The Increasing Use of Mobile Stockpile Conveyors
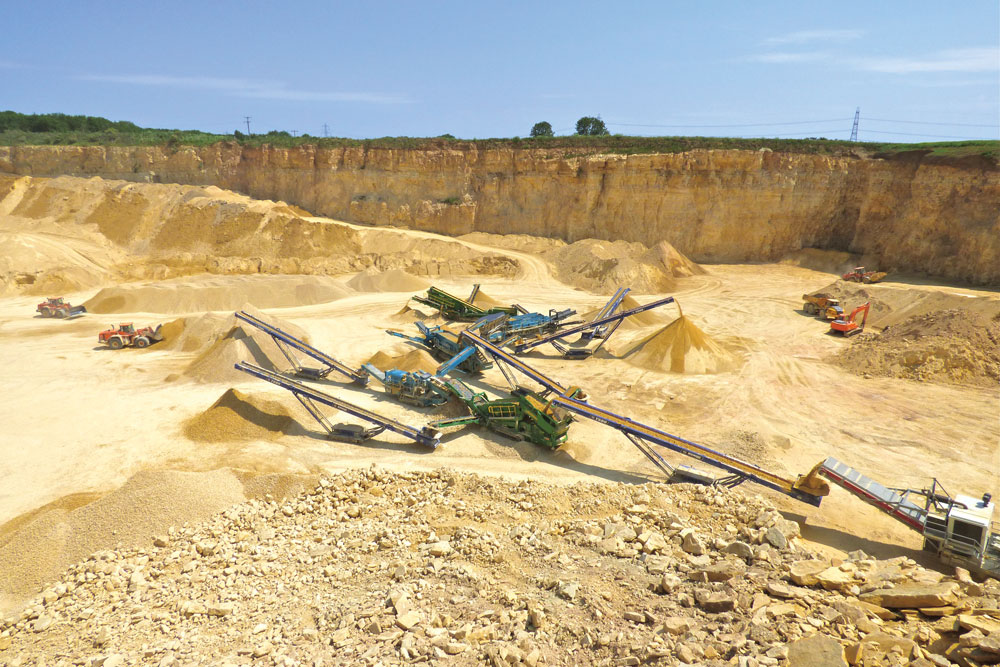
First published in the August 2017 issue of Quarry Management as Material Movers
From port terminals to quarries, mobile stockpile conveyors are increasingly being added to mobile crushing and screening fleets, thanks to their operating efficiency and cost-effectiveness
Conveyors offer the most cost-effective means of transferring or stockpiling bulk materials on the market. Within the quarrying industry, mobile conveyors offer an efficient, reliable and robust material-handling solution that reduces the operator’s dependency on haul trucks or wheel loaders, whilst offering a reduction in downtime and a longer equipment lifespan.
The extensive list of conveyor types and options available to quarrying operators is testament to the various benefits they can bring to such operations. Differences in discharge height and transfer length requirements, the condition of terrain, the availability of power, the frequency of repositioning, throughput and, of course, budget are all among the factors that have driven the market to create a large range of mobile conveyor models. A quick look at the extensive material-handling range offered by EDGE Innovate alone serves to highlight the various solutions available to meet the different challenges faced by operators, not to mention the extensive list of materials that are being transported.
Quarry operators are continually striving for improved productivity whilst attempting to bring their overall cost per tonne down. For this reason, in last two or three decades quarries have increasingly looked towards the use of mobile crushing and screening equipment. Having a mobile plant that follows the quarry face has become a more common sight in operations around the globe, to such an extent that the utilization of plant in this way is no longer questioned; it is now a well-proven operational model.
The switch from bringing the plant to the material rather than transporting material to the plant has obvious-cost saving benefits. The static conveyors that were once the mainstay of many quarrying operations and which were relied upon to move hundreds of tonnes per hour now find themselves ‘moving’ further away from the action.
To benefit from the efficiencies and cost savings resulting from the integration of conveyors to move or stockpile material, operators have turned to mobile stockpile conveyors to complement their fleet of mobile crushers and screeners. As one of the leading manufacturers of feeding and conveying solutions with decades of experience and thousands of conveyors installed throughout the globe, EDGE Innovate say they are well aware of the benefits mobile conveyors bring to operators across various applications.
Benefit of stockpiling via conveyors
As the short discharge conveyors found on most mobile screeners or crushers are generally only capable of creating small stockpiles, wheel loaders are often employed on rehandling duties, with material constantly being moved from the initial stockpile to another larger stockpile, before eventually being loaded on to trucks. Quarries that employ this system are effectively handling the finished products at least twice. By introducing mobile conveyors or stockpilers into the processing line, operators can leave crushers and screens running, with the wheel loader only having to move the finished product once – directly into the delivery truck. Ultimately, this can eliminate the double handling of material and reduce the operator’s cost per tonne.
