Safer for All
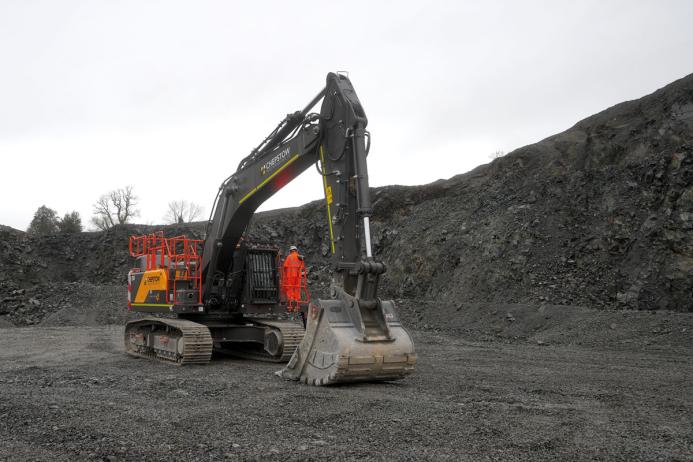
First published in the February 2025 issue of Quarry Management
Chepstow Plant International continue to raise the bar in on-site safety with the introduction of a pioneering ground-level refuelling concept on two recently delivered Volvo F-Series crawler excavators at Tarmac’s Dolyhir Quarry
As the mineral products and extractives sector aims to achieve zero lost-time accidents, incidents, and injuries in the workplace, the Strategic Safety Forum (SSF) has identified working at height as one of the leading causes of fatalities, serious injuries, and incidents within the sector over the last decade.
Recent Health and Safety Executive (HSE) statistics show little improvement in the number of workplace falls from height. In 2023/24, 51 workers lost their lives due to falls from height – a significant increase from the 40 fatalities the previous year.
These alarming statistics show that much work still needs to be done to ensure that those who work at heights do so in as safe an environment as possible. Notably, quarrying remains one of the more dangerous industries to work in. While sustainability, decarbonization, and lowest cost-per-tonne productivity are essential for any aggregate extraction operation – none of these factors should ever trump safety.
‘Health and safety is our top priority, and we must continue to collaborate with our partner organizations, taking a holistic approach to drive safety at all levels across the mineral extractives and quarrying sector,’ commented James Thorne, joint chief executive officer of The Institute of Quarrying (IQ) and Mineral Products Qualifications Council (MPQC).
‘A key focus of the Strategic Safety Forum is to eliminate harm from the Fatal 6, which has been identified as responsible for many fatalities and serious injuries in our industry. In a modern, ever-evolving workplace like mineral extractives, everyone working in the sector has a moral obligation to operate at the highest levels of safety competence and to create a safer working environment for all.
‘Mitigating the Fatal 6 high-consequence hazards – which include working at height – is critical to protecting the health, safety and welfare of workers, ensuring compliance with regulations, and helping us to reach our ultimate goal of delivering quarrying as a zero-harm industry.’
Demonstrating an ongoing commitment to embedding health and safety within the culture of an organization is always the first step to achieving successful behavioural change within a business. Risk assessment is another crucial step in safeguarding employees, and the most vital aspect of this is to identify and prioritize those hazards which could seriously affect the health and safety of workplace personnel and potentially cause real harm or injury.
At Chepstow Plant International (CPI) – one of the UK’s leading aggregates and earthmoving contractors – safety is an absolute priority for managing director John Corcoran, who is widely recognized within the industry for his trailblazing initiatives in health and safety.
‘Safety is an integral part of our DNA and operations because people are at the heart of everything we do,’ said Mr Corcoran. ‘It is a value shared by our entire organization – from the headquarters and workshop facilities down to our UK-wide network of mobile service engineers.
‘Setting high safety standards will always be our main priority. As a business committed to driving the health and safety agenda, we work closely with our customers and equipment partners to maintain, share, and spread best working practices across the wider mineral products industry.’
Indeed, CPI are no strangers to raising health and safety standards. The company has established strategic and long-term collaborative partnerships with some of the world’s leading heavy construction OEMs, such as Volvo CE and Bell Equipment, which have led to the implementation of inclinometers on articulated dumptrucks (ADTs) and game-changing onboard telematics systems.
