How Service Support Agreements Help Reduce Machine Downtime
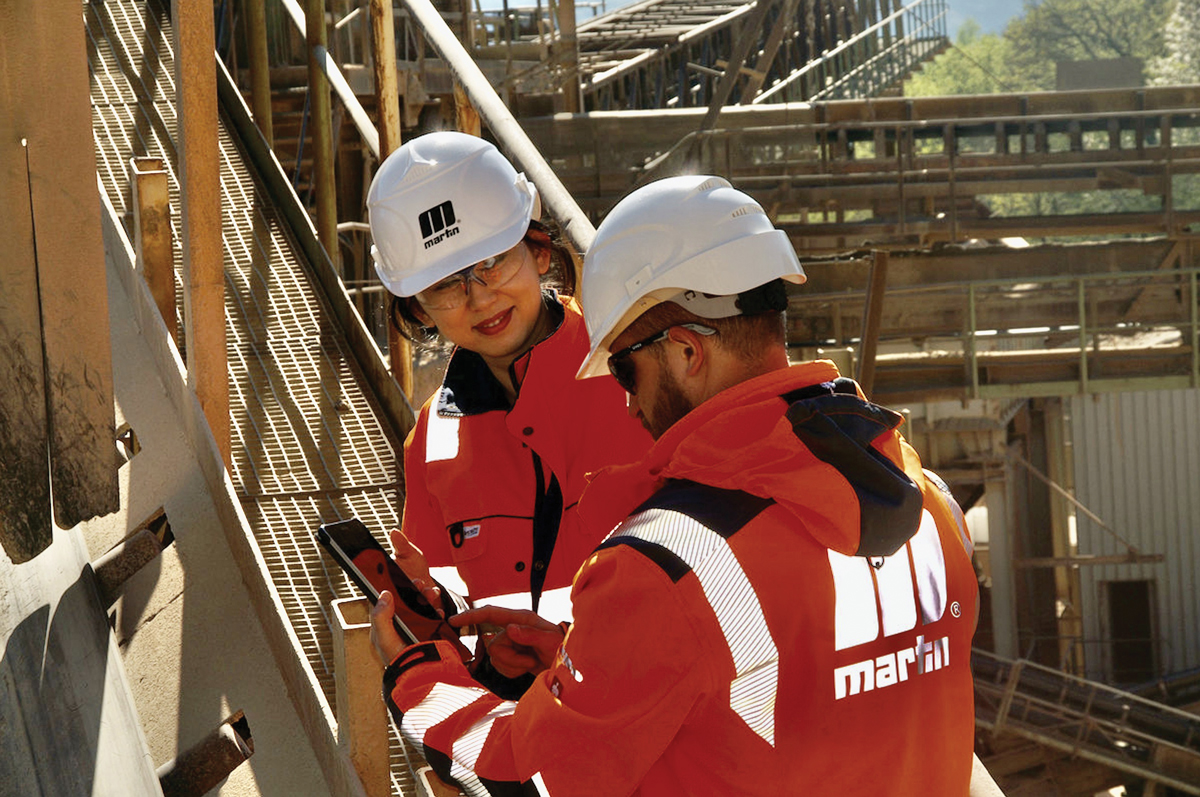
First published in the July 2020 issue of Quarry Management as Scheduled Support
In the aggregates industry, a growing number of operators are outsourcing key tasks, such as machinery optimization and maintenance, to plant and equipment suppliers. Bulk material handling specialists Martin Engineering explain how having a service support agreement in place can help their customers reduce conveyor downtime, improve workplace safety and minimize operating costs
Operators within the quarrying, waste-recycling and related sectors are increasingly turning to plant machinery specialists for properly managed maintenance programmes and expert support services. Conducted by experienced and well-trained technicians from specialty companies, these maintenance/service contracts have helped businesses improve safety and control their operating costs.
Specialty contracting may be a better choice for servicing than internal resources, as the providers are fully trained on the newest equipment designs and safety procedures. In many cases, they may be able to secure replacement equipment more quickly during periods of unscheduled downtime due to their industry-wide contacts.
Performance problems with conveyor components and systems can frequently be traced to improper installation or insufficient maintenance. It is recommended that the component manufacturer or expert contractor install equipment on both new and retrofit applications.
Serious performance problems stem from a lack of proper maintenance. Using a specialty contractor (also known as a ‘certified contractor’) for installation and ongoing maintenance contributes to safer and more efficient production, with less unscheduled downtime, and, in the long run, saves money and reduces injuries.
