A Burning Issue
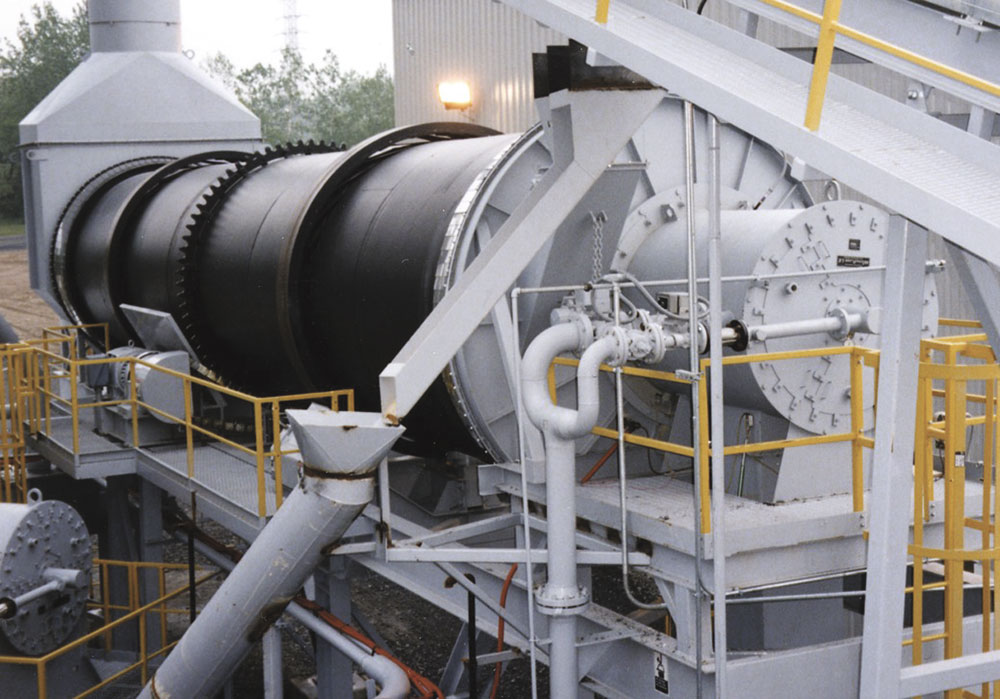
New legislation that comes into effect at the end of 2005 will have a major impact on UK roadstone producers
The Waste Incineration Directive 2000/87/EC is new legislation that incorporates the old Waste Oil Directive and will have a major impact, particularly on the UK roadstone industry. From 28 December 2005 all users of reclaimed fuel oil (RFO) will be subject to the same directive as major incineration plants. This includes all new plants built since 28 December 2002.
With constraints on emissions of NOx, SO2, HCI, HF and dust, one of the main implications is that products of combustion will need be held at a minimum residence temperature of 850°C for two seconds.
Currently, there is no burner system installed on an asphalt or aggregate-drying plant in the UK that comes close to satisfying this requirement. The industry will, therefore, be forced to look for other viable solutions.
The few options available include:
Permanent gas-oil (diesel) firing — Switching from RFO to gas oil will move the process outside the constraints of the Waste Incineration Directive. For most operators this will represent minimum or zero capital cost, as a gas-oil facility is often already installed as an alternative fuel option. This will, however, have a major impact on operating costs. Current prices of around 25p per litre for gas oil represent up to three times the cost of RFO. On a plant producing 100,000 tonnes of asphalt per year, the extra fuel cost would be around £125,000 per annum.
Natural gas conversion or other available gas fuels (LPG, landfill gas etc) — Natural gas conversions will give producers around a 50% saving on fuel cost (against gas-oil only users). In most cases burners would need to be replaced and capital costs would essentially be for fundamental burner modifications and the provision of a gas-connection pipeline. The main limiting factor, however, will be the availability of gas supply in remote areas.
Close-coupled combustion/residence chambers — Close-coupled combustion chambers could represent a significant capital cost but would allow users to continue to take advantage of RFO as a readily available and inexpensive fuel. From December 2005 it is widely expected that the cost of RFO will drop to around 2–3p per litre. Any operators continuing to use RFO could therefore expect a payback on capital expenditure of around 12–18 months, and hence continue to reap the benefit of this useful energy source.
The close-coupled chamber would need to be designed to raise the products of combustion up to a guaranteed minimum 850°C for a residence time of 2s. Plant alterations required might include modifications to the extraction system and dryer lifters, particularly to optimize the changed energy transfer.
Combustion specialists NA-Stordy are able to offer guidance on the Waste Incineration Directive and will conduct feasibility studies of all the options as well as providing innovative solutions, typically:
- low-NOx technology short-flame burners for soil remediation
- dual-fuel burner packages for dryers
- conical-flame burners for batch plants
- proportioning oil burners
- control and safety systems
- pumps and spares.
The company’s team of experienced service and commissioning engineers regularly handle projects ranging from £5,000 to £1,000,000, providing full engineering design, drawings, installation and project-management services.
For further information contact: Jonathan Farmer, industry sales manager (asphalt), on tel: (07870) 270221; or email: jonfarmer@na-stordy.com
NA-Stordy Combustion Ltd, Heath Mill Road, Wombourne, Wolverhampton, W. Mids WV5 8BD; tel: (01902) 891200; fax: (01902) 895552; website: www.na-stordy.com