Babcock's approach to reducing the whole-life cost of mobile plant assets
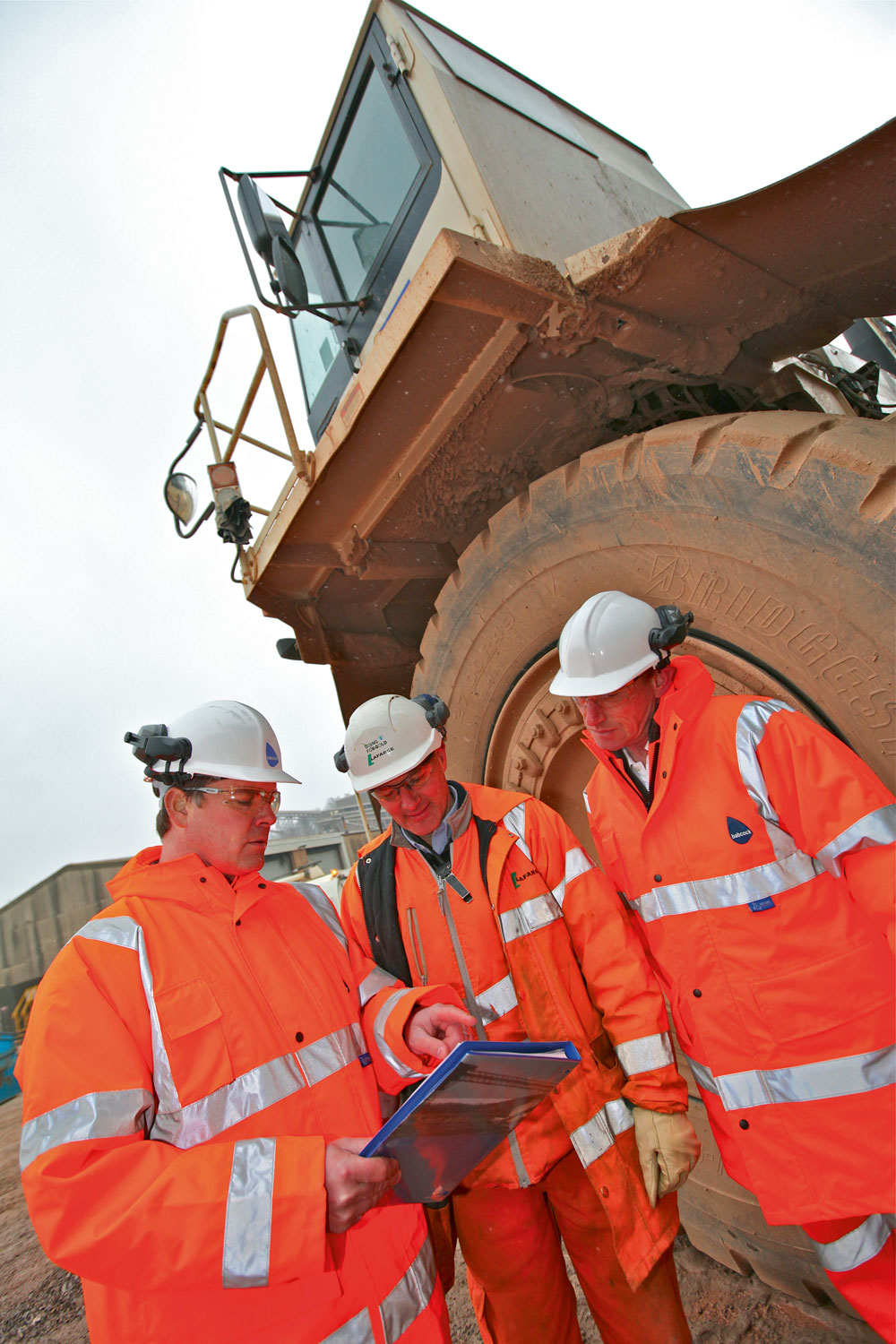
First published in the October 2013 issue of Quarry Management as ALCAMiE in Action
Fuel and maintenance are seen as the key areas for fleet operators in quarrying to find efficiencies. Simon Purchon, business development director at Babcock, examines how savings can be optimized at these stages, and if there are other areas where fleet operators can deliver increased efficiencies to their global fleets.
The quarrying industry in the UK faces a series of challenges in the coming years as budgets become ever tighter and operational costs continue to rise. There are many reasons for this, but one thing is certain, the cost of getting aggregate products out of the ground is not going to decrease while quarries and pits increase in size and depth.
The cost of operations dictates that efficiencies need to be found in areas other than fuel and maintenance, and one way of achieving this is through improving the whole-life cost of the assets used to extract and transport the quarried product. Whole-life cost refers to the total asset ownership costs over its lifetime. It is the purchase price of an asset minus the residual value and plus the maintenance and fuel costs. Traditionally, quarry operators have tended not to worry about the purchase price, writing it off as a depreciating asset. Where they have felt able to deliver efficiencies is through maintenance and fuel costs.
Standardized approach
The most effective way of driving down fuel and maintenance costs is to implement a standardized approach across all operations. This delivers efficiencies through a cheaper supply chain and allows assets to be transferrable across sites to provide increased resilience. Yet many large organizations have evolved through merger and acquisition, leaving sites to work independently when it comes to asset management. This variance means that a business cannot always provide a complete picture of cost and performance across its assets base.
