Moving on up
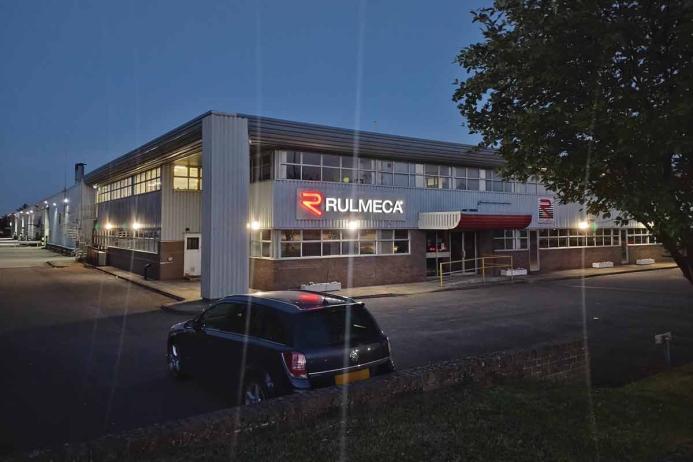
First published in the March 2024 issue of Quarry Management
QM meets up with Roy Ball, managing director of Rulmeca
QM headed to Corby to meet Roy Ball, managing director of Rulmeca, global specialists in bulk handling and unit handling. The whole thrust of the business is conveyor components – motorized pulleys, drums, idlers and other conveyor accessories that help materials handling businesses across all sectors run operations more smoothly and more efficiently. Rulmeca offer their own ranges of products, and anything they sell is generally manufactured by the company at one of its nine manufacturing sites across the world – plus it has a further eight sales companies. And if there is a large demand for products in a particular market, the company will put a plant in that market.
The business across the world is roughly split with about 32% focusing on unit handling and 68% on bulk handling, and deals with end-users on a technical basis, as well as large and small OEM’s and distributor companies.
During the pandemic when factory doors were shut and parts were tricky to source, the team at Rulmeca were working around the clock with three shift patterns to manufacture parts for businesses who were depending on the company to keep operations on track.
‘We were extremely careful during the pandemic. But we carried on manufacturing six to seven days a week and we didn’t close or take the Queen’s shilling,’ said Mr Ball. ‘Many other suppliers took furlough and closed down for a long period of time. Many clients came to us as an alternative. During the lockdown period we had many working from home and it worked out nicely. And then at the end of the pandemic, everybody wanted to get back to the office as quick as possible.’
The implications of Brexit and the following Covid-19 outbreak have been tough on business but these have also been record years for Rulmeca – not only in the UK, but also group-wise. Only last year, Rulmeca Holding Spa purchased US-based Douglas Manufacturing Ltd – manufacturers and distributors of components and engineered conveying solutions for bulk materials handling applications – to further expand their reach into the US.
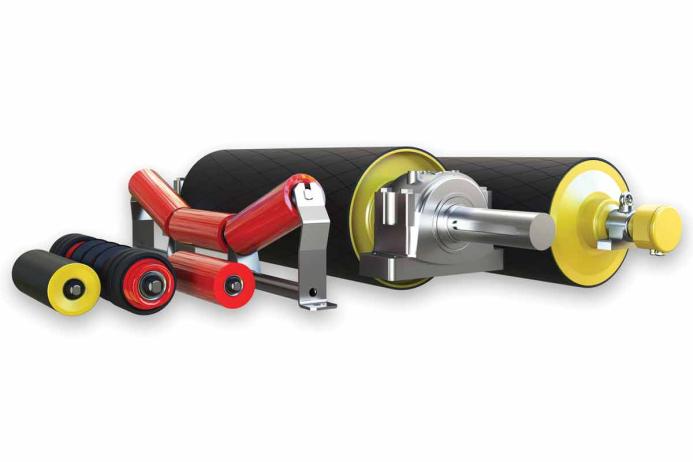
Back on British soil, the Corby premises is the UK base for the brand that was founded in Italy in 1962. Today it is still a family company run by brothers Fabio and Marco Ghisalberti (whose father founded the company), who regularly travel to their other facilities across the globe – Australia, South Africa, Indonesia, Thailand and many more, and are personally heavily involved in the day-to-day running of the business.
‘The holding company was established a few years ago and makes for more collaborative working looking after all the different areas, and everyone is extremely supportive, backing you up on investments and assisting with relationship building. If there are parts within the company and someone else needs them, we can swap and change between us. We hold a lot of stock items here in Corby that comply with different local standards, for example, America, Europe and the Far East.’
Mr Ball added: ‘These last few years have been absolutely crazy from a UK perspective. Ever since Brexit came along, we’ve just gone on a massive upward spiral.’
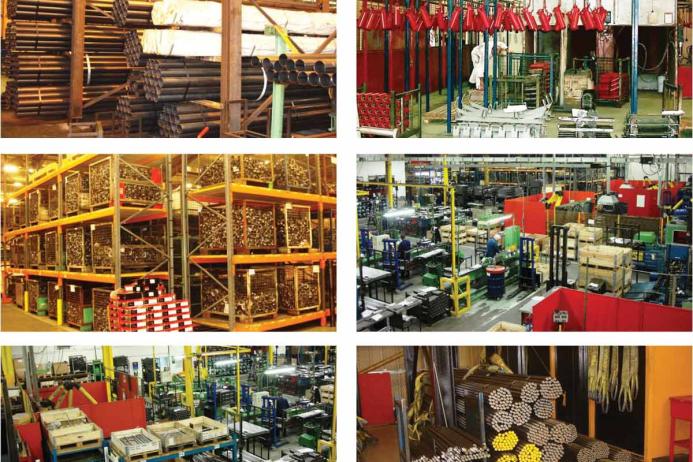
Despite this growth, Rulmeca are still headquartered in Italy and their diverse geographical spread ensures they can serve more than 85 countries.
And while this is very much a global brand, Mr Ball works with his team as if it was an extended family and is keen to attract and retain a diverse team who can progress through the company. When we meet, he tells QM about a couple of his employees who have shown particular interest in the workings of the business and have been promoted from production to work within sales: ‘After all, he knows the product inside out and is in the best position to answer customers’ queries and provide the best service,’ said Mr Ball, ‘You need to physically feel the product, you need to cut the steel to weld it, assemble it and understand how it works.
‘We have a comprehensive ESG policy with regular sessions in the UK and in Italy, and we talk about how we want other people to see us; we believe in each other and work interdepartmentally learning from each other.’
In the 37 years that Roy Ball has been with the company, he’s seen a great many changes. Corby manufactures roughly 10,000 rollers a week, and globally the company is producing around 6 million rollers a year, and that is increasing year on year. ‘The ability to do that is not only manpower, but also machinery development and efficiencies, and the technological improvements we’ve made – most of our machines are purpose built for us,’ explained Mr Ball.
‘I’ve got confidence in our production, volume and capability. But even more, I’ve got confidence in our people, too.’
Find at more at rulmeca.com
Subscribe to Quarry Management, the monthly journal for the mineral products industry, to read articles before they appear on Agg-Net.com