The Competitive Conveyor Belt Market
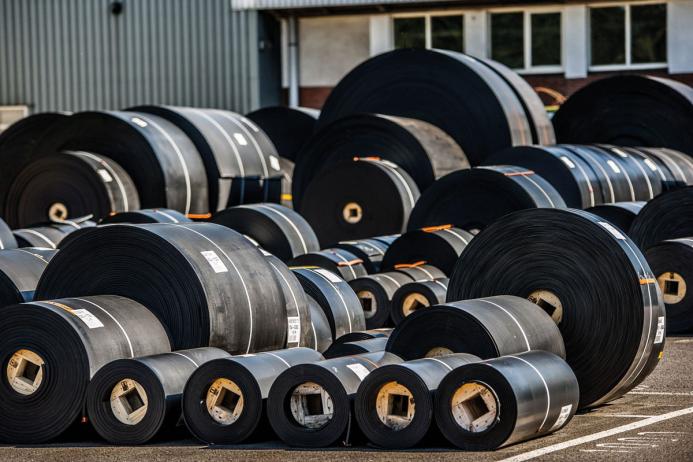
First published in the March 2023 issue of Quarry Management as Why the difference?
Conveyor belt specialist Leslie David explains how the price of an apparently identical specification conveyor belt can be as much as 50% less than one produced by another manufacturer
The industrial conveyor belt market in Europe has always been very competitive. However, as the volume of belting being imported into Europe continues to increase dramatically, the huge variations in the prices being offered by traders and manufacturers are becoming increasingly difficult to understand. It is not uncommon to see differences of 50% or more for belts that are supposedly of exactly the same specification. So, how can such a huge difference be achieved?
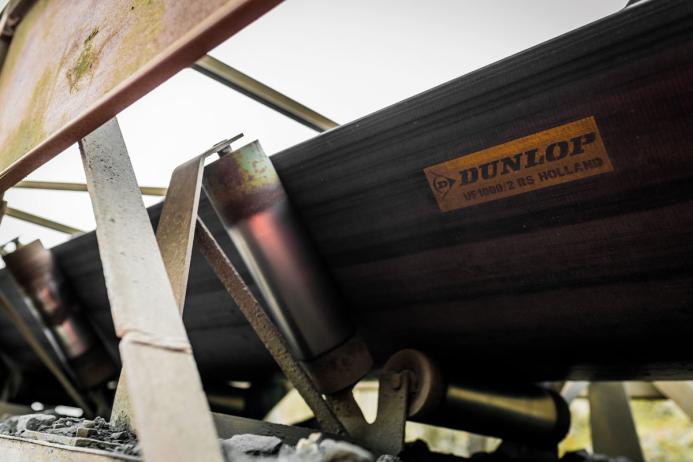
Paying for the name?
A common assumption is that the reason for the higher price is that you are ‘paying for the name’. Another common misconception is that European manufacturers apply much bigger profit margins or that labour costs in Asia are much lower than those in Europe. However, none of these theories are actually correct. The fact is that ‘big brand name’ European manufacturers such as Dunlop Conveyor Belting and Contitech have built their brand images based on producing belts of much higher quality standards compared with those at the bottom end of the market. When you consider the extreme levels of competition, no manufacturer would survive for very long if they applied unrealistic margins. In fact, European manufacturers can only dream of having a margin that even comes close to double figures.
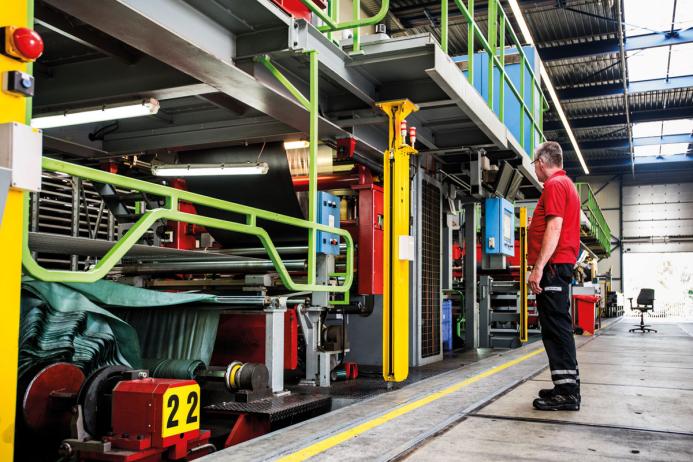
Buying power is not a reason because virtually all of the biggest conveyor belt manufacturers are part of, or at least closely associated with, major tyre manufacturers and all the essential raw materials are available on the global market. The ‘lower labour costs’ argument does not hold water either because the very high level of automation means that the labour cost element of producing a conveyor belt is actually insufficient to make a significant difference to the selling price.
