Scheduling Downtime for Maintenance Activities
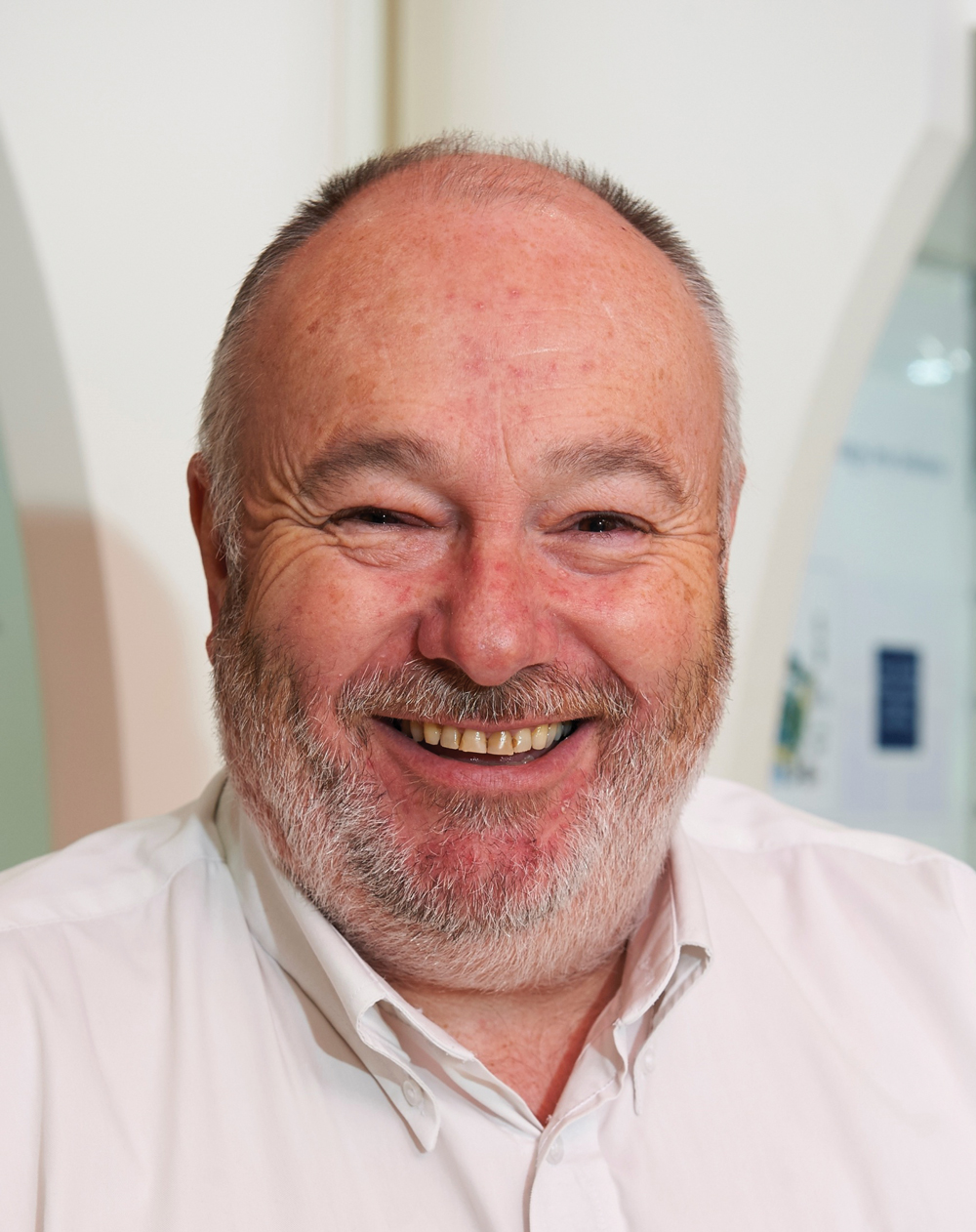
First published in the August 2016 issue of Quarry Management as Scheduling Downtime
How ‘planned’ is your planned maintenance? Terry Davis, national technical manager with Brammer, looks at how to prepare for scheduled downtime and ensure maintenance activities are fully resourced, carefully planned and efficiently executed
Due to a combination of increased production demands, changing lifestyles and more advanced predictive-maintenance technology, the traditional annual two-week summer shutdown is, in most factories, a thing of the past. Today’s manufacturers have to fit maintenance around production demands, which means shorter windows, longer intervals, and often less notice.
While some industries, such as quarrying, still operate a shutdown – typically during spells of anticipated bad weather – most periods of downtime occur at fairly short notice when a particular production line is taken out of operation for a defined period of time. Maintenance teams must be ready to move in and act quickly, ensuring the equipment goes back online at the required time. But how can they prepare and make the most of this planned downtime?
