Life In The Old Cat
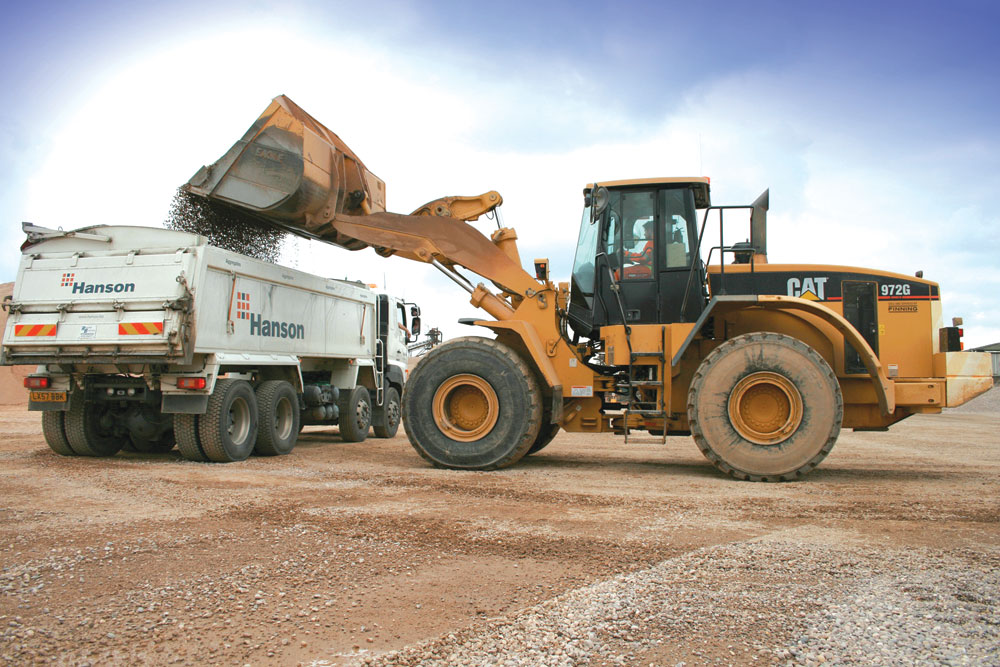
Two-week engine and transmission refurbishment helps breathe up to 14,000h of new life into Barton Quarry’s Cat 972G wheel loader
Finning product support consultant Noel Hancock and Damian McClean, South Staffordshire unit manager for Hanson Aggregates, explain what is involved in this increasingly popular maintenance solution
Located in Barton under Needwood, near Burton-upon-Trent, Hanson Aggregates’ strategically important Barton Quarry produces 750,000 tonnes of sand and gravel a year, supplying both local businesses and Hanson’s own concrete operations throughout the region. With demand for sand, in particular, seeing the need for an increase in output at the quarry, a major investment programme has already resulted in the commissioning of a new fixed processing plant, to be constructed in the coming months.
In line with this increased workload, further investment has also seen the quarry commission its first Finning Caterpillar refurbishment project, giving the site’s popular Cat 972G wheel loader a new lease of life.
Having worked for more than 13,000h loading sand and gravel into hoppers and articulated dumptrucks for two shifts a day, six days a week, the quarry’s six-year-old Cat 972G wheel loader has just received a complete engine and transmission makeover. The success of the carefully planned refurbishment project was made possible by the ongoing close scrutiny of the Cat 972G’s performance by Hanson’s operators and Finning’s field-service personnel.
Having performed all of the regular 500h scheduled maintenance and conducted SOS (Scheduled Oil Sampling) at each service interval, as part of an agreed support package with Hanson since the machine was purchased in September 2002, Finning engineers, led by product support consultant Noel Hancock, were able to identify the need for repair-before-failure (RBF) engine and transmission work to be carried out.
‘When you are able to gather data from a piece of plant equipment over a long period of time, you are in a very strong position to identify the key performance indicators that can lead to equipment failure,’ said Mr Hancock. ‘For example, with our analysis of oil samples taken from the Cat 972G, we were able to confirm that, although the engine and transmission were showing normal signs of wear for the age of the machine, no critical parts had been damaged and, therefore, it would be the ideal time to carry out a before-failure repair.
‘The importance of this process and information becomes clear when you look to analyse the cost of refurbishment, as until you have been able to take the machine, engine and transmission apart you can’t truly understand what work is required. Through oil sampling, however, you have a good indication that key parts are still intact and can be refurbished,’ explained Mr Hancock.