Training and retention
The time and resources required to train employees on equipment and certify them to conduct certain procedures (eg confined space entry, electrical work etc) can be a significant ongoing expense. As workers become more experienced and gain certification to properly maintain efficient systems, their value in the marketplace rises and retention can become an issue. In contrast, specialty contractors must be experienced, knowledgeable and certified to conduct the appointed maintenance, and it is up to the contracted company to retain and train the staff.
Maintenance danger zones
Due to a greater emphasis on safety and the expensive consequences of unscheduled downtime, bulk handling operators are being more meticulous about conveyor operation and maintenance. This increased scrutiny includes regular cleaning of spillage, improved dust control, as well as additional monitoring and maintenance, exposing employees to a moving system more often. These changes have introduced a variety of hazards.
Most common conveyor-related issues are found across a wide range of industries and personnel who work around the equipment on a daily basis often become complacent about the conditions – viewing issues as an unavoidable outcome of production rather than abnormalities in need of resolution. An experienced maintenance contractor would recognize these problems and may present solutions that internal resources have overlooked. The improvements are designed to reduce employee exposure, improve workplace safety and maximize productivity.
Types of service contracts
Maintenance programmes differ by provider and may be customizable to suit individual customers, but they generally fall into three categories: inspection/report; cleaning/servicing; and full service.
With a scheduled inspection and report contract, a specialty contractor thoroughly examines a system, from belt health and equipment function to the surrounding environment, and identifies any potential issues. A report is produced that presents findings and offers solutions.
Cleaning and servicing contracts are perhaps the most common. From spillage and silo cleaning to monitoring and changing belt cleaner blades, services can be very specific and are designed to fill the gap when maintenance crews might be overstretched. The first advantage to this is that a conveyor can be surveyed without requiring the attention of plant personnel, freeing them to go about their usual tasks. A second advantage is that the external surveyors are experts in best conveyor practices and current government regulations.1
At the highest level, full service and maintenance contracts send trained technicians who take accountability for monitoring, maintaining and reporting on every level of system function. They will replace wear components when needed and propose required upgrades in order to maximize efficiency, safety and uptime. This provides operators with cost certainty, making it easier to project and manage the total cost of operation.
Return on investment
Increasing speeds and volumes on older conveyor systems (originally designed for lower production levels) contribute to workplace injuries and increased downtime.2 Capital investments in newer semi- or fully-automated systems (designed for higher throughputs) require less labour, but maintenance staff need to be highly trained and specialized technicians.
Maintenance service contracts deliver the best return on investment (ROI) through a series of factors:
- Compliance – the contractor points out compliance issues and offers solutions prior to expensive fines and violations
- Injuries/liability – contractors rely on a strict set of safety procedures to conduct maintenance and reduce liability
- Efficiency – maintenance service contracts focus on improving and sustaining uptime with the least capital investment possible
- Consistency – contractors have a clear directive and are not affected by internal factors (eg labour disputes, morale etc)
- Cost of operation – with a defined scope of work on a set budget, along with clear reporting and recommendations on pending needs, operators can better forecast improvements and control labour costs, further improving ROI over time.
Conclusion
Maintenance service contracts are not just a way of controlling and potentially reducing the cost of operation; they are also a safety mechanism. For example, one case study showed a 79% reduction in lost-time incidents and a 40% improvement in production using specialty services, which demonstrated payback in days from an annual specialty maintenance contract.3
Workloads may preclude staff from maintaining proper compliance or they just might not notice some violations. Outside resources take ownership of the plant’s efficient and productive use of the conveyor system and strive to improve conveyor efficiency, maximize equipment life and increase safety to add value to the operation.
At the core of the issue is lower operating costs and improving production. The work should match or enhance efficiency with regard to downtime and throughput. If the criteria of compliance, cost savings and efficiency are met, the maintenance service contract has provided a tenable ongoing solution.
References
- ‘Standards: 1926.555 – Conveyors’ U.S. Occupational Safety and Health Administration (OSHA), Department of Labor, Washington, D.C. www.osha.gov/laws-regs/regulations/standardnumber/1926/1926.555
- Swinderman, Todd; Marti, Andrew D.; Marshall, Daniel: Foundations for Conveyor Safety, Sec. 5, pp 426 (2.7), by Martin Engineering, Worzalla Publishing Company, Stevens Point, Wisconsin, 2016. www.martin-eng.com/content/product/690/safety-book
- Swinderman, Todd; Marti, Andrew D.; Marshall, Daniel: Foundations for Conveyor Safety, Sec. 6, pp 472-476, ‘Case Study Return on Safety at a Coal Mine’, by Martin Engineering, Worzalla Publishing Company, Stevens Point, Wisconsin, 2016. www.martin-eng.com/content/product/690/safety-book
- Subscribe to Quarry Management, the monthly journal for the mineral products industry, to read articles before they appear on Agg-Net.com