Behavioural Safety
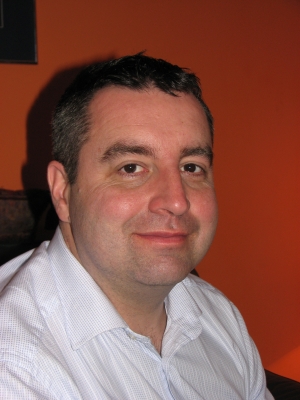
Many organisations have excellent procedures for examining the causes of accidents and incidents and implement appropriate risk control strategies and this is of paramount. But what do they do to prevent the incident in the first place. As in most industries, almost all incidents are due either to active or passive human behaviour. Although incidents can sometimes be exacerbated by poor working conditions and/or poor systems of work, there is a fundamental need to change they way people think within business to ensure that not only are they carrying out their job safely but to also give them the confidence to stop and say no to an unsafe situation that they are exposed to.
On many occasions the words ‘a good health and safety culture’ is associated with the continual reporting of near hit incidents or the positive reaction of employees in emergency situations. These are important factors in health and safety management…..but they are reactive. Successful behavioural safety is about investigating the unsafe acts that lead to near hit incidents; its about challenging the business when things appear to be going well, not just when something goes wrong; it’s about creating a transparent management structure so the person at the top can clearly see what is happening at the ‘sharp end’ of the business, the employees can see the commitment from the leaders and it’s about developing an interdependent culture where the emphasis is placed on ‘team’ rather than individuals.
At this point you are probably thinking that this is good advice and you may have already identified these solutions as something everybody tries to aspire to. The question is how do we get there?
There is a process (business model) you can follow which can make a difference to the health and safety performance of your business and over time ensure that all employees within your business suggest, develop and drive new initiatives. The process is based around five simple steps:
Step 1: Problem solving
If you really want to understand where the issues are within your business you need to speak to the people doing the job. By talking, listening and challenging all aspects of the business (employees, managers, contractors) will give you an appreciation of what the employees perceive are the health and safety issues in the workplace. This can be achieved by involving a percentage of your workforce in a problem solving workshops. The workshop should be interactive and challenge attendees to come forward with both the policy and site specific issues that are affecting the business. Then it requires the people attending the workshop to work together to find solutions. This may sound simple, but the involvement of the workforce at an early stage will ensure the solutions are appropriate, will make them feel part of the forthcoming changes, and will also ensure they understand what is expected.
The workshop forms one part of the problem solving exercise, and it should be run in conjunction with a site specific review. The review will focus on key health and safety procedures (risk assessment, contractor control, policy) and the physical controls that are being used within the business. The objective is to identify if they are understood and being followed by the workforce.
The information gathered in step 1 will be used in step 2.
Step 2: Planning
The findings from the workshops and the site specific review are transferred into a health and safety business plan. The plan consists of strategic bridges that outline how to improve from where you currently are to, if necessary, become an industry leader in health and safety performance.
The strategic bridges are usually based around:
- The introduction of simple systems and procedures;
- Clear duties, responsibilities and behaviour enhancement;
- Modular interactive employee training;
- Improved supervisory and management training;
- Key performance indicators;
- The reduction of accidents;
- Other initiatives, review and future planning.
Once the business plan has been developed, it should be reviewed prior to implementation. This can be achieved through safety committee meetings, management meetings, notice board displays or any other format which will encourage feedback from the workforce. When agreed the plan can be formally introduced into the business. The plan must be kept under review and treated as a live document. Progress against the plan must be routinely communicated to all staff.
Step 3: Delivery
The first two steps will have gone a long way to improving communications in your workplace but you may find there is some cynicism. This will only be removed when people see and feel the delivery of the business plan. In most cases, the plan will include, as a main health and safety improvement, the delivery of interactive training. The word ‘interactive’ is something which is quite often proposed but very rarely delivered. Good training provides delegates with that essential information and knowledge and gives them the time and support to apply that knowledge in their working environment. In simple terms, training days should have less time spent in the classroom and more time spent in the workplace practically learning what is expected.
It’s so easy to fall into the trap of releasing employees for training and then realising that it hasn’t made any improvement in your business. In general employees want to learn, they want to make a difference and feel they have achieved something.
Health and safety training is a continual process and the delivery of it needs to be effective. Find courses that stimulate your employees and challenge them to make that difference. If you get it right at the beginning, your employees and your business will reap the benefits.
Step 4: Worker participation
By now you should have cemented a solid foundation in place, it’s now time take it to the next level. Worker participation requires a further visible commitment from the business to:
- Train managers to make better use of their employees;
- Introduce qualified safety representatives or a specific health and safety forum;
- Increase the ownership, understanding and confidence of all employees;
- Promote the development of an Inter-dependant culture;
- Ensure that visible felt leadership in an integral part of their business.
Every time you enter the workplace you confirm the level that you are allowing the business to operate at. Ask yourself ‘have you set the bar high enough?’ Lead by example, challenge your employees on how they are undertaking work activities. Good interaction will encourage the workforce to take ownership of health and safety and suggest new initiatives to improve the current performance.
Step 5: Behavioural auditing
The final step in the process is the task of reviewing the current performance. The reviewing process should not be a ‘ticking the box’ exercise but should be a systematic audit of the attitude and behaviour of the workforce.
The audits objective is to:
- Ensure that the loop is closed on all improvements that have been agreed;
- Ensure that complacency and cynicism have been removed from the business;
- Challenge everyone in the business (even when things appear to be going well);
- Demonstrate that managers, employees and contractors are working together to improve health and safety in the workplace; and
- Clarify that employees fully understand what is expected of them regarding their health and safety duties and responsibilities.
Summary
These simple steps are a concept that has worked and is still working in many businesses. Changing the mindset of a workforce can be a lengthy process but it’s certainly not a difficult one. Commit to building a solid foundation and you will reap the benefits for many years to come.
Colin Nottage
Director, Safety Horizon Ltd