Under the microscope: Conveyor Belt Costs
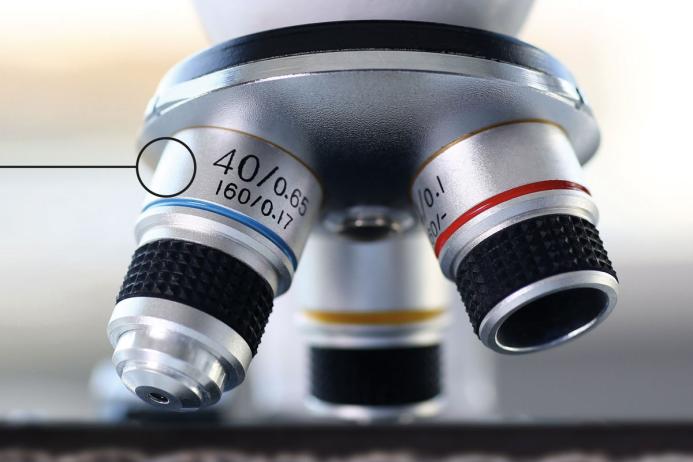
First published in the May 2025 issue of Quarry Management
When ordering conveyor belts, always try to keep it simple. Conveyor belt specialist Leslie David explains
Replacing conveyor belts can be a costly process, not only in terms of the belt itself but also the cost of downtime while it is being fitted. Every year industry spends millions replacing belts, yet, ironically, a great deal of that expenditure could be avoided by having a better understanding of conveyor belt manufacturing and stock control processes, and applying a few simple buying principles.
Countless permutations
When you consider the different types of rubber-covered fabric-ply belts, such as abrasion resistant, rip and tear resistant, oil, fire, cold and heat resistant, and then multiply those types by different DIN/ISO quality standards applicable to each type, you immediately have a very large number of permutations. However, these permutations must then be multiplied again by variables such as tensile strength, width, cover thicknesses, and number of plies. The permutations created are almost countless.
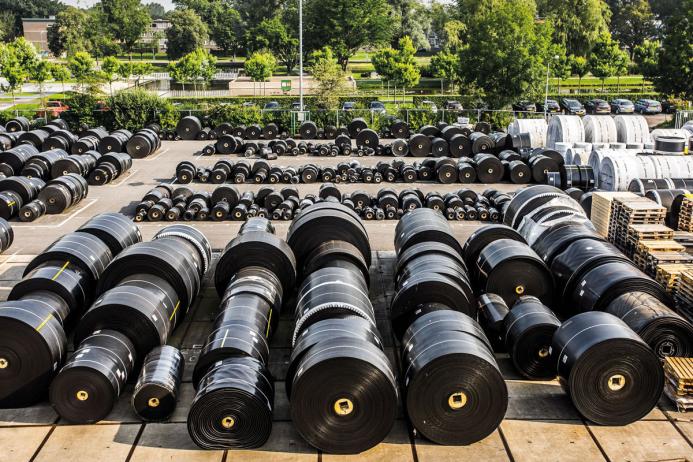
This presents a big challenge for manufacturers; what quantities of each to manufacture, and, for manufacturers, service companies, and traders, what to hold in stock? Understanding this is important because these permutations act as a major influence on the buying process and, ultimately, on the price and, therefore, the quality and longevity of what can be afforded.
Cost-effective manufacturing
As with virtually all production processes, good economy of scale is essential. The longer the uninterrupted production run of a specific type, size, and specification, the lower the unit cost. The same principle applies to the raw materials being fed into that production process.
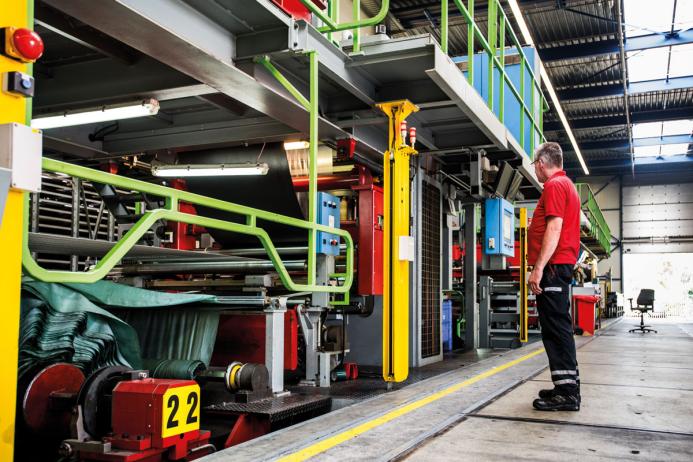
The different permutations together with the principles of economies of scale must then be combined with a third factor, which is the level of demand, commonly referred to as the ‘fast movers’. Together, these three factors not only dictate what is manufactured in terms of type and volume, but also what is held in stock and therefore, by default, what needs to be made to order. Probably the most popular ‘standard stock’ belt is EP 400/3 4+2mm DIN Y abrasion resistant belt. However, even the slightest deviation from that specification will cause it to become a ‘made-to-order’ belt.