No name, no shame
Strong brand images are built up over many years based on producing belts with much higher quality standards and lowest ‘whole-life cost’ compared with those at the middle and bottom end of the market. That reputation for quality has also had to stand the test of time, 100 years in the case of Dunlop. A big brand name is only as strong as the quality and value for money consistently provided by the products that carry the manufacturer’s name. Indeed, big brand companies should actually be applauded for being prepared to be held accountable for their products. They are brave enough to have their names on them whereas cheap import goods with no name have little or no accountability at all. When unbranded products fail or simply disappoint, there is nowhere to seek recompense. Where there is no name there is no shame.
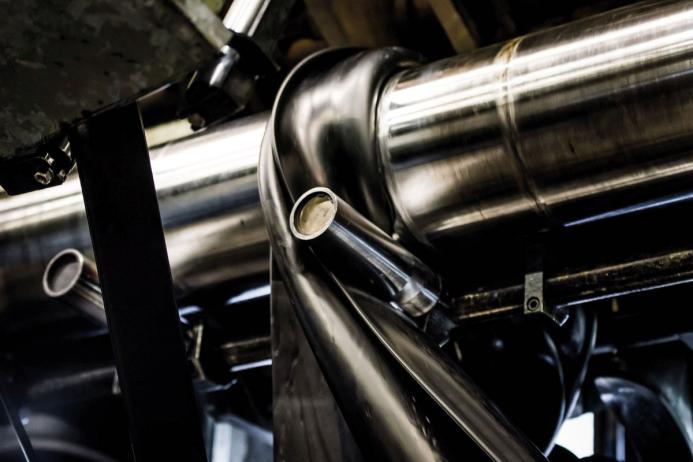
What goes in must come out
The key to the huge differences in price almost entirely lies in the quality of the materials being used. It is an inescapable truth that for products to be comparable in quality they must at least contain raw materials of a comparable quality. Another inescapable truth is that when poor quality ingredients are used the end product cannot be anything other than poor quality. What goes in must come out. Raw materials constitute between 70–75% of the total cost of producing a conveyor belt and are available on the global market, with price ultimately determining the quality. Logically, this means that if there is a big difference in price, there must be a comparable difference in the quality of the materials used.
Ignorance is bliss
Conveyor belts are technically complex components and, over the years, have become even more complicated. Not surprisingly, most of those responsible for buying conveyor belts usually have only a very basic understanding of conveyor belts. The natural consequence is that the alarm bells do not start ringing when there is a big disparity between the prices being offered. Without any other way of judging, the price becomes the primary buying criteria rather than reliability and longevity.
What the eye cannot see
Many traders and manufacturers rely on this lack of knowledge, plus the fact that all conveyor belts look pretty much identical in terms of their outward appearance. Even to the most experienced eye, it is impossible to tell how well the rubber will perform or how long the inner carcass will handle the stresses and strains placed upon it before handling or steering problems start to occur, repairs are necessary, or the belt fails completely. Based on the principle of ‘what the eye cannot see’, there are several methods and tricks that belt manufacturers use in order to undercut their competitors’ prices.
The rubber
Some 85% of industrial conveyor belts used in Europe are rubber ‘multi-ply’ with a polyester/nylon (EP) fabric-reinforced carcass protected by an outer cover of rubber with a thin layer (skim) of rubber between the layers of fabric. It is the quality of the rubber covers, in particular the ability to resist wear and tear, that mostly influences the performance and operational lifetime of a conveyor belt. The rubber used for multi-ply and steelcord conveyor belts usually constitutes at least 70% of the volume mass of a conveyor belt and more than 50% of the cost. Consequently, it is the single biggest opportunity for manufacturers to cut corners in order to minimize costs.
