The Issues Surrounding Level Monitoring in Screen Houses
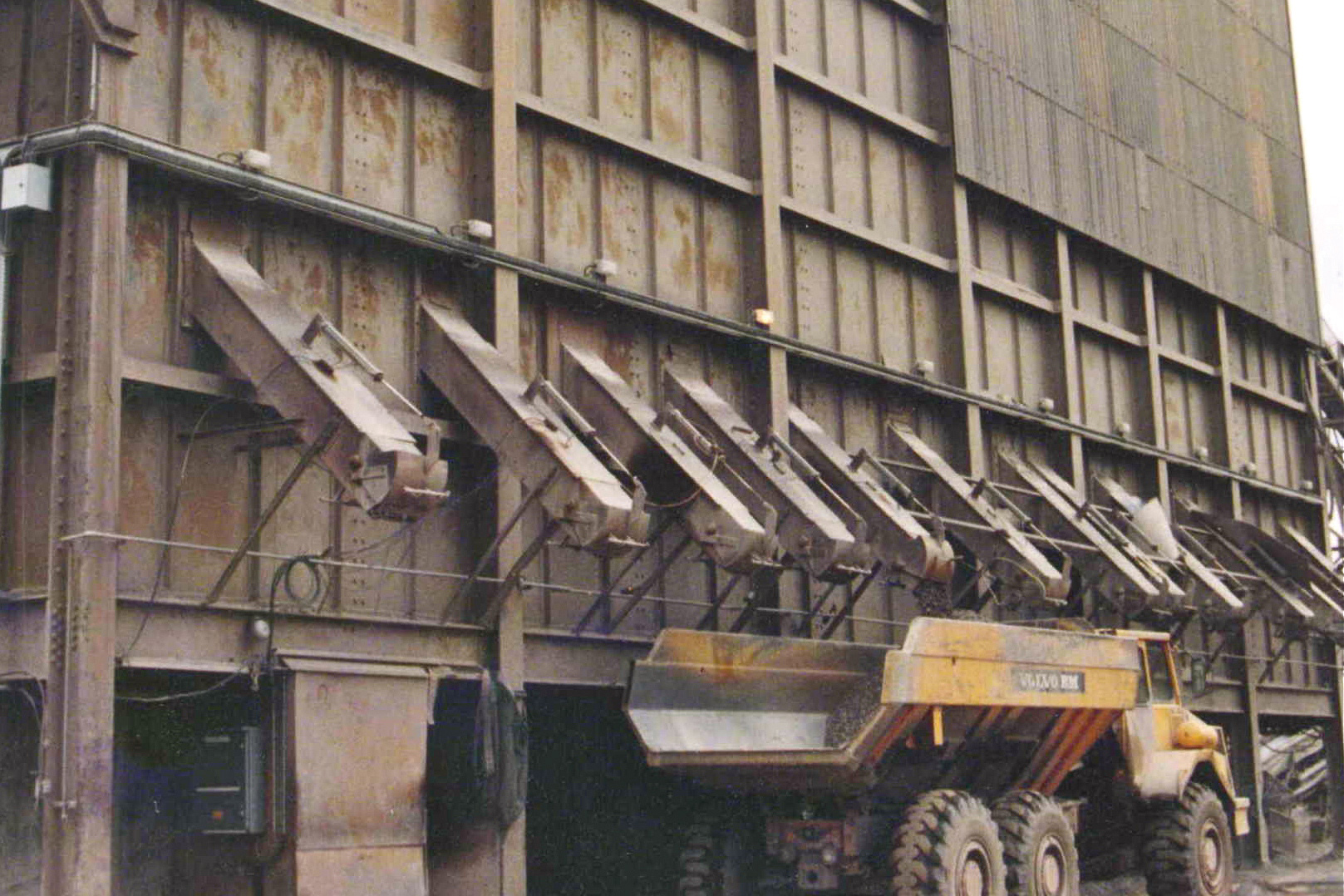
First published in the February 2016 issue of Quarry Management as Stars of the Screen
Reliable level measurement can improve screen house productivity and reduce downtime. Level measurement experts Hycontrol examine the issues surrounding level monitoring in screen houses and outline the optimum measurement solutions for this challenging environment.