Made to order
The term ‘made to order’ applies to any belt specification that is not regularly produced and held in stock. Perhaps a more accurate term would be ‘Made to cost a lot more than is probably necessary’, because making a belt to order presents significant challenges and additional costs. To begin with, unless the belt is at least 200m in length, the manufacturer (and therefore the buyer) does not begin to benefit from economy of scale. In fact, quite the opposite because the production line must be stopped and set up to accommodate the change of specification and, as always, time is money.
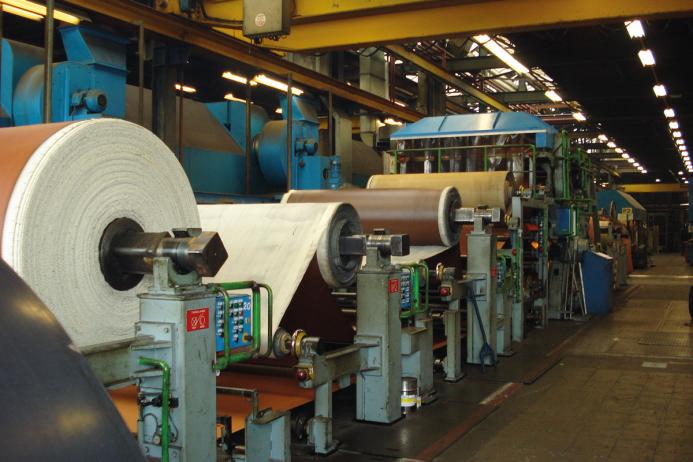
Other economies are also lost in relation to the width of the belt because standard-width stock belts are usually made as wide as the manufacturing machinery will allow to maximize efficiency of production and to reduce the wastage of raw materials such as the fabric plies. The finished product, known as ‘slabs’, are then cut and sealed to create a variety of popular narrower widths. For example, 400m of 2,200mm wide belt would be manufactured and then slit (cut) to produce 400m of 1,000mm wide belt and 400m of 1,200mm wide belt.
Lead times and downtime
Having a belt unnecessarily made to order not only increases the cost but, in the event of needing a full replacement, seriously increases the amount of costly downtime. Whereas standard stock belts can usually be delivered quickly, the manufacture and delivery of a bespoke belt can take several weeks and sometimes months.
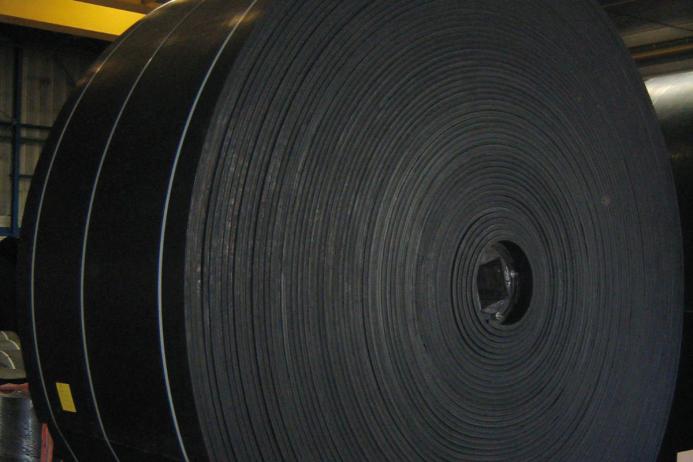
This is because every order needs to be scheduled into a pre-existing production programme. Almost invariably, this is managed on a ‘first come, first served’ basis with lower priority understandably being given to short length orders (less than a full 200m roll). Bearing all this in mind and applying it to buying conveyor belts hopefully makes the following guidance much more logical.
Rubber quality is more important than thickness
One of the most common reasons for non-standard specifications is inflated cover thicknesses. For example, ordering an EP 630/4 belt with 8+3mm covers rather than the commonly stocked 6+2mm thick covers. Usually this is simply because the covers are wearing too rapidly and damaged too easily, especially the top cover, which proportionately wears four times faster than the bottom cover. Although increasing the thickness would seem to be the easiest way to improve belt life, experience proves that this is rarely the case.