As one of the most resource-intensive activities a manufacturing/processing facility can undertake, all aspects of a shutdown or planned maintenance must be justified. In putting together a work plan, certain activities such as oil changes may be scheduled simply because it is always done during planned downtime, rather than because of a specific need. It is important that old practices are challenged to uncover true best practice. For example, many facilities prescribe a hydraulic oil change every six months, whereas the oil may actually last a year or more. Frequent condition monitoring and oil sampling will reveal the correct interval for changes, which in many cases means the oil is left in situ for longer, reducing the cost of disposal and new fluid.
Many activities scheduled for planned downtime will be uncovered as a result of such condition monitoring, analysis of mean time to failure, and known equipment life cycles. However, the role of the equipment operator should not be overlooked. Coming to know their machinery as well as they know their own car, they can flag changes of pitch, deviations from normal operation, increased heat and other factors which may be symptomatic of damage and would not be noticed by maintenance engineers who spend less time with that equipment. Operators should always be engaged when planning for downtime, and plants that encourage everyone to take responsibility for maintenance will be well ahead in this respect.
After using condition monitoring, visual inspection and root-cause analysis to develop an outline plan, maintenance teams next need to ensure they have all the tools to complete each activity by referring to the spares list provided by the original equipment manufacturer (OEM), as well as considering any ancillary activity. For example, some equipment, such as filter-regulator-lubricators (FRLs), may be installed at height or behind other machinery. Scaffolding may be required to assist with access and its installation needs to be factored in to the overall timetable, while if a machine needs to be stripped down in order to reach and replace a component, it is good practice to include extra time to attend to any other issues which may be identified during the strip down. Working at height or in restricted spaces may require additional personal protective equipment (PPE) over and above what is usually held in stock, and this too must be planned and sourced.
The aim of planned downtime is to return the equipment to the same or better state as it was beforehand. Therefore, even if equipment has been inspected prior to downtime and all condition-monitoring data has been analysed, time must still be allocated to manual inspection as damage and other issues will no doubt be identified and added to the schedule – areas of concern cannot be overlooked if they did not appear on the original plan. For example:
If replacing a belt, also inspect the pulleys. Look for correct alignment and tension throughout – over-tensioned belts can affect the motor bearing on the drive end by reducing the clearances from where the belt is being pulled. Consider the use of roller bearings at the drive end as this will give longer life when dealing with heavy overhung loads.
If replacing a chain, check for sprocket wear – tooth wear on one side only points to misalignment at installation which must be remedied. Chains jumping sprockets may be due to sprocket misalignment or material build-up on the sprocket. Corrosion could point to a lack of lubrication, so the autolube device or re-lubrication pattern should be checked.
The art of engineering comes in to play when determining the best course of action when a damaged component is discovered. For example, in a set of three bearings, if one bearing is found to have failed while the others are operating satisfactorily, the engineer must decide whether to replace one, which is, at face value, the cheaper option, or to replace all three. When total cost of ownership is considered, however, replacing all three bearings may well prove to be cheaper in the long run. One consideration is that the asset has already been shut down. Should another of the bearings fail, the equipment must be taken out of operation for another day leading to unnecessary production delays.
As well as giving the opportunity to inspect related components in more detail, planned downtime also allows time for testing and monitoring devices to be fitted to improve predictive maintenance in the future. For example, real-time lubrication particle detectors can provide crucial data on the health of hydraulic oil, which can both prevent unnecessary oil changes as well as flagging any deviation to assist in early diagnosis of contamination. Other manufacturers may use the occasion to fit flow meters to compressed-air lines to monitor pressure and identify opportunities for point-of-use pressure and flow reductions, thus saving money.
The most important aspects of a successful planned maintenance programme are:
- Identifying what to do and why – including what not to do
- Ensuring the availability of spares, tools and other equipment, such as scaffolding
- Continuing to inspect machinery during repairs and replacement, to uncover other areas which need attention.
Before planned downtime, engineers should assemble a kit of all the possible components that might be required, and specialist maintenance, repair and overhaul (MRO) distributors building these kits should allow manufacturers to return unused items afterwards, only paying for what has been used. When selecting an MRO partner, this flexibility must also be matched by their agility in meeting demanding schedules – planned shutdowns do not always take place between 9am and 5pm, and therefore distributors and technical support teams must be able to work around this. When on site, MRO specialists, such as Brammer, can assist in all stages of shutdown, from inspecting FRLs in restricted areas to tagging hydraulic hoses for repair and suggesting appropriate remediation techniques for frequently occurring damage.
- Subscribe to Quarry Management, the monthly journal for the mineral products industry, to read articles before they appear on Agg-Net.com