Taking The Lead
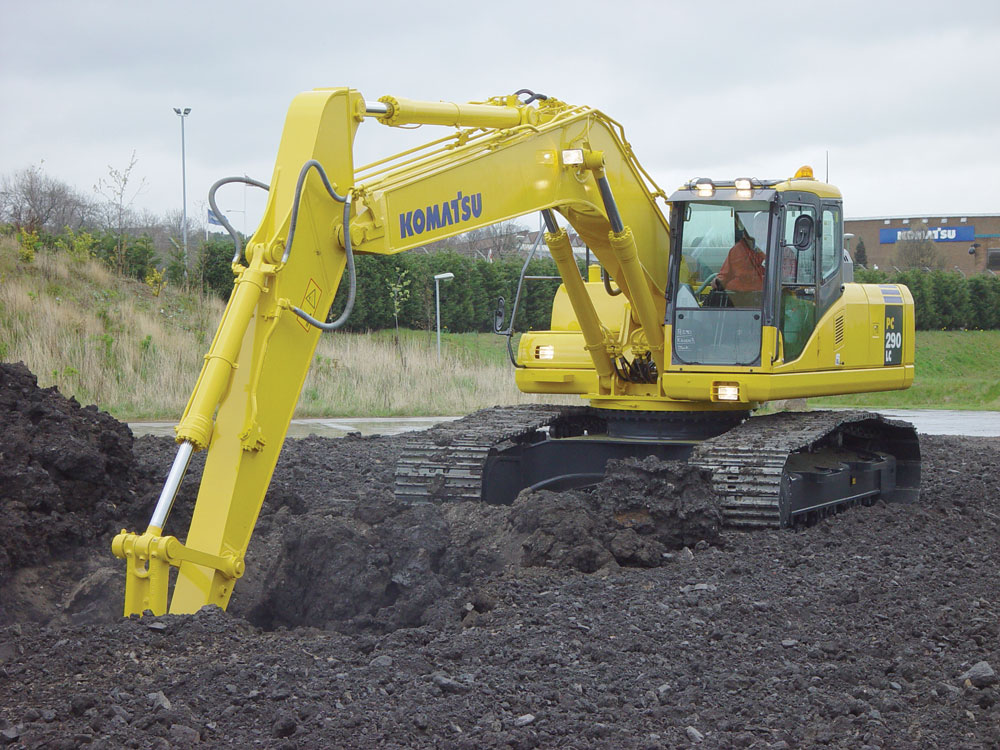
The introduction of Komatsu’s new-generation Dash-7 excavator models earlier this year was heralded as the beginning of a new approach to excavator design. Like the earlier Dash-5 and Dash-6 models, the new machines are being rolled out in stages. First to be launched in the UK were the PC290-7 and PC340-7, rated at 29 tonnes and 34 tonnes respectively. These have now been joined by the 21-tonne PC210-7 and 24-tonne PC240-7 machines.
Komatsu claim to have raised the benchmark in excavator design with a number of significant achievements in the development of this new series, including increased productivity, improved fuel economy, reduced operating noise, full compliance to European Stage 2 emission requirements, and even higher levels of operator comfort. For example, the PC340-7 is said to offer an 8% increase in productivity, a 4% improvement in fuel efficiency and an extra 14% cab space over its Dash-6 equivalent.
Of particular note, each of the new Dash-7 models is equipped with Komatsu’s sophisticated EMMS (Equipment Management and Monitoring System) and VHMS (Vehicle Health Monitoring System) on-board electronic systems, both of which are accessed via a combined keypad and multi-colour LCD panel in the cab. Komatsu were the first plant manufacturer to introduce electronic computer control into their excavators, and these new, upgraded systems represent the next level of sophistication over the control system found on the Dash-6 machines.
As their names imply, EMMS is designed to achieve optimal productivity by controlling and monitoring all excavator operations and functions via a highly intuitive, multi-function user interface, while VHMS provides a precise health check on all the machine’s running conditions and the alerts operator and service technician to events and conditions that could damage vital components.
Using EMMS, the excavator operator has fingertip control of the machine’s three working modes (Active, Economy and Breaker), plus a Lifting mode, each of which is designed to match the engine speed, pump speed and system pressure to the operational requirement.
Active mode provides maximum power and fast cycle times as well as allowing access to the ‘PowerMax’ function, which temporarily increases digging force by 7% for added power in tough situations. The environmentally friendly Economy mode reduces engine noise, fuel consumption and emission levels, while the Breaker mode delivers optimum hydraulic pressure, flow and engine rev/min for breaker applications. Lifting mode raises hydraulic pressure to increase lifting capacity by 7%.
EMMS also gives the operator fingertip control of several other functions such as low, mid- or high travel-speed selection, hydraulic pump oil-flow adjustment and password protection for machine start-up, to prevent theft or unauthorized use.
The VHMS real-time monitoring system allows machine functions and abnormalities to be checked by the operator at the beginning of, and during, each working shift. The system monitors engine oil level, cooling water level, fuel level, engine water temperature, engine oil pressure, battery charging level, air-filter clogging and numerous other operational parameters, and indicates when any abnormalities are detected. A new Maintenance Indicator function has also been added to the system; this raises an alarm when oil and filters need to be replaced.
To assist the service technician, up to four different operating parameters can be monitored and displayed simultaneously by VHMS to provide a broader diagnostic overview for faster troubleshooting. Parameters include operating conditions such as hydraulic oil pressure, engine rev/min, and various voltages, current and temperature measurements.
Unlike the earlier system, mechanical system failures are now monitored by VHMS, in addition to electrical system failures, and a new data memory allows any such failures and abnormalities to be stored and recalled to assist in troubleshooting. To ensure accurate documentation of vital service management information, mechanical system failures cannot be erased from the VHMS, while up to 20 of the most recent electrical system failures can be stored on the system. All failures are indicated by a six-digit fault code which is displayed on screen together with the relevant contact phone number, to allow the service technician to call for replacement parts or further technical help and advice, as required.
Marubeni-Komatsu Ltd, Padgets Lane, Redditch, Worcs B98 0RT; tel: (01527) 512512; fax: (01527) 502310; email: info@mkl.co.uk; website: www.MarubeniKomatsu.com