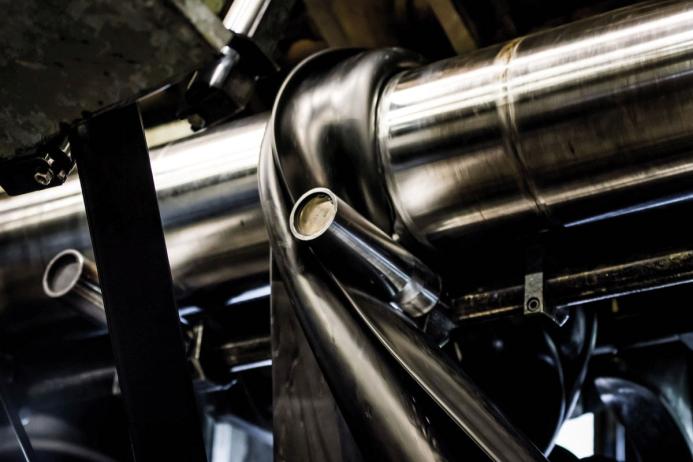
The biggest reason for rapid belt cover wear and damage is that the rubber compound does not provide the necessary level of resistance to wear and tear. For example, a manufacturer may claim that the rubber meets DIN Y (ISO 14890 L) standards for abrasion resistance (maximum volume loss in cubic millimetres of 150mm3 under ISO 4649/DIN 53516 test methods). However, in reality the wear resistance may only be borderline at best or, as laboratory testing consistently confirms, be among the 50% of belts that do not even reach the minimum required standard.
(As a reminder: When comparing abrasion test results, higher figures represent a greater loss of surface rubber under testing, which means that there is a lower resistance to abrasion. Conversely, the lower the figure the better the wear resistance).
Increasing the cover specification
The most common cover type is abrasion resistant and within that there are three standards: DIN Y (ISO 14890 L), DIN X (ISO 14890 H), and DIN W (ISO 14890 D). The most commonly used and, therefore, most highly stocked is DIN Y (ISO 14890 L). As with the thickness of the covers, another frequent reason for deviating from standard stock options is an increase in cover specification, usually specifying DIN X rather than DIN Y to compensate for rapid wear problems.
It is important to remember that one manufacturer’s DIN Y grade belt can often outperform another manufacturer’s allegedly superior DIN X grade belt by a considerable margin. For example, Fenner Dunlop’s DIN Y standard rubber (RA grade) has some 20% more abrasion resistance compared with the more costly DIN X standard. This especially applies to low-priced belts imported from south-east Asia rather than those genuinely made in Europe. DIN X cover grade belts are rarely kept in stock so beware of a promise of quick turnaround on your order because it is not unknown for DIN X grade belts to be substituted with DIN Y grade.
Bigger is not better
Another reason for non-standard, extra-thick belt specifications is a consequence of attempts to overcome rip, tear, and impact damage caused by demanding environments and aggressive materials. To try to prolong operational lifetime and minimize repairs, many conveyor belt users fit belts with extra-thick covers and/or extra plies, but this is invariably a mistake because the conveyor will not have been designed to operate using increased belt dimensions.
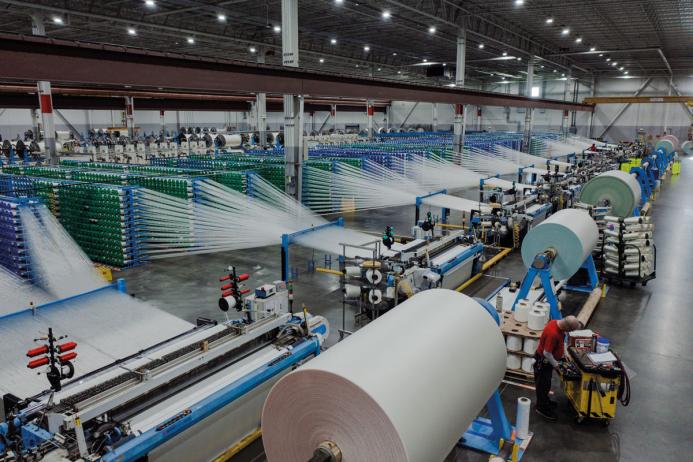
The fact is that the greatest influence on the strength and other essential physical properties of a conveyor belt is the design and quality of the ply material used to create the carcass. As a result, the most practical and economical solution to rip, tear, and impact problems is to fit a belt that has been specifically engineered for the purpose, especially the strength and weave design of the fabric. A good example is Dunlop UsFlex, which is so popular, that it is available from stock.