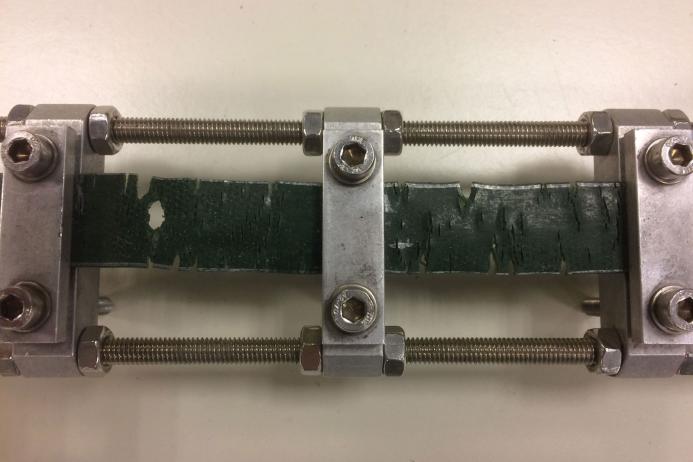
Missing protection
Because of its adaptability, most of the rubber is synthetic. Dozens of different chemical components and substances are used to create the numerous different synthetic rubber compounds needed to cope with a multitude of different demands. These chemical components and additives are very costly so a combination of using low-grade chemicals at the absolute minimum levels all helps to contribute towards the ‘lowest-possible cost’ objective. Perhaps the best example of this concerns the additives needed to combat the considerable damage caused by ground-level ozone and ultraviolet light. Ozone becomes a pollutant at ground level and exposure is unavoidable. It increases the acidity of carbon black surfaces and causes reactions to take place within the molecular structure of the rubber, resulting in surface cracking and a marked decrease in tensile strength.
Rubber degradation is also caused by ultraviolet (UV) light from sunlight and artificial (fluorescent) lighting because it produces photochemical reactions that promote the oxidation of the surface of the rubber resulting in a loss in mechanical strength. In both cases, this kind of degradation causes the covers of the belt to wear out faster than they should. Protecting the rubber against ozone and UV is easily achieved simply by adding special antioxidant additives during the mixing process of the rubber compound. These additives are, therefore, an essential ingredient in any belt of reasonable quality. However, despite their critical importance, anti-ozonants are not used in the vast majority of conveyor belts purely because they are an avoidable cost.
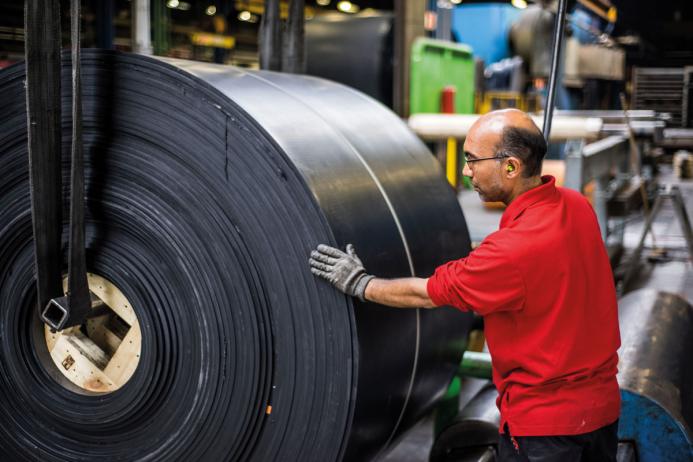
Safe to handle?
To make some rubber compounds it is unavoidable that chemicals that may be extremely dangerous in their own right have to be used. Fortunately, there are very strong regulations in place to protect humans and the environment in the form of REACH (Registration, Evaluation and Authorisation of Chemical substances) regulations EC 1907/2006.