Bigger throughput
Another big advantage enjoyed by operations that employ conveyors for stockpile creation is an improvement in production. With crushers and screeners no longer starved, operators can focus on continuously loading feed material, leaving conveyors to create larger stockpiles in a much smaller area. This is achieved by a stockpile conveyor’s ability to reach much higher discharge heights. In many circumstances improved production can eliminate expensive overtime needed to meet productivity demands and reduce the maintenance work that results from increased running hours. Studies have shown that a wheel loader, with its greater number of moving parts, shorter service intervals and more expensive components, can cost up to 95% more per year to maintain than a conveyor.
There are also health and safety benefits to be gained by integrating mobile conveyors into the processing line. By eliminating the use of loaders when stockpiling materials, the volume traffic moving about on the site is reduced. Studies have shown that more than 40% of waste and recycling site accidents in the UK occur due to manoeuvring or operating vehicles. In addition to the health and safety benefits, stockpile conveyors can also make a significantly contribution to towards environmental improvements, such as reductions in noise, dust and emission levels.
Financial rewards
Having the ability and flexibility and to adapt to new challenges is vital for any successful business. Cash flow is a continuing problem for one in five small business owners, although larger businesses are just as likely to encounter cash flow problems, if not more so, than the smallest. On average, wheel loaders command a retail price of around £180,000, representing a substantial financial outlay and one that may hinder the successful financing of other vital equipment to allow a business to grow.
As an alternative to wheel loaders, stockpile conveyors represent a considerable financial saving in capital costs, thereby freeing up vital funds to help a business expand, whilst also delivering significant reductions in fuel consumption – the EDGE TS-Series tracked stockpiler, for example, consumes less than 10 litres/h. Any reduction in the number of wheel loaders at a site will also lessen the need for drivers, thereby helping to diminish high labour costs. In addition, conveyors have the ability to operate at a maximum efficiency with minimum supervision during every hour of operation, thus reducing labour costs still further.
Which conveyor and what to consider?
Even when a quarry operator makes the decision to opt for a mobile conveyor solution, there are further considerations to be taken into account, such as the choice of a wheel- or track-mounted conveyor. Every operator has different needs and challenges to overcome, and how they wish to integrate the conveyor into their existing system and how they want to stockpile their materials will determine the type of conveyor they are seeking. There are pros and cons to all conveyor formats.
The track-mounted option is particularly suitable for operators who frequently reposition their conveyors. A tracked stockpiler is an independent self-propelled unit that can be easily and quickly manoeuvred across rough terrain, although it may not be the ideal product for the creation of radial stockpiles. The mobile (wheeled) stockpiler can have the added advantage of a radial stockpile function, but it will have to be towed by another self-propelled vehicle. The ultimate solution is to combine the best of both formats into one unit. A radial tracked stockpiler encompasses a track unit with radial stockpile functionality.
Loading method
Operators must also take into consideration other deciding factors such as loading methods and applications. If the conveyor is to be loaded directly by excavator or wheel loader then a feed conveyor would best suit this application, whilst a low-feed track stockpiler would be the best option for those wishing to load directly by wheel loader on all three sides of the hopper but who do not want the extra cost of constructing ramps. To run a constant material feed while retaining the ability to track parallel to, for example, a barge, a conveyor with a 360° slew functionality would provide the flexibility required. EDGE pioneered the inclusion of slewing technology with their LTS 360° Unlimited range.
Power source
The way in which operators wish to power their conveyors will also vary depending on the application and material being transferred. Other determining factors may include the availability of diesel or electricity, the current power source being utilized, the capabilities of the operator’s service staff, the throughput required, and past experiences.
The biggest advantage of a self-contained diesel/hydraulic driven conveyor is that it can be operated in remote locations with only fuel being required. Also, diesel/hydraulic-powered units tend to be simpler to service than their more complex electric-driven counterparts. However, the advantages of electrically powered equipment over diesel models extend well beyond the obvious savings on diesel fuel and maintenance costs. They also provide unbeatable dependability and uptime. EDGE Innovate offer flexibility in terms of power source configuration with hydraulic coupling, diesel/hydraulic, electric/hydraulic, direct electric, diesel genset and dual power all available for their entire material-handling range.
As well as providing a wide choice of power source options, conveyor formats, and conveyor lengths and throughputs, EDGE material-handling equipment can also be customized to meet precise customer specifications and specific throughputs. With more than 1,000 mobile stackers and stockpilers currently working around the world, the company’s products have been tried and tested in the harshest of environments. For more information visit: www.edgeinnovate.com
- Subscribe to Quarry Management, the monthly journal for the mineral products industry, to read articles before they appear on Agg-Net.com