Power To The People
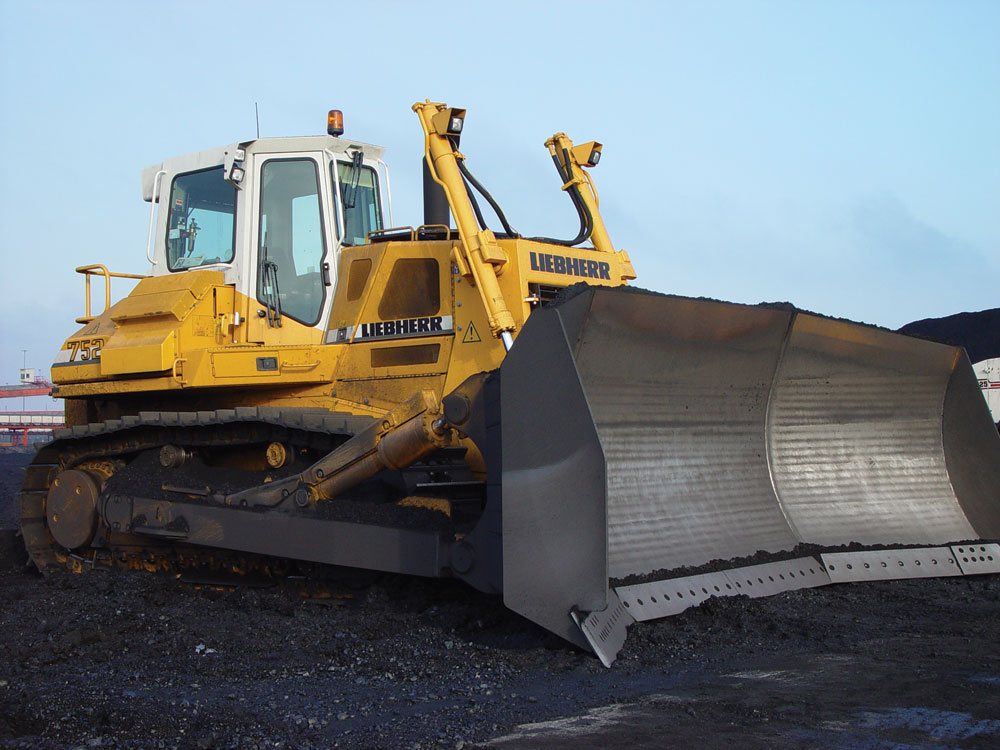
Liebherr PR752 Litronic dozer plays vital role in dockyard coal-handling operations for leading electricity generator
Innogy plc are the UK’s leading generator and distributor of electricity and co-owner of a major import–export bulk-handling facility at the Royal Portbury Dock in Bristol. Representing a combined investment of around £120 million, this facility is run as a joint venture with The Bristol Port Company, receiving, processing and transporting a wide range of bulk products, including some 6–7 million tonnes of coal a year as well as grain, fertilizer and aggregate materials.
The port’s fully automated coal-handling facilities are located on both sides of the river Avon, the Portbury side being the import operation with two berths capable of receiving ships up to 110,000 tonnes. Here, two 2,000 tonnes/h Kone continuous ship unloaders, an extensive covered transfer conveyor system and a 65-acre coal stock yard equipped with three Strachan & Henshaw stacker/reclaimers provide round the clock cargo removal, stockpiling and reclaiming capabilities. Meanwhile, on the Avonmouth side, which is linked to Portbury by a tunnel conveyor under the river, operations are devoted to the distribution of coal by rail, with over 75 deliveries a week to Innogy’s Didcot and Aberthaw power stations.
Following a comprehensive programme of site assessments and performance tests, Innogy recently purchased a Liebherr PR752 Litronic hydrostatic dozer to assist with coal-handling duties in the coal stock yard, where the machine is operated and maintained on Innogy’s behalf by The Bristol Port Company. The PR752 is Innogy’s first Liebherr machine and was selected for the task because of its high level of mobility and agility, with both forward and reverse speeds said to be noticeably better than previous equipment.
By reducing cycle times, the dozer is expected to make a significant improvement in the tonnage of coal that can be handled and processed at the site. Working a 50h week in the 700,000-tonne capacity, three-bay stock yard, the dozer is primarily involved in managing coal movements to and from the stacking conveyors and reclaimers, as well as undertaking coal recovery and consolidation work and other clean-up and road-clearance duties around the site.
The PR752 Litronic has an operating weight of 40 tonnes and is powered by a turbocharged, fuel-efficient, six-cylinder Liebherr D9406 TI-E engine which delivers 243kW. Travel drive is via a closed-loop hydrostatic system, with each track driven independently. Travel direction, speed, steering and track counter-rotation is via a single, easy-to-use, multi-directional electronic joystick which is integrated into the operator’s seat armrest. The machine’s speed range is infinitely variable up to 11km/h, while a speed-sensing control ensures a constant balance between travel speed and drawbar pull to avoid engine overload. Straight line travel is also electronically controlled. Low fuel consumption and easy serviceability of both the engine and the hydrostatic system were also said to be important considerations in the decision to purchase the Liebherr machine.
