Safeguarding Plant and Machinery
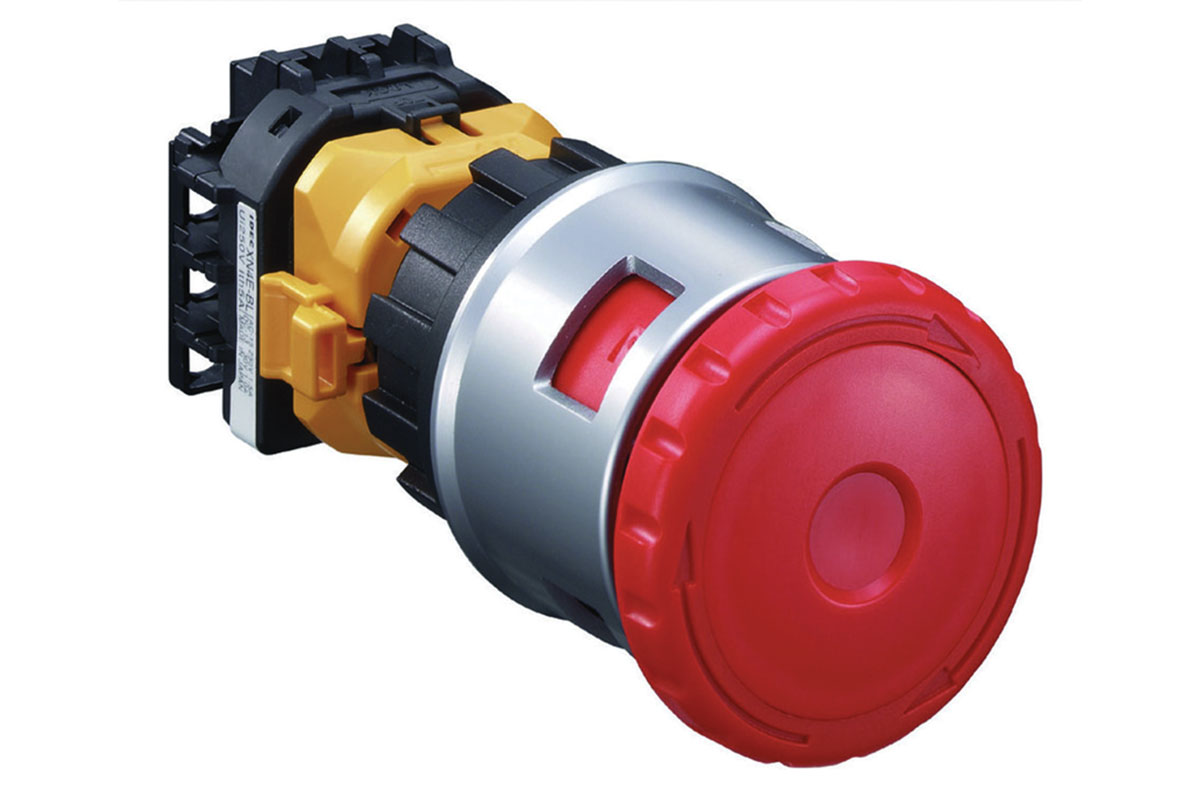
First published in the July 2021 issue of Quarry Management
Overcoming the challenges in the mineral extraction and processing industry
Despite robust legislation, the Health and Safety Executive (HSE) still identifies UK quarrying as one of the most dangerous industries to work in. Safeguarding plant and machinery is essential to meet the legal obligations already in place, including the PUWER regulations and the strict requirements of the Quarrying Regulations Act 1999, for managing risks and avoiding injuries. This article examines some of the engineering challenges for protecting people and machinery commonly used in the mineral extraction and aggregate processing industry, such as crushing, screening, washing, drying and bagging equipment.
Everyone is aware that quarrying and its associated activity is highly demanding work. Machinery must be durable enough to withstand the daily rigours of the task in hand as well as having the ability to be maintained and operated in a safe manner. In terms of machinery safety, one size does not fit all, and compared with other industries, mineral processing equipment has several additional challenges to deal with that are not regularly witnessed elsewhere, including:
- Nothing is uniform – Dealing with a natural product such as limestone or a reclaimed aggregate often causes jams and breakages, requiring frequent access.
- Throughput is king – Incentivised operators often push the equipment to or even beyond its original design limit. Anything that slows things down is seen as a big hinderance.
- When one machine stops, we all stop – Space required for stockpiling is often limited on site so halting one link in the process chain often results in a site-wide shutdown shortly afterwards.
- A long way to walk – With material-handling conveyors often stretching hundreds of metres into the distance, short-cuts are often considered when something does go wrong.
- Stop when you can – High loads and long over-run times mean emergency-stop commands are likely to be too late to make a difference, preventing access is often the more suitable solution.
- Shake and vibration – Quarrying equipment is not noted for its quiet and smooth running as it reduces one-tonne lumps of granite into aggregate material.
- Taking no prisoners – Powerful, high-torque equipment requires high-performance safety-related control systems. Escaping with only ‘broken bones’ could be seen as a good outcome following an accident with most quarry equipment.
