Modified ToughFlex belt for overband magnets
Bunting join forces with Smiley Monroe to create modified heavy-duty belt for harsh applications
BUNTING have joined forces with Smiley Monroe to modify a ToughFlex belt for overband magnets. The new belt is more resistant to excessive wear in arduous working conditions.
Overband magnets have a permanent or electromagnetic block mounted between two pulleys over which a cleaning belt runs continuously. In operation, the overband magnet is suspended over a conveyor transporting material such as quarried rock or industrial and commercial waste. The magnetic field of the centrally located magnet block attracts ferrous metals and other magnetic materials up and out of the conveyed material. Between the magnet box face and the separated metal is the moving cleaning belt with upstands, which transfers the captured material away from the conveyor and out of the magnetic field into a separate collection area.
The separated metal is often angular with sharp edges, which can damage the rubber cleaning belt. In certain applications, such as when handling industrial and commercial waste, there can be a high content of metal in a form that commonly causes belt damage. In particular, customers using Bunting’s ultra-strong but lightweight ElectroMax overband magnet achieve high levels of metal separation but with a higher rate of belt wear.
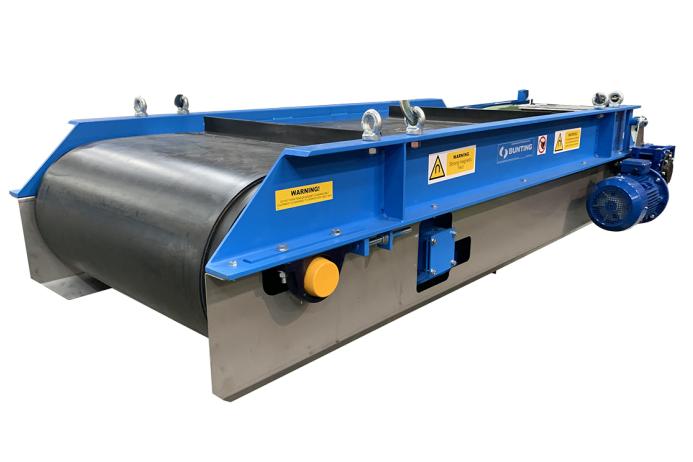
Whilst assessing methods to extend belt life in difficult applications, Bunting approached Smiley Monroe, leading producers of endless conveyor belts, cut rubber, and plastic parts for the materials processing equipment manufacturing sector. Smiley Monroe routinely test the abrasion resistance, tensile strength, and adhesion levels of both the cover rubber and fabric plies of their raw materials and finished products in their well-equipped labs, to ensure conformity to DIN, ISO, and company standards.
After considering several options, Smiley Monroe recommended the ToughFlex belt, which is designed to handle the toughest conveying applications, from bulk handling to mobile crushing. The belts are constructed with a special weave of two fabric plies and an additional binder warp. The plies are reinforced to resist puncturing and are protected with heavy-duty, wear-resistant top and bottom covers.
The belt material and design met the criteria for reducing damage from ferrous metal piercing and tearing the belt, even when the metal pieces are extremely angular with multiple sharp edges. This means less maintenance and extended production hours between replacing belts.
Once the belt material had been selected, the engineering design teams at Bunting and Smiley Monroe worked together to modify the belt for use on an overband magnet, adding integrally moulded cleats for the transfer of captured ferrous metal.
‘We are continually looking to make improvements that help our customers,’ explained Bunting technical director Adrian Coleman. ‘An increasing number of our customers are turning to the ElectroMax overband magnet because of its increased magnetic power yet compact design. However, for certain applications we identified the benefit of using a belt with better wear characteristics and therefore contacted Smiley Monroe.’