REACH regulations stipulate that all European manufacturers are legally obliged to comply with the regulations relating to chemicals, preparations and substances used to create finished products. Although not commonly known by consumers, the use of any ‘substance of very high concern’ (SVHC) listed within the regulations must be registered with ECHA (European Chemical Agency) headquarters in Helsinki. For example, if a product contains a SVHC that is more than 0.1% of the total weight of the finished product, the manufacturer is compelled to both register its use with the ECHA and provide their customer with a safety datasheet.
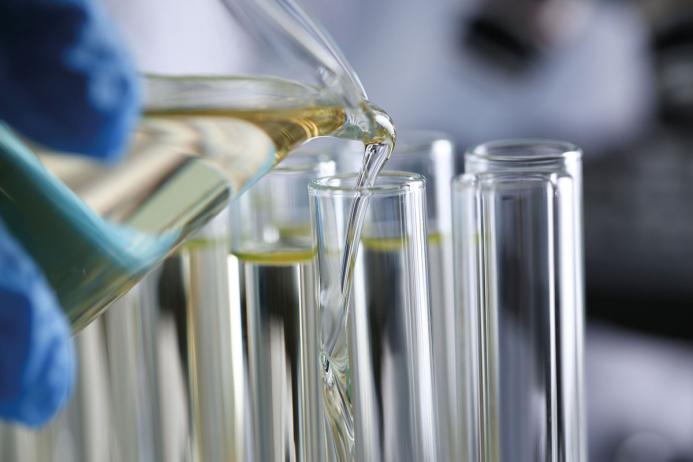
One of the biggest concerns involves short-chain chlorinated paraffins (SCCPs). These are commonly used, especially in Asia, to artificially speed up the vulcanizing process. REACH regulations clearly stipulate that SCCPs should either not be used at all or only used on a very restricted basis because they are persistent organic pollutants. They are bioaccumulative* in human and wildlife and toxic to aquatic organisms at low concentration. These chemicals pose hazards to human health and the environment because they have category 2 carcinogenic classifications and are what is scientifically termed as ‘persistent’. The clue to their presence is a strong, pungent aroma, whereas good-quality rubber usually has very little smell at all. (*Author’s note: Bioaccumulation occurs when an organism absorbs a substance at a rate faster than that at which the substance is lost or eliminated).
The formation of nitrosamine gasses is another concern and known to occur when certain types of vulcanization accelerators are used. Nitrosamine gasses gradually release themselves from rubber belts, which could be a problem when the belts are stored indoors. Nitrosamines are chemical compounds classified as probable human carcinogens, based on animal studies. Investigative research is still ongoing but publicly available information from the rubber industry (primarily from within Germany and The Netherlands) indicates that nitrosamine formation can be avoided if the accelerators are replaced by others that do not contain nitrosatable substances.
Sadly, most European manufacturers have chosen to ignore these legal requirements, either completely or at least partially because of the impact on production costs. Of even more concern is that those manufacturers located outside EU member states and the UK are not subject to EU regulation concerning the use of hazardous chemicals or the use of Persistent Organic Pollutants (POPs). This provides them with an open door because they are free to use unregulated raw materials that cost much less on the global market compared with their regulated counterparts, even though those same materials may be entirely prohibited or at least have strict usage limitations within the European community.
Other methods used to minimize rubber costs include the use of recycled rubber of highly questionable origin, the use of reject rubber compounds and cheap ‘bulking’ fillers such as chalk to replace part of the otherwise more expensive rubber polymers. An even more alarming cost-cutting practice involves a key component contained in every black rubber conveyor belt – carbon black.