Current legislation identifies the need for taking a hierarchical approach to safeguarding the dangerous elements of equipment. Due to the inherently unsafe nature of the quarrying process, it is often not possible to completely design out the hazard and simply providing a padlock or warning sign to an opening access door would not be deemed suitable if better methods could be used. If the guard door can be replaced with a fixed panel, this should be used, but if frequent access is needed, an interlocked door should be provided instead, ie where the hazard is removed upon opening the door by bringing motion to an instant stop or delaying the unlocking of the guard door where longer run-down times are experienced.
Too often the safety interlocks fitted to a machine end up being subject to manipulation or being disconnected completely. This often occurs when the interlocking device reduces operator efficiency or when regular access to an aging machine is required for maintenance. This highlights the increased need for a considered selection of safety devices for any application, as well as for adequate maintenance procedures and safety checks to be in place. For example, the interlock used on a food packaging line is unlikely to be suitable for safeguarding the flywheel on a large jaw crusher. Features such as wide-tolerance, ‘ramp-based’ locking systems that do not rely on tongue-type actuators fitting into a slot can eradicate downtime caused by misalignment and make the overriding of safety interlocks a thing of the past.
Keeping the plant running will be on everyone’s mind; a single failure can lead to the entire operation grinding to a halt, and considering that safety interlocks, emergency-stop devices and rope-pull switches are crucial in allowing the plant to operate, comprehensive diagnostics and interlock reliability become a very important feature. Unlike a company making widgets, a quarry operator does not usually have the option of switching production to a different site when things go wrong. At the fundamental ‘on-machine’ level, bright daylight-visible LEDs give a clear indication of current status as well as additional diagnostics to the machine control system, all helping to increase the ‘uptime’ of the operation. For more complex equipment, safety and diagnostic information can often be sent via proprietary or conventional fieldbus systems, including Siemens PROFINET and PROFISAFE, substantially reducing the amount of wiring required and even providing information, eg to allow preventative maintenance programmes to advise when a guard door may need to be serviced.
Although not always ideal, maintenance operations often require access to the dangerous parts of equipment and preventing inadvertent start-up or reducing the hazard to an acceptable level needs to be considered. The Lock-Out Tag-Out system is well established nowadays but the thought of the long walk back to the control panel to place the padlock may possibly provide the motivation to ignore the safety procedures in place and ‘risk it’. By using local interlocking devices that incorporate a local padlock ‘lock-out’ facility, the likelihood of an operator side-stepping the safety procedures is greatly reduced. Several interlocks are able to accommodate up to six padlocks on a single device.
The ability to ‘lock out’ is great when the person involved recognizes the danger to themselves or others, but what about when an operator or maintenance person tries to deliberately override an interlocking system, often to make things easier for themselves? The most common method of overriding a guarding system is by using a spare actuator (key) to trick the guarding system into believing the door is closed. This is an easy problem to overcome using RFID ‘coded’ actuators paired to the safety-switch – only one actuator can be ‘paired’ at a time and if the operator tries to use a different actuator the machine will not run.
David Dearden from safety equipment manufacturers Euchner is proud of the company’s solutions in this field. ‘As the company responsible for developing the first RFID locking guard switch, we know a thing or two about preventing defeat or manipulation of safety systems,’ he commented. ‘With greater focus being placed on this subject within the relevant safety standards, including BS EN 14119, it is vitally important that all equipment manufacturers and end-users consider whether their existing arrangements are adequate.’
Although some may feel that electronic safety devices are unsuitable for use in the arduous applications within a quarry, these devices can handle pull-out forces up to 8kN (much more than even the strongest person could manage), often use vibration-tolerant encapsulated solid-state, fail-safe electronics and achieve very high ingress protection ratings, including IP65, IP67 and IP69.
The selection of the safety interlock is only part of the story; plant and equipment used in the mineral extraction industry is often extremely dangerous and, therefore, the safety-related control system used to safeguard many of the dangerous parts needs to be designed to meet a high performance level and detect faults when they occur. It is no good only to find out your guard interlock has failed when the machine does not stop on opening the guard door.
According to David Dearden, this is one of the most common issues he comes across when visiting sites, with machinery operators not being aware of their responsibilities and the risk assessments that have been undertaken into the safeguarding measures provided by a particular safety control system not being thorough enough. ‘Many site-based risk assessments highlight the safeguard measures that are fitted to a machine, such as interlocks, pull-cords etc, but has someone actually assessed the design of the electrical control system behind these devices? The standards, including BS EN 13849-1, assist in the process of determining the performance level (PL) required for the control system protecting the hazard, and although it is sometimes seen as too complex, plenty of help is available from companies, including Euchner, to assist with this much-too-often missing step. The safety manager needs to be sure that the safety-related control systems have been designed and verified irrespective of how much functional testing takes place during the working week.’
The functional test often used at the start of a shift only shows the system is working at that single moment in time; it does not give any guarantee the system will operate next time it is called upon, which may be when someone’s life depends on its correct operation.
Not all applications are the same and it is always important for the correct components to be selected for any given application. Because of the often-heavy nature of the product being processed, combined with a very demanding operational environment, the machinery used in the mineral extraction industry creates a lot of additional challenges for equipment users and original equipment designers alike. But, by focusing on good practice with suitable equipment, it is possible to achieve increased plant efficiency at the same time as running a safer site, quashing the long-considered opinion that machinery safety reduces throughput – and without having to consider the distressing consequences of not getting plant safety right in the first instance.
- Subscribe to Quarry Management, the monthly journal for the mineral products industry, to read articles before they appear on Agg-Net.com