manufacturers who design their own range of feeders, jaw crushers, cone crushers, screens and conveyors. In addition, they carry a comprehensive stock of spares and offer on-site maintenance and modifications for existing plant. Their in-depth knowledge allows them to repair and refurbish plant produced by all leading manufacturers.
Capable of handling up to 650 tonnes/h, depending on the application, CMB supplied TAL with a new CMB 280 ‘Dual Drive’ 1.8m x 6.0m triple-deck horizontal screen that was designed to fit in the original envelope and pick up on existing feed and discharge points. New spray bars and a new spray bar support structure were also supplied.
Liam Holland, general manager of CMB International, commented: ‘TAL engineers removed the old screen and fitted the new one, and our engineers commissioned the screen. We had to make a few adjustments as the new screen was too close to an existing beam that would have fouled it whilst running.
‘We took some measurements and manufactured some packers to lift the screen away from the beam, whilst still picking up the feed and discharge points. This issue was corrected within a few days of the screen being installed.’
The new screen at Overby is driven using a ‘Dual Drive’ twin-shaft unit with two on-board electric motors, which is a tried and tested CMB design that has been utilized on many major installations in the UK.
CMB horizontal or low-angle screens, which are particularly suitable where height is critical, can be supplied with up to four decks for use in sizing or scalping applications. The size range is from 1,220mm x 2,500mm (4ft x 8ft) up to 1,500mm x 9,600 (8ft x 30ft).
The screens feature a straight-line vibrating motion, which is produced by an oil-lubricated vibrator unit with two or more counter-weighted eccentric shafts geared together and mounted on spherical roller bearings.
By varying the timing of the gears, the vibrating motion can be fine-tuned to assist optimum screening of various aggregates, whilst coil springs efficiently isolate the screen from its supporting structure. The decks themselves are rigidly constructed from generously sized box-section, which, unlike I-section, eliminates trapped material that can cause wear to the cross-members.
Numerous other benefits include friction checks built into the screen supports, which efficiently retard the screen during shutdown, thus reducing the forces transmitted to surrounding structures.
CMB say maintenance of their horizontal screens is simple with generous height between decks allowing for easier screen media changes. Moreover, if spray bars are required, they can be built into the screen side-plates, thereby eliminating spray bar supports and improving maintenance access.
Summing up, Ian Morrison said he would be happy to recommend CMB International to anyone in the industry. ‘We are extremely pleased with the screen and the service that CMB have provided. We are now in full production again with the screen making the operation more efficient.’
- Subscribe to Quarry Management, the monthly journal for the mineral products industry, to read articles before they appear on Agg-Net.com