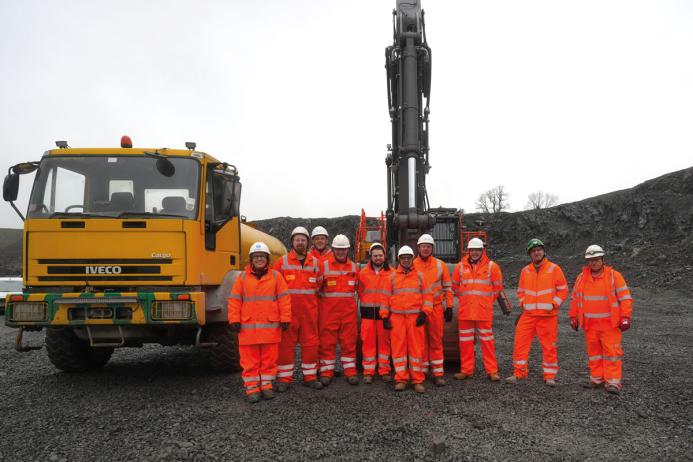
Cath Pickett, CPI’s national health and safety manager, commented: ‘Quarrying health and safety has come a long way over the last two decades, driven by rigorous adherence to regulations, enhanced safety measures, and more serious investment in health and safety systems.
‘However, there is still much work to be done – the figures are still far too high with 51 workers fatally injured in the construction sector during 2023/24. As an industry, it is important to come together to address this and ensure everyone goes home safe and well every day.
‘Sharing is a key part of making the quarrying workplace safer and healthier, raising standards and maintaining the best-possible levels of safe working practices on site. We’re at our best when we learn from each other – focusing on the causes of the most serious incidents and working together to eliminate the Fatal 6 from our workplaces.’
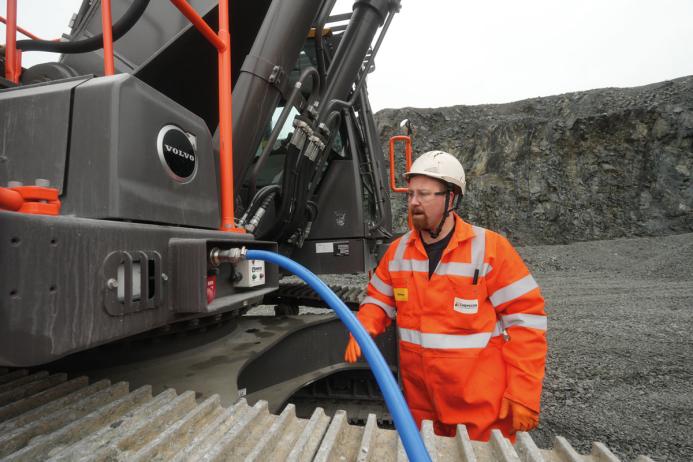
Addressing falls from height
According to HSE statistics, falls from heights remain the leading cause of work-related deaths in the UK. Fatal falls accounted for 36% of all worker fatalities in 2023/24, an increase from 30% in 2022/23 and 25% in 2021/22. This alarming trend underscores the necessity of prioritizing safety measures and equipment to protect workers in the mineral extractives and heavy equipment sectors.
Chepstow Plant and Volvo CE dealers SMT GB, for instance, are elevating on-site safety with the introduction of innovative ground-level refuelling points (for both diesel and AdBlue) on two recently delivered new-generation Volvo F-Series crawler excavators, an EC500 and an EC400, at Tarmac’s Dolyhir Quarry in Powys, Wales.
The game-changing safety solution was prompted by a serious incident five years ago involving a Chepstow Plant worker, who fell from a walkway on mobile plant during refuelling and suffered a broken rib.
Following the accident, CPI conducted a thorough health and safety investigation to identify how future injuries and incidents of this kind could be prevented by determining the root cause. This included reviewing the company’s extensive mobile plant fleet and best-practice equipment across the mineral extractives and aggregates industry.
The results of the investigation prompted Mr Corcoran to take on the challenge of addressing working at height in load and haul operations and developing a newer, safer approach to refuelling all heavy earthmoving machinery.
He remarked: ‘When trying to avoid slips and falls, it is easy to overlook steps as basic as ensuring proper footing when climbing machinery. Add in factors such as operator fatigue, adverse weather conditions, and AdBlue spillages – which make walkways and steps more slippery – and the likelihood of workers falling from height increases. It was, therefore, critical for us and SMT GB to find innovative and efficient ways to eradicate working from height when refuelling mobile construction plant.’
The consensus among safety professionals is that the most effective way to mitigate health and safety risks is to design the hazard out of the machine, component, or system. Designs should be forward-thinking and transformational – exceeding compliance standards and increasing the operators’ ability to incorporate future upgrades cost-effectively and easily by taking a modular approach.
Quarrying is a constantly evolving industry, so fundamentally, the focus on health, safety, and mental well-being should always be unrelenting. Chepstow Plant’s strong partnership with SMT GB serves the UK construction materials sector as a reminder that to achieve zero harm in the workplace, everyone across the value chain needs to be working collaboratively – and not in isolation or competition.
Following months of meetings and development work with Volvo CE and SMT GB, agreements were finally put in place to incorporate CPI’s ground-level refuelling concept on all Volvo excavators ordered by the business in 2024. Going forward, there are also plans to retrofit all existing E-Series excavators across the company’s mobile equipment fleet.