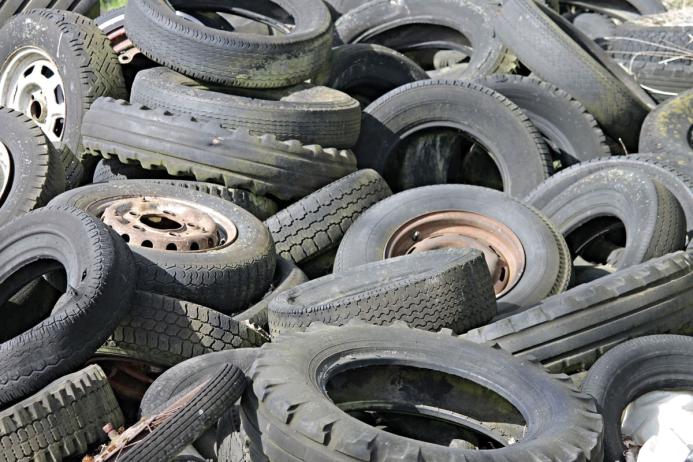
Up in smoke
Carbon black is one of the most important ingredients of synthetic rubber. It represents some 20% of a rubber compound and is used not only as a pigment but, much more importantly, as a reinforcing compound. Carbon black is produced by the reaction of a hydrocarbon fuel, such as oil or gas, with a limited supply of combustion air at temperatures of 1,320–1,540°C. The unburned carbon is collected as an extremely fine black fluffy particle.
Good-quality carbon black is costly to produce. However, the important role it plays should not be underestimated. For example, it prolongs belt life by helping to conduct heat away from the surface area of the belt, thereby reducing thermal damage, and it also absorbs ultraviolet radiation. Belts offered with much lower prices are almost certain to contain carbon black that is of a much lower quality and which has been produced much more cheaply by burning scrap car tyres. It is also much more damaging to the environment.
Out of control
Only a limited number of genuine conveyor belt companies who actually manufacture belts themselves still exist in Europe. Apart from one notable exception, virtually all European manufacturers import belting from outside Europe to some degree in order to supplement their own production. Many manufacturers outsource the manufacturing of their rubber to large-scale rubber compound manufacturers (again, mostly outside Europe) rather than produce it in house. Although it is cheaper, the downside is that it is virtually impossible to ensure the consistency of the rubber’s physical properties and equally impossible to ensure compliance with REACH regulations or those concerning Persistent Organic Pollutants.
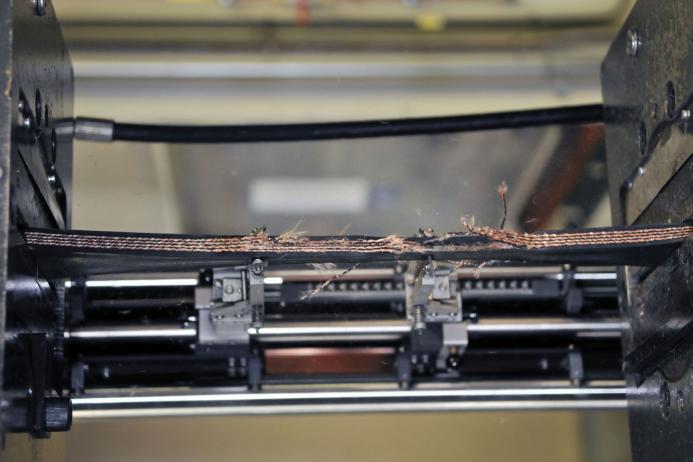
The carcass
The carcass provides the innate strength of any conveyor belt. Very significantly, the strength under load needs to be consistent throughout the belt both longitudinally and transversely in order for the belt to steer and handle correctly. This is pointed out for a very good reason. Although they may be the same basic specification, there are often huge differences in the quality of the fabric plies between one belt and another.
In cheaper, lower-quality fabrics, although the amount of material used in the longitudinal (polyester) strands of the fabric may be adequate, the amount of transversal weft material (nylon) is kept to an absolute minimum in order to reduce cost. Although the required tensile strength is achieved, rip and tear resistance are reduced and elongation (stretch) is unacceptably low. Elongation that is too low can cause problems with transition distances and a general inability to accommodate the contours of the conveyor and its drums and pulleys, and ultimately leads to the premature failure of the belt.
