A data-driven approach to hearing conservation
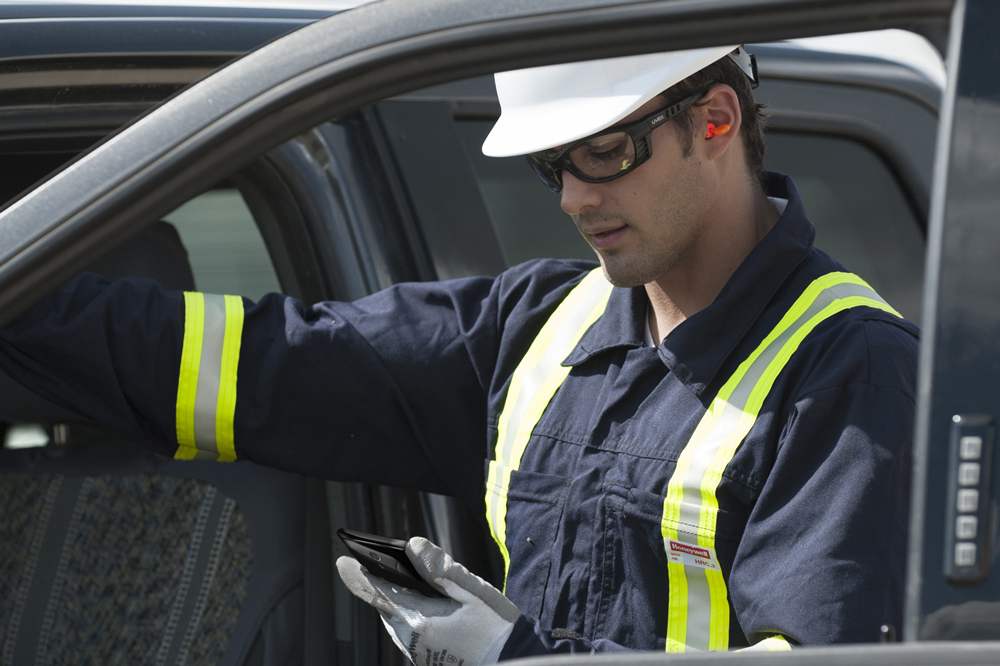
First published in the October 2018 issue of Quarry Management as Focus on the Fit
Kjersti Rutlin, global technical training specialist for hearing conservation at Honeywell Industrial Safety, looks at how fit-testing can help combat noise-induced hearing loss (NIHL)
Quarrying remains one of the most dangerous industries to work in, with a fatal injury rate five times as high as the average across all industries. Physical injuries – from falls to being struck by moving objects – are clearly a major threat to workers, but invisible risks such as loud noise can also have life-changing consequences. A quarry blast, for example, can produce noise levels in the region of 140dB, while pneumatic drills and generators can reach 130dB and 116dB respectively, all significantly above the daily exposure limit above which wearing hearing protection becomes mandatory (80dB). Even short-term exposure to loud noise can seriously damage hearing, but as noise-induced hearing loss (NIHL) tends to develop gradually, its devastating effects are often not experienced in full until it is too late to take action. That is why it is essential that workers have hearing protection that fits them well and is fit for purpose, and that they wear it consistently.
‘Fit-testing’ of hearing protection – a process whereby a safety manager looks into a worker’s ear and provides guidance on the correct size, shape and fit of earplugs – is an effective way of preventing NIHL. While the testing method has been available for quite some time, the uptake of the practice has been slow due to lack of education, awareness and specific regulations. Recent developments across health and safety and trade organizations, as well as successful applications, for example in the oil and gas sector, suggest that the industry could be reaching a turning point and upping its game against this workplace hazard.
NIHL: the role of legislation
Gaps in legislation combined with inadequate training practices are often cited as the reason why NIHL remains so widespread amongst workers. Whilst regulations have been in place for some time, fit-testing is yet to become mandatory.
Consequently, with no pressure from legislation driving the uptake, very few companies have made fit-testing an integral part of their hearing-conservation strategies, with the majority of them relying on the single number rating (SNR) value to identify attenuation levels. As SNR is population-based, it provides only a rough estimate of the potential attenuation and there can be significant variation between individuals using the same type of earplug, depending on how well they have fitted them.
