New Technology Enhances The Maintenance Process
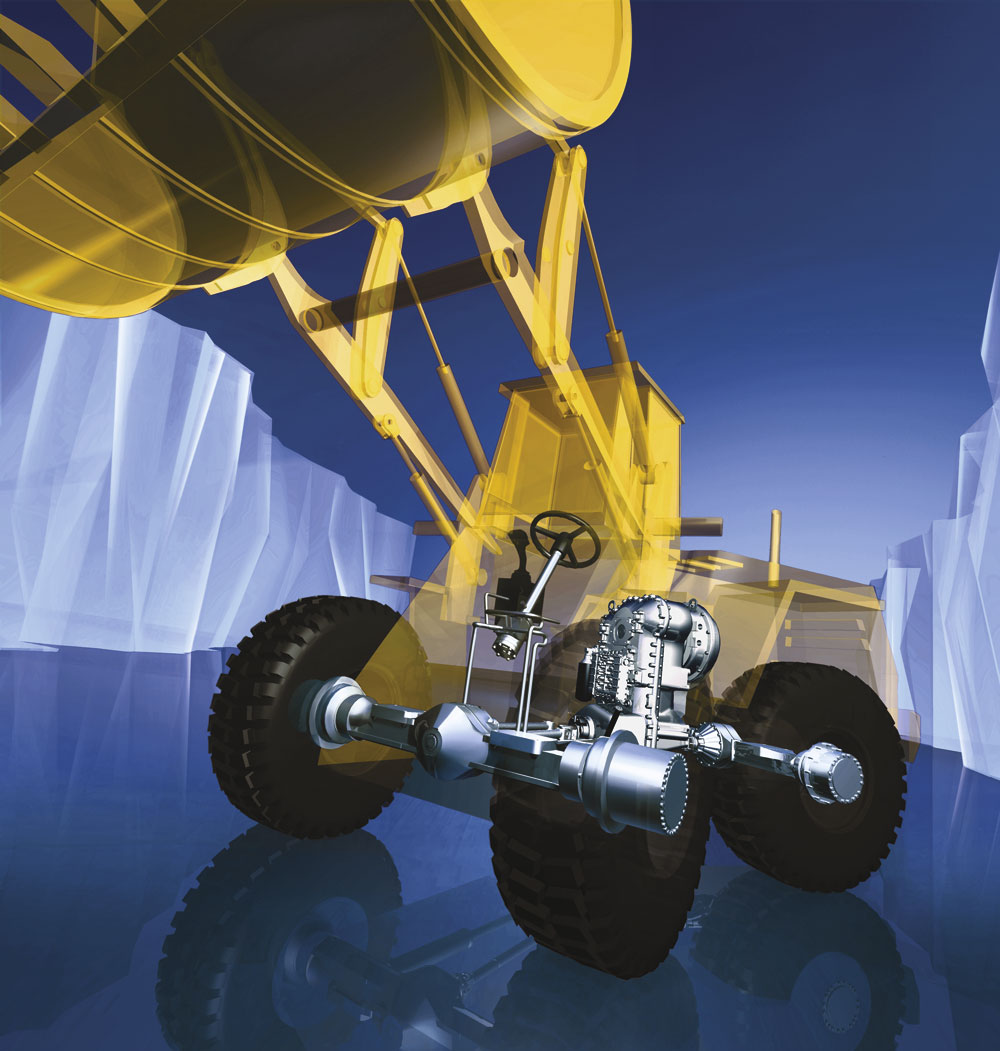
Today’s off-highway transmissions, featuring state-of-the-art electronic control systems and advanced diagnostics capabilities, deliver levels of performance, efficiency and reliability that were impossible to achieve with earlier mechanically controlled gearboxes. They are also helping to streamline the troubleshooting process and reduce the need for expensive and time-consuming ‘out of chassis’ repairs
In the last 15 to 20 years customer demands for more productive, efficient and reliable machines that are easier to operate and maintain have led to major developments in transmission design.
These developments have been most pronounced in the off-highway market where the latest wheel loaders, articulated dumptrucks and wheeled excavators use electronically controlled transmissions that deliver levels of performance, efficiency and reliability way beyond the capabilities of earlier mechanically controlled gearboxes. Transmissions such as ZF’s Ergopower range of automatic powershift transmissions are specified by many of the world’s leading manufacturers of off-highway equipment including Bell, Case, Hyundai, John Deere, JCB, and Terex.