Screen houses are a standard feature in the quarrying industry. The design and size of screen houses varies from site to site, but they all fulfil the same basic function. Usually, belt conveyors are used to feed processed, crushed stone to the top of the screen house, whereupon the rock passes over a series of different-sized vibrating grilles which initially allows the smallest particles of dust and stone to fall through into a bin below.
As the remaining unsorted rocks descend a ‘staircase’ of slightly angled, vibrating screens, progressively larger pieces of rock, up to a size of 60mm, are allowed to pass through into the appropriate bins. After screening, the sorted stone can be released from one of the discharge points at the bottom or side of the bin for use in a wide range of potential applications, including aggregate, concrete, roadstone and general construction.
The challenges of screen house level monitoring
Reliable level control is essential in the harsh environment of the quarry screen house, but there are many challenges that this vital monitoring equipment will have to withstand, both in terms of the environment of the screen house and the characteristics of the product being monitored.
Screen houses are usually large, noisy environments with many potential hazards for workers, including high levels of dust, limited visibility and large oscillating plant. As such, appropriate goggles, filter masks and ear defenders must be worn at all times by staff working in these buildings. Clearly, this abrasive environment will also have a detrimental effect on any equipment that is used, including the vital level measurement instrumentation used to monitor the sorted stone in the bins.
Reliable level control is essential not only for inventory purposes when the stone is removed, but, more importantly, for preventing overfilling of the bins. Product overflow will inevitably lead to equipment damage, plant downtime and a costly clean-up, not to mention the potential for health and safety issues. The worst-case scenario is if excess product lifts a screen off its vibrating mountings. Bearing in mind that some screens can be mounted up to 30m above ground level, this is nothing short of a catastrophic event.
Such an event is likely to cause extensive damage to the screen house, creating a hazardous working environment and leading to significant downtime while the very difficult and potentially dangerous task of repairing the screen is carried out. Moreover, the cost of such an event can be considerable with lost production and repair charges.
However, the nature of the screen house environment restricts the level measurement options that are available. Strain-gauge load-cell and force-based systems, which work by fitting special strain sensors to key parts of the load-bearing structure of a vessel, are highly sensitive devices and are, therefore, unable to cope with the constant vibration of the screen house structure.
Likewise, contact-based level measurement technologies such as TDR (time domain reflectometry – sometimes erroneously called ‘radar on a rope’) and outdated plumb-bob meters are both unsuitable for the screen house environment. Whilst both technologies have many other successful applications in the quarry environment, in the screen house they are far too likely to be damaged by the falling stone and so would be limited to use on the dust bins only.
This leaves a choice of two technologies that are suitable for screen house level measurement, namely ultrasonics and radar.
Ultrasonics
Ultrasonic technology provides a highly cost-effective, easy-to-install, non-contact solution for a wide range of solids level measurement applications. The transducer, mounted at the top of the vessel, emits sound waves that are reflected back from the surface of the material. The instrument measures the ‘time of flight’ of these waves in order to calculate distance, from which is discerned the level of product in the vessel.
Frequencies as low as 5kHz are used on long-range solids materials and higher frequencies at 40kHz or above are used on shorter ranges. The latest low-frequency ultrasonics can be used for ranges of up to 60m, although a number of environmental and operational factors within the silo can reduce this range. Whilst traditional ultrasonic devices struggled with the effects of false echoes and temperature changes, the latest corrective software can compensate for a number of adverse operational factors relating to weak and false echoes caused by dust, internal silo structures (for example ladders or cross-braces) and temperature changes affecting time of flight.
It should be noted that when using ultrasonics, consideration has to be given to the so-called ‘dead band’, a range directly below the transducer face where measurement is not possible. This area can vary from 300mm to 1,500mm, depending on the frequency being transmitted. However, this usually only presents a problem for applications with shorter measurement ranges and rarely affects screen house applications.