To cope with its coal-handling operations, the dozer has been supplied with wider than normal tracks and a large 5.5m x 2.0m (22m3) U-blade which is also controlled via a multi-directional joystick. For this particular application, the machine also features a coal-deflector undercarriage, a radiator guard and additional hydraulics for angle and semi-U-blade operations.
Catering for operator comfort and safety, the PR752 features a spacious and ergonomically designed cab which is air-conditioned and resiliently mounted with integrated ROPS and FOPS and all-round safety glass. The seat is fully adjustable and a comprehensive instrument panel provides the operator with continuous performance data. The entire cab can be tilted to an angle of 40° by means of a hand pump to allow easy access to machine components for servicing purposes.
Innogy’s PR752 Litronic also features a wide range of safety equipment including additional rear lights, a reversing alarm, reversing lights, a flashing beacon, additional front lights on the lift cylinders, a rear access platform with guardrail and an Ardent fire-suppression system.
Liebherr Great Britain Ltd, Travellers Lane, Wellham Green, Hatfield, Herts AL9 7HW; tel: (01707) 268161; fax: (01707) 261695; email: info@lgb.liebherr.com
Innogy plc are the UK’s leading generator and distributor of electricity and co-owner of a major import–export bulk-handling facility at the Royal Portbury Dock in Bristol. Representing a combined investment of around £120 million, this facility is run as a joint venture with The Bristol Port Company, receiving, processing and transporting a wide range of bulk products, including some 6–7 million tonnes of coal a year as well as grain, fertilizer and aggregate materials.
The port’s fully automated coal-handling facilities are located on both sides of the river Avon, the Portbury side being the import operation with two berths capable of receiving ships up to 110,000 tonnes. Here, two 2,000 tonnes/h Kone continuous ship unloaders, an extensive covered transfer conveyor system and a 65-acre coal stock yard equipped with three Strachan & Henshaw stacker/reclaimers provide round the clock cargo removal, stockpiling and reclaiming capabilities. Meanwhile, on the Avonmouth side, which is linked to Portbury by a tunnel conveyor under the river, operations are devoted to the distribution of coal by rail, with over 75 deliveries a week to Innogy’s Didcot and Aberthaw power stations.
Following a comprehensive programme of site assessments and performance tests, Innogy recently purchased a Liebherr PR752 Litronic hydrostatic dozer to assist with coal-handling duties in the coal stock yard, where the machine is operated and maintained on Innogy’s behalf by The Bristol Port Company. The PR752 is Innogy’s first Liebherr machine and was selected for the task because of its high level of mobility and agility, with both forward and reverse speeds said to be noticeably better than previous equipment.
By reducing cycle times, the dozer is expected to make a significant improvement in the tonnage of coal that can be handled and processed at the site. Working a 50h week in the 700,000-tonne capacity, three-bay stock yard, the dozer is primarily involved in managing coal movements to and from the stacking conveyors and reclaimers, as well as undertaking coal recovery and consolidation work and other clean-up and road-clearance duties around the site.
The PR752 Litronic has an operating weight of 40 tonnes and is powered by a turbocharged, fuel-efficient, six-cylinder Liebherr D9406 TI-E engine which delivers 243kW. Travel drive is via a closed-loop hydrostatic system, with each track driven independently. Travel direction, speed, steering and track counter-rotation is via a single, easy-to-use, multi-directional electronic joystick which is integrated into the operator’s seat armrest. The machine’s speed range is infinitely variable up to 11km/h, while a speed-sensing control ensures a constant balance between travel speed and drawbar pull to avoid engine overload. Straight line travel is also electronically controlled. Low fuel consumption and easy serviceability of both the engine and the hydrostatic system were also said to be important considerations in the decision to purchase the Liebherr machine.
To cope with its coal-handling operations, the dozer has been supplied with wider than normal tracks and a large 5.5m x 2.0m (22m3) U-blade which is also controlled via a multi-directional joystick. For this particular application, the machine also features a coal-deflector undercarriage, a radiator guard and additional hydraulics for angle and semi-U-blade operations.
Catering for operator comfort and safety, the PR752 features a spacious and ergonomically designed cab which is air-conditioned and resiliently mounted with integrated ROPS and FOPS and all-round safety glass. The seat is fully adjustable and a comprehensive instrument panel provides the operator with continuous performance data. The entire cab can be tilted to an angle of 40° by means of a hand pump to allow easy access to machine components for servicing purposes.
Innogy’s PR752 Litronic also features a wide range of safety equipment including additional rear lights, a reversing alarm, reversing lights, a flashing beacon, additional front lights on the lift cylinders, a rear access platform with guardrail and an Ardent fire-suppression system.
Liebherr Great Britain Ltd, Travellers Lane, Wellham Green, Hatfield, Herts AL9 7HW; tel: (01707) 268161; fax: (01707) 261695; email: info@lgb.liebherr.com