A major feature of these new electronically controlled transmissions is that they can be programmed to ‘communicate’ with the other major components of a machine so that its engine and ground speeds are always optimized during gear changes with no interruption in power. Other benefits of this ‘fly-by-wire’ technology include: reduced noise and exhaust emissions; increased reliability and durability; simplified operation and maintenance; and lower operating costs.
Advanced diagnostics
The operation and maintenance of these transmissions has been enhanced by their advanced diagnostics capabilities that can be used to either programme the transmission to optimize its performance or streamline the troubleshooting process in the event of a fault.
This is done by connecting the transmission’s control system to a laptop computer loaded with a diagnostic software system, such as ZF-Testman pro, which allows a service technician to download and analyse a wide range of operating data with just a few clicks of a mouse. The data is collected with the vehicle moving or stationary and can even be downloaded to a remote location via a mobile telephone network.
Another major benefit of this software is that it can significantly reduce the need for costly and time-consuming ‘out of chassis’ repairs. This is because it can reduce the risk of unexpected component failures and can virtually eliminate the need for ‘just in case’ repairs.
Electronic control systems and diagnostics software provide a comprehensive picture of what is going on inside a transmission and can even allow the identification of transmission faults before they develop into a costly component failure.
These developments, which have made a similar impact in the commercial vehicle and bus/coach sectors, have led to major changes in the way UK and Irish customers expect suppliers to support their transmissions and other driveline components.
This was confirmed by the results of a survey carried out by ZF, which showed how customers in the off-highway market require much greater levels of technical expertise and specialist support than they needed in the days of the old mechanically controlled transmissions.
Transmission repair options
The survey, which highlighted the growing emphasis being placed on diagnostic services and on-site support from mobile service engineers, also showed that customers want faster turnaround times on their transmission repairs and a wider range of repair options that can be tailored to their specific business needs.
There was surprisingly little demand for preventative maintenance and planned component-exchange programmes. This is despite the fact that these services are now widely available throughout the off-highway equipment market.
Preventative maintenance and planned component-exchange programmes are, nevertheless, something that ZF believe will become increasingly popular as more customers look to reduce downtime and lower the whole-life costs of their plant fleets. This point is confirmed by the growing number of ZF customers who want their transmissions covered by a service agreement that includes oil analysis and regular preventative maintenance inspections.
Another development that is having an important influence on the whole-life costs of off-highway transmissions and axles is the introduction of new oils that offer increased performance and reliability, while extending service intervals. Examples include ZF-Ecofluid and ZF-Powerfluid that use tailor-made formulas with highly efficient additives that deliver the high shear stability needed in transmission applications, while also delivering high wear protection and corrosion protection.
Maintenance costs are thus reduced with oil-change intervals being increased by up to 50% according to the application, which also makes a positive contribution to the environment.
In the last 12 months ZF have responded to the key points in their aftermarket survey by making major changes to the way they support their customers in the UK and Irish markets. The changes, which have led to a significant increase in the number of regionally based mobile service technicians operated by ZF DriveCentres, have made the company and its service dealers much more responsive to the needs of customers.
Faster response times
DriveCentres can respond much more quickly to customers’ service calls than they did in the past. Service technicians are also much better equipped to diagnose and repair faults on site, because they all carry and are fully trained in the use of the latest ZF diagnostic tooling. This means that most faults can be rectified on site without having to remove the transmission from the machine, which dramatically reduces the time the customer is without his machine.
ZF are also committed to further reducing the cost and turnaround times for more major transmission repairs.
This involves making further investments at the company’s extensive workshop facilities in Nottingham where they offer a number of repair options from simple repairs to fully remanufactured transmissions that can even incorporate all the latest design updates. By the end of this year the typical turnaround time for a ZF off-highway transmission repair, once it arrives in Nottingham, will be between 72h and six days, depending on the transmission and work involved.
ZF acknowledge that, ultimately, it is all about listening to customers and responding to their changing business needs with a range of products and services that deliver the best possible combination of quality and value. The company are therefore confident that the combination of new technology and the changes they have made to their support strategy will further enhance the performance, reliability and durability of their off-highway transmissions.
ZF Great Britain Ltd, Abbeyfield Road, Lenton, Nottingham NG7 2SX; tel: (0115) 986 9211; fax: (0115) 986 9261; email: webenq@zf-group.co.uk