‘In Barton Quarry’s case, knowing this information before the process began in earnest was particularly important, as it allowed us to guarantee that we could refurbish the Cat 972G in the tight time frame required, to coincide with the site’s planned Easter shutdown.’
Given just two weeks to complete the whole refurbishment project, Finning divided the tasks of engine, transmission and associated machine refurbishment work between four key personnel. ‘By splitting the task of engine and transmission rebuild between two people working side by side, we were able to give each part of the project a dedicated focus and individual ownership,’ said Mr Hancock.
Before any work took place, however, the Cat 972G was washed down and pre-inspected for any other maintenance needs, identifying potential issues that could be fixed at the same time to avoid future downtime.
‘No additional work was discovered during the inspection, so together with the historic data that we already had on the machine, we were confident that the rebuild process would not throw up any surprises,’ explained Mr Hancock.
Having pre-ordered all of the required parts for the rebuild, the engine and transmission units were extracted in one piece from the chassis by removing the cab and engine guards. Transported via overhead crane to the specialist component workshop bays at Finning’s Cannock branch, the engine and transmission were then separated from one another.
Following Caterpillar’s dedicated written guidelines for each machine, the engine was completely stripped down with all parts checked for wear and inspected for damage using the Cat Service Information System, which provides all the specifications and guidelines needed to perform the refurbishment.
Taking just two days to perform the engine strip-down, Finning’s engine specialist, Dave Skitts, took a further six days to replace and refurbish a whole range of parts, including the turbochargers, bearings, gaskets and seals, injectors, pistons and liners.
‘Because our Finning engineers had looked after the Cat 972G for so long, and the operators at Hanson had taken care to use the machine correctly, there were no surprises waiting for us when we stripped the engine down,’ commented Mr Hancock.
Undertaken by Finning’s transmission specialist, Mick Witts, the refurbishment of the Cat 972G’s transmission unit also involved a complete strip-down, with particular attention paid to the transfer block, torque converter and transmission pump, all of which were completely overhauled. In a similar fashion to the engine refurbishment, bearings and gaskets were also replaced.
‘Unlike the engine refurbishment, we were presented with a small challenge with one of the transmission housings, where Mick found a few cracks that were developing,’ said Mr Hancock. ‘Fortunately, this did not set back the project timing, as we were able to replace the housing with parts already available and in stock on site.’
Completed within a day of each other, both the engine and transmission were linked back together before being replaced in the Cat 972G chassis, which had also received attention with line seals, coolant hoses, coolant and all fluids replaced. Lowered into place on the Thursday before the Easter break, the task of completing the project fell to Mick Daniel and Dave Kennerley, who worked through the Easter break to ensure the Cat 972G was completed and loaded on to its transport early on Monday morning, ready to go back to the quarry to commence work immediately.
Commenting on the success of the project, Damien McClean, Hanson’s unit manager for South Staffordshire, which includes Barton Quarry, said: ‘The Cat 972G is a vital piece of equipment for our operations, so it’s easy to see the dilemma of having to take this unit out of circulation for even a day. This is why, when I learnt from Finning that we needed to look at carrying out repair-before-failure work, I was very conscious of the planning process. By using the information and window we had for the repair work we were able to schedule it to coincide with a planned shutdown.
‘This obviously worked extremely well with the unit repaired and back on site in just two weeks. From an operational perspective, we are now able to benefit from a machine that has had potentially another 14,000h of life put back into the engine and transmission – effectively doubling its life for its current application, for a fraction of the cost of a new machine.’
Mr McClean was particularly grateful to the engineering team at Finning, especially those who worked through their Easter break to ensure the unit was completed on time. ‘It is always reassuring to know that we are working with a company like Finning who have such a flexible workforce that they are able to work to customers tight deadlines,’ he said.
Commenting on the conclusion of the rebuild, Noel Hancock added: ‘When you plan for this kind of activity it can be such a positive experience for the business, as specific operations can be planned around the absence of the equipment or units can be hired in for short periods to provide cover. If you don’t take this approach, however, the consequences can be severe, with operational shutdowns and the added expense of failed parts. Not only can such failure double the refurbishment cost, it can, in some cases, take the machine beyond economical repair.
‘In this particular case Hanson chose to refurbish the engine and transmission; the other option would have been to opt for replacement or off-the-shelf refurbished exchange units that we hold in stock. This approach can help to reduce the time it takes for replacement down to as little as four days. The options are definitely there and worth taking, as there is no accounting for the damage and inconvenience machine failure can cause a business.’