Case Study: Dunlop Superfort at Whatley Quarry
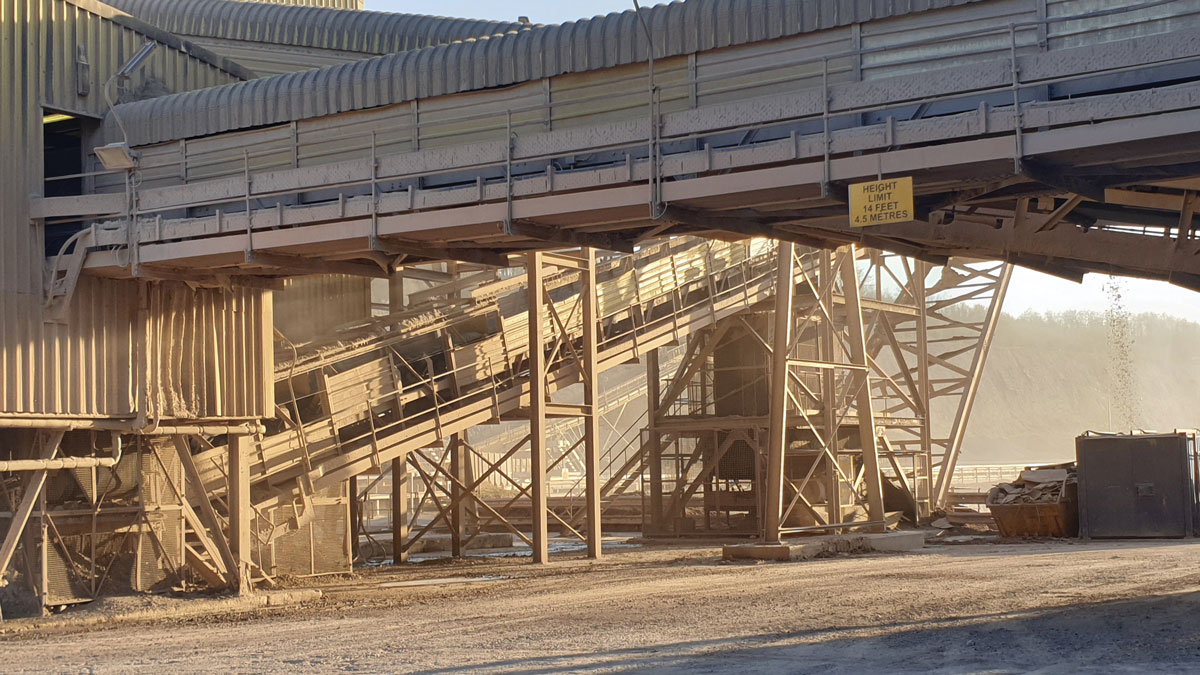
First published in the April 2021 issue of Quarry Management
Vulcanising South West Ltd supply and install new conveyor belt at Hanson’s flagship site
Whatley has been operating since the 1960s and is the largest of Hanson UK’s quarries. Situated between the villages of Mells and Chantry in the Mendip Hills, around four miles west of Frome, it employs more than 60 people directly, along with a wide range of support staff and contractors. Operating 24h a day, five days a week, and producing 4–5 million tonnes a year, the quarry supplies crushed limestone aggregate to local markets by road, and to depots in London and the South East via a dedicated rail link, whilst further on-site plants produce asphalt and ready-mixed concrete.
On 15 May 2019, Whatley Quarry approached Vulcanising South West Ltd (VSW) with a view to carrying out a belt calculation on the site’s C7 conveyor – a horizontal belt that carries 63–150mm crushed limestone aggregate and plays a key role in ensuring uninterrupted primary and secondary crushing operations at the site. The maximum expected life of the 1000/4 6+2 belt (of unspecified origin) was, on average, 6–12 months, with a number of repairs being required during this period, especially at the splice, each carrying extra cost and downtime. VSW’s calculations concluded that a type 1000/4 6+2 belt was excessive in this application, especially for the drum diameters on the C7 system. The snub roller diameters, in particular, were too small for the belt, putting unnecessary strain on the belt splice (see table 1).
Under normal running conditions, the C7 belt carries between 500 and 1,400 tonnes of material per hour, depending on the number of crushers in operation. Average tonnage in normal operation is 1,200 tonnes/h, and the average tonnage carried by C7 over a 24h period is 18,000 tonnes. With a maximum material size of 150mm flowing on to the belt from a 600mm height, VSW determined that a Dunlop 630/4 6+2 RA Superfort or Ultra X3 belt would be more than capable of dealing with the demands of this application (see Dunlop Conveyor Belting article).
However, in light of the historical data, VSW decided to increase the specification to an 800/4 6+2, knowing that this would maximize the expected life of the belt whilst still falling within the range of Dunlop’s ‘safety factor’. Both VSW and Dunlop were certain that with its abrasion-resistant ‘RA’ covers coupled with the correct tensile strength selection, Superfort would offer a significant increase in lifespan as well as a reduction in downtime and operating costs, compared with the belts used previously on the C7 conveyor.
After discussing their analysis and findings with Whatley Quarry, VSW submitted a technical data sheet (see fig. 1) and quote for the supply and installation of a Dunlop Superfort 800/4 6+2 RA DIN Y belt with moulded edges. The contract was duly awarded to VSW and the new belt was fitted in June 2019.
Prior to the VSW team’s arrival on site in June, a safe system of work (SSoW) was completed by VSW’s health and safety manager, Craig Jones, and the safe installation of the new belt was planned in conjunction with Hanson’s on-site staff. In co-ordination with the team at Hanson, all lifting and handling equipment was also arranged prior to VSW’s arrival. Once on site, the VSW team carried out job-specific risk assessments and method statements prior to conducting any installation work, such as splicing the belt, which was hot vulcanized on site using the company’s Almex press.
After installation, the new belt remained fully operational for 12 months before unexpectedly having to be changed again, following the mechanical failure of a liner plate which cut the belt along its full length 8in from its edge. Despite this unfortunate setback, Hanson said that during its time in operation, routine inspection activities had continued as normal with a significant reduction in repair and belt maintenance costs. They added that the Dunlop Superfort belt had outperformed the one used previously and, as a result, saved on both downtime and maintenance costs during its life. According to Hanson, total belt life is currently estimated at 18 months, which, they say, represents a 75–100% increase in life against tonnage and an annual cost saving of 45%.
For further information visit: www.vulcanisingsw.com
- Subscribe to Quarry Management, the monthly journal for the mineral products industry, to read articles before they appear on Agg-Net.com