A CAN-do Approach
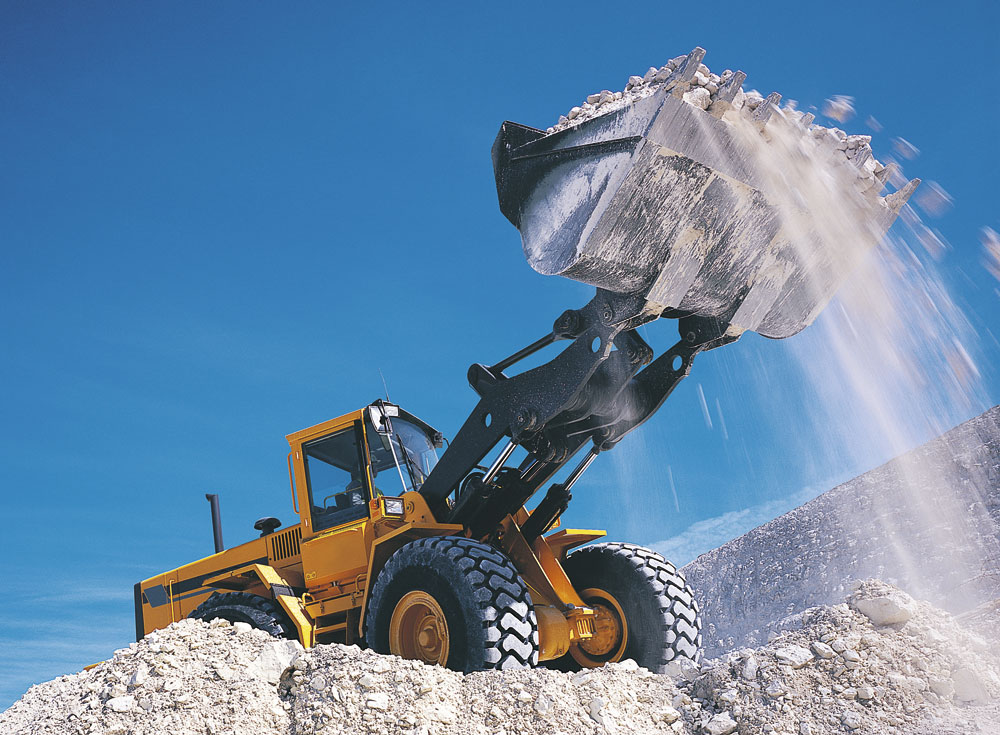
Centralized lubrication systems offer a whole host of advantages to operators and engineers within the construction industry. Phil Burge, communication manager for SKF, looks at how recent advances, including powerful CAN-bus technology, are cutting costs and enhancing efficiency
The capacity to deliver precisely regulated volumes of lubricant exactly where and when needed has established centralized automatic lubrication systems as a powerful force in the construction industry, allowing engineers to improve machine life and reduce operating costs. One reason for this is that the manual application of lubricant is not always appropriately judged, and when either too much or too little lubricant is used machine conditions can swiftly deteriorate.
Engineers have a tendency to over-lubricate because they are keen to prevent bearings from running dry in the elevated temperature that results from inadequate lubrication. However, an overenthusiastic application of lubricant can also cause problems, increasing friction, raising temperature and promoting the migration of grease into parts where it can cause damage, such as electrical motors. Problems can escalate if the incorrect specification of lubricant is applied, as this can reduce both the performance and lifespan of the equipment, increasing maintenance requirements and downtime losses, and adding unwanted costs to the balance sheet.
It is important, therefore, that the finer points of lubrication practice are appreciated and that engineers do more than simply provide lubrication arbitrarily. Re-lubrication at regular intervals is vital to maximize efficiency and machine/component lifespan, providing not only a vital ingredient in the efficient day-to-day running of machinery but also a protective coating that protects against wear and corrosion. To ensure the correct delivery of lubrication, engineers require a reliable method that will maintain efficiency and prevent unnecessary plant expense.
A useful tool that can be employed to avoid machine wear or failure as a result of inappropriate manual lubrication is a centralized automatic lubrication system, which can be incorporated as an external or internal part of construction machinery. Centralized lubrication systems offer the potential for engineers to prescribe the most suitable lubricant for a given piece of equipment and establish a routine whereby the system delivers a precisely regulated volume of that lubricant at regular intervals. This precision control can be especially important for lubrication points with low grease requirement because, as already mentioned, too much lubrication can be as harmful as too little.
Contamination and corrosion present a major challenge to the effective function of mechanical components, especially within the construction industry, but today’s centralized lubrication systems are sturdy constructions that offer high operational reliability. A choice of systems is available and there are many options for customization, with specification depending upon factors such as the type of machinery concerned and the ambient temperature of the application.
