Plant Parts look to the Future
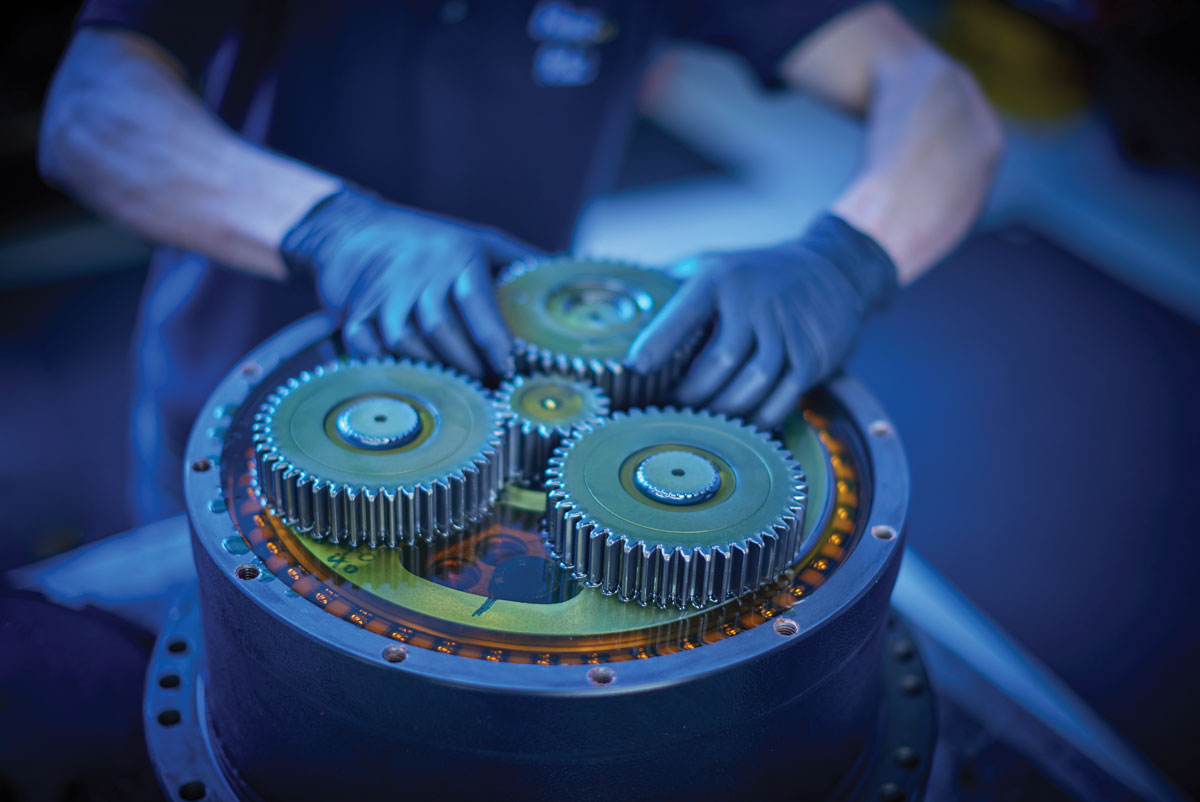
First published in the September 2021 issue of Quarry Management
Company invests in major refit and upgrade of workshop facilities
Suffolk-based Plant Parts Ltd, who have been supplying spare parts and repairing hydrostatic gearboxes for the construction, quarrying, waste recycling and related industries for many years, are currently undergoing a major refit and upgrade of their ISO-approved workshops that will allow the company to accommodate bigger and heavier gearboxes as well as larger-capacity hydraulic motor repairs than is currently possible.
Trading since 1991, Plant Parts have a 30-year history of supplying machinery parts to every segment of the construction and mining industry. From the beginning, their business ethos has been to supply first-quality parts and offer great customer service, and they still follow that same simple model today. In 1995 the company perceived a need for a specialist repair service for rotating case hydrostatic gearboxes, as used on most modern track-laying equipment. At the time the business did not have the facility to undertake repairs, so contracted the labour to a local agricultural repair shop while keeping control of the parts supply chain. In 2003 the business moved into new purpose-built premises and moved the repair and re-conditioning service in house. Today, still family run, Plant Parts undertake repairs and reconditioning of hydrostatic motors and gearbox assemblies for all types of plant and equipment.
