Wash Plant Maintenance
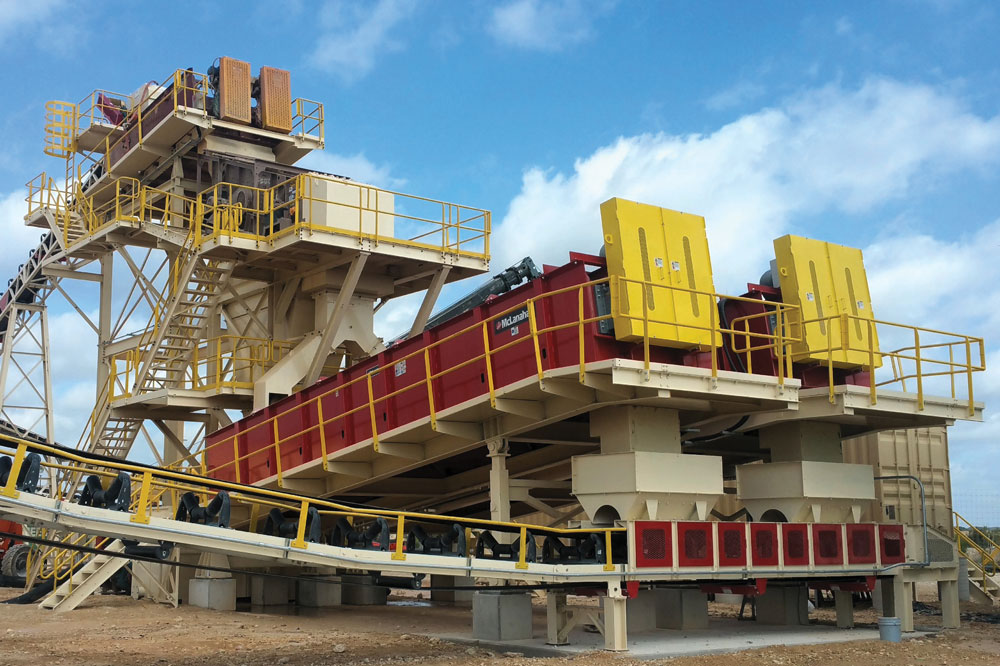
First published in the April 2018 issue of Quarry Management
McLanahan outline the benefits of an effective preventative maintenance plan in ensuring wash plants remain safe, efficient and productive.
The efficiency and availability of any wash plant will be affected by poor or non-existent maintenance practices. Maintenance programmes should be in place to cover safety, lubrication and wear parts. Different types of maintenance include preventative, reactionary and time based, although preventative maintenance is almost always the preferred method. The first, most basic part of any maintenance plan should be a thorough understanding of the equipment manuals; these are designed to ensure equipment longevity and efficiency. However, the number-one priority in any maintenance task is safety. Operators should review the conditions surrounding the maintenance task: What tools are required to complete the task? Which employees and how many are needed? Are they properly trained in the procedures? What communication is needed with other operators? Conditions such as time of day, weather, and the area around the piece of equipment can all affect a maintenance task and the safety of everyone involved.
Keeping equipment and operators safe
As part of routine wash plant maintenance, all safety guards and warning decals should be checked. Guarding is sometimes seen as ‘inconvenient’ and removed from a machine to allow easier access to certain components. These guards may not be put back in place because operators lose the bolts and do not bother to replace them. Guards are intended to keep operators safe and, if they do need to be removed for maintenance, should always be put back before start-up. Warning decals are also there to help keep operators safe and should always be clean and intact. Should an equipment warning decal become damaged, the manufacturer should be contacted immediately for a replacement.
Operators should always check the integrity of all safety items before use, and must not turn a blind eye to a hazard or a hazardous situation. Do not say: ‘it’s not my job’, or ‘I’m not the one who left it there’, or ‘someone else will fix it’. When conducting inspection and/or maintenance, every worker involved should lock out and a lock should never be removed until positive identification verifies that all personnel are out of the area. Every incident or accident should be investigated. Through such investigations, recommendations can be made to improve safety and prevent the event from occurring again. It is vital that these recommendations are implemented otherwise sites are destined to repeat past mistakes.
General maintenance requirements
Some equipment, especially vibratory equipment, requires regular re-torqueing of bolts. A review of the manufacturer’s manual for the relevant data is recommended. If ignored this can cause damage to equipment and possible loss of warranty. A torque-multiplier may be needed if torque specs are higher than available tooling. Prior to such a procedure check if lubricated or dry threads are used.