Centralized lubrication systems incorporate piston pump units with an integrated control unit to distribute lubricant to progressive feeders, which consecutively supply the quantity of grease required to the individual lubrication points. When the pump is running, each point receives an optimum level of lubrication, while a display showing the fill level of the reservoir allows a top-up during work breaks and scheduled machine downtime. The display can also offer feedback on the level of lubricant consumption, alerting engineers to any unexpected deviations from the normal pattern of activity. With a capacity for high lubricant consumption, sturdy construction and the ability to handle highly viscous lubricants, these pump units are fully equipped to meet the demands of heavy machinery.
A universal, easy-to-use, standard control device for progressive centralized lubrication systems is the IG502 base unit from SKF, while further operational features are offered by the company’s LC502 control unit, which can offer control according to either time or pump speed. The latter option provides the benefit of preventing pump speed variations that are not considered when using solely time-dependent control.
For even greater degrees of control over the centralized lubrication system, engineers can now take advantage of CAN-bus technology, which offers integration with other on-board equipment and the facility to increase the level of diagnostic information available. The potential benefits of CAN-bus are illustrated by considering a machine with multiple moving parts, such as a hydraulic excavator; the slewing ring, boom, arm and bucket of a hydraulic excavator can be independently lubricated using CAN-bus technology according to needs and specific operating conditions. CAN-bus technology also allows separate control and monitoring of each section, alerting operators to errors before major problems develop.
A major advantage of CAN-bus technology is that it allows a single pump unit to serve a lubrication system for a single machine that has been divided into up to four independent zones, each controlled using electronic valves. Fully integrated via electronic control with the on-board computer, the lubrication system can be configured using the on-board display, where operators can view precise detection of errors. Functional monitoring is performed using cycle switches which have been engineered to detect and signal possible problems before damage is caused to components by issues such as lack of lubricant. A further advantage of a CAN-bus system is that, when fully integrated into the on-board system, machine manufacturers can reduce the installation effort required for electrical lines.
While the precise specification of a centralized lubrication system will depend on the size of a machine, type of required lubricant and number of lubrication points, the following summary provides a useful overview of the more commonly specified systems. For small- to medium-sized machines, single-line lubrication systems for semi-fluid grease dispense lubricant volumes from 0.01cc to 2.5cc to individual lubrication points on each lube pulse. For medium-sized and larger machines, dual-line lubrication systems for semi-fluid grease and hard grease provide solutions with many lubrication points and long lines operating in harsh conditions, such as those experienced within the construction industry. Progressive lubrication systems for semi-fluid grease and hard grease are ideally suited to machinery such as hydraulic excavators, and when additionally equipped with CAN-bus technology, they can control, deliver and monitor lubricant in real time. This allows lubrication points to be continuously supplied with metered lubricant while the machinery is in operation and all the bearings are moving. More advanced systems will incorporate a malfunction diagnosis memory, which will not only display error notifications, but also record how long a machine has been continuously operated and log the date, time, and type of any error.
In terms of functionality, centralized lubrication systems clearly offer a range of options that can enhance and improve the operation of construction machinery. However, it should be noted that these systems not only increase efficiency and cut costs, but also benefit the environment, as SKF proved when a German customer adopted centralized systems on 50 machines ranging from 3 tonnes up to 87 tonnes. By modelling the impact of the systems on a small wheel loader and a 45-tonne crawler excavator, SKF were able to accurately estimate lubricant savings. If maintained daily and according to instructions, the use of automatic centralized lubrication systems allows a calculated annual lubricant saving of approximately 28% or 668kg for the entire fleet. While this is clearly a major saving in itself, the actual savings will be even greater because, in practice, operators tend to press one additional stroke of grease into the grease nipple rather than use too little, which could amount to a further 20% saving.
The fact that centralized lubrication systems can benefit not only new but also existing machines has allowed a wide audience of end-users to capitalize on enhanced efficiency and performance. Heavy machinery can be conveniently retrofitted with centralized lubrication systems as long as the chosen supplier provides complete kits with all the necessary components, plus the plans and instructions for assembly.
It is crucial to the efficient operation of construction machinery that effective lubrication is provided. The failure of manual lubrication to deliver the correct lubricant to the correct degree can lead to excessive waste, increased cost, machine wear and failure. The latest systems incorporating CAN-bus technology provide not only a greater level of operator control, but also marked reductions in maintenance and running costs, improving the long-term operation of construction machinery.
For further information call SKF on tel: (01582) 490049; email: marketing.uk@skf.com; or visit: www.skf.co.uk