Condition Monitoring With RFID Technology
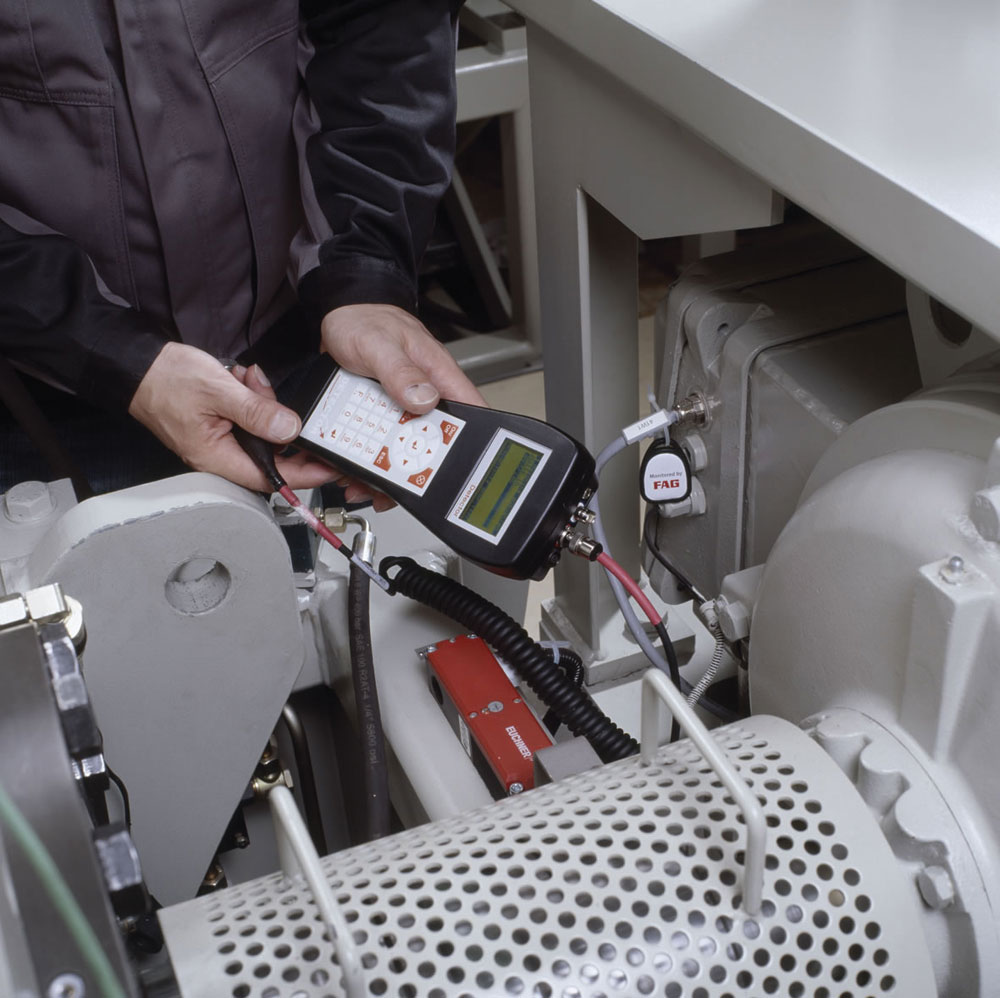
The maintenance management and condition monitoring division of Schaeffler UK, FAG Industrial Services (F’IS), is now offering customers RFID technology for its FAG Detector III device, the company’s hand-held vibration-monitoring and balancing system. RFID technology ensures that all measuring points on a route plan or routine maintenance check through a plant are automatically identified and that the data from these measuring points is recorded in the correct place for further analyses.
As with fixed, online monitoring systems, measurements with hand-held offline devices must be made regularly and at exactly the same measuring points as before. Only in this situation can meaningful data be obtained and analysed to predict potential equipment failure.
As Ian Pledger, F’IS field service engineer at Schaeffler UK, points out: ‘If the maintenance engineer incorrectly selects even one measuring point during his routine maintenance check around the plant and feeds this data into the maintenance management database, the spurious data may distort his trend analyses. An alarm that is triggered by false data may lead him to strip down the wrong machine, while the real fault is left undetected on another machine that potentially could break down, causing a double headache for the company.’
The new FAG Detector III with RFID technology is designed to eliminate user errors such as these. The RFID tags are simply fastened to the machine or equipment, as close to the measuring point as possible. When the maintenance engineer next does his or her routine checks, the RFID reader, built into the FAG Detector III, correctly identifies each of the tags in the plant, ensuring that the user collects repeatable, reliable data from the correct measuring points.
Mr Pledger explained: ‘Basically, the RFID technology ensures that operator error is eliminated. It gives the user an automatic, 100% guaranteed cross-reference check between what he thinks he is measuring, to what he should actually be measuring on his route plan. Up to now, companies have had to rely on the maintenance engineer to record the collected data in the right place, which is where mistakes can happen.’
This new technology is designed for maintenance teams that regularly collect and analyse vibration-monitoring data from multiple, similar measuring points – on machine tools, pumps, bearings, electric motors, fans, compressors, ventilators, gearboxes and spindles. Unlike conventional barcodes, the RFID tags can operate at temperatures up to 120°C and are resistant to dirt, oil and acids.
The FAG Detector III – the latest addition to Schaeffler’s ‘Detector’ series of damage diagnosis instruments – is also available with an optional, extended operational balancing function, which the customer can activate at a later stage after purchasing the basic unit. The device can then be used to balance rotors and shafts in both static and dynamic balancing applications.
The Detector III includes the full range of accessories required to carry out a balancing process, including sensors, trigger, magnetic holder and reflection marks. There is also an integrated, step-by-step user dialogue, which allows inexperienced operators to record and analyse reliable, accurate balancing data.
As well as retaining some of the familiar characteristics of the popular Detector series, the Detector III has a number of new and improved features. In addition to its completely redeveloped 16-bit hardware, the new device has increased storage space, storage of up to 300 time signals and a new reporting function. It also incorporates a second measurement channel for operational balancing, a new expanded keyboard and a viewer for displaying signals.
The built-in FAG Trendline software, which includes a database of more than
20,000 different bearing products from different suppliers, allows the user to analyse measurement data recorded using the FAG Detector III. Used in combination with the data viewer, the bearing database can be used to assess a machine’s condition. For example, up to four different measurement values can be stored and displayed against one measurement point and several defect bearing frequencies can be checked efficiently using a single measurement point.
Users also get an expanded, configurable ‘report generator’, which can be used to prepare a wide range of reports. These can be stored as templates and tailored for different customers. All the information in the system can be used for the report, including time signals, trend curves and alarm data.
For more information on the FAG Detector III with RFID technology call the Schaeffler UK marketing department on tel: (0121) 351 3833.