Noise monitoring technology: the story so far
As noise exposure levels may vary significantly throughout the day and from one location to another, depending on the type of machinery being operated and the number of people in the area, determining the actual exposure levels can be quite a challenge. Technology can give safety managers some guidance, but until recently, it has had its limitations.
For example, a sound level meter can tell that the sound pressure in one section of the workplace is relatively low, yet a step closer to a generator or other equipment, the noise level can be significantly higher. Additionally, the real exposure to noise can dramatically vary between workers in the same location, wearing the same personal protective equipment (PPE), because they are not wearing it correctly or consistently.
The lack of accurate data not only puts the workforce at risk but can also have a negative impact on productivity. If the safety manager has no information about the actual exposure levels, often the only way to ensure workers are protected is to reduce the length of every shift to minimum, thereby increasing downtime.
On the other hand, the same lack of insight can also result in excessive protection and unnecessarily high attenuation, which can make workers give up protection to better hear alarms, colleagues or radio communications, thus heightening the risk of NIHL.
From guessing to knowing real attenuation levels
When it comes to determining individual attenuation levels, research shows that one-to-one training is key. In addition, integrating automatic fit-testing systems can further improve the accuracy of the process as it allows workers to assess, at a glance, if they are wearing their hearing protection correctly and helps them understand how a proper fit should feel. Monitoring and controlling sound exposure in real time over a work shift is also essential. Fortunately, some of the latest hearing-protection and communication technology can help simplify the task.
Personal protective equipment (PPE) such as earplugs embedded with miniaturized and in-ear microphones combined with software and cloud-based platforms allow continuous monitoring and analysis of sound exposure. Some solutions feature external microphones that are able to measure external noise levels and detect external sounds. This means that they can automatically analyze the external and in-ear noise and adapt the attenuation level as needed, in real time.
The ability to adapt rapidly to sudden high-impulse noise can help protect workers in environments where there could be unexpected variations in noise levels, such as quarries, whilst also helping improve situational awareness through lower attenuation when the external noise level is low.
If workers are about to reach the permitted noise threshold, they are immediately alerted through an LED light on the control unit and a spoken alert in the headset. More importantly, these solutions allow each worker’s sound exposure data to be stored in the control unit and downloaded to a PC using wireless data transfer. Safety managers can access this data remotely in order to monitor each worker’s sound exposure at any time to address potential issues quickly and to aggregate the data for further analysis.
Case study: tackling NIHL while boosting productivity
This proactive approach to improving hearing protection has already been put to practice by some forward-thinking companies in the oil and gas industry in Norway.
A major Norwegian offshore operator recently performed a fit-testing exercise on 100 of its workers, which revealed that nearly three-quarters were using their PPE incorrectly, receiving insufficient attenuation (less than 16dB) even though the earplugs they used had an SNR between 30–34dB.
Concerned with this poor performance, the company delivered one-to-one fit-testing training, after which the exercise was repeated. Strikingly, the percentage of workers with a poor fit dropped to just over 7% following the training.
Adopting a data-driven approach to hearing conservation can also enhance productivity. Previously, workers were permitted to perform noisy tasks, such as sand blasting, for a maximum of 15 minutes. The ability to monitor noise exposure in real time, however, means that it is now possible to undertake the same task, safely, for up to four hours.
In addition, as the company is now able to access PPE data remotely, the need for health and safety personnel to travel to offshore platforms to measure and monitor on-site noise exposure levels with dosimeters has reduced dramatically, resulting in both time and cost savings.
Conclusion
With noisy maintenance and other operations becoming a more regular occurrence in work sites across industries, businesses are beginning to recognize that a more proactive, data-driven approach is needed to address the risk of NIHL more effectively. Technology, together with strong hearing-conservation training programmes, can not only play a key role in protecting quarry workers against NIHL, but also help companies streamline processes and reduce downtime, boosting productivity. For more information visit: www.honeywellsafety.com
- Subscribe to Quarry Management, the monthly journal for the mineral products industry, to read articles before they appear on Agg-Net.com