Working Safely
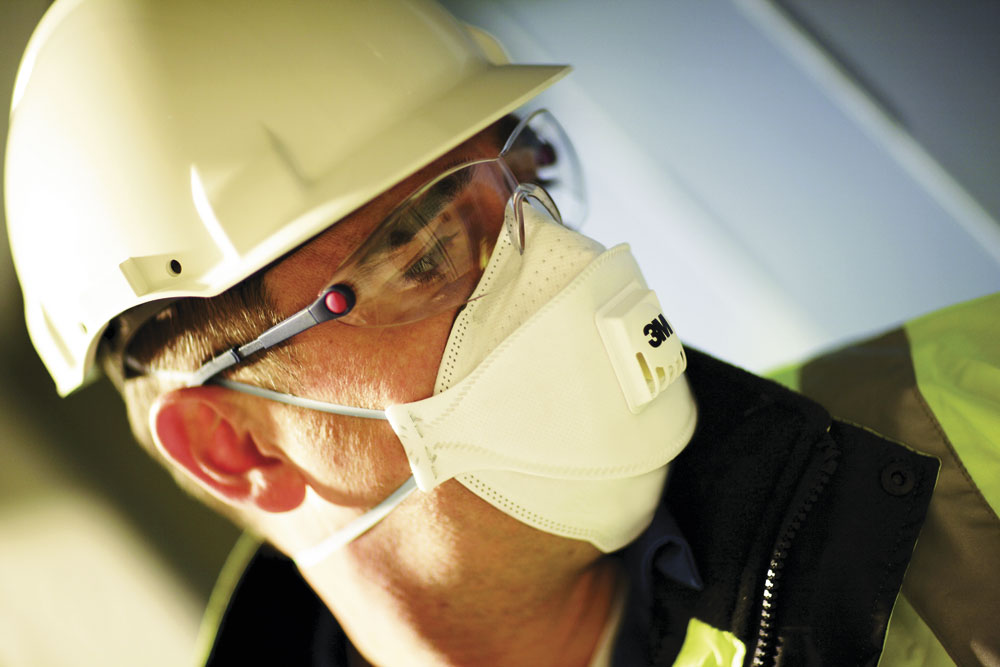
The role of respiratory protective equipment (RPE) and hearing protective equipment (HPE) in creating a safe working environment
British Lung Foundation statistics show respiratory disease is the UK’s second- biggest killer, with deaths from occupational lung disease rising rapidly. 3M have started to investigate personal protective equipment (PPE) use, with specific interest in comfort levels. Fundamentally, if PPE is uncomfortable or impedes the wearer’s job, it is unlikely to be worn correctly for a sustained period, so will not deliver consistent protection.
An independent report commissioned by 3M asked respiratory protective equipment (RPE) users to rate product attributes, with protection and comfort cited as the two most important features when selecting RPE.
Respirators have an assigned protection factor (APF), designed to give a reasonable safety margin. If properly fitted and used, actual protection may exceed the APF. However, protection levels can drop dramatically when a respirator is not used, even for a short period.
While RPE has to meet set standards, these do not necessarily address comfort. Also comfort is subjective – what is comfortable for one person may not be comfortable for another.
When developing new products to address comfort, therefore, consideration is given to all aspects of the product, including: pressure from straps on respirators; headbands on hearing protection; side arms of eye protection; materials used and how these feel against skin; and shape and fit. If equipment does not fit properly, the wearer risks potential health problems. Users should, therefore, be fit-tested to ensure the chosen respirator seals well to their face.
Employers must assess the risks and control them to an acceptable level. Before turning to personal protective equipment, they must consider other controls, depending on the situation.
RPE must suit both the wearer and the situation – it must fit correctly, be comfortable, robust enough for its environment and compatible with any other PPE worn.
RPE broadly falls into two types – those filtering contaminants from the air and those supplying clean air from an outside source. The decision on which to use will depend on the contaminant level and type, and user preference. A variety of RPE that is fully compatible with welding shields is available, protecting against most common fume types.
Getting the best out of reusable respirators
Reusable half-face and full-face respirators help ensure workers receive clean, safe air. Modern products can be fitted with various filters to reduce exposure to gases, vapours and particulates, depending on the filter selected.
However, respirators only protect effectively if timely and correct pre- and post-use checks, care and maintenance, and consumable replacement are undertaken. Appropriate storage is also crucial.
Before donning a previously used reusable respirator, the face piece should be checked for cracks, tears and dirt. The inhalation valve may also harbour cracks and tears. A cracked or torn respirator should not be used.
The next step is to check that head straps are intact and have elasticity. Respirators whose straps have lost their elasticity are unlikely to offer a snug enough fit, potentially leaving gaps through which harmful gases and particulates can pass.
The user should also check all gaskets are present, then remove the exhalation valve cover to examine the valve and seat for dirt, cracking or tearing. Once again, cracked or torn products should not be used. Stocks of spares should be maintained for each product type to allow immediate repair. Lens lifetime can also be prolonged by using peel-off lens covers.