Radar
Frequency modulated continuous wave (FMCW) radar level measurement systems use high-frequency microwave signals (24–26GHz) that are unaffected by dust, pressure, temperature, viscosity, vacuum or foam. The measured level is proportional to the difference in frequency between the transmitted microwaves and those reflected back from the product surface.
This technology is suitable for measurement ranges up to 80m and provides high levels of accuracy for certain applications. However, the effectiveness of radar technology is dependent on the dielectric constant of the material in the vessel. Radar usually works better on products with a dielectric constant greater than 2.0, and in the case of rock in a screen house this is not generally an issue. However, radar equipment is more expensive than ultrasonics, which may be a deciding factor for certain applications.
Effects of filling and emptying
It is important to understand the way in which vessels are filled and emptied when installing level measurement systems, in order to optimize performance. This is especially important given the unusual shape and properties of a screen house. In a normal silo with a width of less than 3.0m, with centrally located single fill and draw-off points, the way in which material behaves is usually repeatable. A single level sensor, located away from the fill point, will usually provide reliable and consistent results (see fig. 1). It should be noted that, depending on the size of the vessel and properties of the material, it may be necessary to locate the sensor an equal distance between the centre and outer edge of the vessel.
Complications can occur with vessels that have multiple fill and draw-off points, as in the case of quarry screen houses (see fig. 2). Typically, bins have three discharge points and this will result in unpredictable product level behaviour. This means that a single sensor located on one side or the other of the vessel will not provide an accurate gauge of the contents – for example, product may come to rest largely on one side of the bin and a sensor located on the opposite side may erroneously show the tank to be empty or near empty. Looking at the vessel shown in figure 2 (example 1), this would be the case for a sensor located at point B. With the ‘staircase’ of screens that runs down the centre of the building, generally it is not possible to centrally locate a sensor in a screen house – the falling product would soon erode it away. Whilst covers could be fitted, it would be extremely impractical to gain access in order to service and conduct maintenance on the sensor.
The most effective solution is to mount two level sensors meters, each an equal distance from each side – in the two examples shown in figure 2 this would be at points A and B. The readings from each sensor are used to discern the average product height in the vessel. This is done simply by feeding the information from both probes to a site PLC or locally mounted display panel where the readings from sensors A and B are added together and divided by two to give the average contents level for the vessel. This also provides the user with separate levels for both sides of the screen, making it easier to decide which point to draw the product from – for instance, in figure 2 (example 2) the product should be taken from draw-off points 1 and 3 to lower the product height at the sides of the bin.
Maintenance
As has been mentioned, level equipment in a screen house is exposed to potentially damaging abrasive material, dust and vibration throughout its working life, so, not surprisingly, the cleaning and maintenance of level equipment in this unpleasant environment is often neglected.
This is a fundamental error and one that will ultimately accelerate the failure of the equipment. For process-critical equipment, maintenance is essential to ensure ongoing functionality and should be regularly scheduled. This should include not only cleaning and visually checking that the equipment has not become damaged, but also a thorough check of the functionality and calibration of the sensors. This will ensure optimum output levels and eliminate the risk of signal drift. Ideally, this should be carried out by experienced specialist engineers as part of a regularly scheduled maintenance programme.
Conclusion
The need for reliable level control in screen houses is clear and well understood by quarry staff. However, achieving that reliability in such a harsh environment continues to be a challenge. It is now accepted that the use of a single sensor will not provide sufficient accuracy, but two sensors will give optimum performance. The chosen instrumentation must provide the precision and reliability required to monitor levels within a dusty atmosphere, whilst having the robustness and durability to cope with damaging environmental conditions. Ultrasonics and radar both meet these different challenges and, when correctly installed, provide reliable level measuring solutions for the screen house. In parallel, regular maintenance is essential for maintaining and prolonging the working life of this equipment. By ensuring all these factors are considered, better screen house performance and a lower overall cost of ownership can be achieved.
- Subscribe to Quarry Management, the monthly journal for the mineral products industry, to read articles before they appear on Agg-Net.com