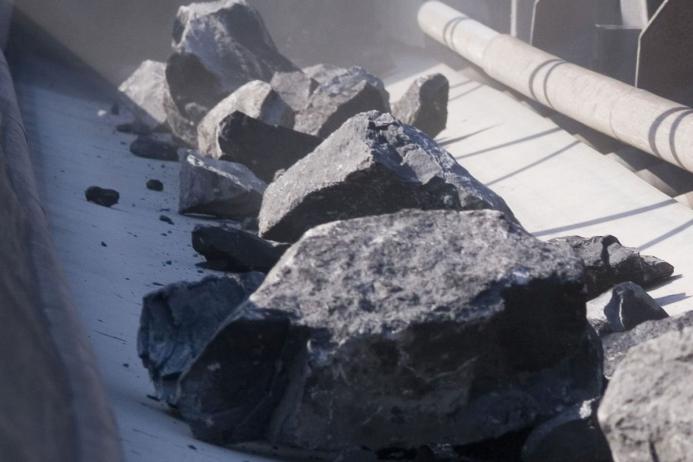
EP or not EP? That is the question
Another deception that is now increasingly common involves the use of totally polyester (EE) fabric plies in a carcass that has been sold as being an EP carcass (polyester/nylon mix) construction. Until fairly recently, this dishonest practice was most frequently found in belting that had been imported from Asia, but it is now being used by a growing number of European-based manufacturers. The whole basis of using a mix of polyester and nylon fabric (EP) is that it has the best balance of mechanical properties, including allowing a conveyor belt to run straight and true, to trough, to flex round pulleys and drums, stretch, provide sufficient transversal rigidity, longitudinal strength, and much more besides.
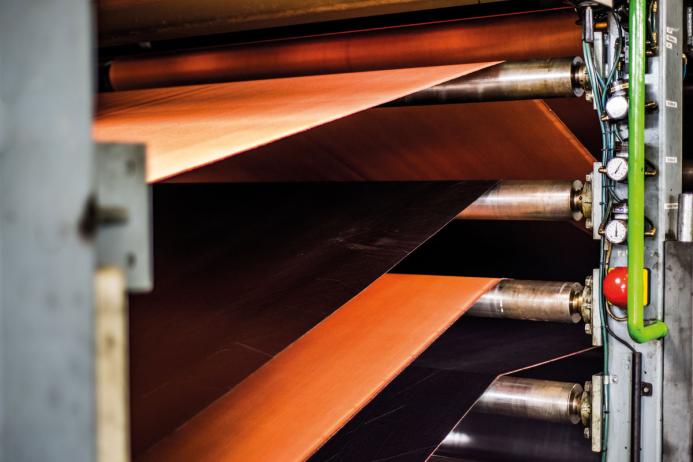
The use of totally polyester (EE) fabric compromises a whole range of essential mechanical properties*. The biggest danger is that a polyester weft can cause low transverse elasticity, which reduces both the troughability and impact resistance of the belt as well as causing tracking issues. In addition, less weft in the belt can also reduce rip resistance, fastener strength and the ability to handle smaller pulley sizes. The seriousness of the detrimental physical effects should never be underestimated. (*Author’s note: The use of fabrics made entirely of polyester (EE) has its place in certain belt types and constructions. However, in those cases the declared specification of the belt should clearly be EE and not EP).
As touched on earlier, the simple reason for this dishonest practice is to keep the selling price down because totally polyester (EE) fabric costs some 30% less than EP fabric. In itself, this may not seem like a great deal, but the fabric plies are a major cost component in any multiple ply conveyor belt, so using cheaper polyester fabric is a big help when trying to achieve the perception of a lower ‘like-for-like’ price. As far as the manufacturer using these underhand tactics is concerned, they know that it is highly unlikely that the end-user will have tests carried out that would reveal their trickery and dishonesty.
The inescapable truth
As mentioned at the beginning, the inescapable truth is that for products to be comparable in quality, they must at least contain raw materials of a comparable quality. Raw materials constitute some 75% of the cost of producing a conveyor belt, so if there is a significant difference in price then the obvious conclusion is that the quality of performance and the longevity of the product will be significantly less. As the old saying goes, ‘Price is what you pay but the cost is what you spend’.
About the author
After spending 23 years in logistics management, Leslie David has specialized in conveyor belting for more than 16 years. During that time, he has become one of the most published authors on conveyor belt technology in the world.
- Subscribe to Quarry Management, the monthly journal for the mineral products industry, to read articles before they appear on Agg-Net.com