Once all these points have been checked, and the correct filters attached, the product can be worn safely.
One issue that can significantly affect the protection offered is when respirators are removed mid-shift, then put on again. Unfortunately, it is not unheard of for users to remove RPE while in the hazardous area. The problem is exacerbated if it is left where contamination can settle on its interior, meaning the user is then breathing potentially highly toxic air. Employees should, therefore, always don the respirator before entering the affected area and only remove it when well clear.
After use, respirators should be cleaned and, if required, disinfected. Masks are generally cleaned with specialist, disposable cleaning wipes or immersion in a cleaning solution. The product should then be rinsed in fresh, warm water and air-dried in a non-contaminated atmosphere.
Once dry, masks should be stored in a clean area, with full-face masks stored face-up to reduce the risk of scratching the lens. Many products also have their own cases, offering further protection.
Given variations in usage levels and gas and particulate quantities being filtered, it is difficult to be prescriptive about intervals for changing filters. Particulate filters can generally be used until they become harder to breathe through, while gas and vapour filters should be replaced before they become saturated or, as a last resort, when the user notices a smell or taste of gas, indicating the carbon within the filter is saturated. For this reason, gas and vapour filters should only be used to guard against gases and vapours with good ‘warning’ properties.
All reusable RPE is subject to COSHH record-keeping requirements. Monthly maintenance and testing records must be kept for at least five years and produced on demand for HSE inspections. Record cards are available from a number of sources including respirator manufacturers. The face seal, nose cup, straps, valves and gaskets, and visor should be checked monthly, with details noted on the record card.
Specifying hearing protection equipment
Current UK law requires employers to implement a hierarchy of control measures before hearing protective equipment (HPE) is considered. The first is the elimination or substitution of noise sources. However, investment in new equipment is an expensive and typically long-term consideration, meaning noisy equipment could remain in situ for an extended period. Meanwhile, many processes still need human control or intervention, requiring operatives to be near equipment during operation.
The second stage is engineering controls, such as using processes generating less noise or reducing noise generated by the source, as well as administrative controls such as job rotation or simply increasing distance between operator and noise source. Only when these two stages have been thoroughly explored should HPE be considered.
The Control of Noise Regulations detail two noise action values and one exposure limit value for occupational noise exposure. If the lower value of 80dB(A) or 135dB(C) is exceeded, employers must offer HPE upon request.
Where exposure exceeds 85dB(A) or 137dB(C), employers must provide HPE where noise cannot be reduced by other means. The limit values of 87dB(A) or 140dB(C) must never be exceeded.
BS EN458 suggests an ideal exposure level between 75 and 80dB(A), with 70–75dB(A) and 80–85dB(A) as acceptable. Anything above 85dB(A) is deemed excessive noise. Conversely, HPE which reduces noise levels below 70dB(A) can cause other problems, as the employee may become isolated from the environment.
HPE attenuation can vary greatly with noise frequency, with overall effectiveness depending on the frequency content of incident noise.
Varying occupational noise hazards and environments therefore require different HPE types, offering different attenuation levels.
Furthermore, not everyone will achieve identical attenuation with identical equipment. If the product is incorrectly fitted, lower protection will be achieved.
Protection levels also suffer if HPE is dirty or poorly maintained, or if there are compatibility issues with other personal protective equipment.
The HSE’s ‘Controlling Noise at Work’ document suggests applying a ‘real world’ factor of 4dB, meaning that when calculating the actual protection offered, 4dB should be deducted from the manufacturer’s predicted figure.
Once the required attenuation level is calculated, including the 4dB allowance, several other factors must be considered.
First, the product must be suitable for the work being undertaken – durable enough for the environment, and should not need regular adjustment. HPE must be compatible with other PPE worn while addressing noise exposure patterns – for example, continuous noise or intermittent loud bangs – and allowing communication, if required. Some products have built-in communication radios or level-dependent ear muffs which electronically analyse sound before transmitting it to the ear. Bluetooth can also be built in.
The environment in which the product is to be used is another consideration when choosing between disposable and reusable HPE – products used in dirty or dusty environments require regular maintenance, such as frequent cleaning and daily visual inspections for wear and damage. For HPE to remain effective, a stringent care and maintenance policy should be established with employees undertaking the simple checks required.
Comfort and user acceptance are vital, with a small period of non-usage due to discomfort or removal significantly affecting the protection offered. Any usage level less than 100% is likely to considerably reduce HPE effectiveness.
The process should also establish whether users have any medical disorders such as earache, ear canal irritation, discharge, hearing loss or noise sensitivity. Where employees have any such conditions, employers should seek medical advice on HPE suitability.
Once the decision is made, it is not acceptable simply to provide HPE and expect that to be enough. Training and information must legally be provided on when to wear HPE, correct fitting and maintenance, and a health surveillance programme should be established.
For further information on RPE and HPE visit: www.3M.co.uk/ohes