While lubrication schedules vary, check the quantity and type of grease/oil that is required. Also, be aware of the recommend frequency for lubrication. Is replacement of lubricant needed a fixed amount of time after start-up? Is that time frame based on environmental conditions? Keep all grease fittings clean. This step should be obvious but is not always followed. Grease fittings should be cleaned before engaging the gun to lubricate the equipment. Remove dirt and other foreign material from around oil filling points, and be sure to inspect old lubricants for contamination. In some cases lubrication analysis should be carried out to trace contaminants associated with certain types of failure that can lead to potentially unsafe washing equipment.
Some equipment specifics
Scrubbers/trommels – In addition to proper lubrication, mounting alignment is very important to prevent permanent damage to tyres and drives. Routine screen media condition checks for wear are also important. The task of inspecting internal lifters and advancing or retarding paddles is equally important for optimum production. If their height is below a certain critical point material will not rotate and interact effectively. Allowing these paddles to wear away and not replacing them may save a few pounds in the short term, but will prove costly with regard to loss of production over the longer term.
Log-washers, blade-mills, aggregate conditioners, coarse-material washers and fine-material washers – New equipment should always be ordered with the optional guards to prevent accidents; and guards should be retrofitted to older equipment if there are dangerous access points. All screw/log shaft types of equipment have a common weakness – the lower bearing. Most manufacturers have different designs. Some are complex and feature a ‘submerged’ bearing and some have a simple outboard pillow block with a rubber boot seal assembly. Each claim to offer different advantages, but they all require lubrication. Paddles and flights also need periodic inspection for wear and possible replacement. With metallic paddles or shoes, operators should be aware that worn ends can become razor sharp and cause serious injury if not handled properly. It is important to check wear on these items and also the fasteners that secure these wear parts to the shaft. Occasionally, the operator should check the shaft for run-out, as a bent shaft can cause premature failure of support bearings and even the shaft itself. Shaft straightening should only be carried out after consulting the manufacturer’s manual. To ensure proper lubrication of the bearings, many manufacturers offer optional automatic lubrication systems that deliver regular periodic lubrication and minimize site personnel exposure to the operating environment.
Pumps – These are the heart of any wet process, but serious injury can result from a poor installation whereby solids settle out and an explosion can occur – always consult the manufacturer when reinstalling or modifying a pump installation. The correct selection of the material of construction is critical to long-term, cost-effective service life and safe operation. There are three key areas in any pump: wet end, gland and bearings. It is important, particularly with open vane style impellers, to check the clearance between the impeller and the suction side liner. Too wide a gap will lead to bypass inefficiency and, in slurry pumps, accelerated wear. A reduction in performance will most likely be due to impeller wear, which should be monitored regularly. Heat should not be applied to any area of the pump’s impeller when trying to loosen it during maintenance, as this can result in serious injury or even death.
Hydrocyclones – While these have no moving parts, there are two failure modes – delamination and wear – that impact on performance and could also affect the safety of the machine. Liners that come loose due to wear or adhesion failure can cause disruption of flow inside the unit. Ultimately, this causes poor performance with misplaced particles. Checking the internal lining of a cyclone should be done at least seasonally; this is particularly important when dealing with siphon (vacuum) assisted cyclones/Separators. The apex (spigot) is the component that wears out most quickly. These are sized based on mass flow, so that as they wear the underflow becomes more dilute and more fines will bypass into that stream. So, if a product is getting dirtier, check the apex. Worn vortex finders can allow coarse fractions to short-circuit into the overflow and fill the ponds or contaminate the next stage of production. In extreme cases, wear can cause the pipe to detach from the plate, causing significant damage to the equipment and possibly injuring the operator.
Dewatering screens – Safer working conditions result from the use of dewatering screens, with less carry-back and spillage to clean up around conveyors. While these devices typically have a very long service life, there are still some things to monitor to keep the machine running safely and effectively. If a crack appears in the side plate, trace it back to its end with dye penetrant and drill a 1/8in to 3/16in hole. This will generally resolve the problem and the side plate will last the life of the screen. Cracks in cross members should be referred to the manufacturer immediately, as should any bolt breakage. The problem of cracking in dewatering screens is often caused by the support structure rather than machine integrity. Lubrication is a general maintenance activity, but extra care should be taken as some vibrator motor manufacturers use special grease that, if not used, may void the warranty. Often, motor wiring gets draped across a vibrating motor to the side of the screen and vibrates against adjacent surfaces – this is a very dangerous condition. Look out for this and replace the wiring as necessary. Always check the direction of motor rotation on restarting after electrical work to keep the equipment running properly.
For more information visit: www.mclanahan.com
- Subscribe to Quarry Management, the monthly journal for the mineral products industry, to read articles before they appear on Agg-Net.com