A standardized repair and maintenance regime across a business’ operations is an important way of driving down costs, but it is only one chapter in a longer story. By only focusing on fuel and maintenance as a means to find efficiencies, and not the asset itself, quarrying and mining companies are missing the chance to significantly reduce the whole-life cost of their assets.
Babcock’s approach
Babcock have a vast amount of experience in managing complex combinations of assets in critical environments, ranging from the nuclear sector to the emergency services, and currently manage more than £42 billion of assets for customers globally. This has allowed the company to develop a proven process that delivers whole life-cycle asset management for quarrying and mining companies around the world, including Lafarge and Aggregates Industries.
The Babcock process starts by formalizing the asset review process – providing the rationale for all future purchasing decisions and ensuring that the right asset is identified for each job. Babcock work in partnership with their customers to understand the production volume cycles, the annual tonnage forecast, and what equipment is in use, thus allowing planning for the next 12 months. Everything is considered, from forecasting scheduled maintenance to identifying which equipment is reaching its optimum refurbishment point and due for an overhaul or even replacement.
By consolidating procurement processes, assets can be purchased in bulk to leverage the capital cost, specification and warranty conditions. Similarly, when a significant number of orders are placed for the coming year, it allows OEMs to forward plan their manufacturing schedules, smoothing production flows and reducing costs, which provides opportunities for additional discounts to be offered.
Driving productivity
Once the asset-review process has been completed, the focus turns to how the equipment is operated and managed on the ground to maximize productivity. Knowledge of best practice in asset management can eliminate unnecessary repair or maintenance costs, delivering long-term savings across the year.
This is where Babcock’s heritage is essential. The company’s experience and expertise has enabled it to develop ALCAMiE, a customized ‘toolbox’ of asset-management systems and processes that allow assets to be cost-effectively managed throughout their life.
ALCAMiE identifies the criticality of equipment, such as what assets will bring a quarry to a grinding halt if they break down, as opposed to other equipment whose function, whilst important, can be replicated by other tools. By dividing assets according to criticality, ALCAMiE re-prioritizes what needs to be done first to ensure equipment is available when and where needed.
More than just upgrading
Effective asset management is more than buying new kit to replace old stock. Babcock’s methodology is to extract the maximum value out of every asset but not to take it beyond what is acceptable for optimum performance. The company helps customers to fully appreciate that extending the lifespan of existing assets can be as important as replacing them.
There is a time in every asset’s life cycle when reliability fades and a decision has to be made to repair, rebuild or replace the asset – the so-called ‘three Rs’. Babcock recognize when it is appropriate to replace an asset but, when possible and in the customer’s best interests, will always look to rebuild equipment to deliver an extended operational lifespan.
An average large mobile asset is designed and built to operate for an optimal life in excess of 30,000h, subject to size and working environment. By performing interventions at the right time, usually around 16,000h, it is possible to ensure that the asset will operate effectively for the rest of its optimal life. Typically, a rebuild includes reworking of the powertrain, hydraulic and electrical systems that support the machine. The key is to carry out comprehensive condition monitoring (including oil and fluid analysis) on all machines to ensure that major unit failures are foreseen and prevented from occurring. Unplanned failures not only disrupt the operation, but can double the rectification cost base.
Results
When the time does arrive for equipment to be replaced, Babcock guide customers through the process to identify the right equipment for them to drive productivity and improve overall running costs. To date, Babcock have procured more than 65 assets for Lafarge with a combined value of more than £25 million, all built with the latest technology to drive down fuel consumption, maintenance costs, and meet the latest health, safety and environmental regulations. However, over the same time, Babcock have arranged for some 133 pieces of equipment to be rebuilt – where it has made clear economic sense to do so.
Data hungry
The impact of ALCAMiE will grow as Babcock collate more unique data from fleets working in varying terrains and environments around the world. As part of this, the company is working to merge different OEM telemetric data platforms into a single dashboard within ALCAMiE. By consolidating this information, it will be possible to reveal united data that was previously unseen, including the fuel burn, location, system faults, driver behaviour, and engine idling time. This will help determine what preventative work is necessary to maximize efficiency and increase productivity. Babcock’s aim is to display useful information that drives behaviour, rather than overwhelming people with complex data that is too difficult to analyse and easily ignored.
Moving forward
Babcock’s approach is transforming how the mining and quarrying industry manages its critical fleets of vehicles and equipment, and this impact is growing. In June 2013 Aggregate Industries awarded Babcock a £50 million, five-year contract (with a five-year extension option) to provide a fleet-managed service for their heavy mobile equipment in the UK. Through this, Babcock will use ALCAMiE to optimize the performance of more than 400 items of heavy mobile equipment located across more than 150 sites.
By consistently developing and improving the service supplied to customers as the company’s role and impact across new and existing territories grows, Babcock will continue to prove the uniqueness of their approach and demonstrate how they are an ideal partner for fleet-management operations.
For further information visit: www.babcockinternational.com
- Subscribe to Quarry Management, the monthly journal for the mineral products industry, to read articles before they appear on Agg-Net