Belt edge selection
Over-specifying the type of belt edge can also result in a belt having to be unnecessarily made to order. Despite the enormous advances in technology, a great many belt buyers seem to retain outdated beliefs. There are only two commonly used types of belt edge, moulded edge and sealed edge. Many years ago moulded edges were the standard because cotton was used as the reinforcing fabric in multi-ply belts. A fully covered rubber edge was, therefore, essential to prevent moisture penetrating the cotton fabric and causing it to rot. However, since the introduction of synthetic ply fabrics using polyester and polyamide, this problem effectively no longer exists.
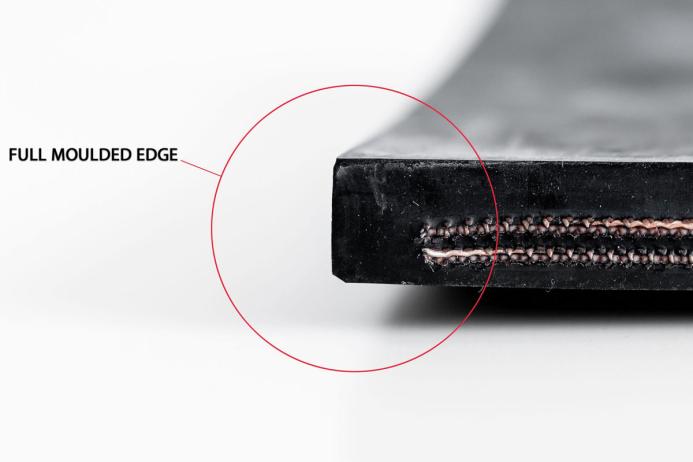
Moulded edges can only be created when a belt is manufactured to an exact width. During the calendaring of the belt, a small strip of unreinforced rubber is attached to the side of the carcass, which becomes an integral part of the belt during the vulcanizing process. It is important to note that moulded edges do not provide any structural advantage and can be susceptible to damage.
The most common type of belt edge is the ‘cut and sealed edge’ or simply ‘sealed edge’. As previously explained, standard-width stock belts are usually made as wide as possible and then cut and sealed in a variety of widths. This is why the vast majority of rubber fabric-ply belting held in stock by manufacturers, distributors, and traders has sealed edges.
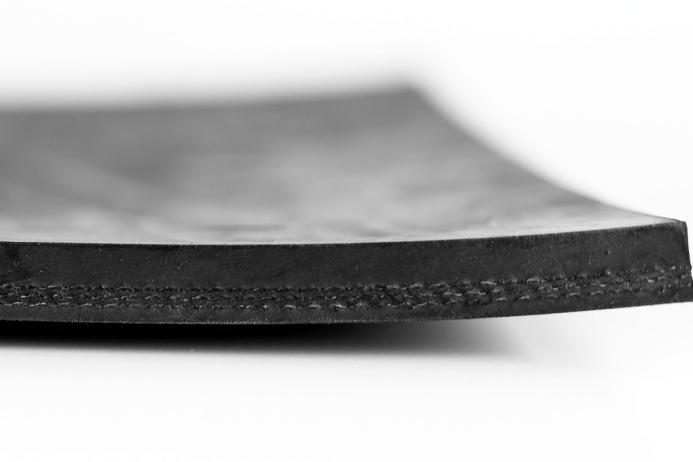
Specifying moulded edges when they are not entirely necessary invariably means that the belt needs to be made to order rather than supplied from stock (especially for lengths shorter than 200m/full roll) and significantly increases the price and delivery lead time.
Common reasons
There are two common reasons that cause conveyor belts to be made to order rather than supplied from standard stock ranges. First, it is the perceived need to increase the specification in order to achieve improved performance and operational longevity, and secondly, it is because of a lack of understanding of the negative cost and lead time implications. Almost without exception, a well-made, premium quality belt supplied from stock will deliver the shortest lead times, best performance, and lowest ‘whole-life cost’.
Conclusion
Always try to specify belts that manufacturers and suppliers are most likely to have in stock. If you are not sure, be prepared to be flexible by asking for the nearest technically suitable alternative options from stock. These may even be higher specification but, because they do not have to be made to order, may be less expensive and certainly much faster in terms of delivery time.
About the author
After spending 23 years in logistics management, Leslie David has specialized in conveyor belting for more than 18 years. During that time he has become one of the most published authors on conveyor belt technology in the world.
Subscribe to Quarry Management, the monthly journal for the mineral products industry, to read articles before they appear on Agg-Net.com