Workshop upgrade
Commenting on the workshop upgrade, workshop manager David Finch said: ‘The changes being invoked now represent a substantial investment for Plant Parts and will have a positive effect on both our efficiency and our ability to refurbish the larger and more complex hydraulic motors which are used in the field today. Part of the £500,000 upgrade will see a new ergonomic work layout, new design of gearbox teardown bench and fresh cleaning plant. The new setup will ensure there will be no need to manually handle any heavy components in the workshop. Safety is at the forefront of the design.’
The jewel in the crown, however, will be the fully automated test facility, still under construction at the time of writing, which will be the most advanced hydraulic motor test rig in the sector. Mr Finch said: ‘Our new rig spent many months in the design stage and will have a number of unique attributes. Once the test piece is bolted to the rig, the operator will be able to enter a ‘motor type’ code into the HMI (Human Machine Interface) and the rig will run a pre-programmed series of tests. It will continuously monitor pressure, flow, and oil temperature at multiple points as well as output torque and shaft speed to calculate efficiency, which will be compared to the manufacturer’s standards. It will even measure maximum rated torque at zero rev/min shaft speed to simulate real-world starting conditions. All test results are captured by the software and retained for future reference.’
Running hydraulic components under full load is inherently dangerous, as hot oil at high pressure can kill, and any unprotected rotating components would not meet the company’s strict safety protocols. The new rig is of a torque tube design and all moving parts are completely enclosed inside a steel casing. This arrangement also allows for a pressure cut-out switch to be employed, preventing the large forced-air cooled 132kW dynamometer from being activated while the input shaft is exposed.
Quality is another issue that requires constant attention. Plant Parts gained ISO 9001 accreditation for workshop practices in 2014 and work hard to maintain the high standards set by the procedures. The rewards are tangible, as Plant Parts Ltd have the only workshop outside of Italy to have been granted approval from Bonfiglioli Spa, arguably the world’s leading manufacturer of gearboxes for mobile equipment in this industry.
‘Our greatest challenge is finding and training good staff,’ said Mr Finch. ‘It seems that very few youngsters want to get their hands dirty nowadays, but we are lucky as we have a great team of enthusiastic staff in the workshop and in all areas of the business.’
Plant Parts’ core business has always been the supply of spare parts for plant and machinery and the business is strong in five key components: final drives for track-laying equipment, excavator swing drives, excavator hydraulic pumps, slew rings, and track recoil spring assemblies.
‘We stock a vast range of these key components,’ said sales manager Duncan Vowles. ‘In fact, we believe we hold more stock of these items in the UK than anyone else. In keeping with the company’s ethos of quality, our customers expect the very best from us and we stock OEM components from the likes of Trasmital Bonfiglioli, Rexroth, Kayaba and Nabtesco. These are premium products and while not the cheapest, we believe they offer better value than the cheap and often inferior parts sometimes offered by others.’
The company also stocks internal parts for every hydrostatic drive it sells and can support these components for the full service life of the equipment to which they are fitted. ‘This is another significant advantage of choosing to purchase a high-quality component from us,’ said Mr Vowles.
From their early days, Plant Parts have also stocked and supplied spare parts for Komatsu dozers, wheel loaders and excavators. ‘We keep an excellent range of pins and bushes, seals, engine parts, hydraulic gear pumps transmission parts and more, a mix of genuine OEM and high-quality aftermarket parts,’ continued Mr Vowles. ‘Our experienced sales team can quote a long list of Komatsu parts in minutes and are always ready to help identify what you need. We guarantee to ship stock items the same day for orders received before 3pm but we always go the extra mile to help the customer, however late in the day they call.’
The future
Once the workshop upgrade is complete in early November 2021, Plant Parts will seek to expand their repair offering to include all types of industrial hydraulic motors and gearboxes found in construction, quarrying, mining, and waste recycling equipment. ‘We regularly repair rotating case hydrostatic gearboxes rated up to 220,000Nm,’ said David Finch, ‘but will be able to handle even bigger units by the end of the year.’
For more information visit: www.plantparts.eu
- Subscribe to Quarry Management, the monthly journal for the mineral products industry, to read articles before they appear on Agg-Net.com