James Thorne commented: ‘John Corcoran’s simple yet ingenious and effective ground-level refuelling system is not just eliminating serious accidents in the field but also aiming to change the whole culture regarding health and safety by integrating safer practices in the workplace that focus on continuous improvement and proactive prevention.
‘With many hazards present, standardizing ground-level refuelling for the UK mineral products industry demonstrates the need to take innovative steps and encourage the sector to be progressive in its thinking – further improving the quarrying workplace and raising health, safety, and environmental standards.’
Since taking delivery of the new-generation Volvo EC500 and EC400 excavators at Dolyhir Quarry, both machines are proving a big hit with the site operatives, as Tarmac machine operator Eddie John explained: ‘The EC500 is hands down the best excavator I’ve ever operated at Dolyhir – it’s powerful, comfortable, efficient, and highly productive, packed with innovative safety features.’
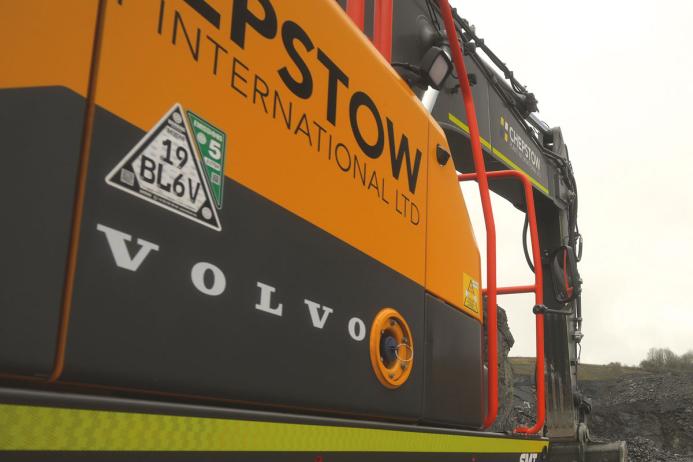
Echoing Mr John’s sentiments, Rhys Morgan, CPI engineer at Tarmac’s Dolyhir and Gore quarries, said: ‘The bespoke Volvo F-Series excavators have ticked every box on the customer’s agenda, from improved productivity and machinery uptime to a host of cab upgrades and enhanced safety measures.
‘With the new EC500 and EC400 machines, I don’t have to worry about working at height during refuelling tasks – as both diesel and AdBlue fuelling points are easily accessible from ground level and filling up is straightforward, much quicker, and more efficient than other excavators on site.
‘There are also automatic shut-off features to prevent overfilling, and a lot of thought has gone into avoiding AdBlue contamination and allowing for easy cleaning around the filler cap before use. The greatest benefit of ground-level fuelling, however, is the total elimination of regular working at height from the machine operators’ working day. This safety approach protects machinery assets, the environment and, most importantly, site personnel.’
Better together
The mineral products industry has undergone significant change in the last few years. Driven by advances in technology, the increasing emphasis on sustainability, and evolving safety standards, there has never been a more critical time for quarry operators and materials suppliers to adopt new and emerging trends.
Cath Pickett believes working in ‘true partnership’ is pivotal to driving sustainability and reducing the number of industry fatalities and incidents. The success of Chepstow Plant’s innovative ground-level refuelling concept is a prime example of what can be achieved through collaborative working.
‘Working in close collaboration with our customers and suppliers has always been part of our culture, so we need to continue to take this unified approach – as the Strategic Safety Forum and IQ have demonstrated – to improve safety standards further and prevent serious accidents/incidents and ill health across the sector,’ reiterated Mrs Pickett.
Indeed, CPI have clearly gone above and beyond in taking innovative steps and encouraging the aggregates industry to be forward-thinking in maintaining the safety and well-being of quarry operatives and driving its quest for zero harm.
Mr Corcoran emphasized the importance of breaking free from the safety improvement plateau and urged companies to foster collaboration and take proactive measures to improve safety performance continually by using the Fatal 6 as strategic drivers.
Workplace safety is a critical aspect of any business, and organizations must be aware of the dangers of becoming complacent and falling into a safety plateau. CPI’s pioneering ground-level refuelling project and their strong partnerships with IQ, SSF and SMT GB exemplify the drive for widespread health and safety transformation across the UK mineral products sector.
Continuously striving for improved safety performance is essential to ensure that employees are safe and protected from harm while on the job. Mr Corcoran concluded: ‘Collaboration is the key to safety innovation, so we are very grateful to our supply chain partners SMT GB, particularly Simon Albert and Matt Jennings, who helped get the project off the ground and to fruition.
‘The ground-level refuelling project has proven to be a huge success, and with the support of the Strategic Safety Forum, we’ll be looking to standardize this safety improvement not just for Chepstow Plant, but also across the wider minerals and aggregates sector.’
Subscribe to Quarry Management, the monthly journal for the mineral products industry, to read articles before they appear on Agg-Net.com