Dust: What’s the Problem?
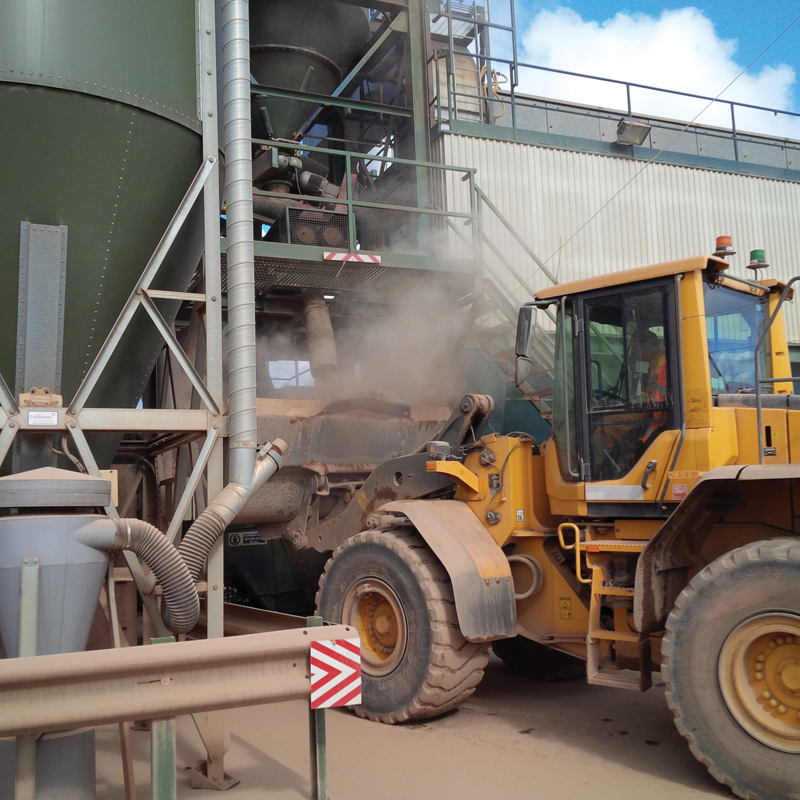
First published in the December 2015 issue of Quarry Management
Bill Noakes of Atlantic Pumps discusses the problems caused by airborne dust to quarry operators, an area increasingly being focused on by the HSE, and looks at some of the solutions available
The dust caused by quarrying activities is a major headache for the quarry operator for two main reasons: the effect of dust pollution on the nearby communities, and the impact of the dust on the health and welfare of the quarry workers.
If a quarry creates levels of dust that could cause damage to property or disturbance to the surrounding community, the local council’s environmental health department can place restrictions on the operation or require steps to be taken to reduce the nuisance. Levels of dust pollution can also affect planning permission and operating licences. As cities grow closer to quarries and environmental regulation increases, this problem is likely to increase in the future.
The dust generated at a quarry will also be inhaled by the quarry operatives. Depending on what is being quarried and the mineral type, the impact of this can range from a nuisance to a serious health hazard. Health hazards include asthma, chronic obstructive pulmonary disease (COPD), silicosis and lung cancer. The effect of this is increased sick leave and exposure to claims for industrial disease. All quarries have to comply with health and safety legislation, with the HSE particularly focusing on the potential for long-latency disease from exposure to respirable crystalline silica (RCS).
A further consideration is the impact of dust on the operation of a quarry, eg through reduced visibility, smeary windscreens and dirty office accommodation.
Many of the processes in a quarry can cause the disturbed material to become airborne. The extraction of minerals, especially if done by blasting, is a major cause of dust. Processing of the minerals, particularly crushing and screening, is another key source. Many quarries have vehicles running on unsealed roads, which can cause widespread dust, sometimes close to the communities bordering the site.
Controlling dust
Three options are available: dust can be extracted, contained or suppressed. Dust extraction is possible if processes are indoors, but is much more difficult in an open-air environment. Dust containment is only effective where a process can be enclosed, for example by boxing-in a fixed conveyor. This leaves dust suppression as the primary method of dust control in most quarries.
Dust suppression involves spraying water either to wet the material being processed or to capture airborne dust, or both. The use of water sprays is popular because this method is both economical and effective, and can be rapidly implemented. Installation is straightforward and, with regular maintenance, offers a long-term solution. Wetting of the material is possibly the simplest solution; the quarry product can be sprayed both when static and when being moved. Roadways can be sprayed before vehicles use them. Sometimes surfactants are added to the water to lower the surface tension of the water, which spreads the water droplets further and increases the penetration of the water into the material pile.
An alternative to wetting the material is to spray very fine water droplets into the dust after it has become airborne. The water and dust collide, forming a heavier agglomerate which falls to the ground, removing the dust from the air. Sometimes marketed as a ‘dry’ method of dust suppression, an advantage of this method is that very little water comes into contact with the material or the quarry operatives. The size of the water droplet is critical, because if they are bigger than the dust particles, the dust is likely to flow round the water rather than collide with it.
Dust-suppression systems typically consist of the permanent installation of a high-pressure ring main with numerous spray heads. These heads are located wherever dust is likely to be generated. Careful consideration needs to be given to the length of pipe used, the number of spray heads, the distance the water has to be pumped and the diameter of the pipe. Mobile mist cannons are available for more temporary requirements or if the solution is required to be portable to accommodate mobile site operations or dust-emission points. Mist cannons use electrical oscillation and turbofan propulsion of finely-atomized water droplets to cover large open areas without excessive water usage. Some mist cannons can utilize recycled water, which reduces dependence on potable water supplies.
Water source
It is important that there is a regular supply of clean or filtered water for a dust-suppression system. An ideal method is to reuse the water obtained from dewatering the quarry, from the lagoon at the bottom of the quarry or from a borehole on site. In some cases it is necessary to use water from the mains, but this is the most expensive and least environmentally friendly source.
Pumping water out of a lagoon will involve an industrial submersible pump in the lagoon feeding a storage tank. Water is drawn from the storage tank using high-pressure multi-stage pumps which fill the ring main at the required pressure. Often the water being drawn from the lagoon is clean enough to use without any strainers or filters because any quarry residue will have settled on the bottom of the lagoon. Specialist borehole pumps are available which can draw clean water directly from an on-site borehole to a storage tank, or directly into the ring main system. These pumps can supply the water at high pressure, so there is often no need for a multi-stage pump if the water is being fed straight into the ring-main. Mains water is typically fed into a storage tank and a booster pump is used to produce the required pressure.
For more information visit: www.atlanticpumps.co.uk
- Subscribe to Quarry Management, the monthly journal for the mineral products industry, to read articles before they appear on Agg-Net.com